
Lauf- und Leitschaufeln in einer Dampfturbine: In einer Dampfturbine spielen die Stufen, die aus Lauf- und Leitschaufeln bestehen, eine entscheidende Rolle für die Umwandlung der thermischen Energie des Dampfs in mechanische Energie. Jede Stufe besteht aus zwei Hauptkomponenten: den Leitschaufeln und den Laufschaufeln. Die Leitschaufeln sind stationär und lenken den Dampf so, dass er mit dem optimalen Winkel auf die Laufschaufeln trifft. Diese Laufschaufeln sind beweglich und befinden sich auf der rotierenden Turbinenwelle. Wenn der Dampf mit den Laufschaufeln in Kontakt kommt, übt er eine Kraft auf die Schaufeln aus, die die Welle in Bewegung versetzt. Die Anzahl und Gestaltung der Stufen sind entscheidend für die Effizienz und Leistung der Turbine, da sie die Energieübertragung optimieren und den Druck sowie die Temperatur des Dampfs schrittweise reduzieren. Jede Stufe nutzt den Dampfenergieverlust aus der vorherigen Stufe, wodurch eine kontinuierliche Umwandlung von Wärmeenergie in mechanische Energie ermöglicht wird. Eine sorgfältige Konstruktion und Anordnung der Stufen beeinflussen maßgeblich die Leistung der Dampfturbine und tragen zur Optimierung der Energieausnutzung bei.
Die Bedeutung der Stufen in einer Dampfturbine, bestehend aus Lauf- und Leitschaufeln, ist fundamental für die Effizienz und Leistung der gesamten Turbine. In einer typischen Dampfturbine gibt es eine Reihe von Stufen, wobei jede Stufe aus einem Satz von Leitschaufeln und einem Satz von Laufschaufeln besteht. Der Dampf, der in die Turbine eintritt, hat typischerweise einen hohen Druck und eine hohe Temperatur. Dieser Dampf wird durch die Leitschaufeln geführt, die den Dampfstrom lenken und die Richtung des Dampfs ändern, bevor er auf die Laufschaufeln trifft. Dabei wird die Bewegungsrichtung des Dampfs optimiert, sodass er mit dem richtigen Winkel auf die Laufschaufeln trifft, um die größtmögliche Energieübertragung zu gewährleisten.
Die Leitschaufeln haben in der Dampfturbine eine wichtige Rolle als „Lenker“ des Dampfs. Sie sorgen dafür, dass der Dampf mit der richtigen Geschwindigkeit und Richtung auf die Laufschaufeln trifft, was für eine effiziente Umwandlung der thermischen Energie in mechanische Energie entscheidend ist. Durch die richtige Auslegung der Leitschaufeln wird die Strömungsgeschwindigkeit des Dampfs und damit der Druckverlust in der Turbine optimiert. Auf diese Weise kann die Turbine mehr Arbeit leisten und eine höhere Energieausbeute erzielen.
Die Laufschaufeln sind beweglich und befinden sich auf der rotierenden Welle der Turbine. Wenn der Dampf auf die Laufschaufeln trifft, übt der Dampf eine Kraft aus, die auf die Laufschaufeln wirkt und diese in Bewegung versetzt. Diese Drehbewegung der Laufschaufeln überträgt die kinetische Energie des Dampfs auf die Welle der Turbine, wodurch mechanische Arbeit erzeugt wird. Jede Stufe der Dampfturbine trägt dazu bei, den Dampf schrittweise zu entladen und dabei die thermische Energie in mechanische Arbeit umzuwandeln. In jeder Stufe wird der Druck des Dampfs reduziert, während die Geschwindigkeit des Dampfs und die kinetische Energie erhalten bleiben.
Der Grad der Reduktion von Druck und Temperatur in jeder Stufe ist entscheidend für die Effizienz der Dampfturbine. Eine zu starke Reduktion in einer einzigen Stufe würde zu einem zu großen Druckabfall führen, was die Effektivität der Energieumwandlung beeinträchtigen könnte. Daher wird der Druckverlust auf mehrere Stufen verteilt, um eine kontinuierliche und gleichmäßige Umwandlung der Energie zu gewährleisten. Jede Stufe nutzt die verbleibende Energie des Dampfs, der in der vorherigen Stufe teilweise entspannt wurde, um die Energieübertragung weiter zu optimieren und den Wirkungsgrad zu steigern.
Die Anordnung und das Design der Stufen sind für die Leistung der Dampfturbine von zentraler Bedeutung. Eine Vielzahl von Stufen, die speziell aufeinander abgestimmt sind, ermöglicht es, den Dampf in mehreren Schritten zu entlasten und die mechanische Energie der Welle effizienter zu nutzen. Der Übergang des Dampfs von einer Stufe zur nächsten erfolgt schrittweise, was es der Turbine ermöglicht, ihre Arbeit über einen breiten Bereich von Druck- und Temperaturbedingungen hinweg zu leisten, ohne dass es zu signifikanten Effizienzverlusten kommt.
Ein weiterer wichtiger Aspekt der Stufenanordnung ist, dass sie zur Vermeidung von Kavitation und anderen Strömungsproblemen beitragen muss. Cavitation tritt auf, wenn der Dampf an bestimmten Stellen in der Turbine einen zu niedrigen Druck erreicht, was zu Dampfblasenbildung und damit zu mechanischen Schäden führen kann. Durch eine durchdachte Gestaltung und Anordnung der Leitschaufeln und Laufschaufeln wird dieser Prozess minimiert, wodurch die Lebensdauer der Turbine verlängert und die Wartungskosten gesenkt werden.
Zusammengefasst lässt sich sagen, dass die Stufen einer Dampfturbine eine wesentliche Funktion für die effektive Nutzung der thermischen Energie des Dampfs haben. Die Wechselwirkung zwischen den Leitschaufeln und Laufschaufeln ermöglicht eine schrittweise Reduktion von Druck und Temperatur des Dampfs, was in der Umwandlung von Wärmeenergie in mechanische Arbeit resultiert. Die Anzahl und Konstruktion der Stufen bestimmen die Leistungsfähigkeit der Turbine, und eine sorgfältige Abstimmung dieser Komponenten ist entscheidend für die Effizienz und Langlebigkeit der Dampfturbine.
Die Auslegung der Stufen in einer Dampfturbine ist eine hochkomplexe ingenieurtechnische Aufgabe, da sie direkt die Effizienz, Leistung und Betriebsstabilität der Turbine beeinflusst. Jede Stufe hat eine spezifische Aufgabe in der Energieumwandlungskette, und die Kombination aus Leitschaufeln und Laufschaufeln muss optimal aufeinander abgestimmt sein, um den thermodynamischen Prozess zu maximieren.
Ein zentrales Prinzip bei der Gestaltung der Stufen ist die Nutzung des sogenannten Impulseffekts und/oder des Reaktionseffekts, die je nach Turbinenkonzept unterschiedlich gewichtet sein können. In einer Impulsturbine wird der größte Teil der Energie des Dampfs in kinetische Energie umgewandelt, bevor er die Laufschaufeln erreicht. Die Leitschaufeln fungieren hier als Düsen, die den Dampf beschleunigen und in einen Hochgeschwindigkeitsstrom verwandeln, der dann auf die Laufschaufeln trifft und diese in Bewegung setzt. In einer Reaktionsturbine hingegen erfolgt die Energieübertragung sowohl in den Leitschaufeln als auch in den Laufschaufeln. Hier arbeiten beide Schaufelarten zusammen, um die kinetische Energie und die Druckenergie des Dampfs gleichzeitig auszunutzen, was eine kontinuierlichere Energieumwandlung ermöglicht.
Die Entscheidung für die Anzahl und Art der Stufen hängt von verschiedenen Faktoren ab, darunter die Eigenschaften des Dampfs, wie Druck, Temperatur und Feuchtegehalt, sowie die spezifischen Anforderungen des Systems, in das die Turbine integriert wird. Hochdruckstufen am Anfang der Turbine nutzen den Dampf mit maximalem Druck und Temperatur, um die größte Energiemenge zu extrahieren. In den nachfolgenden Mitteldruck- und Niederdruckstufen wird der Dampf weiter expandiert, wobei der Druck und die Temperatur weiter abnehmen, während die Volumenströme zunehmen. Dieser Prozess erfordert eine kontinuierliche Anpassung der Geometrie der Schaufeln und der Abstände zwischen den Stufen, um den Dampfstrom effizient zu lenken und Energieverluste zu minimieren.
Die Laufschaufeln und Leitschaufeln selbst werden aus hochfesten Materialien gefertigt, die den extremen Betriebsbedingungen standhalten können. Diese Materialien müssen nicht nur hohen Temperaturen und Drücken widerstehen, sondern auch Korrosion und Erosion, die durch den Dampf und eventuell enthaltene Fremdpartikel verursacht werden. Die Oberfläche der Schaufeln wird oft speziell behandelt oder beschichtet, um den Wirkungsgrad zu erhöhen und den Verschleiß zu reduzieren. Darüber hinaus wird die Aerodynamik der Schaufeln sorgfältig gestaltet, um Strömungsverluste zu minimieren und die Turbulenz zu reduzieren, die den Wirkungsgrad der Turbine beeinträchtigen könnte.
Ein weiterer entscheidender Aspekt der Stufenauslegung ist die Reduktion von Schwingungen und mechanischen Belastungen. Während des Betriebs wirken enorme Kräfte auf die Schaufeln, die zu Schwingungen führen können. Diese Schwingungen können Resonanzeffekte auslösen, die im schlimmsten Fall zu Materialversagen führen. Um dies zu verhindern, werden die Schaufeln so ausgelegt, dass sie in ihrer natürlichen Frequenz den Betriebsfrequenzen der Turbine nicht entsprechen. Darüber hinaus werden oft mechanische Verstärkungen, wie Zungen- oder Bandverbindungen zwischen den Schaufeln, eingesetzt, um ihre Stabilität zu erhöhen.
Die Stufen einer Dampfturbine sind zudem so ausgelegt, dass sie mit dem gesamten thermodynamischen System, zu dem die Turbine gehört, harmonieren. Beispielsweise muss die Turbine in einem Kraftwerk an die Eigenschaften des Dampferzeugers (z. B. eines Kessels) und des Kondensators angepasst werden. Der Kondensator, der den Abdampf der Turbine aufnimmt, beeinflusst die Entspannung des Dampfs in den Niederdruckstufen maßgeblich. Ein effektiver Kondensator ermöglicht eine stärkere Expansion des Dampfs in den letzten Stufen der Turbine, was den Wirkungsgrad weiter steigern kann. Die Gestaltung der Stufen muss auch die Möglichkeit von Tropfenbildung in den Niederdruckstufen berücksichtigen, da dies zu Erosion führen kann. In solchen Fällen werden spezielle Maßnahmen wie Tropfenabscheider oder Tropfenresistente Schaufelbeschichtungen eingesetzt.
Darüber hinaus spielt die Wartungsfreundlichkeit eine wichtige Rolle bei der Auslegung der Stufen. Moderne Dampfturbinen sind oft für einen Betrieb über Jahrzehnte ausgelegt und müssen regelmäßig gewartet werden, um ihre Effizienz und Zuverlässigkeit zu gewährleisten. Die Stufen und ihre Schaufeln werden so konzipiert, dass sie im Falle von Schäden oder Verschleiß relativ leicht ausgetauscht oder repariert werden können. Dies ist besonders wichtig, da der Austausch oder die Reparatur von Schaufeln in einer laufenden Turbine kostspielig und zeitaufwendig sein kann.
Zusammenfassend lässt sich sagen, dass die Stufen in einer Dampfturbine weit mehr sind als nur mechanische Komponenten. Sie sind das Herzstück des Energieumwandlungsprozesses und bestimmen maßgeblich die Effizienz, Leistung und Lebensdauer der gesamten Turbine. Durch die präzise Gestaltung der Lauf- und Leitschaufeln, die sorgfältige Auswahl der Materialien und die Berücksichtigung aller thermodynamischen und mechanischen Aspekte wird sichergestellt, dass die Dampfturbine ihre Aufgabe über einen langen Zeitraum zuverlässig erfüllt. Die komplexe Interaktion zwischen den Stufen, der Dampfströmung und den Betriebsbedingungen zeigt die herausragende Bedeutung der Stufen in der modernen Dampfturbinentechnologie.
Lauf- und Leitschaufeln in einer Dampfturbine

Ein besonders wichtiger Aspekt bei der Auslegung der Stufen in einer Dampfturbine ist die Anpassung an die spezifischen Betriebsbedingungen, die durch den thermodynamischen Kreislauf vorgegeben werden. Die Effizienz einer Dampfturbine hängt maßgeblich davon ab, wie gut die Stufen den Energieinhalt des Dampfs nutzen können, während sie die auftretenden Verluste minimieren. Zu diesen Verlusten zählen unter anderem Reibungsverluste, Stoßverluste, Sekundärströmungsverluste und Wärmeverluste. Um diese zu verringern, wird jedes Detail der Stufen – von der Form der Schaufeln bis zur Strömungsführung – präzise optimiert.
Die Leitschaufeln einer Stufe haben die Aufgabe, die Strömungsgeschwindigkeit und -richtung des Dampfs so anzupassen, dass die nachfolgenden Laufschaufeln die maximale Energie aufnehmen können. Dies erfolgt durch die Umwandlung eines Teils der thermischen Energie des Dampfs in kinetische Energie. Diese kinetische Energie wird dann in den Laufschaufeln in mechanische Energie umgewandelt, die die Welle der Turbine in Drehung versetzt. Die Gestaltung der Schaufeln folgt dabei aerodynamischen Prinzipien, wobei modernste Simulationstechnologien eingesetzt werden, um den Dampfstrom möglichst verlustfrei zu gestalten. Hierbei kommen rechnergestützte Strömungsmechanik (CFD – Computational Fluid Dynamics) und experimentelle Prüfverfahren zum Einsatz, um die Strömungsverhältnisse und die Energieübertragung genau zu analysieren und zu verbessern.
Ein weiteres wichtiges Kriterium bei der Auslegung der Stufen ist die Anpassung an die sich verändernden Parameter des Dampfs im Verlauf seines Wegs durch die Turbine. In den Hochdruckstufen, in denen der Dampf mit sehr hohen Druck- und Temperaturwerten ankommt, müssen die Schaufeln extrem widerstandsfähig gegenüber mechanischen Belastungen und thermischen Spannungen sein. Hierbei kommen Hochleistungswerkstoffe wie legierte Stähle oder Nickelbasislegierungen zum Einsatz, die speziell für den Betrieb unter diesen Bedingungen entwickelt wurden. Die Geometrie der Schaufeln in diesen Stufen ist auf eine hohe Energieumwandlung bei maximaler Strömungskontrolle ausgelegt.
In den Mitteldruck- und Niederdruckstufen, wo der Dampf bereits einen Großteil seines Energieinhalts abgegeben hat, steigt das spezifische Volumen des Dampfs stark an. Das bedeutet, dass der Dampf größere Strömungsquerschnitte benötigt, um ungehindert durch die Turbine zu strömen. Dies erfordert Schaufeln mit zunehmender Länge, insbesondere in den Niederdruckstufen, die oft die größten Schaufeln einer Dampfturbine aufweisen. Diese langen Schaufeln müssen nicht nur die Strömung effizient lenken, sondern auch mechanisch stabil genug sein, um der Zentrifugalkraft und den durch den Dampf erzeugten Kräften standzuhalten. Hier werden oft innovative Konstruktionen wie aerodynamische Profilierungen und Dämpfungselemente eingesetzt, um Schwingungen zu minimieren und die Lebensdauer der Schaufeln zu verlängern.
Ein weiterer Faktor, der die Auslegung der Stufen beeinflusst, ist die Gefahr der Feuchtigkeitsbildung im Dampf. Insbesondere in den Niederdruckstufen, in denen der Dampf nahe an die Sättigungsgrenze expandiert, kann es zur Kondensation kommen. Die entstehenden Wassertropfen können durch ihre hohe Geschwindigkeit Schäden an den Schaufeln verursachen, ein Phänomen, das als Erosion bezeichnet wird. Um diesem Problem entgegenzuwirken, werden spezielle Tropfenabscheider integriert, und die Schaufeln werden mit verschleißfesten Materialien oder Beschichtungen versehen, die die Lebensdauer der Komponenten erhöhen.
Neben der aerodynamischen und thermodynamischen Optimierung spielt auch die mechanische Stabilität der Turbine eine entscheidende Rolle. Während des Betriebs unterliegen die Schaufeln nicht nur den Kräften des strömenden Dampfs, sondern auch der Zentrifugalkraft, die durch die Rotation der Turbine entsteht. Diese Kräfte können Spannungen erzeugen, die langfristig zu Materialermüdung führen. Um dies zu verhindern, werden moderne Fertigungstechniken wie Präzisionsguss, Schmieden und additive Fertigung (3D-Druck) eingesetzt, um Schaufeln mit hoher struktureller Integrität und minimalen Fehlstellen zu produzieren. Darüber hinaus werden Schaufeln häufig mit Verstärkungen wie sogenannten “Shrouds” (Schaufelkopfbändern) ausgestattet, die die Stabilität erhöhen und Schwingungen reduzieren.
Die fortschreitende Entwicklung der Dampfturbinentechnologie hat auch zur Einführung von innovativen Konzepten wie den sogenannten “Lastverteilungsstufen” geführt. Diese Stufen sind so ausgelegt, dass sie die Belastung zwischen den einzelnen Schaufeln optimal verteilen, was zu einer gleichmäßigeren Abnutzung und einer verbesserten Betriebsstabilität führt. Solche Innovationen ermöglichen es, die Wartungsintervalle zu verlängern und die Zuverlässigkeit der Turbine zu steigern.
Zusammenfassend lässt sich sagen, dass die Stufen in einer Dampfturbine ein hochkomplexes Zusammenspiel aus thermodynamischen, aerodynamischen und mechanischen Faktoren darstellen. Jede Stufe ist individuell auf ihren Beitrag zum Energieumwandlungsprozess ausgelegt, wobei höchste Präzision und technologische Expertise erforderlich sind. Die Optimierung der Lauf- und Leitschaufeln trägt entscheidend dazu bei, die Effizienz und Langlebigkeit der Turbine zu maximieren, und stellt einen zentralen Schwerpunkt in der Entwicklung moderner Dampfturbinen dar.
Leitschaufeln

Leitschaufeln sind ein zentraler Bestandteil von Dampfturbinen und übernehmen die wichtige Aufgabe, den Dampfstrom gezielt zu lenken und ihn optimal auf die nachfolgenden Laufschaufeln auszurichten. Sie sind in der Regel stationär angeordnet und dienen dazu, den Dampf mit der richtigen Geschwindigkeit und dem passenden Winkel auf die beweglichen Laufschaufeln zu leiten. Durch diese präzise Ausrichtung wird eine maximale Energieübertragung vom Dampf auf die Turbinenwelle erreicht, was entscheidend für die Effizienz der gesamten Turbine ist. Leitschaufeln werden so konstruiert, dass sie den Druck und die Temperatur des eintretenden Dampfs in kinetische Energie umwandeln, indem sie den Dampf beschleunigen und dabei die Strömungsverluste minimieren.
Ihre Geometrie und Anordnung spielen eine wesentliche Rolle, um die Strömungseigenschaften des Dampfs zu optimieren und Turbulenzen oder unerwünschte Druckverluste zu vermeiden. Sie müssen dabei hohen thermischen Belastungen standhalten, da der Dampf in den ersten Stufen oft sehr hohe Temperaturen und Drücke aufweist. Hier kommen spezielle Werkstoffe wie hitzebeständige Legierungen oder beschichtete Materialien zum Einsatz, die diesen extremen Bedingungen widerstehen können. Gleichzeitig müssen die Leitschaufeln so gestaltet sein, dass sie auch mechanischen Belastungen wie durch die Strömung entstehenden Kräften oder Materialermüdung über lange Betriebszeiten hinweg standhalten.
Ein weiterer wichtiger Aspekt bei der Gestaltung der Leitschaufeln ist ihre aerodynamische Form, die darauf abzielt, die Energieverluste durch Reibung oder Stoßströmungen zu minimieren. Die Oberfläche der Schaufeln wird oft poliert oder mit speziellen Beschichtungen versehen, um den Strömungswiderstand zu verringern und die Effizienz zu erhöhen. In modernen Dampfturbinen werden zudem fortschrittliche Simulationsmethoden wie die rechnergestützte Strömungsmechanik (CFD) eingesetzt, um die Form und Position der Leitschaufeln präzise zu optimieren. Darüber hinaus können Leitschaufeln bei bestimmten Turbinenarten variabel gestaltet sein, um den Dampfstrom unter unterschiedlichen Lastbedingungen anzupassen und die Leistung der Turbine zu maximieren.
In mehrstufigen Turbinen ist die Rolle der Leitschaufeln besonders wichtig, da sie den Dampfstrom zwischen den einzelnen Stufen gleichmäßig verteilen und sicherstellen, dass jede Stufe optimal arbeitet. In den späteren Stufen, in denen der Druck des Dampfs bereits stark reduziert ist, müssen die Leitschaufeln für die stark expandierten Dampfvolumen dimensioniert sein, um weiterhin eine effiziente Strömungslenkung zu gewährleisten. Insgesamt sind Leitschaufeln essenziell für die Funktion und Effizienz einer Dampfturbine, da sie die Energie des Dampfs gezielt in eine Form umwandeln, die von den Laufschaufeln genutzt werden kann, und somit die Grundlage für den gesamten Energieumwandlungsprozess bilden.
Leitschaufeln sind eine der entscheidenden Komponenten in der Konstruktion und Funktion von Dampfturbinen, da sie die gezielte Lenkung und Steuerung des Dampfstroms übernehmen und somit den Energieübertragungsprozess ermöglichen. Ihre Hauptaufgabe besteht darin, den eintretenden Dampf so zu formen, dass er mit optimaler Geschwindigkeit, Winkel und Strömungsverteilung auf die nachfolgenden Laufschaufeln trifft, die den Dampfstrom dann in mechanische Energie umwandeln. Als feststehende Elemente einer Dampfturbine bilden sie das erste Glied in jeder Stufe und bestimmen maßgeblich, wie effizient die kinetische Energie des Dampfes genutzt wird. Die Gestaltung der Leitschaufeln ist von höchster Bedeutung, da sie die Strömungsverluste minimieren und die Effizienz des gesamten thermodynamischen Prozesses maximieren müssen.
Leitschaufeln sind so konstruiert, dass sie den Druck des Dampfs reduzieren und ihn gleichzeitig beschleunigen, indem sie die thermische Energie in kinetische Energie umwandeln. Diese Funktion ist besonders in den Hochdruckstufen von großer Bedeutung, da hier der Dampf mit extrem hohen Temperaturen und Drücken ankommt. Die Form der Leitschaufeln, oft mit einem aerodynamischen Profil, sorgt dafür, dass der Dampf gleichmäßig beschleunigt wird und keine Turbulenzen oder Strömungsabrisse entstehen, die zu Energieverlusten führen könnten. Die Geometrie der Schaufeln ist dabei exakt auf die nachfolgenden Laufschaufeln abgestimmt, sodass der Dampf den idealen Eintrittswinkel und die optimale Geschwindigkeit erreicht, um die maximale Energieübertragung sicherzustellen.
Ein weiteres wichtiges Kriterium bei der Konstruktion von Leitschaufeln ist ihre Materialauswahl. Da die Schaufeln in den Hochdruck- und Hochtemperaturbereichen der Turbine arbeiten, müssen sie extremen thermischen und mechanischen Belastungen standhalten. Hier kommen fortschrittliche Legierungen, wie beispielsweise Nickelbasislegierungen, zum Einsatz, die hohe Festigkeit mit einer ausgezeichneten Beständigkeit gegen Oxidation und Korrosion kombinieren. Zudem werden die Schaufeln oft mit speziellen Beschichtungen versehen, die ihre Lebensdauer verlängern und ihre Widerstandsfähigkeit gegen die durch den Dampf verursachten Verschleißerscheinungen verbessern. In den späteren Stufen der Turbine, in denen der Dampf einen niedrigeren Druck und eine höhere Feuchtigkeit aufweist, können die Leitschaufeln zusätzlichen Herausforderungen ausgesetzt sein, wie der Bildung von Wassertröpfchen, die die Oberfläche der Schaufeln erodieren können. Auch hier tragen spezielle Materialien und Beschichtungen dazu bei, die Erosion zu minimieren und den Wirkungsgrad der Turbine aufrechtzuerhalten.
Neben der Materialwahl spielt auch die aerodynamische Gestaltung der Leitschaufeln eine entscheidende Rolle. Die Schaufeln müssen so geformt sein, dass sie die Strömungseigenschaften des Dampfs optimieren und dabei möglichst geringe Verluste erzeugen. Hierbei kommen moderne Simulationswerkzeuge wie die rechnergestützte Strömungsmechanik (CFD) zum Einsatz, die es ermöglichen, den Strömungsverlauf um die Schaufeln detailliert zu analysieren und zu verbessern. Diese Simulationen helfen, den idealen Krümmungsradius, die Neigung und die Oberfläche der Schaufeln zu bestimmen, um die Energieverluste durch Reibung, Stoß oder Sekundärströmungen zu minimieren. Auch die Positionierung der Leitschaufeln innerhalb der Turbinenstufe wird mithilfe solcher Technologien präzise abgestimmt, um die maximale Effizienz zu gewährleisten.
Ein weiterer wesentlicher Aspekt bei Leitschaufeln ist ihre Rolle in der Regelung und Anpassung der Dampfturbine an unterschiedliche Betriebsbedingungen. In einigen Turbinentypen, insbesondere in Kraftwerken, die flexibel auf schwankende Energieanforderungen reagieren müssen, können die Leitschaufeln verstellbar gestaltet sein. Solche variablen Leitschaufeln ermöglichen es, den Eintrittswinkel des Dampfs anzupassen und so die Leistung der Turbine zu optimieren. Diese Flexibilität ist besonders wichtig, wenn die Turbine in einem Teillastbetrieb arbeitet, da sie dabei hilft, die Effizienz auch unter suboptimalen Bedingungen aufrechtzuerhalten.
In mehrstufigen Dampfturbinen haben Leitschaufeln zusätzlich die Aufgabe, den Dampfstrom zwischen den einzelnen Stufen zu lenken und sicherzustellen, dass er gleichmäßig auf die nachfolgenden Stufen verteilt wird. Da der Dampf bei jeder Stufe einen Teil seiner Energie abgibt und dabei sein Volumen vergrößert, müssen die Leitschaufeln der späteren Stufen entsprechend angepasst sein, um die größere Dampfmenge effizient zu handhaben. Hierbei kommen oft längere und stärker gekrümmte Schaufeln zum Einsatz, die den expandierten Dampf ohne nennenswerte Verluste lenken können.
Ein kritischer Punkt bei der Konstruktion von Leitschaufeln ist die Vermeidung von Schwingungen und Materialermüdung. Während des Betriebs wirken kontinuierlich Kräfte auf die Schaufeln, die zu Schwingungen führen können. Werden diese Schwingungen nicht kontrolliert, können sie Resonanzen erzeugen, die langfristig Schäden oder gar den Ausfall der Schaufeln verursachen. Um dies zu vermeiden, werden Leitschaufeln so gestaltet, dass ihre Eigenfrequenz nicht mit den Schwingungsfrequenzen im Betrieb übereinstimmt. Zusätzlich werden sie oft durch mechanische Verbindungen oder spezielle Dämpfungssysteme stabilisiert, um ihre Lebensdauer zu erhöhen.
Zusammenfassend lässt sich sagen, dass Leitschaufeln eine essenzielle Funktion in der Dampfturbine erfüllen, indem sie die Energie des Dampfs effizient in eine Form umwandeln, die von den Laufschaufeln genutzt werden kann. Ihre präzise Gestaltung, Materialauswahl und Anordnung tragen maßgeblich zur Effizienz, Langlebigkeit und Zuverlässigkeit der Turbine bei. Durch den Einsatz moderner Technologien in der Entwicklung und Fertigung sowie durch fortlaufende Innovationen, wie verstellbare Leitschaufeln oder verschleißresistente Materialien, wird ihre Leistung kontinuierlich verbessert. Leitschaufeln sind damit ein unverzichtbarer Bestandteil moderner Dampfturbinentechnologie und ein zentraler Faktor für die Optimierung der Energieumwandlung in industriellen und energetischen Anwendungen.
Laufschaufeln

Laufschaufeln sind die zentralen beweglichen Komponenten in einer Dampfturbine, die die Aufgabe haben, die kinetische Energie des durch die Leitschaufeln gelenkten Dampfs aufzunehmen und in mechanische Rotationsenergie umzuwandeln, die letztlich über die Turbinenwelle abgeführt wird. Diese Rotationsenergie wird in den meisten Fällen zur Stromerzeugung oder zur mechanischen Arbeit in industriellen Prozessen genutzt. Die Laufschaufeln sind so konstruiert, dass sie den Dampf mit maximaler Effizienz aufnehmen und gleichzeitig die auftretenden Kräfte und Belastungen gleichmäßig verteilen. Sie sind radial an einem Laufrad oder einer Turbinenwelle befestigt und bilden zusammen mit den Leitschaufeln die Stufen der Dampfturbine, die die Energie des Dampfs schrittweise abbauen und nutzbar machen. Ihre Form und Ausrichtung sind präzise abgestimmt, um die Strömungsführung des Dampfs zu optimieren und Verluste durch Turbulenzen, Stoß oder Reibung zu minimieren. Die aerodynamische Gestaltung der Laufschaufeln ist entscheidend für die Effizienz der Energieumwandlung und hängt von der Turbinenart ab. In Impulsturbinen erfolgt die Energieübertragung hauptsächlich durch die Geschwindigkeit des Dampfs, der auf die Schaufeln trifft und diese in Bewegung versetzt. In Reaktionsturbinen hingegen wird die Energie sowohl durch den Druckunterschied als auch durch die Geschwindigkeit des Dampfs auf die Schaufeln übertragen, sodass hier eine gleichmäßigere Energieübertragung stattfindet.
Die Materialien, aus denen Laufschaufeln gefertigt werden, müssen den extremen Betriebsbedingungen in einer Dampfturbine standhalten. Sie sind hohen Temperaturen, hohem Druck und mechanischen Belastungen durch die Rotationsbewegung sowie der Krafteinwirkung des Dampfs ausgesetzt. Häufig kommen hitzebeständige und korrosionsbeständige Legierungen wie Stähle oder Nickelbasislegierungen zum Einsatz, die eine hohe Festigkeit mit einer langen Lebensdauer kombinieren. Besonders in den Hochdruckstufen, in denen der Dampf bei Temperaturen von über 500 °C und Drücken von mehreren hundert bar arbeitet, müssen die Laufschaufeln speziell behandelt oder beschichtet sein, um Oxidation und Verschleiß zu widerstehen. Neben der Materialwahl spielt auch die Fertigungstechnologie eine wichtige Rolle. Moderne Fertigungsmethoden wie Präzisionsguss oder additive Fertigung (3D-Druck) ermöglichen es, Laufschaufeln mit komplexen aerodynamischen Profilen und hoher struktureller Integrität herzustellen. Diese Verfahren tragen dazu bei, die Leistungsfähigkeit der Schaufeln zu maximieren und gleichzeitig ihre Lebensdauer zu verlängern.
Ein besonderes Merkmal von Laufschaufeln in den mittleren und niedrigeren Druckstufen ist ihre zunehmende Länge. Da der Dampf während des Expansionsprozesses an Druck verliert, gleichzeitig aber sein Volumen stark zunimmt, müssen die Laufschaufeln dieser Volumenänderung angepasst werden. Längere Schaufeln ermöglichen es, den expandierten Dampf effizient zu lenken, ohne dass es zu erheblichen Strömungsverlusten kommt. Diese längeren Schaufeln sind jedoch größeren Zentrifugalkräften ausgesetzt, die durch die Rotation der Turbine entstehen. Um diese Belastungen zu bewältigen, werden die Schaufeln oft mit Verstärkungen wie Bändern oder mechanischen Verbindungen zwischen den Schaufelspitzen ausgestattet. Diese Konstruktionen reduzieren nicht nur die Schwingungen, die durch die Zentrifugalkräfte entstehen, sondern tragen auch zur Stabilität des gesamten Schaufelkranzes bei. Schwingungen stellen eine der größten Herausforderungen bei Laufschaufeln dar, da sie Resonanzeffekte auslösen können, die langfristig zu Materialermüdung oder sogar zum Versagen der Schaufeln führen können. Die Konstruktion der Schaufeln berücksichtigt daher die Eigenfrequenzen und stellt sicher, dass diese nicht mit den Betriebsfrequenzen der Turbine übereinstimmen. Zusätzlich können Dämpfungssysteme eingesetzt werden, um die durch die Rotation entstehenden Vibrationen zu reduzieren.
Die aerodynamische Gestaltung der Laufschaufeln spielt eine wesentliche Rolle bei der Effizienz der Turbine. Die Strömungsprofile der Schaufeln sind so ausgelegt, dass sie den Dampf gleichmäßig aufnehmen und entlang ihrer Oberfläche lenken, ohne dass es zu Strömungsabrissen oder Turbulenzen kommt, die Energieverluste verursachen könnten. Die Oberfläche der Schaufeln wird oft poliert oder mit speziellen Beschichtungen versehen, um die Reibung zu minimieren und die Beständigkeit gegen Erosion zu erhöhen. Insbesondere in den Niederdruckstufen, in denen der Dampf eine hohe Feuchtigkeit aufweist, können Wassertröpfchen auf den Schaufeln zu Erosionsschäden führen. Um diesem Problem entgegenzuwirken, werden die Schaufeln mit verschleißfesten Materialien oder Tropfenabweiser-Beschichtungen versehen. Darüber hinaus kommen in modernen Turbinen oft innovative Technologien wie Tropfenabscheider oder spezielle Oberflächenbehandlungen zum Einsatz, die die Auswirkungen der Tropfenbildung minimieren und die Lebensdauer der Schaufeln verlängern.
Ein weiterer entscheidender Faktor bei der Gestaltung von Laufschaufeln ist ihre Anpassung an die spezifischen Betriebsbedingungen der Dampfturbine. In vielen Anwendungen, wie beispielsweise in Kraftwerken, die auf wechselnde Energiebedarfe reagieren müssen, spielen Laufschaufeln eine wichtige Rolle bei der Regelung und Anpassung der Turbine an verschiedene Lastbedingungen. Dies geschieht oft in Kombination mit den Leitschaufeln, die den Dampfstrom auf die Laufschaufeln lenken. Die Präzision, mit der Laufschaufeln gefertigt und montiert werden, ist entscheidend für die Leistung und Zuverlässigkeit der Turbine. Fehler in der Geometrie oder Ausrichtung können erhebliche Effizienzverluste verursachen und zu einem erhöhten Verschleiß oder Ausfällen führen. Aus diesem Grund werden Laufschaufeln während der Herstellung und Montage gründlich geprüft und getestet, um sicherzustellen, dass sie den hohen Anforderungen des Betriebs gerecht werden.
Zusammenfassend sind Laufschaufeln das zentrale Element in der Energieumwandlung einer Dampfturbine. Sie spielen eine Schlüsselrolle bei der Aufnahme der kinetischen Energie des Dampfs und ihrer Umwandlung in mechanische Energie. Durch ihre präzise Gestaltung, Materialauswahl und Anpassung an die Betriebsbedingungen tragen sie maßgeblich zur Effizienz, Zuverlässigkeit und Langlebigkeit der Turbine bei. Moderne Fertigungstechnologien, fortschrittliche aerodynamische Designs und innovative Materialien haben die Leistungsfähigkeit von Laufschaufeln kontinuierlich verbessert, was es ermöglicht, den steigenden Anforderungen an Dampfturbinen in der Energie- und Industriebranche gerecht zu werden.
Laufschaufeln sind untrennbar mit der Funktionsweise und Effizienz von Dampfturbinen verbunden und repräsentieren das zentrale Element der Energieübertragung in diesem System. Sie sind so ausgelegt, dass sie den durch die Leitschaufeln gelenkten Dampf optimal aufnehmen und dessen kinetische und thermische Energie in Rotationsenergie umwandeln, die durch die Welle abgeführt wird. Die gesamte Leistung der Turbine hängt maßgeblich von der Fähigkeit der Laufschaufeln ab, diese Energie mit minimalen Verlusten und maximaler Effizienz zu nutzen. In einer mehrstufigen Dampfturbine kommen Laufschaufeln in jeder Stufe vor, wobei sie spezifisch für die Druck- und Temperaturverhältnisse sowie die Strömungscharakteristik des Dampfs in der jeweiligen Stufe ausgelegt sind. Dabei unterscheidet sich ihre Gestaltung je nach Einsatz in Hochdruck-, Mitteldruck- oder Niederdruckstufen deutlich.
In den Hochdruckstufen, in denen der Dampf sehr hohe Geschwindigkeiten und Temperaturen erreicht, ist die Geometrie der Laufschaufeln auf die präzise Aufnahme dieser Energie abgestimmt. Sie sind vergleichsweise kurz und kompakt, um den hohen mechanischen Belastungen, die durch die extremen Drücke und Temperaturen entstehen, standzuhalten. Diese Schaufeln werden aus speziellen Hochleistungslegierungen gefertigt, die eine hohe Temperaturbeständigkeit sowie eine ausgezeichnete mechanische Festigkeit bieten. Hinzu kommen oft zusätzliche Beschichtungen, die den Schutz vor Oxidation und Korrosion erhöhen. Die aerodynamische Gestaltung der Schaufeln ist in dieser Phase besonders kritisch, da der Dampf mit hoher Geschwindigkeit eintritt und selbst kleine Unregelmäßigkeiten in der Schaufeloberfläche zu erheblichen Energieverlusten führen können. Der Fokus liegt daher auf einem optimierten Strömungsprofil, das den Dampf gleichmäßig entlang der Schaufelfläche leitet und Turbulenzen vermeidet.
Mit der Expansion des Dampfs in den späteren Stufen der Turbine verändern sich die Bedingungen erheblich. Der Druck nimmt ab, während das spezifische Volumen des Dampfs stark zunimmt. Dies erfordert eine Anpassung der Laufschaufeln an die neuen Strömungsbedingungen. Die Schaufeln in den Mitteldruck- und Niederdruckstufen sind deutlich länger als die in den Hochdruckstufen, um das größere Dampfvolumen effizient zu verarbeiten. Diese längeren Schaufeln unterliegen jedoch größeren Zentrifugalkräften und müssen daher besonders stabil konstruiert sein. Häufig werden sie mit Verstärkungsbändern an den Schaufelspitzen verbunden, um die mechanische Belastung zu reduzieren und die Stabilität des gesamten Schaufelkranzes zu gewährleisten. Gleichzeitig werden fortschrittliche Simulationstechniken wie die Finite-Elemente-Analyse eingesetzt, um die Struktur der Schaufeln zu optimieren und Schwachstellen zu vermeiden.
Ein weiteres bedeutendes Konstruktionsmerkmal der Laufschaufeln ist ihre Fähigkeit, Schwingungen zu kontrollieren. Im Betrieb wirken hohe dynamische Kräfte auf die Schaufeln, die Resonanzeffekte hervorrufen können, wenn die Eigenfrequenz der Schaufeln mit den Schwingungsfrequenzen der Turbine übereinstimmt. Um dies zu vermeiden, werden Laufschaufeln so gestaltet, dass sie außerhalb der kritischen Resonanzfrequenzen arbeiten. Darüber hinaus kommen spezielle Dämpfungstechnologien zum Einsatz, um unerwünschte Schwingungen zu minimieren und die Lebensdauer der Schaufeln zu erhöhen. Schwingungskontrolle ist besonders in den Niederdruckstufen wichtig, wo die längeren Schaufeln anfälliger für Materialermüdung durch oszillierende Kräfte sind.
In modernen Dampfturbinen spielt die Oberflächenbehandlung der Laufschaufeln eine entscheidende Rolle bei der Effizienzsteigerung. Polierte oder speziell beschichtete Oberflächen verringern den Strömungswiderstand und tragen dazu bei, den Wirkungsgrad zu verbessern. Diese Beschichtungen sind oft auch notwendig, um die Schaufeln vor den erosiven und korrosiven Effekten des feuchten Dampfes zu schützen, insbesondere in den Niederdruckstufen. Hier kann es durch die Kondensation von Wassertröpfchen zu einer sogenannten Tropfenerosion kommen, die die Schaufeloberfläche beschädigt und die Effizienz der Turbine verringert. Um dies zu verhindern, werden fortschrittliche Materialien und innovative Beschichtungstechniken verwendet, die die Schaufeln widerstandsfähiger gegen diese Einflüsse machen.
Die Präzision in der Herstellung und Montage der Laufschaufeln ist ein weiterer kritischer Aspekt ihrer Leistung. Schon geringste Abweichungen in der Geometrie oder Ausrichtung der Schaufeln können zu signifikanten Effizienzverlusten führen. Deshalb kommen in der Fertigung hochmoderne Technologien wie der Präzisionsguss und der 3D-Druck zum Einsatz, die eine exakte Reproduktion komplexer Schaufelprofile ermöglichen. Nach der Fertigung werden die Schaufeln umfassend getestet, um sicherzustellen, dass sie den hohen Anforderungen im Betrieb standhalten können. Diese Tests umfassen nicht nur mechanische Belastungstests, sondern auch thermische Prüfungen und Strömungstests, um die Leistung der Schaufeln unter realen Betriebsbedingungen zu überprüfen.
Ein weiterer wesentlicher Punkt ist die Integration der Laufschaufeln in das Gesamtsystem der Turbine. Sie müssen nahtlos mit den Leitschaufeln interagieren, um eine gleichmäßige Energieübertragung und Strömungsführung zu gewährleisten. Dies erfordert eine präzise Abstimmung der Schaufelgeometrie und -position innerhalb der Turbinenstufe. Zudem müssen die Laufschaufeln so ausgelegt sein, dass sie unterschiedliche Betriebsbedingungen, wie Lastwechsel oder Teillastbetrieb, effizient bewältigen können. In vielen modernen Turbinen wird dies durch den Einsatz fortschrittlicher Regelungstechniken und variabler Komponenten erreicht, die die Anpassung der Strömungsverhältnisse an die aktuellen Betriebsanforderungen ermöglichen.
Insgesamt sind Laufschaufeln nicht nur ein zentrales Element der Dampfturbine, sondern auch ein Paradebeispiel für die Synergie von Ingenieurwissenschaften, Materialtechnologie und Aerodynamik. Ihre kontinuierliche Weiterentwicklung ist entscheidend, um die Leistungsfähigkeit und Effizienz von Dampfturbinen weiter zu steigern und sie an die wachsenden Anforderungen der Energie- und Industriebranche anzupassen. Von ihrer Gestaltung über ihre Fertigung bis hin zu ihrem Einsatz im Betrieb spiegeln Laufschaufeln die höchsten Standards moderner Technik wider und bleiben ein unverzichtbarer Bestandteil jeder Dampfturbine.
Laufschaufeln sind nicht nur wesentliche Komponenten zur Energieumwandlung in Dampfturbinen, sondern auch entscheidende Elemente für die Zuverlässigkeit und Betriebssicherheit des gesamten Systems. Ihre Funktion, den vom Dampf übertragenen Impuls in Rotationsbewegung umzuwandeln, setzt voraus, dass sie sowohl mechanisch als auch thermisch extrem belastbar sind. Die Optimierung der Laufschaufeln hat in der modernen Turbinenentwicklung einen hohen Stellenwert, da sie direkten Einfluss auf die Effizienz, Lebensdauer und Wirtschaftlichkeit der Turbine hat. Besonders bei Hochleistungsturbinen, die in Kraftwerken oder industriellen Prozessen eingesetzt werden, ist eine präzise und robuste Auslegung der Laufschaufeln entscheidend, um den steigenden Anforderungen hinsichtlich Energieausbeute und Zuverlässigkeit gerecht zu werden.
Ein grundlegender Aspekt bei der Konstruktion von Laufschaufeln ist das Verständnis der komplexen Strömungsmechanik innerhalb der Turbine. Der Dampf, der auf die Schaufeln trifft, besitzt eine hohe Geschwindigkeit, die in Impulsturbinen eine dominierende Rolle spielt, während in Reaktionsturbinen der Druckabfall über die Schaufeln ebenfalls eine signifikante Energiequelle darstellt. In beiden Fällen muss die Schaufel so gestaltet sein, dass sie den Dampfstrom effizient aufnimmt und leitet, ohne dass es zu nennenswerten Energieverlusten kommt. Die aerodynamische Form der Laufschaufeln ist daher ein zentrales Forschungs- und Entwicklungsfeld. Hierbei werden computergestützte Simulationsmethoden wie Computational Fluid Dynamics (CFD) verwendet, um den Strömungsverlauf um die Schaufeln zu analysieren und zu optimieren. Diese Technologien ermöglichen es, die Geometrie der Schaufeln so zu gestalten, dass Turbulenzen, Stoßverluste und Reibung minimiert werden, was direkt zu einer Steigerung der thermodynamischen Effizienz der Turbine führt.
Neben der aerodynamischen Gestaltung spielt die Materialauswahl eine entscheidende Rolle für die Leistung und Lebensdauer von Laufschaufeln. Die extremen Betriebsbedingungen, unter denen sie arbeiten, erfordern Materialien mit außergewöhnlichen mechanischen und thermischen Eigenschaften. In den Hochdruckstufen, wo der Dampf Temperaturen von über 600 °C und Drücke von mehreren hundert Bar erreicht, kommen fortschrittliche Superlegierungen zum Einsatz, die eine hohe Festigkeit mit einer hervorragenden Oxidations- und Korrosionsbeständigkeit kombinieren. Diese Materialien, oft auf Nickel- oder Kobaltbasis, werden zusätzlich durch Wärmebehandlung oder Beschichtungen weiter verbessert, um ihre Beständigkeit gegen Verschleiß und Ermüdung zu erhöhen. In den Niederdruckstufen, wo die Schaufeln längeren Dampfströmen und höheren Feuchtigkeitsgehalten ausgesetzt sind, müssen sie besonders widerstandsfähig gegen Erosion sein, die durch kondensierte Wassertropfen verursacht wird. Hier werden spezielle Schutzbeschichtungen wie Hartmetalle oder keramische Schichten eingesetzt, um die Erosionsbeständigkeit zu verbessern und die Standzeit der Schaufeln zu verlängern.
Ein weiterer wichtiger Punkt bei der Konstruktion von Laufschaufeln ist die Bewältigung der enormen Zentrifugalkräfte, die durch die Rotation der Turbine entstehen. Insbesondere in den Niederdruckstufen, wo die Schaufeln oft Längen von über einem Meter erreichen, wirken enorme Kräfte auf die Schaufelbasis und die Befestigungspunkte am Rotor. Um diesen Belastungen standzuhalten, werden die Schaufeln mit präzisen mechanischen Verbindungssystemen ausgestattet, die eine sichere und dauerhafte Fixierung gewährleisten. Zusätzlich werden Maßnahmen wie das Anbringen von Schaufelbändern oder Dämpfungselementen an den Spitzen der Schaufeln ergriffen, um Schwingungen zu kontrollieren und die strukturelle Integrität des Schaufelkranzes zu gewährleisten. Die Resonanzvermeidung ist ein kritischer Aspekt der Konstruktion, da Resonanzeffekte zu schweren Schäden oder sogar zum Versagen der Schaufeln führen können. Durch den Einsatz fortschrittlicher Berechnungsmethoden und Tests wird sichergestellt, dass die Schaufeln außerhalb ihrer kritischen Frequenzen betrieben werden.
Die Fertigung von Laufschaufeln ist ein hochpräziser Prozess, der modernste Technologien und strengste Qualitätskontrollen erfordert. Technologien wie der Präzisionsguss oder die additive Fertigung (3D-Druck) ermöglichen die Herstellung komplexer Schaufelgeometrien mit minimalen Abweichungen. Nach der Fertigung durchlaufen die Schaufeln umfangreiche Prüfverfahren, einschließlich zerstörungsfreier Tests wie Ultraschall- oder Röntgenprüfungen, um sicherzustellen, dass sie frei von Materialfehlern sind. Zudem werden sie auf ihre mechanischen, thermischen und strömungstechnischen Eigenschaften getestet, um sicherzustellen, dass sie den hohen Anforderungen des Betriebs gewachsen sind.
Die Integration von Laufschaufeln in die Turbine erfordert ebenfalls höchste Präzision. Ihre Positionierung und Ausrichtung müssen exakt mit den Leitschaufeln abgestimmt sein, um eine gleichmäßige Energieübertragung und Strömungsführung zu gewährleisten. Selbst geringfügige Abweichungen können zu erheblichen Wirkungsgradverlusten führen, da sie Turbulenzen oder ungleichmäßige Belastungen verursachen können. In der Praxis wird diese Abstimmung durch den Einsatz präziser Messtechniken und computergestützter Montageverfahren sichergestellt, die eine hohe Genauigkeit und Wiederholbarkeit gewährleisten.
Die fortlaufende Weiterentwicklung von Laufschaufeln ist entscheidend, um den steigenden Anforderungen an Effizienz, Zuverlässigkeit und Umweltfreundlichkeit gerecht zu werden. Neue Materialien, innovative Fertigungstechnologien und fortschrittliche Simulationsmethoden tragen dazu bei, die Leistungsfähigkeit von Laufschaufeln kontinuierlich zu verbessern. Gleichzeitig werden sie an spezifische Anforderungen wie den Betrieb unter Teillastbedingungen oder die Integration in hybride Energiesysteme angepasst. Diese Fortschritte machen Laufschaufeln zu einem Schlüsselfaktor für die zukünftige Entwicklung von Dampfturbinen und deren Rolle in einer nachhaltigen Energieversorgung.
Die Laufschaufeln der Dampfturbine repräsentieren nicht nur technologische Präzision, sondern auch die Evolution eines jahrzehntealten Ingenieurwissens, das sich stetig weiterentwickelt hat, um den wachsenden Herausforderungen moderner Energiesysteme gerecht zu werden. Ihre Rolle geht über die reine Energieumwandlung hinaus, da sie entscheidend für die Effizienz, Stabilität und Lebensdauer der gesamten Turbine sind. Dies macht sie zu einem zentralen Punkt der Forschung und Entwicklung, insbesondere im Hinblick auf die Optimierung von Wirkungsgraden, die Senkung von Emissionen und die Anpassung an neue Energiequellen und Betriebsbedingungen.
Ein entscheidender Aspekt bei der Entwicklung moderner Laufschaufeln ist die Bewältigung von Teillast- und Lastwechselbedingungen, wie sie in der heutigen Energieversorgung immer häufiger auftreten. Mit dem zunehmenden Einsatz erneuerbarer Energien wie Wind- und Solarenergie, die stark schwankende Einspeiseprofile aufweisen, müssen Dampfturbinen flexibler und schneller auf wechselnde Anforderungen reagieren können. Diese Flexibilität erfordert eine neue Generation von Laufschaufeln, die nicht nur für maximale Effizienz im Dauerbetrieb, sondern auch für häufige Lastwechsel und Teillastbedingungen ausgelegt sind. Dies wird durch die Verwendung adaptiver Designs erreicht, die beispielsweise variierende Winkel oder modifizierbare Strömungsprofile bieten können. Kombiniert mit fortschrittlichen Steuerungssystemen, ermöglichen solche Lösungen eine präzise Anpassung der Schaufeln an die jeweiligen Betriebsbedingungen und tragen so zu einer Reduktion von Verschleiß und Energieverlusten bei.
Die Integration von digitalen Technologien und der sogenannten Digital Twin-Technologie stellt einen weiteren Meilenstein in der Entwicklung und dem Betrieb von Laufschaufeln dar. Hierbei wird ein virtuelles Modell der Turbine und ihrer Schaufeln erstellt, das die physikalischen Eigenschaften und Betriebsbedingungen in Echtzeit simuliert. Diese Technologie ermöglicht eine genauere Überwachung der Leistung und des Zustands der Laufschaufeln, indem Daten aus Sensoren in der Turbine gesammelt und analysiert werden. So können potenzielle Probleme, wie Materialermüdung oder Strömungsverluste, frühzeitig erkannt und behoben werden, bevor sie zu schwerwiegenden Ausfällen führen. Darüber hinaus können auf Basis dieser Daten optimierte Wartungspläne entwickelt werden, die sowohl die Betriebskosten senken als auch die Lebensdauer der Schaufeln verlängern.
Auch die Forschung an neuen Materialien bleibt ein zentrales Feld bei der Weiterentwicklung von Laufschaufeln. Neben den bereits weit verbreiteten Superlegierungen auf Nickel- oder Kobaltbasis wird an der Entwicklung neuer Werkstoffe gearbeitet, die noch höhere Temperaturen und Belastungen standhalten können. Ein Beispiel hierfür sind keramische Matrixkomposite (CMC), die nicht nur leichter als herkömmliche Metalle sind, sondern auch extrem hohe Temperaturen ohne Verlust ihrer mechanischen Eigenschaften aushalten können. Diese Materialien könnten in Zukunft die Effizienzgrenzen von Dampfturbinen weiter verschieben und ihre Umweltverträglichkeit verbessern, da sie höhere Wirkungsgrade und geringere Emissionen ermöglichen. Gleichzeitig wird an der Entwicklung intelligenter Materialien gearbeitet, die ihre Eigenschaften an wechselnde Betriebsbedingungen anpassen können, etwa durch eine Veränderung ihrer Oberflächenstruktur oder ihrer thermischen Leitfähigkeit.
Ein weiterer Fokus liegt auf der Reduzierung von Energieverlusten durch Strömungsphänomene wie Turbulenzen oder Leckagen. Neben der Verbesserung der aerodynamischen Profile der Schaufeln wird auch an der Minimierung der Spaltverluste zwischen den Schaufeln und dem Gehäuse gearbeitet. Hier kommen fortschrittliche Dichtsysteme wie Labyrinth- oder Bürstendichtungen zum Einsatz, die den Dampfverlust in diesen kritischen Bereichen erheblich reduzieren können. Zusätzlich werden die Schaufelspitzen mit speziellen Beschichtungen versehen, die den Verschleiß in diesen hoch beanspruchten Bereichen minimieren und gleichzeitig die Reibung reduzieren.
Die Anforderungen an die Nachhaltigkeit moderner Energieerzeugungssysteme haben auch dazu geführt, dass Laufschaufeln zunehmend so gestaltet werden, dass sie eine längere Lebensdauer und eine einfachere Wiederaufbereitung bieten. Dies wird durch modulare Designs unterstützt, bei denen einzelne Komponenten der Schaufeln bei Bedarf ausgetauscht oder recycelt werden können, ohne die gesamte Turbine stilllegen zu müssen. Solche Designs tragen nicht nur zur Kostensenkung bei, sondern auch zur Reduktion von Ressourcenverbrauch und Abfall, was sie zu einer Schlüsselstrategie für eine nachhaltige Zukunft der Energieerzeugung macht.
Zusammenfassend lässt sich sagen, dass Laufschaufeln in Dampfturbinen weit mehr sind als nur mechanische Bauteile. Sie verkörpern eine hochentwickelte Technologie, die sowohl auf präzise Ingenieurkunst als auch auf tiefgehendes Wissen in Strömungsmechanik, Materialwissenschaft und Thermodynamik basiert. Ihre kontinuierliche Weiterentwicklung ist entscheidend, um den steigenden Anforderungen an Effizienz, Flexibilität und Nachhaltigkeit gerecht zu werden. Ob in traditionellen fossilen Kraftwerken, modernen kombinierten Gas-Dampf-Kraftwerken oder innovativen Anwendungen wie solarthermischen Kraftwerken und Geothermieanlagen – Laufschaufeln bleiben eine Schlüsseltechnologie für die effiziente und zuverlässige Nutzung thermischer Energie. Ihr Potenzial, durch technologische Fortschritte weiter verbessert zu werden, macht sie zu einem wesentlichen Element der globalen Energiewende.
Die kontinuierliche Weiterentwicklung der Laufschaufeln in Dampfturbinen hat das Ziel, nicht nur die Effizienz zu maximieren, sondern auch die Robustheit und Anpassungsfähigkeit an immer vielfältigere Betriebsbedingungen zu erhöhen. Ein zentrales Thema ist dabei die Aerodynamik. Jede Verbesserung in der Strömungsführung durch die Laufschaufeln hat direkte Auswirkungen auf den Wirkungsgrad der Turbine. Selbst kleinste Optimierungen im Design, etwa an der Krümmung oder Oberflächenstruktur der Schaufeln, können den Energieverlust durch Reibung oder Turbulenzen signifikant reduzieren. Dies erfordert fortlaufende Forschung und Entwicklung, die durch den Einsatz modernster Simulationssoftware und strömungstechnischer Experimente unterstützt wird. Aerodynamische Optimierungen werden dabei nicht nur für konventionelle Betriebsmodi, sondern auch für extreme Bedingungen, wie sie bei Spitzenlasten oder schnellen Lastwechseln auftreten, entwickelt.
Ein weiterer wichtiger Fokus liegt auf der Minimierung von Schaufelschwingungen und der Vermeidung von Resonanzeffekten. Laufschaufeln sind durch ihre Rotationsbewegung und die Kräfte des durchströmenden Dampfs ständig hohen Belastungen ausgesetzt, die Schwingungen induzieren können. Werden diese nicht ausreichend gedämpft oder liegen sie im Bereich der Eigenfrequenzen der Schaufeln, können Resonanzphänomene auftreten, die zu Schäden oder sogar einem Totalausfall führen. Um dies zu verhindern, werden hochpräzise Schwingungsanalysen durchgeführt, und die Schaufeln werden so konstruiert, dass sie außerhalb ihrer kritischen Frequenzen arbeiten. Zudem kommen moderne Dämpfungsmethoden zum Einsatz, wie etwa Schaufelbänder oder interne Dämpfungselemente, die Schwingungen effektiv reduzieren und die Betriebssicherheit erhöhen.
Die Materialwissenschaft spielt ebenfalls eine entscheidende Rolle in der Weiterentwicklung von Laufschaufeln. Mit den steigenden Anforderungen an Wirkungsgrade und Temperaturen in Dampfturbinen müssen Materialien immer höheren thermischen und mechanischen Belastungen standhalten. Traditionelle Legierungen stoßen dabei zunehmend an ihre Grenzen, weshalb neue Werkstoffe wie Titanaluminide oder keramische Matrixkomposite in den Fokus rücken. Diese Materialien bieten nicht nur eine verbesserte Hochtemperaturbeständigkeit, sondern sind oft auch leichter, was die Zentrifugalkräfte auf die Schaufeln reduziert und die Belastung der gesamten Turbine senkt. Gleichzeitig wird intensiv an Beschichtungen geforscht, die die Oberflächen der Schaufeln vor Erosion, Korrosion und anderen Verschleißerscheinungen schützen. Besonders in den Niederdruckstufen, wo der Dampf häufig kondensiert und Wassertropfen auf die Schaufeln treffen, sind solche Schutzmechanismen essenziell, um die Lebensdauer der Komponenten zu verlängern.
Die zunehmende Digitalisierung und Automatisierung in der Energieindustrie hat auch bei Laufschaufeln neue Möglichkeiten eröffnet. Mit der Integration von Sensorik in die Schaufeln können Betriebsdaten in Echtzeit überwacht werden. Dies ermöglicht nicht nur eine genaue Analyse der Schaufelbelastungen und der Strömungsverhältnisse, sondern auch eine vorausschauende Wartung. Mithilfe von Predictive Maintenance können potenzielle Schäden frühzeitig erkannt und gezielt behoben werden, bevor es zu einem Ausfall kommt. Gleichzeitig ermöglichen digitale Zwillinge, also virtuelle Modelle der Turbine, die Simulation unterschiedlicher Betriebszustände und die Optimierung von Designs, ohne dass physische Prototypen erforderlich sind. Dies beschleunigt den Entwicklungsprozess und senkt die Kosten.
Ein weiterer Innovationsbereich ist die additive Fertigung, auch bekannt als 3D-Druck. Diese Technologie erlaubt es, Laufschaufeln mit extrem komplexen Geometrien herzustellen, die mit konventionellen Fertigungsmethoden nur schwer oder gar nicht realisierbar wären. Durch den 3D-Druck können beispielsweise interne Kühlkanäle oder besonders filigrane Strukturen direkt in die Schaufeln integriert werden, was ihre Effizienz und Funktionalität erhöht. Zudem ermöglicht der 3D-Druck eine individualisierte Produktion, bei der Schaufeln exakt an die spezifischen Anforderungen einer Turbine angepasst werden können.
Die Nachhaltigkeit spielt ebenfalls eine immer größere Rolle in der Entwicklung von Laufschaufeln. Durch den Einsatz langlebiger Materialien und effizienterer Designs wird nicht nur der Energieverbrauch der Turbine gesenkt, sondern auch der Ressourcenaufwand für Wartung und Ersatzteile minimiert. Darüber hinaus arbeiten viele Hersteller daran, die Recyclingfähigkeit von Schaufeln zu verbessern. Am Ende ihres Lebenszyklus sollen die verwendeten Materialien möglichst wiederverwertet werden können, um den ökologischen Fußabdruck der Turbine zu reduzieren.
In Zukunft könnten auch völlig neue Technologien die Gestaltung und Funktion von Laufschaufeln revolutionieren. Eine vielversprechende Möglichkeit sind biomimetische Ansätze, bei denen sich Ingenieure von natürlichen Strukturen, wie etwa den Flügeln von Insekten oder Vögeln, inspirieren lassen. Diese Ansätze könnten zu Schaufeln führen, die noch effizienter mit den Strömungskräften des Dampfs interagieren. Ebenso könnten intelligente Materialien und aktives Design, bei dem sich die Schaufeln während des Betriebs an veränderte Bedingungen anpassen, eine neue Ära der Dampfturbinentechnologie einläuten.
Zusammenfassend bleibt die Entwicklung von Laufschaufeln ein zentraler Treiber für Innovation in der Dampfturbinentechnik. Sie sind ein Schlüsselbauteil, dessen Optimierung weitreichende Auswirkungen auf die Effizienz, Zuverlässigkeit und Umweltverträglichkeit von Kraftwerken hat. Ihre fortwährende Verbesserung ist nicht nur für die derzeitige Energieversorgung essenziell, sondern auch für die Herausforderungen der Zukunft, wie die Integration erneuerbarer Energien und die Reduktion von CO₂-Emissionen. Laufschaufeln sind somit ein Paradebeispiel für die Schnittstelle von Ingenieurskunst, Materialforschung und Digitalisierung, die das Potenzial hat, die Energieerzeugung nachhaltig zu transformieren.
Energieumwandlung
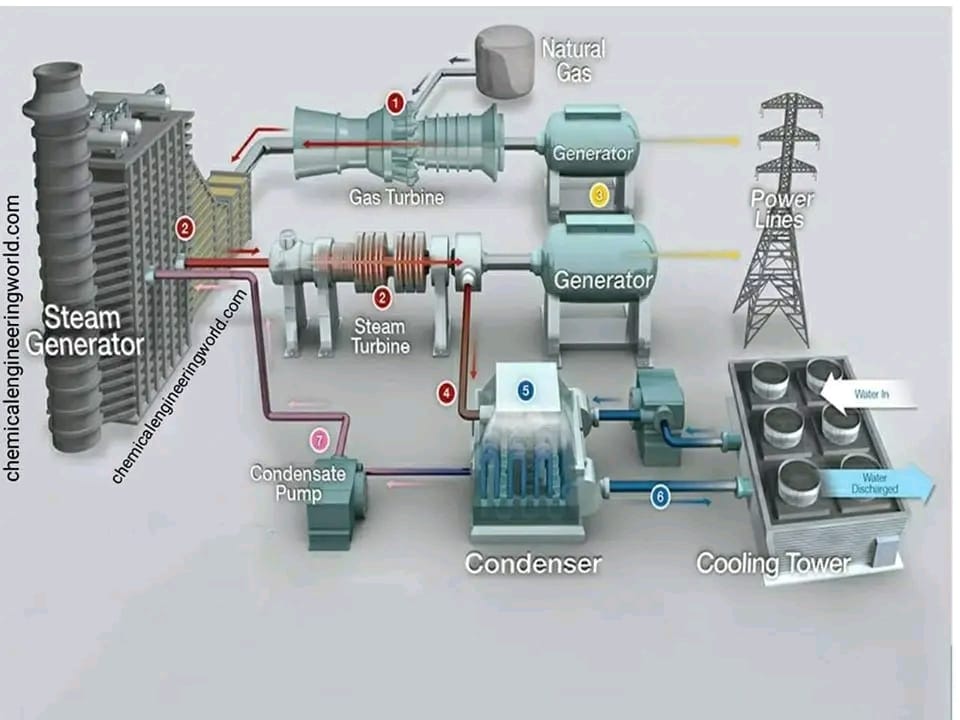
Energieumwandlung ist der Prozess, bei dem Energie von einer Form in eine andere überführt wird, um sie für verschiedene Anwendungen nutzbar zu machen. In Dampfturbinen, einem der zentralen Bestandteile der thermischen Stromerzeugung, erfolgt die Energieumwandlung durch die Umwandlung thermischer Energie des Dampfes in mechanische Energie. Dies geschieht, wenn der hochdruckdampf auf die Schaufeln der Turbine trifft und diese in Rotation versetzt. Der Dampf, der in einem Kessel durch die Verbrennung von Brennstoffen wie Kohle, Gas oder Öl erhitzt wurde, hat eine hohe thermische Energie. Diese Energie wird auf die Laufschaufeln der Turbine übertragen, die sich durch die Umströmung des Dampfes bewegen und dabei mechanische Arbeit leisten. Der rotierende Rotor, an dem die Laufschaufeln befestigt sind, ist mit einem Generator verbunden, der die mechanische Energie in elektrische Energie umwandelt. Die Umwandlung von thermischer Energie in mechanische Energie erfolgt in mehreren Schritten, beginnend mit dem Dampfdruck, der die Schaufeln der Turbine antreibt. Dabei wird ein großer Teil der thermischen Energie in kinetische Energie des Dampfes umgewandelt, die dann mechanische Arbeit verrichtet. Dieser Vorgang ist von entscheidender Bedeutung für die Effizienz eines Kraftwerks, da er bestimmt, wie gut die Turbine die zugeführte Wärmeenergie in nutzbare mechanische Energie umwandeln kann. Ein wichtiger Faktor bei der Energieumwandlung in Dampfturbinen ist die Temperatur und der Druck des Dampfs, die je nach den Eigenschaften des Kraftwerks und den verwendeten Brennstoffen variieren können. Durch die richtige Steuerung der Prozessparameter kann der Wirkungsgrad der Turbine optimiert und der Energieverlust minimiert werden. Die Umwandlung von Wärme in mechanische Energie stellt einen zentralen Schritt dar, um Elektrizität in großem Maßstab bereitzustellen und ist daher von großer Bedeutung für die Energieversorgung in vielen Industrien und Haushalten.
Die Energieumwandlung in Dampfturbinen ist ein komplexer, aber hochoptimierter Prozess, der eine Reihe von physikalischen Prinzipien wie Thermodynamik und Strömungsmechanik nutzt. Um die Umwandlung von thermischer Energie in mechanische Arbeit effizient zu gestalten, muss der Dampf durch die Turbine strömen, wobei er auf die Laufschaufeln trifft. Diese Schaufeln sind so geformt, dass sie den Dampfstrom bestmöglich aufnehmen und den Dampfimpuls effizient in eine Drehbewegung umsetzen. Die Ausrichtung und Geometrie der Schaufeln, sowohl der Leitschaufeln als auch der Laufschaufeln, spielen dabei eine entscheidende Rolle. Leitschaufeln lenken den Dampfstrom in die richtige Richtung, bevor er auf die Laufschaufeln trifft, die dann die kinetische Energie des Dampfes in mechanische Energie umwandeln. Der Dampf verliert bei der Passage durch die verschiedenen Stufen der Turbine kontinuierlich an Druck und Temperatur, wobei ein Teil der thermischen Energie in Arbeit umgewandelt wird, während der Rest als Abwärme abgeführt wird.
Ein wichtiger Aspekt in diesem Prozess ist die thermodynamische Effizienz, die durch den sogenannten Carnot-Prozess beschrieben wird, der das theoretische Maximum an Energieumwandlung beschreibt. In der Praxis wird jedoch immer ein gewisser Teil der Energie durch Reibung, Turbulenzen oder Wärmeverluste an die Umgebung verloren gehen. Die Gestaltung und der Betrieb der Dampfturbine sind daher auf eine möglichst effektive Nutzung der verfügbaren thermischen Energie ausgerichtet. Ein hoher Wirkungsgrad bedeutet, dass ein größerer Teil der zugeführten Wärmeenergie in mechanische Arbeit und letztlich in elektrische Energie umgewandelt wird. Ein weiterer Faktor, der die Effizienz beeinflusst, ist die Art und Weise, wie der Dampf nach der Expansion durch die Turbine kondensiert wird. In modernen Kraftwerken wird häufig eine Konditionierung des Dampfs erreicht, bei der der Dampf in mehreren Stufen abgekühlt und kondensiert wird, um die Energieausbeute zu maximieren.
Die Energieumwandlung in Dampfturbinen ist nicht nur auf den klassischen Betrieb von fossilen Kraftwerken beschränkt. Sie wird auch zunehmend in Kombination mit anderen Technologien verwendet, etwa in sogenannten Combined-Cycle-Kraftwerken, die eine Dampfturbine mit einer Gasturbine kombinieren, um die Effizienz weiter zu steigern. In diesem Fall wird die Abwärme der Gasturbine genutzt, um Wasser zu verdampfen und eine zusätzliche Dampfturbine zu betreiben, was den gesamten Energieumwandlungsprozess optimiert. Auch in der Nutzung erneuerbarer Energien, wie in solarthermischen Anlagen, wird Dampfturbinen-Technologie eingesetzt, um thermische Energie aus konzentriertem Sonnenlicht in mechanische und schließlich elektrische Energie umzuwandeln.
Die Umwandlung von Wärme in mechanische Arbeit stellt einen wichtigen Schritt in der modernen Energieversorgung dar. Angesichts der steigenden Nachfrage nach Energie und der Notwendigkeit, den CO₂-Ausstoß zu reduzieren, liegt der Fokus auf der Verbesserung der Energieeffizienz und der Verringerung der Verluste. Fortschritte in der Materialtechnologie, wie hochtemperaturbeständige Legierungen oder neue Fertigungsprozesse, tragen dazu bei, die Leistung von Dampfturbinen weiter zu steigern. Ein weiteres Zukunftsziel besteht darin, die Betriebskosten zu senken, indem die Lebensdauer der Turbinen verlängert und die Wartungsintervalle optimiert werden. All diese Maßnahmen tragen dazu bei, den gesamten Energieumwandlungsprozess sowohl wirtschaftlich als auch ökologisch effizienter zu gestalten.
Die Weiterentwicklung der Dampfturbinen-Technologie zielt darauf ab, die Effizienz der Energieumwandlung zu maximieren und gleichzeitig die Umweltbelastung zu minimieren. Dies wird durch die kontinuierliche Verbesserung der thermodynamischen Prozesse, der Materialtechnologie und der Betriebsbedingungen erreicht. Ein Schlüsselansatz ist die Verbesserung der Temperatur- und Druckbedingungen, unter denen die Dampfturbinen arbeiten. Höhere Temperaturen und Drücke ermöglichen eine größere Menge an thermischer Energie im Dampf, die in mechanische Arbeit umgewandelt werden kann, was die Effizienz des gesamten Systems steigert. Dies erfordert jedoch den Einsatz fortschrittlicher Materialien, die extremen Bedingungen standhalten können, ohne ihre mechanischen Eigenschaften zu verlieren. Superlegierungen auf Nickel- oder Kobaltbasis, die in den Hochtemperaturbereichen der Turbine eingesetzt werden, sind hier von zentraler Bedeutung. Diese Materialien müssen nicht nur hitzebeständig sein, sondern auch korrosions- und verschleißfest, da die Turbine ständig mechanischen und thermischen Belastungen ausgesetzt ist.
Ein weiterer Bereich, der die Effizienz der Energieumwandlung verbessern kann, ist die Optimierung der Strömungsmechanik innerhalb der Turbine. Durch die präzise Gestaltung der Schaufeln, die den Dampf in Bewegung setzen, kann der Wirkungsgrad erheblich gesteigert werden. Dabei spielen neben der aerodynamischen Form der Laufschaufeln auch die Leitschaufeln eine wichtige Rolle. Diese lenken den Dampfstrom so, dass er die Schaufeln der Turbine in einem optimalen Winkel trifft, wodurch der Impuls des Dampfes maximiert und die mechanische Arbeit effizienter erzeugt wird. Kleine Anpassungen in der Geometrie und Ausrichtung der Schaufeln können einen großen Unterschied in der Gesamtleistung der Turbine ausmachen, da sie die Strömung besser ausnutzen und Verluste durch Turbulenzen oder Reibung verringern.
In modernen Dampfturbinen kommen auch digitale Steuerungssysteme zum Einsatz, die eine genauere Überwachung und Steuerung des Energieumwandlungsprozesses ermöglichen. Durch die kontinuierliche Erfassung von Betriebsdaten in Echtzeit, wie etwa Dampfmenge, Temperatur und Druck, können Turbinenbetreiber den Betrieb der Anlage optimieren und die Effizienz steigern. Dies wird insbesondere durch den Einsatz von Predictive Maintenance-Technologien unterstützt, bei denen durch Datenanalysen potenzielle Probleme frühzeitig erkannt werden können. Solche Systeme erlauben es, Wartungsmaßnahmen genau zu planen, um Ausfälle zu vermeiden und die Lebensdauer der Turbinen zu verlängern.
Ein weiterer Aspekt, der zunehmend an Bedeutung gewinnt, ist die Integration erneuerbarer Energien in das Dampfturbinen-System. In traditionellen thermischen Kraftwerken wird die Energieumwandlung durch Dampfturbinen vor allem aus fossilen Brennstoffen gespeist. Angesichts der globalen Bestrebungen zur Reduktion von CO₂-Emissionen gewinnt die Nutzung von Solarenergie, Biomasse oder geothermischer Energie zunehmend an Bedeutung. In solaren Thermikkraftwerken wird beispielsweise durch konzentrierte Sonnenstrahlung Wasser erhitzt, das anschließend in Dampf umgewandelt und durch Dampfturbinen geführt wird, um elektrische Energie zu erzeugen. Die Technologie zur Nutzung erneuerbarer Energien stellt besondere Anforderungen an die Dampfturbinen, da die Dampferzeugung in diesen Anlagen nicht konstant ist, sondern stark von den äußeren Bedingungen abhängt. Dennoch bleibt die Dampfturbine ein bewährtes Mittel zur Energieumwandlung, da sie sich flexibel an verschiedene Betriebsarten anpassen lässt.
Zukunftsweisende Konzepte zur weiteren Verbesserung der Energieumwandlung beinhalten die Entwicklung von Hybridkraftwerken, bei denen Dampfturbinen mit anderen Energieumwandlungstechnologien kombiniert werden. In Combined-Cycle-Anlagen werden beispielsweise Dampfturbinen mit Gasturbinen kombiniert, um die Abwärme der Gasturbine zu nutzen und zusätzlich Dampf zu erzeugen, der eine weitere Dampfturbine antreibt. Dies führt zu einer signifikanten Steigerung des Gesamtwirkungsgrads und einer Reduzierung der Emissionen pro erzeugter Kilowattstunde Strom. Weitere Fortschritte könnten durch die Verbesserung der thermischen Speichertechnologien erzielt werden, die es ermöglichen, die erzeugte Wärmeenergie effizienter zu speichern und nach Bedarf zu nutzen. Dies würde nicht nur die Flexibilität der Dampfturbinen erhöhen, sondern auch ihre Integration in ein smartes, sich dynamisch anpassendes Stromnetz erleichtern.
Zusammenfassend lässt sich sagen, dass die Energieumwandlung in Dampfturbinen weiterhin eine Schlüsseltechnologie in der globalen Energieversorgung darstellt, insbesondere im Hinblick auf die Stromerzeugung aus thermischen Quellen. Die kontinuierliche Forschung und Entwicklung in den Bereichen Materialwissenschaft, Strömungsmechanik, digitale Steuerung und Integration erneuerbarer Energien wird die Effizienz und Nachhaltigkeit der Dampfturbinen in den kommenden Jahren weiter verbessern. Die steigende Nachfrage nach Energie, gepaart mit der Notwendigkeit, Emissionen zu reduzieren, macht es erforderlich, dass Dampfturbinen als Teil eines zunehmend komplexen und umweltbewussteren Energiesystems weiter optimiert und modernisiert werden.
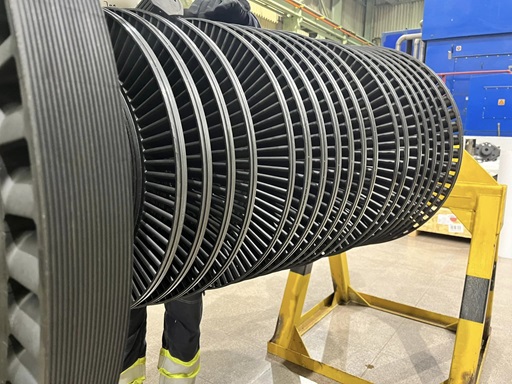
Die fortschreitende Verbesserung der Dampfturbinen-Technologie geht Hand in Hand mit den globalen Bestrebungen, die Energieeffizienz zu steigern und die Umweltbelastung durch fossile Brennstoffe zu reduzieren. Eine wichtige Entwicklung in diesem Zusammenhang ist die verstärkte Nutzung von Abwärme. Dampfturbinen können nicht nur Energie aus traditionellen Brennstoffen, sondern auch aus industriellen Abwärmequellen gewinnen. Dies ermöglicht die Erzeugung von Strom, indem die Wärme, die sonst ungenutzt verloren ginge, in nutzbare Energie umgewandelt wird. In Kraft-Wärme-Kopplungsanlagen (KWK) beispielsweise wird sowohl Strom als auch Wärme erzeugt, indem die erzeugte Abwärme genutzt wird, um Wasser zu verdampfen und durch eine Dampfturbine zu leiten. Diese Art der Kraftwerkstechnik maximiert den Gesamtwirkungsgrad und reduziert den Brennstoffverbrauch, wodurch auch die CO₂-Emissionen gesenkt werden.
Ein weiteres Konzept, das an Bedeutung gewinnt, ist die sogenannte „Flexibilisierung“ von Dampfturbinen. In den letzten Jahren wurde ein wachsender Bedarf an flexiblen Kraftwerkskapazitäten festgestellt, die schnell auf Änderungen in der Stromnachfrage reagieren können. Dies ist besonders relevant in einem Energiemix, der zunehmend von erneuerbaren Energiequellen wie Wind und Solar abhängt, deren Stromerzeugung naturgemäß schwankt. Dampfturbinen werden zunehmend so konstruiert, dass sie nicht nur im kontinuierlichen Betriebsmodus, sondern auch im Teillastbereich effizient arbeiten können. Dies erfordert eine feinere Abstimmung der Dampfdruck- und Temperaturregulierung sowie eine verbesserte Regelungstechnik, um Turbinen auch bei wechselnden Betriebsbedingungen mit maximaler Effizienz zu betreiben.
Zudem ist die Entwicklung von Turbo-Kompressoren und anderen Hilfskomponenten, die in Dampfturbinen eingesetzt werden, ein weiteres wichtiges Element, um den Gesamtwirkungsgrad zu steigern. Diese Komponenten tragen dazu bei, den Druck und die Strömung des Dampfs zu optimieren, was wiederum zu einer besseren Umwandlung der thermischen Energie führt. Turbo-Kompressoren etwa sind in der Lage, die Luft in Kraftwerken effizienter zu verdichten, was die Leistung von Dampfturbinen bei der Stromerzeugung weiter steigert.
Parallel zur technologischen Weiterentwicklung der Dampfturbinen werden auch fortschrittliche Steuerungssysteme entwickelt, die eine präzisere Überwachung und Anpassung der Betriebsparameter ermöglichen. Der Einsatz von Künstlicher Intelligenz (KI) und maschinellem Lernen zur Analyse großer Datenmengen aus den Betriebsabläufen ermöglicht es, noch effizientere Regelstrategien zu entwickeln. KI-gestützte Systeme können Muster in den Betriebsdaten erkennen und auf dieser Grundlage Vorhersagen zu Wartungsbedarfen oder zu Leistungsverbesserungen treffen. Diese intelligenten Steuerungen machen den Betrieb von Dampfturbinen nicht nur effizienter, sondern auch sicherer, indem sie den Verschleiß der Turbine minimieren und gleichzeitig Ausfallzeiten durch präventive Wartungsmaßnahmen reduzieren.
Ein weiterer wichtiger Trend ist die Forschung zu alternativen Brennstoffen, die die Umweltauswirkungen der Dampfturbinen weiter verringern können. Biomasse und synthetische Kraftstoffe aus erneuerbaren Quellen bieten vielversprechende Möglichkeiten, Dampfturbinen mit einer deutlich geringeren CO₂-Bilanz zu betreiben. Diese Brennstoffe können in bestehenden Dampfturbinenanlagen verwendet werden, um die Abhängigkeit von fossilen Brennstoffen zu verringern und gleichzeitig die bestehende Infrastruktur zu erhalten. Darüber hinaus gibt es Bestrebungen, Dampfturbinen mit Wasserstoff zu betreiben. Wasserstoff ist ein sauberer Brennstoff, der bei der Verbrennung keine CO₂-Emissionen erzeugt, was ihn zu einer attraktiven Option für die Dekarbonisierung der Energieerzeugung macht.
Das Potenzial zur Verbesserung der Energieumwandlung in Dampfturbinen reicht also weit über die klassischen Parameter wie Druck und Temperatur hinaus. Es umfasst auch eine breitere Perspektive, die innovative Technologien zur Nutzung erneuerbarer und alternativer Brennstoffe, intelligente Systeme zur Betriebsoptimierung und fortschrittliche Materialien für eine längere Lebensdauer und bessere Leistung beinhaltet. In einer Welt, die zunehmend auf Nachhaltigkeit und CO₂-Reduktion angewiesen ist, werden Dampfturbinen eine zentrale Rolle in der Energieerzeugung der Zukunft spielen, sowohl als Teil konventioneller Kraftwerke als auch in der Integration mit erneuerbaren Energiequellen und modernen, flexiblen Energienetzen. Sie sind und bleiben eine Schlüsseltechnologie auf dem Weg zu einer effizienten und umweltfreundlicheren Energieversorgung.
Strömungsführung
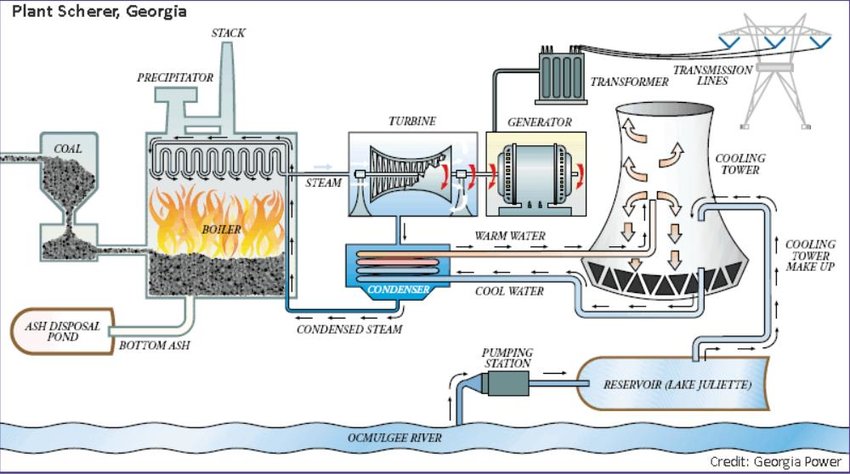
Die Strömungsführung in Dampfturbinen ist entscheidend für die Effizienz der Energieumwandlung und die Optimierung der mechanischen Arbeit, die aus der thermischen Energie des Dampfes gewonnen wird. Der Dampf, der unter hohem Druck und hoher Temperatur aus dem Kessel austritt, muss in einer bestimmten Weise durch die Turbine geführt werden, um die maximale Leistung zu erzielen. Die Strömungsführung umfasst dabei die Steuerung und Lenkung des Dampfs von der Eintrittsstelle der Turbine bis zum Auslass, wobei die Umwandlung von thermischer Energie in mechanische Arbeit erfolgt. Eine präzise Strömungsführung beginnt mit den Leitschaufeln, die den Dampfstrahl in die richtige Richtung lenken, sodass der Dampf mit dem optimalen Winkel auf die Laufschaufeln trifft.
Diese Laufschaufeln sind so geformt, dass sie die kinetische Energie des Dampfs aufnehmen und in eine Drehbewegung des Turbinenrotors umwandeln. Durch die richtige Geometrie und Ausrichtung der Schaufeln wird die Strömung des Dampfs kontrolliert, um Turbulenzen, die zu Energieverlusten führen könnten, zu minimieren und gleichzeitig die Energieumwandlung zu maximieren. Die Strömungsführung ist nicht nur von der Form der Schaufeln abhängig, sondern auch von der präzisen Regulierung des Dampfdrucks und der Dampftemperatur während des gesamten Turbinenprozesses.
Da der Dampf beim Durchströmen der Turbine an Druck und Temperatur verliert, wird eine effektive Strömungsführung durch verschiedene Stufen, bei denen der Dampf schrittweise expandiert und an Energie verliert, immer wichtiger. Jede dieser Stufen ist speziell so ausgelegt, dass der Dampf optimal durch die Turbine geführt wird, um die mechanische Arbeit zu maximieren und die Energieeffizienz zu erhöhen. Eine effiziente Strömungsführung trägt dazu bei, dass die Turbine ihre maximale Leistung bei minimalen Verlusten erreichen kann.
Die Strömungsführung in Dampfturbinen ist ein kritischer Aspekt für den Betrieb und die Leistungsfähigkeit der gesamten Anlage. Um die Energieumwandlung effizient zu gestalten, muss der Dampf nicht nur durch die Turbine strömen, sondern dies muss auf eine kontrollierte und präzise Weise geschehen. Der Dampf, der sich unter hohem Druck und hoher Temperatur in einem Kessel gebildet hat, wird in die Turbine eingeführt, wo er durch eine Serie von Schaufeln geleitet wird, die so konstruiert sind, dass sie die bestmögliche Nutzung der thermischen Energie des Dampfs ermöglichen. Die Leitschaufeln spielen in diesem Prozess eine zentrale Rolle. Sie sind so angeordnet, dass sie den Dampfstrom in eine bestimmte Richtung lenken und seine Geschwindigkeit sowie den Strömungswinkel kontrollieren. Dies stellt sicher, dass der Dampf mit dem optimalen Impuls auf die Laufschaufeln trifft, wodurch der Dampf die maximale mechanische Arbeit leisten kann.
Die Laufschaufeln sind so gestaltet, dass sie die kinetische Energie des Dampfs in Drehbewegung umwandeln. Der Dampf trifft auf diese Schaufeln, deren Form und Neigung so optimiert sind, dass der Impuls des Dampfs in mechanische Energie überführt wird. Dabei sind die Laufschaufeln so geformt, dass der Dampf mit minimalem Widerstand und ohne unnötige Turbulenzen über die Schaufeln gleitet, was dazu beiträgt, dass der Energieumwandlungsprozess so effizient wie möglich abläuft. Eine präzise Strömungsführung ist besonders wichtig, da der Dampf auf seiner Reise durch die Turbine stetig an Druck und Temperatur verliert. Ohne eine effektive Strömungsführung könnten diese Verluste zu einem erheblichen Verlust an mechanischer Arbeit führen.
Ein weiteres wichtiges Element der Strömungsführung ist die Turbulenzkontrolle. Turbulenzen können die Strömung des Dampfs destabilisieren und führen zu Energieverlusten. Um dies zu vermeiden, werden die Schaufeln in der Turbine so gestaltet, dass sie die Strömung stabilisieren. Darüber hinaus werden die Strömungsprofile des Dampfs so angepasst, dass er möglichst gleichmäßig und in einer kontrollierten Weise durch die Turbine strömt. Dies ist besonders bei mehrstufigen Dampfturbinen von Bedeutung, in denen der Dampf nach und nach in mehreren Stufen expandiert und dabei kontinuierlich an Druck und Temperatur verliert. Jede dieser Stufen muss optimal aufeinander abgestimmt sein, um sicherzustellen, dass der Dampf in jeder Phase seiner Expansion effizient genutzt wird.
Die Strömungsführung wird zudem durch verschiedene technische Maßnahmen wie Drosselventile und Druckregelungen optimiert, die sicherstellen, dass der Dampf jederzeit unter den besten Bedingungen in die Turbine eintritt. Die Regulierung des Dampfdrucks und der Temperatur ist dabei von entscheidender Bedeutung, da der Wirkungsgrad der Dampfturbine stark von diesen Parametern abhängt. In vielen modernen Dampfturbinen sind fortschrittliche Steuerungssysteme integriert, die die Strömungsführung in Echtzeit überwachen und anpassen. Diese Systeme können beispielsweise den Druck und die Temperatur des Dampfs konstant halten und so eine gleichmäßige und stabile Strömung durch die Turbine gewährleisten. Solche Systeme tragen nicht nur zur Verbesserung der Effizienz bei, sondern auch zur Verlängerung der Lebensdauer der Turbine, da sie den mechanischen Stress auf die Schaufeln und andere Teile der Turbine minimieren.
Ein weiterer wichtiger Aspekt der Strömungsführung ist die Integration der Turbine in das Gesamtsystem des Kraftwerks. Die Dampfturbine ist in der Regel Teil eines komplexen Systems, das auch Wärmetauscher, Kondensatoren und andere Komponenten umfasst. Die Strömungsführung muss daher so abgestimmt werden, dass sie mit diesen anderen Systemen zusammenarbeitet. Beispielsweise muss der Dampf am Ende der Turbine auf den richtigen Druck und die richtige Temperatur reduziert werden, um in den Kondensator überführt zu werden, wo er wieder in Wasser umgewandelt und zurück in den Kreislauf des Kraftwerks geführt wird. Dies erfordert eine genaue Abstimmung der Strömungsführung, um sicherzustellen, dass der Dampf in jeder Phase seiner Expansion und Abkühlung effizient genutzt wird.
Darüber hinaus wird in modernen Dampfturbinen zunehmend auf die Verwendung fortschrittlicher Materialien und Fertigungstechniken geachtet, um die Strömungsführung weiter zu optimieren. Materialien, die besonders widerstandsfähig gegenüber den extremen Temperaturen und Drücken in der Turbine sind, sowie fortschrittliche Fertigungstechniken, die eine präzisere Konstruktion der Schaufeln und anderer Turbinenkomponenten ermöglichen, tragen dazu bei, die Strömungsführung zu verbessern. Dies führt nicht nur zu einer besseren Energieumwandlung, sondern auch zu einer höheren Zuverlässigkeit und Langlebigkeit der Turbine.
Die Strömungsführung in Dampfturbinen hat also weitreichende Auswirkungen auf die Leistung und Effizienz der gesamten Energieumwandlungseinheit. Durch die präzise Kontrolle des Dampfdurchflusses und die Minimierung von Energieverlusten durch Turbulenzen und Widerstände wird sichergestellt, dass die Turbine ihre maximale Leistung entfaltet. Um dies zu erreichen, ist eine enge Zusammenarbeit von verschiedenen technischen Disziplinen notwendig, einschließlich Thermodynamik, Strömungsmechanik, Materialwissenschaft und Steuerungstechnik. Nur durch die kontinuierliche Optimierung dieser Bereiche kann die Dampfturbine ihre Rolle als effiziente und zuverlässige Energiequelle in einer zunehmend komplexeren und nachhaltigeren Energieversorgungssysteme voll ausspielen.
Die kontinuierliche Weiterentwicklung der Strömungsführung in Dampfturbinen ist von wesentlicher Bedeutung für die Steigerung der Effizienz und Leistungsfähigkeit moderner Kraftwerke. Neben der Optimierung der geometrischen Gestaltung von Schaufeln und der Steuerung des Dampfdurchflusses spielen auch fortschrittliche Simulationstechniken eine immer größere Rolle. Mit Hilfe von Computational Fluid Dynamics (CFD) können Ingenieure präzise Vorhersagen über das Verhalten des Dampfs innerhalb der Turbine treffen und die Strömungsführung in allen Bereichen der Turbine genau untersuchen. Diese Simulationen ermöglichen es, potenzielle Probleme wie Turbulenzen, Strömungsabrisse oder ungleichmäßige Strömung in den Schaufeln frühzeitig zu identifizieren und gezielt zu beheben. Dies führt zu einer erheblichen Verbesserung der Strömungsführung und trägt dazu bei, die Turbine unter unterschiedlichen Betriebsbedingungen zu optimieren.
Ein weiterer wichtiger Fortschritt in der Strömungsführung ist die Minimierung von Energieverlusten durch Reibung und Druckabfall. In jeder Phase des Dampfstroms müssen die Strömungsprofile so gestaltet werden, dass sie Reibung und Widerstand auf den Turbinenkomponenten verringern. Hier kommen auch moderne Beschichtungen und Materialinnovationen zum Einsatz, die die Oberflächenrauigkeit der Schaufeln reduzieren und die Strömung des Dampfs so reibungsarm wie möglich gestalten. Diese fortschrittlichen Beschichtungen tragen nicht nur zur Verbesserung der Strömungsführung bei, sondern erhöhen auch die Lebensdauer der Turbine, indem sie die Auswirkungen von Korrosion und Erosion verringern, die durch den konstanten Kontakt des Dampfs mit den Turbinenkomponenten entstehen.
Ein weiterer Bereich, in dem die Strömungsführung optimiert werden kann, ist die Nutzung von sogenannten „Strömungskonditionierern“ oder „Preconditioning-Elementen“. Diese Vorrichtungen werden oft vor den Leitschaufeln oder Laufschaufeln eingesetzt und dienen dazu, den Dampfstrom zu stabilisieren und eine gleichmäßige Strömung zu gewährleisten. Sie können dazu beitragen, die Geschwindigkeit und den Druck des Dampfs zu regulieren und eine optimale Strömungskondition für die Schaufeln zu schaffen. Solche Strömungskonditionierer sind besonders in mehrstufigen Dampfturbinen von Vorteil, da sie dafür sorgen, dass der Dampf in jeder Stufe der Expansion gleichmäßig und kontrolliert durch die Turbine strömt.
Die Anpassung der Strömungsführung an verschiedene Betriebsarten der Turbine ist ebenfalls ein wichtiger Faktor. In vielen modernen Dampfturbinen wird der Betrieb nicht mehr nur auf eine konstante Leistungsabgabe ausgelegt, sondern auf eine variable Lastregelung, die sich je nach Nachfrage ändern kann. Eine präzise Anpassung der Strömungsführung ermöglicht es, die Turbine auch bei Teillastbedingungen effizient zu betreiben. Dies ist besonders wichtig, da die Stromerzeugung aus erneuerbaren Quellen wie Wind- und Solarenergie stark schwankt und die Nachfrage nach Flexibilität im Energiesystem steigt. Dampfturbinen müssen in der Lage sein, ihre Leistung schnell an Veränderungen der Nachfrage oder an das Angebot von erneuerbarem Strom anzupassen. Dies erfordert eine präzise Steuerung der Strömung und eine ständige Überwachung der Betriebsparameter in Echtzeit.
Die Implementierung solcher flexiblen Betriebsmodi wird durch die fortschreitende Digitalisierung von Dampfturbinen unterstützt. Durch den Einsatz von Sensoren, die den Dampfdruck, die Temperatur, die Strömungsgeschwindigkeit und andere kritische Parameter messen, können Turbinenbetreiber den Dampfstrom und den gesamten Energieumwandlungsprozess genau überwachen. Künstliche Intelligenz (KI) und maschinelles Lernen spielen eine immer größere Rolle in der Überwachung und Optimierung der Strömungsführung. Diese Technologien sind in der Lage, aus historischen und Echtzeit-Daten Muster zu erkennen und Vorhersagen zu treffen, die es den Betreibern ermöglichen, auf Veränderungen im System schneller und präziser zu reagieren. KI-Algorithmen können beispielsweise den Dampfdruck automatisch anpassen, um den Strömungswiderstand zu minimieren und gleichzeitig die maximale Effizienz zu gewährleisten.
Darüber hinaus ist die Strömungsführung in modernen Dampfturbinen auch im Kontext der gesamten Energieeffizienz von Bedeutung. Die Abwärme, die bei der Energieumwandlung in der Turbine entsteht, muss ebenfalls effizient genutzt werden. Hier wird die Strömungsführung so angepasst, dass der Dampf nicht nur optimal durch die Turbine strömt, sondern auch möglichst wenig Energie in Form von Wärme verloren geht. In Combined-Cycle-Anlagen, bei denen Abwärme aus einer Gasturbine genutzt wird, um Dampf zu erzeugen und eine Dampfturbine anzutreiben, spielt eine präzise Strömungsführung eine zentrale Rolle, um den gesamten Prozess zu optimieren. Die Strömungskonditionierung in solchen Anlagen ermöglicht es, die Abwärme so effizient wie möglich in Strom umzuwandeln und gleichzeitig den Wirkungsgrad der gesamten Anlage zu erhöhen.
Abschließend lässt sich sagen, dass die Strömungsführung in Dampfturbinen ein äußerst komplexes, aber auch faszinierendes Zusammenspiel von Technik, Materialwissenschaften, Strömungsmechanik und modernen digitalen Steuerungen ist. Die kontinuierliche Verbesserung in diesen Bereichen trägt entscheidend dazu bei, die Effizienz, Flexibilität und Nachhaltigkeit von Dampfturbinen zu steigern. Die Entwicklung neuer Materialien, intelligenter Steuerungssysteme und innovativer Fertigungstechniken sorgt dafür, dass Dampfturbinen auch in Zukunft eine Schlüsseltechnologie für die nachhaltige Energieversorgung bleiben. Die Herausforderung besteht darin, die Strömungsführung ständig an die sich verändernden Anforderungen der Energiebranche anzupassen und gleichzeitig die Leistung und Effizienz der Turbinen weiter zu steigern.
Dampfexpansion

Die Dampfexpansion in Dampfturbinen ist ein entscheidender Prozess, bei dem die thermische Energie des Dampfs in mechanische Arbeit umgewandelt wird. Dieser Vorgang findet statt, wenn der Dampf unter hohem Druck und hoher Temperatur in die Turbine eintritt und sich während des Durchgangs durch die verschiedenen Turbinenstufen ausdehnt. Die Expansion des Dampfs erfolgt schrittweise und kontrolliert, wobei der Dampf an Druck und Temperatur verliert, während er die mechanische Arbeit auf die Turbine überträgt. Der Prozess beginnt in der Regel in der ersten Stufe der Turbine, wo der Dampf zunächst in einem sehr komprimierten Zustand mit hohem Druck und hoher Temperatur vorliegt. Beim Eintritt in die Turbine wird der Dampf durch die Leitschaufeln gelenkt, die seine Richtung und Geschwindigkeit steuern, sodass der Dampf mit dem optimalen Winkel auf die Laufschaufeln trifft. Diese Schaufeln übernehmen dann die kinetische Energie des Dampfs und setzen sie in Drehbewegung um.
Dabei expandiert der Dampf weiter, was bedeutet, dass sich sein Volumen vergrößert, während der Druck sinkt und die Temperatur allmählich abnimmt. Jede Stufe der Turbine ist so ausgelegt, dass die Expansion des Dampfs schrittweise und unter optimalen Bedingungen erfolgt. Der Dampf verliert in jeder Stufe an Druck, wobei die Temperatur in der Regel nur in einem begrenzten Bereich gesenkt wird, um die Effizienz der Turbine zu maximieren. Eine präzise Kontrolle der Dampfexpansion ist notwendig, um die mechanische Arbeit auf die Turbine zu übertragen, ohne dass es zu unnötigen Verlusten kommt. Wenn der Dampf zu stark expandiert oder zu schnell abkühlt, kann dies zu einer geringeren Effizienz oder sogar zu Schäden an den Turbinenkomponenten führen.
Daher wird die Expansion in Dampfturbinen in mehreren Stufen durchgeführt, um eine gleichmäßige und effiziente Umwandlung der thermischen Energie in mechanische Arbeit zu gewährleisten. In modernen Dampfturbinen werden diese Prozesse durch fortschrittliche Steuerungssysteme und Simulationstechniken überwacht, die sicherstellen, dass der Dampf in jeder Stufe der Expansion unter optimalen Bedingungen arbeitet, um die höchstmögliche Effizienz zu erzielen.
Die Dampfexpansion in Dampfturbinen erfolgt nicht nur durch die physikalische Ausdehnung des Dampfs, sondern auch durch die Umwandlung von thermischer Energie in kinetische Energie. Der Dampf verliert beim Durchströmen der Turbine an Druck und Temperatur, was zu einer Zunahme des Volumens führt. Dieser Druckabbau und die Zunahme des Volumens sind entscheidend für die Funktionsweise der Turbine. Während der Expansion dehnt sich der Dampf aus, was bedeutet, dass die Moleküle weiter auseinander rücken und der Dampf seine ursprüngliche Dichte verliert. Dies führt zu einer Reduktion des Dampfdrucks und der Temperatur, während die kinetische Energie zunimmt. Diese kinetische Energie wird von den Laufschaufeln der Turbine aufgenommen und in eine Drehbewegung des Turbinenrotors umgewandelt.
Der Prozess der Dampfexpansion erfolgt in mehreren Stufen innerhalb der Dampfturbine, wobei jede Stufe für einen Teil der Gesamtenergieumwandlung verantwortlich ist. In jeder Stufe verliert der Dampf an Druck und Temperatur, wobei der Druck über die Stufen hinweg stetig sinkt. Jede Turbinenstufe ist dabei so konzipiert, dass sie die Energie des Dampfs effizient in mechanische Arbeit umwandelt. Der Übergang von einer Stufe zur nächsten erfolgt unter kontrollierten Bedingungen, um sicherzustellen, dass der Dampf weiterhin effektiv expandieren kann. Um die Energie möglichst effizient zu nutzen, wird die Expansion des Dampfs in mehreren Schritten durchgeführt, wobei der Dampf in den höheren Stufen stärker expandiert und somit noch mehr kinetische Energie in Arbeit umwandelt.
Wichtig für die Effizienz der Dampfexpansion ist auch die Gestaltung der Schaufeln und der Strömungsführung. Die Leitschaufeln und Laufschaufeln sind so angeordnet, dass sie die Strömung des Dampfs optimieren und die Expansion effizient steuern. Durch eine präzise Gestaltung der Geometrie dieser Schaufeln wird der Dampf in einem optimalen Winkel auf die Laufschaufeln gelenkt, was zu einer maximalen Umwandlung der thermischen Energie in mechanische Energie führt. Eine gleichmäßige und kontrollierte Expansion des Dampfs ist dabei entscheidend, um den Wirkungsgrad der Turbine zu maximieren.
In der Praxis ist es zudem wichtig, die Expansion so zu steuern, dass keine überschüssige Wärme verloren geht. Der Dampf sollte gleichmäßig und mit einem möglichst niedrigen Energieverlust expandieren. Um dies zu gewährleisten, werden in modernen Dampfturbinen präzise Steuerungssysteme eingesetzt, die den Dampffluss überwachen und bei Bedarf anpassen. Diese Systeme können die Dampfdruckverhältnisse und Temperaturen während der Expansion automatisch regeln, um die Turbine unter den besten Bedingungen zu betreiben.
Darüber hinaus wird die Expansion des Dampfs auch durch den Einsatz fortschrittlicher Materialien und Beschichtungen unterstützt. Da die Turbinenkomponenten bei der Expansion hohen thermischen und mechanischen Belastungen ausgesetzt sind, werden zunehmend hochfeste und temperaturbeständige Materialien verwendet, um die Lebensdauer und Leistung der Turbine zu verbessern. Diese Materialien müssen nicht nur den extremen Temperaturen und Drücken während der Expansion standhalten, sondern auch den sich ändernden Bedingungen, die während des Betriebs der Turbine auftreten können.
Zusammenfassend lässt sich sagen, dass die Dampfexpansion in Dampfturbinen ein komplexer und wichtiger Prozess ist, bei dem thermische Energie in kinetische Energie umgewandelt wird. Eine präzise Steuerung der Dampfexpansion, die richtige Geometrie der Schaufeln und eine optimierte Strömungsführung sind entscheidend, um eine maximale Effizienz bei der Umwandlung der Wärmeenergie in mechanische Arbeit zu erreichen. Moderne Dampfturbinen setzen fortschrittliche Steuerungssysteme, Materialien und Fertigungstechniken ein, um den Expansionsprozess zu optimieren und den Wirkungsgrad der Turbine zu steigern.

Die Dampfexpansion in Dampfturbinen ist ein fortlaufend optimierter Prozess, der nicht nur auf die Umwandlung von thermischer Energie in mechanische Arbeit abzielt, sondern auch auf die Maximierung der Effizienz der gesamten Energieumwandlung. Der Prozess beginnt mit der kontinuierlichen Überwachung des Dampfdrucks und der Temperatur, um sicherzustellen, dass der Dampf in jeder Phase der Expansion optimal genutzt wird. Dies ist besonders wichtig, da Dampfturbinen in modernen Kraftwerken oft unter wechselnden Betriebsbedingungen laufen, beispielsweise bei Lastschwankungen oder variierenden Brennstoffqualitäten. In solchen Fällen muss die Expansion flexibel gesteuert werden, um den Wirkungsgrad unter verschiedenen Betriebsbedingungen konstant hoch zu halten.
Ein wichtiger Aspekt der Dampfexpansion ist die Art und Weise, wie der Dampf durch die verschiedenen Turbinenstufen geführt wird. In jeder Stufe verliert der Dampf an Druck und Temperatur, und das Volumen nimmt zu. In der ersten Stufe der Turbine, in der der Dampf noch den höchsten Druck hat, ist die Expansion relativ gering, aber schon hier wird die kinetische Energie durch die Laufschaufeln aufgenommen und in eine Drehbewegung umgesetzt. In den nachfolgenden Stufen expandiert der Dampf weiter und verliert zunehmend an Druck und Temperatur, wobei der Volumenstrom wächst. Jede dieser Stufen ist so ausgelegt, dass sie diese Energiedifferenz bestmöglich nutzt, ohne dass es zu Energieverlusten durch Turbulenzen oder unregelmäßige Strömungsprofile kommt.
Die genaue Gestaltung der Schaufeln ist ein weiteres entscheidendes Element, das die Dampfexpansion effizienter macht. Leitschaufeln und Laufschaufeln müssen exakt aufeinander abgestimmt sein, um den Dampf in der richtigen Geschwindigkeit und Richtung zu lenken. Besonders wichtig ist die Form der Schaufeln, die die Energieübertragung maximiert, indem sie eine gleichmäßige Strömung des Dampfs gewährleisten. Auch die Neigung und das Profil der Schaufeln sind dabei von Bedeutung, da sie verhindern, dass der Dampf zu schnell oder zu langsam über die Schaufeln strömt. Ein gut abgestimmtes System sorgt für eine gleichmäßige Energieabgabe und verhindert, dass der Dampf durch zu starke Beschleunigung oder Verzögerung seine Energieeffizienz verliert.
Ein weiteres Konzept, das die Effizienz der Dampfexpansion unterstützt, ist die sogenannte „interaktive Expansion“, bei der der Dampf durch sogenannte Zwischenstufen oder Umkehrkammern geführt wird. Diese Kammern sind so ausgelegt, dass sie dem Dampf Zeit und Raum geben, sich weiter auszudehnen und dabei zusätzlich mechanische Energie abzugeben, bevor er in die nächste Stufe übergeht. Diese Art der Dampfexpansion führt zu einer noch gleichmäßigeren Druck- und Temperaturverteilung, was den gesamten Energieumwandlungsprozess effizienter macht. Dabei wird nicht nur die thermische Energie des Dampfs effektiv in Arbeit umgewandelt, sondern es wird auch dafür gesorgt, dass keine unnötigen Wärmeverluste auftreten.
Darüber hinaus ist die Abführung der Restwärme ein wichtiger Faktor. Am Ende des Expansionprozesses hat der Dampf in der Turbine seine gesamte verfügbare thermische Energie in mechanische Arbeit umgewandelt. Was noch verbleibt, ist ein Dampf mit relativ niedrigem Druck und Temperatur. Diese Restwärme wird in den meisten Kraftwerken über einen Kondensator abgeführt, wo der Dampf in Wasser umgewandelt wird, das dann in den Kreislauf zurückgeführt wird. Die richtige Gestaltung der Kondensationsstufe und die effiziente Rückführung des Wassers sind ebenfalls Teil des gesamten Prozesses der Dampfexpansion, da sie dafür sorgen, dass der Zyklus geschlossen bleibt und keine Energie verschwendet wird.
Ein weiteres bedeutendes Ziel der Dampfexpansion ist es, die Entstehung von Schäden an den Turbinenkomponenten zu verhindern. Die hohe kinetische Energie, die während der Expansion entsteht, muss kontrolliert abgebaut werden, um Turbulenzen und mechanische Belastungen zu minimieren. Wenn der Dampf zu schnell expandiert oder abrupt auf die Schaufeln trifft, kann dies zu einer Beschädigung der Bauteile führen. Daher werden die Turbinenkomponenten so ausgelegt, dass sie den Dampfstrom gleichmäßig verteilen und die kinetische Energie allmählich in mechanische Arbeit umwandeln.
Schließlich trägt die kontinuierliche Forschung und Entwicklung zur Verbesserung der Dampfexpansion dazu bei, dass Dampfturbinen immer effizienter und zuverlässiger werden. Die Einführung neuer Werkstoffe, die den extremen Bedingungen innerhalb der Turbine standhalten können, ebenso wie die Verwendung innovativer Steuerungssysteme, die den Dampfstrom in Echtzeit optimieren, führen zu einer stetigen Verbesserung der Gesamtleistung. Dabei werden auch neue Konzepte wie die „abgestufte Expansion“ untersucht, bei der der Dampf in mehreren kontrollierten Phasen expandiert, um maximale Energieeffizienz zu erreichen.
Zusammenfassend lässt sich sagen, dass die Dampfexpansion in Dampfturbinen ein hochkomplexer Prozess ist, bei dem thermische Energie Schritt für Schritt in mechanische Arbeit umgewandelt wird. Jede Phase dieses Prozesses muss präzise kontrolliert werden, um die maximale Energieeffizienz zu erzielen. Dies erfordert eine ausgeklügelte Strömungsführung, eine sorgfältige Gestaltung der Turbinenkomponenten und die ständige Überwachung und Anpassung der Betriebsbedingungen. In einer zunehmend energieeffizienten und nachhaltigen Welt wird die Dampfexpansion weiterhin eine Schlüsselrolle in der Energieumwandlung spielen und ist ein zentraler Bestandteil moderner Dampfturbinen-Technologie.
Die Weiterentwicklung der Dampfexpansion in Dampfturbinen geht Hand in Hand mit den Fortschritten in den Bereichen Materialwissenschaften, Fertigungstechnologien und digitalen Steuerungssystemen. Neue Materialien, die widerstandsfähiger gegenüber hohen Temperaturen und Drücken sind, ermöglichen eine noch effektivere Nutzung des Dampfs bei der Expansion. Diese Materialien müssen nicht nur den extremen thermischen Bedingungen standhalten, sondern auch den mechanischen Kräften, die während des Dampfstroms auf die Turbinenkomponenten wirken. Besonders hochfeste Legierungen und innovative Beschichtungen, die die Oberflächenrauigkeit minimieren und die Widerstandsfähigkeit gegenüber Korrosion und Erosion verbessern, tragen dazu bei, die Lebensdauer der Turbine zu verlängern und die Effizienz der Dampfexpansion zu steigern.
Ein weiteres bedeutendes Entwicklungsfeld ist die Einführung von 3D-Drucktechnologien in der Turbinenfertigung. Der 3D-Druck ermöglicht eine präzisere Herstellung von komplexen Schaufelgeometrien und anderen Turbinenkomponenten, die mit herkömmlichen Fertigungsmethoden schwer oder gar nicht realisierbar wären. Durch diese Technologie können die Schaufeln und Leitschaufeln so gestaltet werden, dass sie eine noch gleichmäßigere Strömung des Dampfs ermöglichen und somit die Dampfexpansion weiter optimieren. Dies führt zu einer Verbesserung der Effizienz und verringert den Energieverlust durch Turbulenzen und unregelmäßige Strömung.
Darüber hinaus wird die Digitalisierung und Automatisierung von Dampfturbinenanlagen zunehmend wichtiger. Moderne Dampfturbinen sind mit einer Vielzahl von Sensoren ausgestattet, die die wichtigsten Parameter wie Dampfdruck, Temperatur, Strömungsgeschwindigkeit und Vibrationen in Echtzeit überwachen. Diese Daten werden an zentrale Steuerungseinheiten weitergeleitet, die mithilfe von fortschrittlichen Algorithmen und Künstlicher Intelligenz (KI) die Dampfexpansion kontinuierlich an die aktuellen Betriebsbedingungen anpassen. KI-basierte Systeme können schnell auf Veränderungen reagieren und den Dampfstrom optimieren, um den Wirkungsgrad der Turbine zu maximieren. Gleichzeitig ermöglicht die kontinuierliche Überwachung, dass potenzielle Probleme frühzeitig erkannt werden, wodurch Wartungskosten gesenkt und Ausfallzeiten minimiert werden.
Die Flexibilität der Dampfexpansion wird auch durch den Einsatz von variablen Turbinengeometrien erhöht. Hierbei kommen sogenannte verstellbare Leitschaufeln und verstellbare Laufschaufeln zum Einsatz, die es ermöglichen, den Dampfstrom in Echtzeit an die unterschiedlichen Lastbedingungen anzupassen. Diese Anpassungen verbessern die Effizienz der Turbine, insbesondere in Situationen, in denen der Dampf nicht konstant mit maximaler Leistung expandiert, wie es bei der Nutzung von erneuerbaren Energiequellen der Fall sein kann. Solche flexiblen Betriebsarten sind besonders wichtig in modernen Kraftwerken, die zunehmend auf eine Mischung aus erneuerbaren und fossilen Energieträgern angewiesen sind, und ermöglichen eine Optimierung des gesamten Kraftwerksbetriebs.
Ein weiterer interessanter Trend ist die Entwicklung von “Supercritical” und “Ultra-supercritical” Dampfturbinen. Diese Turbinen arbeiten mit Dampfdruck und -temperaturen, die über den kritischen Punkt hinausgehen, wodurch die thermische Effizienz signifikant gesteigert wird. Die Dampfexpansion in solchen Turbinen erfolgt unter extrem hohen Drücken und Temperaturen, was zu einer noch besseren Umwandlung von Wärme in mechanische Arbeit führt. Dies erfordert jedoch spezielle Materialien, die in der Lage sind, diesen extremen Bedingungen standzuhalten. Daher ist die Forschung in diesem Bereich besonders intensiv, um geeignete Werkstoffe und Designmethoden zu entwickeln, die eine effiziente und langlebige Expansion des Dampfs bei diesen hohen Parametern gewährleisten.
Zusätzlich zur Effizienzsteigerung durch technologische Innovationen ist die Optimierung der Betriebsbedingungen in Bezug auf den gesamten Kraftwerksbetrieb von großer Bedeutung. Die Dampfexpansion ist dabei nur ein Teil eines komplexen Systems, das die Energieerzeugung möglichst effizient und umweltfreundlich gestalten soll. So wird der Prozess der Dampfexpansion in den Gesamtkontext des Kraftwerksbetriebs integriert, um sowohl die Effizienz der einzelnen Turbinenstufen als auch die Gesamtleistung der Anlage zu maximieren. Durch den Einsatz von datenbasierten Modellen und prädiktiven Wartungssystemen kann der Betrieb der Dampfturbine optimiert werden, was zu einer weiteren Reduzierung der Betriebskosten und einer Erhöhung der Lebensdauer der Turbine führt.
Nicht zuletzt wird die Dampfexpansion auch im Zusammenhang mit der Reduzierung von Treibhausgasemissionen und der Verbesserung der Umweltbilanz von Kraftwerken immer wichtiger. Die höhere Effizienz bei der Energieumwandlung führt zu einer Verringerung des Brennstoffverbrauchs und damit auch zu einer Senkung der CO₂-Emissionen. In Kombination mit CO₂-Abscheidetechnologien oder in hybridisierten Anlagen, die beispielsweise mit erneuerbarem Strom kombiniert werden, kann die Dampfexpansion zu einer Schlüsseltechnologie für die Dekarbonisierung der Energieproduktion werden.
Insgesamt zeigt sich, dass die Dampfexpansion in Dampfturbinen ein komplexer, aber äußerst entscheidender Prozess für die Energieumwandlung ist. Durch kontinuierliche Innovationen in den Bereichen Materialtechnik, Fertigung, Digitalisierung und Betriebsoptimierung wird der Prozess immer effizienter und flexibler. Diese Entwicklungen tragen nicht nur zur Steigerung der Leistung und Lebensdauer von Dampfturbinen bei, sondern auch zur nachhaltigen Verbesserung der Energieproduktion weltweit.
Wirkungsgrad
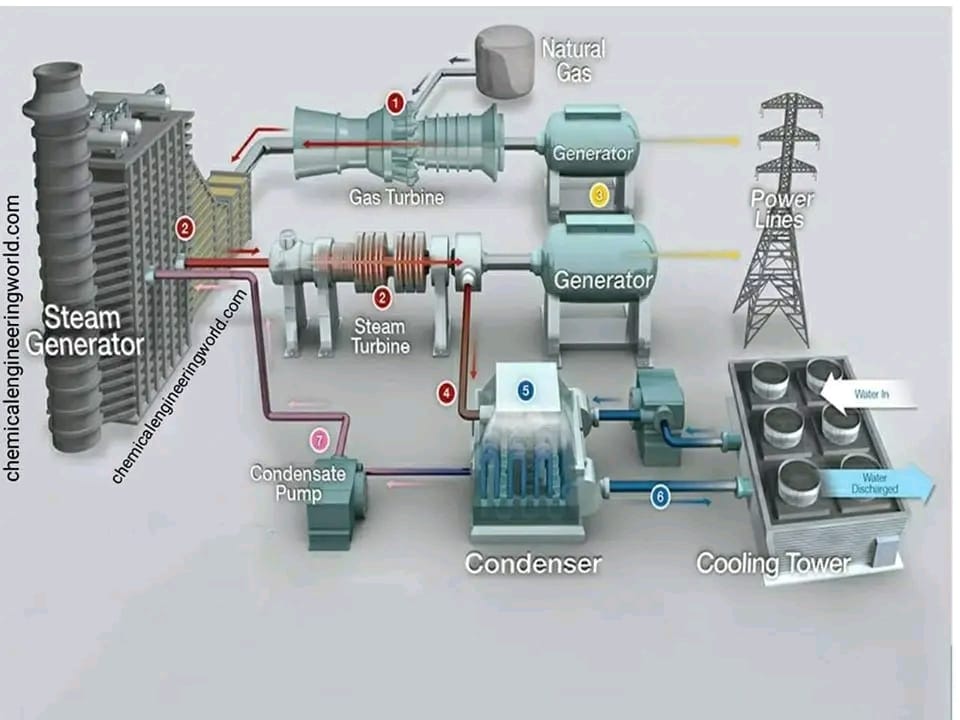
Der Wirkungsgrad einer Dampfturbine ist ein Maß dafür, wie effizient die Turbine die im Dampf enthaltene thermische Energie in mechanische Arbeit umwandelt. Ein hoher Wirkungsgrad bedeutet, dass ein größerer Anteil der zugeführten Energie in nützliche Arbeit umgewandelt wird, während ein niedriger Wirkungsgrad darauf hinweist, dass viel Energie verloren geht, hauptsächlich durch Wärmeverluste und ineffiziente Umwandlungsprozesse. Der Wirkungsgrad wird maßgeblich durch verschiedene Faktoren beeinflusst, darunter die Temperatur und der Druck des Dampfs, die Effizienz der Dampfturbinenstufen, die Gestaltung der Schaufeln, die Strömungsführung und die Art und Weise, wie der Dampf expandiert. Ein idealer Wirkungsgrad würde bedeuten, dass keinerlei Energie durch Reibung, Turbulenzen oder Wärmeverlust verloren geht, was in der Praxis jedoch nicht erreichbar ist.
Der Wirkungsgrad einer Dampfturbine ist typischerweise in einer Reihe von Bereichen messbar, etwa als Isentropenwirkungsgrad, der den Anteil der Energie darstellt, der unter der Annahme eines idealen thermodynamischen Prozesses, bei dem keine Entropie erzeugt wird, in Arbeit umgewandelt wird. Ein weiterer wichtiger Parameter ist der thermische Wirkungsgrad des gesamten Dampfkraftwerks, der angibt, wie gut das Kraftwerk in der Lage ist, die im Brennstoff enthaltene Energie in elektrischen Strom umzuwandeln. Der Wirkungsgrad hängt eng mit der Temperaturdifferenz zwischen dem Dampf und dem Kondensator ab, wobei größere Temperaturdifferenzen zu höheren Wirkungsgraden führen. Eine Optimierung des Wirkungsgrads kann durch verschiedene Maßnahmen erreicht werden, wie die Erhöhung des Dampfdrucks und der Dampftemperatur, den Einsatz von Regenerativheizsystemen oder die Verbesserung der Turbinentechnologie, etwa durch die Nutzung von Supercritical- oder Ultra-Supercritical-Dampfturbinen.
Diese Maßnahmen ermöglichen eine effizientere Energieumwandlung, indem sie den thermodynamischen Prozess näher an den idealen Zustand bringen. Die kontinuierliche Verbesserung des Wirkungsgrads ist für die Effizienzsteigerung und die Reduzierung des Brennstoffverbrauchs in Dampfturbinen und damit auch für die Verringerung der CO₂-Emissionen von entscheidender Bedeutung. Ein hoher Wirkungsgrad ist also nicht nur aus wirtschaftlicher Sicht wichtig, sondern auch für den nachhaltigen Betrieb von Dampfturbinen und die Verbesserung der Energieeffizienz im globalen Maßstab.
Der Wirkungsgrad einer Dampfturbine spielt eine entscheidende Rolle bei der Bestimmung der Gesamtleistung und Effizienz eines Dampfkraftwerks. Ein höherer Wirkungsgrad bedeutet, dass mehr von der thermischen Energie im Dampf in mechanische Arbeit umgewandelt wird, was den Gesamtenergieverbrauch pro erzeugter Kilowattstunde Strom reduziert. Dies trägt direkt zur Senkung der Betriebskosten und zur Verringerung des Brennstoffverbrauchs bei, was wiederum zur Minimierung der Umweltauswirkungen führt. Die Maximierung des Wirkungsgrads ist insbesondere in Zeiten steigender Energiepreise und wachsender Anforderungen an die CO₂-Reduktion von großer Bedeutung.
Ein wichtiger Faktor für den Wirkungsgrad ist die Temperatur des Dampfes, der in die Turbine eintritt. Laut den Grundsätzen der Thermodynamik führt eine höhere Dampftemperatur zu einer größeren Differenz zwischen der Energie im Dampf und der Energie im Kondensator, was wiederum eine effizientere Umwandlung von thermischer in mechanische Energie ermöglicht. Supercritical- und Ultra-Supercritical-Technologien nutzen diese Idee, indem sie Dämpfe mit deutlich höheren Drücken und Temperaturen erzeugen, als es in traditionellen Dampfturbinen der Fall ist. Diese Technologien können damit den thermischen Wirkungsgrad erheblich verbessern, da sie den Dampf bei höheren Temperaturen und Drücken expandieren lassen, was die Energieausbeute steigert.
Neben der Dampftemperatur ist auch der Dampfdruck ein wichtiger Einflussfaktor auf den Wirkungsgrad. Ein höherer Dampfdruck, insbesondere in den frühen Stufen der Turbine, ermöglicht eine größere Umwandlung der Wärmeenergie in mechanische Arbeit. Dies wird durch den Einsatz von Zwischenüberhitzern und Hochdruckturbinen erreicht, die den Dampfdruck weiter erhöhen und so die thermodynamische Effizienz steigern. Doch auch hier gibt es physikalische Grenzen, da zu hohe Drücke die Materialbelastungen der Turbine stark erhöhen und den Bedarf an hochfesten Materialien steigern, die höheren Temperaturen und Drücken standhalten können.
Ein weiterer kritischer Aspekt ist die Strömungsführung und der Luftwiderstand innerhalb der Turbine. Um den Wirkungsgrad zu maximieren, muss der Dampf möglichst effizient durch die Turbinenstufen geführt werden, ohne dass es zu unnötigen Energieverlusten kommt. Die präzise Gestaltung der Leitschaufeln und Laufschaufeln, die eine gleichmäßige Strömung des Dampfs gewährleisten, sowie die Minimierung von Turbulenzen und Reibungsverlusten sind entscheidend. Eine ineffiziente Strömungsführung, wie sie durch unzureichend designte Schaufeln oder fehlerhafte Geometrien entstehen kann, führt zu einer Erhöhung des Energieverlustes und einer Verringerung des Gesamtwirkungsgrads.
Die Technik der Dampfexpansion spielt ebenfalls eine Schlüsselrolle. Die Art und Weise, wie der Dampf in den verschiedenen Turbinenstufen expandiert, beeinflusst direkt die Umwandlung von Wärme in Arbeit. Die Expansion muss schrittweise und kontrolliert erfolgen, um den Druckverlust gleichmäßig zu verteilen und eine möglichst hohe Leistung in jeder Turbinenstufe zu erzielen. Ein abruptes Abfallen des Dampfdrucks oder eine zu schnelle Expansion führt zu einem ineffizienten Umwandlungsprozess und verringert den Wirkungsgrad. Daher müssen die Leitschaufeln und Laufschaufeln so ausgelegt sein, dass der Dampf in einem optimalen Winkel und mit der richtigen Geschwindigkeit auf die Laufschaufeln trifft, was eine maximale Umwandlung der thermischen Energie in mechanische Arbeit ermöglicht.
Eine weitere Möglichkeit zur Steigerung des Wirkungsgrads ist der Einsatz von Regeneratoren und Überhitzern, die die Abwärme des Dampfes vor der Rückführung in den Boiler nutzen. Diese Vorrichtungen erhöhen die Effizienz, indem sie den Dampf vor der Rückführung in den Heizkreislauf weiter erhitzen, wodurch weniger Brennstoff benötigt wird, um den Dampf auf die gewünschte Temperatur zu bringen. Diese Technologien reduzieren den Brennstoffverbrauch und erhöhen gleichzeitig den Gesamtwirkungsgrad des Systems.
Zusätzlich sind moderne Steuerungssysteme und Optimierungsalgorithmen unerlässlich, um den Wirkungsgrad zu maximieren. Diese Systeme überwachen kontinuierlich alle relevanten Betriebsparameter wie Dampfdruck, -temperatur und Strömungsraten und passen die Betriebsbedingungen in Echtzeit an, um den Wirkungsgrad unter wechselnden Lastbedingungen zu maximieren. In Kraftwerken mit variablen Lasten, wie sie zum Beispiel in Kombination mit erneuerbaren Energiequellen betrieben werden, helfen diese Systeme, die Turbinenleistung dynamisch anzupassen, sodass der Wirkungsgrad auch unter unterschiedlichen Betriebsbedingungen optimal bleibt.
Schließlich ist der Wirkungsgrad auch von der Fähigkeit des Systems abhängig, Wärmeverluste zu minimieren. In Dampfturbinenanlagen ist eine effiziente Wärmedämmung von entscheidender Bedeutung, um die Abwärme zu reduzieren, die ansonsten ungenutzt an die Umgebung abgegeben werden würde. Eine effektive Isolierung der Dampfleitungen, Turbinengehäuse und Kondensatoren trägt dazu bei, die thermische Energie zu bewahren und die Effizienz der Umwandlung zu maximieren.
Insgesamt lässt sich sagen, dass der Wirkungsgrad einer Dampfturbine von einer Vielzahl von Faktoren abhängt, die miteinander interagieren und optimiert werden müssen. Durch den Einsatz fortschrittlicher Technologien wie Hochdruck- und Hochtemperaturdampfturbinen, innovativer Schaufeldesigns, besserer Strömungsführung und modernster Steuerungssysteme wird es möglich, den Wirkungsgrad von Dampfturbinen kontinuierlich zu verbessern. Dies führt nicht nur zu einer Reduktion des Brennstoffverbrauchs und der Betriebskosten, sondern auch zu einer umweltfreundlicheren und nachhaltigeren Energieerzeugung.
Die kontinuierliche Verbesserung des Wirkungsgrads von Dampfturbinen ist nicht nur aus technischer und ökonomischer Sicht wichtig, sondern auch aus ökologischer Perspektive. Durch die Steigerung des Wirkungsgrads kann der Energieverbrauch gesenkt und die CO₂-Emissionen verringert werden, was eine zentrale Rolle bei der Erreichung globaler Klimaziele spielt. In modernen Kraftwerksanlagen wird der Wirkungsgrad als Schlüsselfaktor betrachtet, um die Umweltauswirkungen zu minimieren und gleichzeitig eine zuverlässige Energieversorgung sicherzustellen. Die Entwicklung neuer Technologien, die den Wirkungsgrad weiter steigern, hat daher sowohl ökologische als auch ökonomische Bedeutung.
Ein vielversprechender Ansatz zur weiteren Effizienzsteigerung sind sogenannte hybride Dampfturbinenkraftwerke, die auf eine Kombination aus traditionellen fossilen Brennstoffen und erneuerbaren Energiequellen setzen. In solchen Anlagen können Dampfturbinen durch den Einsatz von Solarenergie oder Biomasse zusätzlich unterstützt werden, um die Effizienz weiter zu erhöhen und den Brennstoffverbrauch zu verringern. In Solarthermiekraftwerken, bei denen Solarenergie genutzt wird, um Dampf zu erzeugen, können Turbinen ebenfalls so optimiert werden, dass sie unter schwankenden Energiebedingungen mit hoher Effizienz arbeiten. Diese hybride Nutzung von Energiequellen erfordert eine genaue Abstimmung der Dampfturbine auf verschiedene Betriebsbedingungen, wobei die Turbinensteuerung und die Anpassung des Dampfstroms eine zentrale Rolle spielen, um den Wirkungsgrad bei wechselnden Lasten zu maximieren.
Ein weiteres Konzept zur Effizienzsteigerung ist die sogenannte „Abwärmenutzung“ oder „Kraft-Wärme-Kopplung“ (KWK), bei der die Abwärme aus dem Dampfturbinenprozess nicht nur zur Stromerzeugung genutzt wird, sondern auch für industrielle Prozesse oder Heizungsanwendungen. Durch die Integration von KWK-Technologien wird der Gesamtwirkungsgrad des Systems erheblich gesteigert, da die Abwärme, die normalerweise verloren gehen würde, genutzt wird, um zusätzliche Energie zu erzeugen. Dies macht das System insgesamt viel effizienter und reduziert den Gesamtbrennstoffverbrauch und die CO₂-Emissionen, indem mehrere Energiebedarfe gleichzeitig gedeckt werden.
Der Fortschritt in der Überwachung und Analyse von Turbinenprozessen hat ebenfalls eine bedeutende Rolle bei der Verbesserung des Wirkungsgrads gespielt. Mit Hilfe von Sensoren, die in die Turbine integriert sind, sowie fortschrittlicher Analysetechnologie können Kraftwerksbetreiber in Echtzeit Daten zu Druck, Temperatur, Strömungsgeschwindigkeit und anderen relevanten Parametern sammeln. Diese Daten werden durch moderne Steuerungssysteme verarbeitet, die sofort Anpassungen an den Betriebsbedingungen vornehmen, um die Turbine stets unter den optimalen Bedingungen arbeiten zu lassen. Diese Anpassungsfähigkeit hilft nicht nur, den Wirkungsgrad zu maximieren, sondern auch, den Verschleiß von Turbinenkomponenten zu verringern und die Lebensdauer der Turbine zu verlängern, was zu geringeren Wartungskosten und einer höheren Betriebseffizienz führt.
Auch die kontinuierliche Forschung zu neuen Materialien hat eine Schlüsselrolle bei der Verbesserung des Wirkungsgrads von Dampfturbinen. Hochleistungswerkstoffe, die extremen thermischen und mechanischen Belastungen standhalten, ermöglichen eine effiziente Nutzung von Hochtemperaturdampf ohne die Gefahr einer vorzeitigen Materialermüdung oder Korrosion. Materialien wie hochfeste Nickellegierungen oder Keramiken, die bei höheren Temperaturen stabil bleiben, ermöglichen es, Dampfturbinen mit noch höheren Drücken und Temperaturen zu betreiben, was die Effizienz weiter steigert. Diese Materialien machen den Betrieb von Supercritical- und Ultra-Supercritical-Dampfturbinen möglich, bei denen der Dampfdruck und die Temperatur die bisherigen Grenzen herkömmlicher Turbinen übersteigen, was zu einer besseren Energieausbeute führt.
Insgesamt zeigt sich, dass der Wirkungsgrad von Dampfturbinen ein zentraler Bestandteil der modernen Energieerzeugungstechnologie ist, der eng mit der Leistungsfähigkeit von Dampfturbinen, der ökologischen Nachhaltigkeit und der Wirtschaftlichkeit von Kraftwerksbetrieben verknüpft ist. Die kontinuierliche Optimierung der Turbinenkomponenten, der Steuerungssysteme, der verwendeten Materialien sowie der Integration von neuen Technologien wie hybriden Kraftwerken und Abwärmenutzungssystemen stellt sicher, dass Dampfturbinen auch in Zukunft eine Schlüsselrolle in der effizienten und nachhaltigen Energieerzeugung spielen werden.
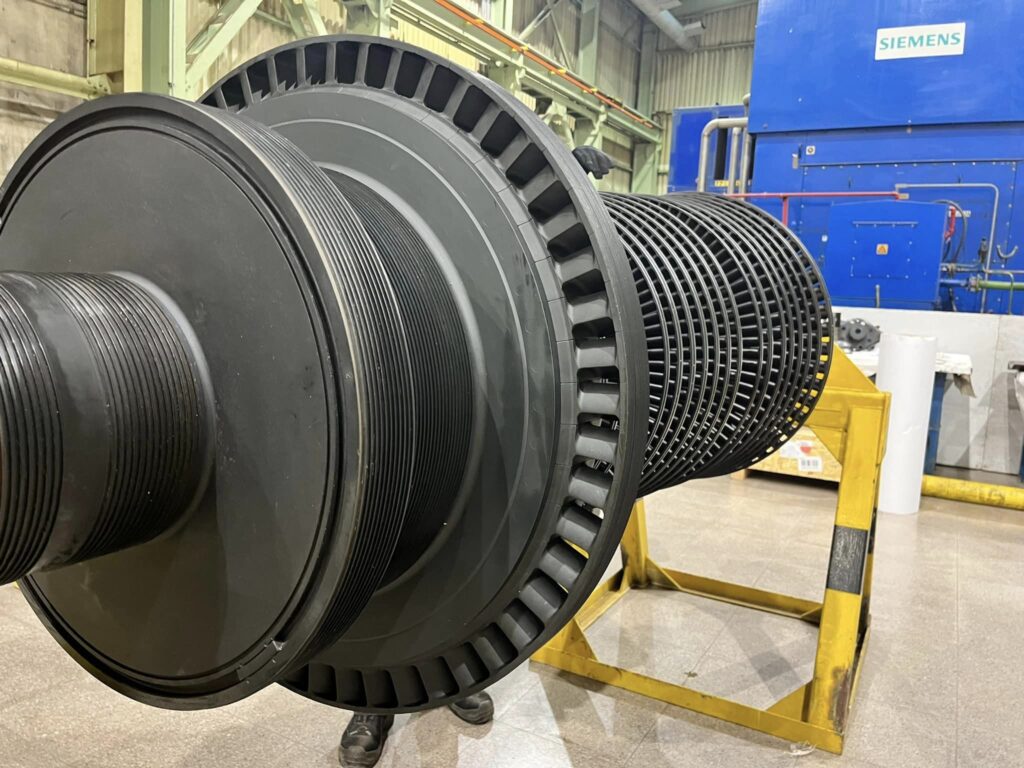
Der Fortschritt in der Dampfturbinen-Technologie und der stetige Fokus auf die Effizienzsteigerung führt zu immer höheren Anforderungen an das gesamte Kraftwerksdesign. Um den Wirkungsgrad weiter zu maximieren, sind nicht nur technologische Innovationen bei den Turbinen selbst erforderlich, sondern auch eine systematische Optimierung des gesamten thermischen Prozesses, der die Dampfturbinen umgibt. Die kontinuierliche Verbesserung der Effizienz bedeutet nicht nur eine Verringerung des Brennstoffverbrauchs, sondern auch eine signifikante Reduzierung der Betriebskosten, was zu einer höheren Wettbewerbsfähigkeit von Dampfturbinenkraftwerken auf dem Energiemarkt führt.
Ein Bereich, der zunehmend an Bedeutung gewinnt, ist die Integration von Digitalisierung und Künstlicher Intelligenz (KI) in die Betriebsführung und Wartung von Dampfturbinen. Mithilfe von Big Data und fortschrittlichen Algorithmen können große Mengen an Betriebsdaten analysiert und ausgewertet werden, um Muster zu erkennen und vorherzusagen, wann und warum Energieverluste oder ineffiziente Betriebszustände auftreten. Diese datengetriebenen Ansätze ermöglichen eine proaktive Wartung, die nicht nur Ausfallzeiten minimiert, sondern auch den Betrieb optimiert und den Wirkungsgrad kontinuierlich überwacht. Predictive-Maintenance-Technologien, die auf KI basieren, können beispielsweise frühzeitig auf Verschleißerscheinungen oder Probleme mit den Turbinenkomponenten hinweisen, bevor diese zu größeren Störungen führen, und so den effizienten Betrieb über die gesamte Lebensdauer der Turbine sichern.
Darüber hinaus ist der Aspekt der Flexibilität bei Dampfturbinen zunehmend von Bedeutung, insbesondere in Bezug auf die Integration erneuerbarer Energiequellen wie Wind- und Solarenergie, die fluktuierende Strommengen liefern. Dampfturbinen in modernen Kraftwerken müssen zunehmend in der Lage sein, schnell auf wechselnde Lastanforderungen zu reagieren und ihre Effizienz auch unter diesen variablen Bedingungen aufrechtzuerhalten. Hier bieten verstellbare Turbinengeometrien, wie etwa verstellbare Leitschaufeln oder variable Laufschaufeln, eine hervorragende Lösung, um den Dampfturbinenbetrieb dynamisch an unterschiedliche Lastprofile anzupassen. Diese Technologie erlaubt eine präzisere Steuerung des Dampfstroms und sorgt dafür, dass die Turbine immer unter den optimalen Betriebsbedingungen arbeitet, was den Wirkungsgrad auch unter wechselnden Belastungen maximiert.
In einem weiteren Schritt sind auch Entwicklungen im Bereich der Brennstofftechnologie von großer Bedeutung für den Wirkungsgrad von Dampfturbinen. Die Umstellung auf kohlenstoffärmere Brennstoffe wie Biomasse, synthetische Brennstoffe oder Wasserstoff könnte die Effizienz in einem zukünftigen, nachhaltigeren Energiesystem weiter verbessern. Die Verbrennung dieser Brennstoffe kann zu einer höheren Dampftemperatur und damit zu einer besseren thermodynamischen Effizienz führen. Allerdings erfordert dies eine Anpassung der Turbinentechnologie, insbesondere im Hinblick auf die Kompatibilität mit den spezifischen Eigenschaften dieser Brennstoffe, was sowohl Forschung als auch Anpassungen im Turbinendesign mit sich bringt.
Zudem wird in vielen Ländern die Rolle der Kohlenstoffabschaltung und die Entwicklung von CO₂-Abscheidungstechnologien für fossile Kraftwerke zunehmend in den Fokus gerückt. Die Dampfturbinen in diesen Anlagen könnten von Fortschritten in der CO₂-Abscheidung profitieren, da Technologien zur CO₂-Reduktion die Effizienz in Kraftwerksprozessen weiter steigern können. Bei der Integration dieser Technologien könnte eine gleichzeitige Reduzierung von Energieverlusten und eine Minimierung der Umweltbelastung erreicht werden, wodurch Dampfturbinen einen noch wichtigeren Beitrag zur nachhaltigen Energieerzeugung leisten.
Die weitere Verbesserung des Wirkungsgrads geht auch mit einer besseren Integration von Dampfturbinen in den Gesamtenergiemix eines Landes oder einer Region einher. Moderne Dampfturbinenkraftwerke werden zunehmend mit anderen Energiequellen kombiniert, wie beispielsweise Geothermie, um den Wirkungsgrad zu optimieren und den Übergang zu einem dekarbonisierten Energiesystem zu unterstützen. In solchen Hybridkraftwerken wird der Wirkungsgrad der Dampfturbine durch die Kombination von Wärmequellen mit unterschiedlichen Charakteristiken weiter gesteigert.
Zusammenfassend lässt sich sagen, dass der Wirkungsgrad von Dampfturbinen ein dynamisches und hochgradig technisches Konzept ist, das von einer Vielzahl von Faktoren beeinflusst wird. Fortschritte in der Turbinentechnologie, der Materialwissenschaft, der Digitalisierung, der Steuerungstechnik sowie der Integration erneuerbarer Energien und kohlenstoffarmer Brennstoffe bieten ein großes Potenzial zur weiteren Effizienzsteigerung. In Kombination mit innovativen Ansätzen zur Prozessoptimierung und flexiblen Betriebsführung, wird der Wirkungsgrad in Zukunft weiterhin verbessert und trägt zu einer nachhaltigeren und wirtschaftlicheren Energieerzeugung bei. Die Herausforderungen bei der Steigerung des Wirkungsgrads erfordern jedoch ein kontinuierliches Engagement für Forschung und Entwicklung, um die Potenziale der Dampfturbinen vollständig auszuschöpfen und gleichzeitig die Umweltbelastungen zu minimieren.
Impuls- und Reaktionsturbinen
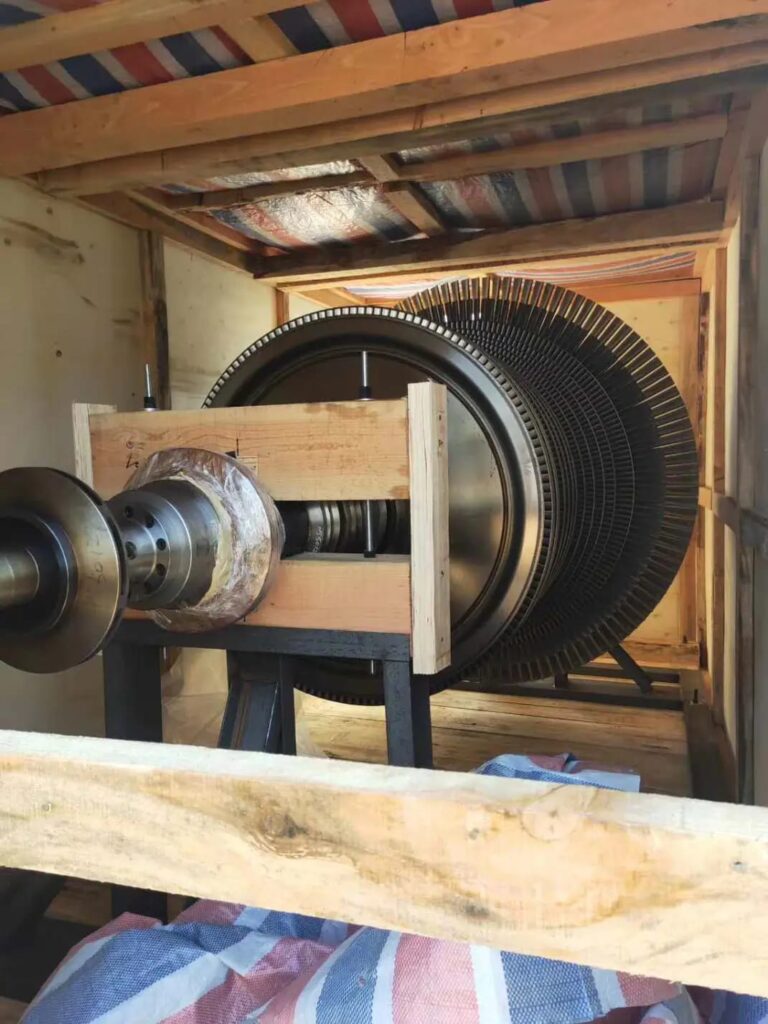
Impuls- und Reaktionsturbinen sind zwei grundlegende Typen von Dampfturbinen, die sich hinsichtlich ihrer Funktionsweise und der Art und Weise, wie sie die Energie des Dampfs nutzen, unterscheiden. In einer Impulsturbine wird die gesamte Energie des Dampfs in der ersten Stufe der Turbine durch die Beschleunigung des Dampfs auf eine sehr hohe Geschwindigkeit umgesetzt.
Der Dampf tritt durch Düsen in die Turbine ein und trifft dort auf die Schaufeln der Laufschaufeln. Der Dampf strömt mit hoher Geschwindigkeit und gibt seine kinetische Energie auf die Laufschaufeln ab, wodurch diese in Rotation versetzt werden. Diese Art der Turbine nutzt also den Impuls des Dampfs, um mechanische Arbeit zu erzeugen. Der Druck des Dampfs bleibt beim Durchströmen der Schaufeln fast konstant, da die Energie hauptsächlich in Form von Geschwindigkeit umgesetzt wird. Ein Beispiel für eine Impulsturbine ist die Pelton-Turbine, bei der der Dampf mit hoher Geschwindigkeit auf Schaufeln trifft und deren Impuls die Rotationsbewegung erzeugt.
Im Gegensatz dazu nutzt eine Reaktionsturbine die Druckänderung des Dampfs zur Energieumwandlung. Hier wird der Dampf in mehreren Stufen durch die Turbine geführt, wobei der Druck im Turbinengehäuse kontinuierlich abnimmt. In jeder Stufe wird ein Teil der Energie des Dampfs durch die Wechselwirkung zwischen Dampf und Schaufeln in mechanische Arbeit umgewandelt. Der Dampf expandiert also in der Turbine, wobei sowohl die kinetische Energie als auch die potenzielle Energie des Dampfs in Rotation umgewandelt werden. Diese Art der Turbine wird häufig in großen Dampfturbinenanlagen verwendet, da sie eine höhere Effizienz und eine bessere Leistung bei hohem Durchsatz ermöglicht. Ein bekanntes Beispiel für eine Reaktionsturbine ist die Francis-Turbine, bei der der Dampf in mehrere Stufen expandiert, was zu einer gleichmäßigen Umwandlung von Druck und Kinetischer Energie führt.
Beide Turbinenarten – Impuls- und Reaktionsturbinen – haben ihre spezifischen Einsatzgebiete, wobei Impulsturbinen besonders dann vorteilhaft sind, wenn eine hohe Geschwindigkeit und eine präzise Steuerung der Dampfströme erforderlich sind, während Reaktionsturbinen ihre Stärken in Anwendungen mit großen Volumenströmen und höherer Effizienz ausspielen. Die Wahl zwischen einer Impuls- und einer Reaktionsturbine hängt daher von den spezifischen Anforderungen der jeweiligen Dampfturbinenanwendung ab, wie etwa der benötigten Leistung, den Betriebsbedingungen und der gewünschten Effizienz.
Im Bereich der Dampfturbinen haben sowohl Impuls- als auch Reaktionsturbinen ihre einzigartigen Merkmale und Anwendungen, die sie für unterschiedliche Betriebsbedingungen geeignet machen. Bei Impulsturbinen ist die Umwandlung der Energie des Dampfs direkt mit der Geschwindigkeit des Dampfs verbunden. Der Dampf tritt durch Düsen mit hoher Geschwindigkeit in die Turbine ein, und die Schaufeln werden durch den Impuls des sich beschleunigenden Dampfs in Bewegung gesetzt. Ein bemerkenswerter Vorteil dieser Konstruktion ist die einfache Kontrolle des Dampfs, da der Dampf in der Regel nur in der ersten Stufe seiner Expansion beschleunigt wird. Impuls-Turbinen sind daher besonders geeignet für Anwendungen, bei denen der Dampf in einer bestimmten Geschwindigkeit und mit einem kontrollierten Druckstrahl eingesetzt werden muss. Da der Druck des Dampfs in Impulsturbinen nicht so stark abnimmt wie in Reaktionsturbinen, sind sie häufig in Anwendungen mit weniger komplexen Druck- und Temperaturanforderungen zu finden.
Im Gegensatz dazu wird in Reaktionsturbinen die gesamte Energie des Dampfs durch eine Kombination von Druck und Geschwindigkeit in mechanische Arbeit umgewandelt. Der Dampf wird in mehreren Stufen geführt, wobei der Druck von Stufe zu Stufe abnimmt. In jeder dieser Stufen gibt der Dampf sowohl einen Teil seiner Energie in Form von kinetischer Energie ab, als auch in Form von Druckenergie. Das bedeutet, dass in Reaktionsturbinen der Dampf ständig expandiert, was zu einer kontinuierlichen Umwandlung der thermischen Energie des Dampfs in mechanische Arbeit führt. Diese Art der Turbine erfordert komplexere geometrische Formen der Schaufeln und eine präzise Steuerung der Dampfströmung, um den maximalen Energiegewinn zu erzielen. Reaktionsturbinen sind aufgrund ihrer Fähigkeit, große Mengen an Dampf effizient zu nutzen, oft in großtechnischen Anlagen wie in Stromkraftwerken zu finden, wo hohe Durchsatzraten und eine konstante Leistung erforderlich sind.
Ein entscheidender Unterschied zwischen diesen beiden Turbinenarten liegt in der Gestaltung der Schaufeln. Bei Impulsturbinen sind die Schaufeln typischerweise so gestaltet, dass sie die kinetische Energie des Dampfs maximieren, während bei Reaktionsturbinen die Schaufeln so ausgelegt sind, dass sie die kontinuierliche Expansion des Dampfs über mehrere Stufen hinweg effektiv nutzen. Dies bedeutet, dass die Schaufeln in Reaktionsturbinen nicht nur in der Lage sein müssen, den Dampf in Bewegung zu setzen, sondern auch dessen Druckänderungen über mehrere Expansionsphasen hinweg zu bewältigen.
In Bezug auf den Betrieb sind Impulsturbinen oft robuster und weniger anfällig für Instabilitäten, da sie mit einer relativ konstanten Geschwindigkeit arbeiten, während Reaktionsturbinen effizienter sind, aber eine sorgfältige Steuerung erfordern, um sicherzustellen, dass der Dampf in jedem Expansionsstadium optimal genutzt wird. Dies hat zur Folge, dass Reaktionsturbinen in größeren Anlagen mit konstanten Betriebsbedingungen und hohem Energiebedarf bevorzugt werden, während Impulsturbinen in kleineren Anlagen oder in Anwendungen, bei denen eine präzisere Steuerung des Dampfs erforderlich ist, häufig anzutreffen sind.
Im praktischen Einsatz werden Impuls- und Reaktionsturbinen oft in Kombination verwendet, um die Vorteile beider Prinzipien zu maximieren. In vielen modernen Kraftwerken finden sich hybride Turbinensysteme, bei denen Impulsturbinen in den ersten Stufen und Reaktionsturbinen in den folgenden Stufen eingesetzt werden, um sowohl eine hohe Geschwindigkeit als auch eine hohe Effizienz zu gewährleisten. Diese Kombination ermöglicht es, die Vorteile beider Technologien zu nutzen, um den Gesamtwirkungsgrad der Anlage zu maximieren. Dabei sind die Impulsturbinen für die schnelle Beschleunigung und die Reaktionsturbinen für die gleichmäßige und effiziente Umwandlung der Dampfenergie verantwortlich.
Die Wahl zwischen Impuls- und Reaktionsturbinen hängt letztlich von den spezifischen Anforderungen der Anwendung ab, insbesondere von der Dampfmenge, der gewünschten Leistung und den Betriebsbedingungen. Impulsturbinen eignen sich besonders für Anwendungen, bei denen hohe Drehzahlen und präzise Steuerungen erforderlich sind, während Reaktionsturbinen bei größeren, energieintensiveren Anwendungen wie Stromerzeugung und industriellen Prozessen zum Einsatz kommen. Beide Typen haben ihren Platz in der modernen Energietechnik, und ihre Weiterentwicklung wird weiterhin entscheidend zur Effizienzsteigerung von Dampfturbinen und damit zur Energieproduktion im Allgemeinen beitragen.
Die Weiterentwicklung von Impuls- und Reaktionsturbinen spielt eine zentrale Rolle in der Verbesserung der Gesamtleistung und Effizienz von Dampfturbinenkraftwerken und industriellen Anwendungen. Ein wichtiger Aspekt dabei ist die kontinuierliche Optimierung der Materialtechnologie, die es ermöglicht, Turbinen unter extremen Betriebsbedingungen effizienter zu betreiben. Da Dampfturbinen sowohl hohen Temperaturen als auch enormen mechanischen Belastungen ausgesetzt sind, werden fortschrittliche Legierungen und hitzebeständige Materialien entwickelt, um den Verschleiß und die Materialermüdung zu minimieren und gleichzeitig die Effizienz zu steigern. In modernen Turbinen werden immer häufiger hochfeste Materialien eingesetzt, die den Druck und die Temperatur besser bewältigen und eine längere Lebensdauer der Turbinenkomponenten gewährleisten.
Ein weiterer bedeutender Faktor für die Weiterentwicklung von Impuls- und Reaktionsturbinen ist die Verbesserung der aerodynamischen Gestaltung der Schaufeln. Der Luftwiderstand und die Strömungsverluste sind in beiden Turbinenarten kritische Punkte, die die Effizienz beeinträchtigen können. Durch die Anwendung fortschrittlicher Strömungsmechanik und die Verwendung von computergestützten Simulationsverfahren wird die Form der Schaufeln zunehmend optimiert, um die Strömung des Dampfs zu maximieren und die mechanische Arbeit effizienter in Drehmoment umzuwandeln. Dies führt zu einer Verringerung der Strömungsverluste und einer besseren Ausnutzung des Dampfs, was den Wirkungsgrad der Turbine insgesamt verbessert.
Ein bemerkenswerter Trend in der Dampfturbinenentwicklung ist der verstärkte Einsatz von hybriden Systemen, bei denen Impuls- und Reaktionsturbinen in einer einzigen Turbine kombiniert werden, um die Vorteile beider Prinzipien zu nutzen. Diese Hybridtechnologie wird vor allem in großen, modernen Kraftwerken verwendet, die eine hohe Leistungsdichte erfordern. Die Impulsturbinen werden oft in den ersten Stufen der Turbine eingesetzt, um den Dampf zu beschleunigen und ihn auf hohe Geschwindigkeiten zu bringen, während Reaktionsturbinen in den späteren Stufen den Dampf weiter expandieren lassen, um die restliche Energie in mechanische Arbeit umzuwandeln. Solche hybriden Systeme ermöglichen es, die Turbine an unterschiedliche Betriebsbedingungen anzupassen, wodurch die Flexibilität und Effizienz der gesamten Anlage erhöht wird.
Die Optimierung der Betriebsbedingungen ist ein weiteres wichtiges Forschungsfeld. Während Reaktionsturbinen typischerweise in Anlagen mit kontinuierlichem Betrieb und stabilen Lasten zum Einsatz kommen, können Impulsturbinen bei wechselnden Lastanforderungen von Vorteil sein. Um die Effizienz weiter zu steigern, ist es entscheidend, dass Dampfturbinen auch bei Schwankungen im Dampfstrom oder bei variierenden Belastungen ihre Leistung optimieren. Dies wird durch die Entwicklung intelligenter Steuerungssysteme erreicht, die es ermöglichen, den Dampfstrom in Echtzeit anzupassen, um immer den besten Wirkungsgrad zu erzielen. Diese Systeme sind in der Lage, auf Veränderungen der Lastanforderungen schnell zu reagieren und den Betrieb der Turbine optimal zu steuern, ohne dass es zu Leistungseinbußen kommt.
Die Flexibilität von Impuls- und Reaktionsturbinen wird auch durch die zunehmende Integration erneuerbarer Energiequellen und die Anpassung an unterschiedliche Brennstoffe erhöht. In hybriden Anlagen, in denen sowohl fossile Brennstoffe als auch erneuerbare Energien wie Biomasse oder Solarenergie genutzt werden, können Impuls- und Reaktionsturbinen so ausgelegt werden, dass sie unter den variierenden Bedingungen der verschiedenen Energiequellen arbeiten. Diese Flexibilität hilft dabei, die Effizienz von Kraftwerken zu maximieren und gleichzeitig den CO₂-Ausstoß zu minimieren, was im Kontext der globalen Energiewende von entscheidender Bedeutung ist.
Ein weiterer Schritt zur Verbesserung der Effizienz von Dampfturbinen ist die Forschung zu neuen Betriebsstrategien, wie der Verwendung von Überhitzer-Dampftechnologien oder der Erhöhung der Dampfdrücke. Durch die Nutzung von Überhitzern, die den Dampf auf noch höhere Temperaturen bringen, wird eine höhere thermodynamische Effizienz erreicht, da mehr Energie aus dem Dampf gewonnen werden kann. Diese Technologien sind jedoch mit Herausforderungen in Bezug auf Materialanforderungen und die thermische Belastung der Turbinenkomponenten verbunden. Durch die Entwicklung von Materialien, die auch unter extremen Bedingungen stabil bleiben, können diese Technologien jedoch weiterhin zur Verbesserung der Dampfturbinenleistung beitragen.
Zusammenfassend lässt sich sagen, dass die Weiterentwicklung von Impuls- und Reaktionsturbinen eng mit den Anforderungen an höhere Effizienz, Flexibilität und Nachhaltigkeit in der Energieerzeugung verbunden ist. Beide Turbinenarten haben ihre spezifischen Stärken und Einsatzgebiete, aber ihre Kombination und die kontinuierliche Optimierung von Design, Materialien und Betriebsstrategien ermöglichen es, die Leistungsfähigkeit von Dampfturbinen in einer Vielzahl von Anwendungen zu maximieren. Indem sie sich den Herausforderungen der modernen Energieerzeugung stellen, leisten Impuls- und Reaktionsturbinen einen entscheidenden Beitrag zur Schaffung effizienter, zuverlässiger und umweltfreundlicher Energiesysteme.
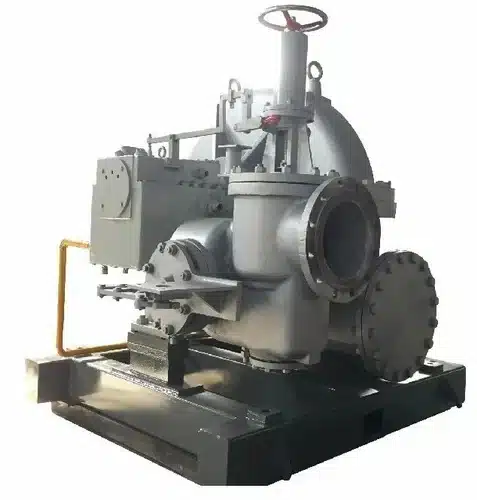
Ein weiterer entscheidender Faktor bei der Weiterentwicklung von Impuls- und Reaktionsturbinen ist die Integration von innovativen Technologien wie der Digitalisierung und Automatisierung. In modernen Dampfturbinenanlagen ist die Anwendung von Sensoren, Echtzeitüberwachungssystemen und fortschrittlicher Datenanalyse von großer Bedeutung. Diese Technologien ermöglichen es, Betriebsdaten in Echtzeit zu überwachen und darauf basierend proaktive Wartungsmaßnahmen zu ergreifen, bevor Probleme auftreten. Predictive Maintenance, das auf Künstlicher Intelligenz und maschinellem Lernen basiert, kann potenzielle Störungen im Turbinenbetrieb frühzeitig erkennen und so Ausfallzeiten minimieren. Für beide Turbinenarten bedeutet dies eine erhebliche Verbesserung der Zuverlässigkeit und Lebensdauer der Anlagen, da ihre Leistung kontinuierlich optimiert wird, basierend auf präzisen Vorhersagen und Anpassungen.
Die Digitalisierung hat auch Auswirkungen auf die Konstruktion und den Betrieb von Impuls- und Reaktionsturbinen. Durch den Einsatz von Simulationssoftware und Computational Fluid Dynamics (CFD) können Ingenieure das Verhalten von Dampfströmen in Turbinen mit noch nie dagewesener Präzision modellieren. Diese Simulationen ermöglichen eine tiefere Einsicht in die komplexen Strömungs- und Druckverhältnisse innerhalb der Turbine, was zu einer besseren Gestaltung der Schaufeln und einer noch effizienteren Umwandlung von thermischer Energie in mechanische Arbeit führt. Insbesondere bei Reaktionsturbinen, bei denen der Dampf in mehreren Stufen expandiert, können durch solche Simulationen die geometrierten Schaufeln optimiert und das Strömungsverhalten verbessert werden.
Für die Zukunft von Dampfturbinen sind auch die Bemühungen um die Verringerung von CO₂-Emissionen von zentraler Bedeutung. Die Industrie arbeitet intensiv an der Entwicklung von CO₂-Abscheidungstechnologien (CCS), die mit Dampfturbinenanlagen kombiniert werden können. Diese Technologien ermöglichen es, das CO₂, das bei der Verbrennung von fossilen Brennstoffen entsteht, abzufangen und zu speichern, bevor es in die Atmosphäre entweicht. In Kombination mit der Weiterentwicklung von Impuls- und Reaktionsturbinen könnte dies nicht nur zur Verbesserung der Effizienz der Turbinen führen, sondern auch dazu, dass Dampfturbinenkraftwerke noch umweltfreundlicher werden. Gleichzeitig werden auch neue Ansätze zur Nutzung erneuerbarer Energien wie Wasserstoff und Biomasse untersucht, bei denen Impuls- und Reaktionsturbinen eine Schlüsselrolle spielen könnten. Diese Brennstoffe ermöglichen eine nachhaltige Stromerzeugung und könnten langfristig fossile Brennstoffe in der Dampfturbinenanwendung ersetzen.
Ein weiterer wichtiger Trend ist die Entwicklung von Turbinen mit höherer Leistung und einer besseren Anpassungsfähigkeit an sich verändernde Lasten. Besonders in Zeiten des Übergangs zu mehr erneuerbaren Energiequellen und schwankender Stromerzeugung wird eine hohe Flexibilität von Kraftwerken gefordert. Dampfturbinen, die in der Lage sind, schnell auf Laständerungen zu reagieren und ihre Effizienz bei Teillast zu maximieren, werden immer wichtiger. Technologien wie variable Leitschaufeln und die Anpassung der Turbinensteuerungssysteme sind Schlüsselfaktoren, um diese Flexibilität zu erreichen. Sie ermöglichen es, die Energieumwandlung in der Turbine zu steuern und so die Gesamtleistung der Anlage aufrechtzuerhalten, auch wenn die Energiemenge aus erneuerbaren Quellen schwankt.
Die Weiterentwicklung von Impuls- und Reaktionsturbinen hat auch Auswirkungen auf kleinere und spezialisierte Anwendungen. Beispielsweise werden Impulsturbinen in immer mehr kompakten und mobilen Anwendungen eingesetzt, wie sie in der Schifffahrt, bei der Stromerzeugung in abgelegenen Gebieten oder in Industrien wie der Luftfahrt erforderlich sind. Diese mobilen Anwendungen erfordern eine hohe Leistung und Effizienz bei gleichzeitig geringerem Gewicht und optimierter Größe der Turbinen. In diesen Bereichen können Fortschritte in der Schaufeltechnologie und der Turbinenkonstruktion dazu beitragen, den Energieverbrauch zu senken und die Umweltauswirkungen zu minimieren.
Nicht zuletzt wird die wirtschaftliche Wettbewerbsfähigkeit von Dampfturbinen zunehmend von der Fähigkeit abhängen, die Gesamtbetriebskosten zu senken und den Energieverbrauch zu maximieren. Während sowohl Impuls- als auch Reaktionsturbinen in großen Kraftwerken eine hervorragende Leistung zeigen, spielen auch Faktoren wie Wartungsaufwand, Materialkosten und Betriebskosten eine wesentliche Rolle bei der Auswahl der richtigen Turbine für eine spezifische Anwendung. Hier können Fortschritte in der Materialwissenschaft und der Fertigungstechnik dazu beitragen, die Kosten zu senken und gleichzeitig die Lebensdauer und Effizienz von Dampfturbinen zu erhöhen.
Die Zukunft von Impuls- und Reaktionsturbinen liegt also in einer Kombination aus technologischem Fortschritt, nachhaltiger Energieproduktion und effizienter Nutzung von Ressourcen. Angesichts der Herausforderungen der Energiewende und der steigenden Anforderungen an die Flexibilität und Effizienz von Kraftwerken wird die kontinuierliche Forschung und Entwicklung in diesem Bereich entscheidend dazu beitragen, die Energiewende zu gestalten und den globalen Energiebedarf nachhaltig zu decken. Beide Turbinenarten, Impuls- und Reaktionsturbinen, werden weiterhin eine Schlüsselrolle spielen, sowohl in großen, zentralisierten Kraftwerken als auch in kleineren, dezentralen Anwendungen, die zunehmend an Bedeutung gewinnen.
Die kontinuierliche Forschung und Entwicklung im Bereich der Dampfturbinen, insbesondere in Bezug auf Impuls- und Reaktionsturbinen, wird auch von den globalen Anforderungen an die Reduktion des CO₂-Ausstoßes und der Notwendigkeit zur Nutzung erneuerbarer Energien vorangetrieben. Neben der CO₂-Abscheidungstechnologie und der Nutzung von Wasserstoff als Brennstoff, spielen auch die Entwicklung und Integration neuer Materialien, die bei höheren Temperaturen und Drücken stabil bleiben, eine zentrale Rolle. Solche Materialien könnten die Leistungsfähigkeit von Dampfturbinen deutlich steigern und dazu beitragen, die thermodynamische Effizienz der Turbinen zu verbessern. Dies wäre insbesondere bei der Nutzung von Überhitzerdampf oder Superkritischem Wasser von Bedeutung, bei dem Temperaturen und Drücke weit über den bisherigen Grenzen liegen.
Im Hinblick auf die Umweltfreundlichkeit und die Integration von erneuerbaren Energiequellen werden Dampfturbinen auch immer mehr in hybridisierten Kraftwerken eingesetzt, in denen sie neben traditionellen fossilen Brennstoffen auch biogene oder synthetische Brennstoffe verwenden. Diese Hybridkraftwerke ermöglichen es, den CO₂-Ausstoß zu reduzieren, indem sie fossile Brennstoffe mit nachhaltigen Brennstoffen kombinieren. In solchen Systemen können Impuls- und Reaktionsturbinen optimal auf die unterschiedlichen Brennstoffarten und Betriebsbedingungen abgestimmt werden. Die Flexibilität dieser Turbinenarten wird zu einer Schlüsselressource für die Bereitstellung von Strom aus verschiedenen Quellen und für die Integration von Strom aus erneuerbaren Energien in das bestehende Netz.
Die Fähigkeit von Dampfturbinen, auch bei wechselnden Betriebsbedingungen stabil zu arbeiten, wird durch den Einsatz von fortschrittlichen Steuerungssystemen und Regeltechniken verbessert. Moderne Steuerungssysteme ermöglichen es, die Turbine schnell an veränderte Lasten und Dampfparameter anzupassen, was besonders bei der Integration von unregelmäßig erzeugtem Strom aus erneuerbaren Energiequellen wie Wind und Sonne von Bedeutung ist. Diese Systeme bieten nicht nur eine höhere Effizienz, sondern auch eine verbesserte Systemstabilität, indem sie die Turbinenleistung dynamisch regulieren, ohne dass es zu Leistungseinbußen kommt. Die Verwendung von variablen Leitschaufeln und adaptiven Steuermechanismen trägt dabei zur Optimierung des Betriebs bei unterschiedlichen Lastbedingungen und Betriebszyklen bei.
Darüber hinaus wird die zunehmende Digitalisierung in der Energieerzeugung dazu beitragen, die Effizienz von Dampfturbinen weiter zu steigern. Künstliche Intelligenz, Big Data und maschinelles Lernen können zur präzisen Vorhersage des Wartungsbedarfs, zur Optimierung der Betriebsparameter und zur vorausschauenden Analyse von Ausfallrisiken eingesetzt werden. Solche Technologien tragen dazu bei, die Lebensdauer von Dampfturbinen zu verlängern, indem sie potenzielle Probleme frühzeitig identifizieren und die Wartungsstrategien an die tatsächlichen Betriebsbedingungen anpassen. Predictive Maintenance-Strategien ermöglichen es, Ausfälle zu minimieren, indem sie genaue Informationen zu den Komponenten der Turbine liefern, die am meisten verschleißen oder gefährdet sind.
Die Forschung zur Effizienzsteigerung von Dampfturbinen geht auch über die klassische Dampfturbinen-Technologie hinaus und umfasst die Entwicklung von neuen, fortschrittlicheren Turbinenkonzepten, die eine noch bessere Anpassung an die variablen Anforderungen des Energiemarkts ermöglichen. So werden beispielsweise Konzepte wie die Integration von Kombinationen aus Dampfturbinen und Gasturbinen in sogenannten kombinierten Kreisprozessen immer häufiger untersucht. Diese Technologien erlauben es, die Abwärme der Gasturbine zur Dampferzeugung zu nutzen und so den Gesamtwirkungsgrad des Kraftwerks zu steigern. In solchen kombinierten Systemen könnten Impuls- und Reaktionsturbinen zusammenarbeiten, wobei die Impulsturbinen in den ersten Stufen die hohe Geschwindigkeit des Dampfes nutzen und die Reaktionsturbinen in den nachfolgenden Stufen den Dampf weiter expandieren, um die Energie optimal zu nutzen.
Die Entwicklung effizienter Turbinen wird auch von der Notwendigkeit unterstützt, den Energiebedarf weltweit zu decken, ohne dabei die Umwelt zu belasten. In vielen Regionen der Welt, in denen erneuerbare Energien noch nicht ausreichend ausgebaut sind, stellt die Dampfturbine eine der effizientesten und zuverlässigsten Technologien zur Stromerzeugung dar. Gleichzeitig wird die Forschung an Dampfturbinen durch die wachsende Bedeutung der Energiespeicherung und die Integration von Energiespeichern wie Batterien und Druckluftspeichern vorangetrieben. In Zukunft könnten Dampfturbinen in Verbindung mit Energiespeichern in der Lage sein, schnell auf Änderungen der Stromnachfrage zu reagieren und so eine stabile Stromversorgung zu gewährleisten.
Die Vielseitigkeit und Effizienz von Impuls- und Reaktionsturbinen werden auch durch ihre Fähigkeit unterstützt, in verschiedenen Branchen über die Stromerzeugung hinaus Anwendung zu finden. In der petrochemischen Industrie, in der Öl- und Gasförderung sowie in der Schifffahrt wird zunehmend auf Dampfturbinen gesetzt, um mechanische Arbeit zu erzeugen oder als Teil von Antriebssystemen. In diesen Bereichen wird die Bedeutung von Kompaktheit und Flexibilität der Turbinen immer größer, während gleichzeitig eine hohe Effizienz und geringe Emissionen erforderlich sind. Auch hier werden die Entwicklungen in der Schaufeltechnologie, Materialforschung und Steuerungstechnik von großer Bedeutung sein, um diese Anforderungen zu erfüllen.
Abschließend lässt sich sagen, dass Impuls- und Reaktionsturbinen auch in Zukunft eine entscheidende Rolle bei der Energieerzeugung und -nutzung spielen werden. Ihre Weiterentwicklung und Optimierung wird weiterhin maßgeblich zur Effizienzsteigerung von Dampfturbinenanlagen und zur Förderung einer nachhaltigeren Energieproduktion beitragen. Dabei werden technologische Innovationen, die Integration erneuerbarer Energiequellen, die Digitalisierung und die Verbesserung der Materialwissenschaften eine entscheidende Rolle spielen. In Kombination mit anderen modernen Technologien wie Energiespeicherung und CO₂-Abscheidung wird die Dampfturbine auch künftig als Schlüsseltechnologie für eine nachhaltige und effiziente Energieversorgung eine zentrale Stellung einnehmen.
Thermische Belastung

Thermische Belastung in Dampfturbinen ist ein kritischer Aspekt, der die Leistung, Effizienz und Lebensdauer der Turbine maßgeblich beeinflusst. Sie bezieht sich auf die mechanischen und thermischen Spannungen, die in den Turbinenkomponenten entstehen, wenn diese extremen Temperatur- und Druckbedingungen ausgesetzt sind. Dampfturbinen arbeiten mit hochtemperiertem Dampf, der bei typischen Betriebsbedingungen Temperaturen von 500°C bis über 600°C erreichen kann. Diese hohen Temperaturen stellen besondere Anforderungen an die Materialien, aus denen die Turbine gebaut ist, und erfordern eine präzise Steuerung der Betriebsparameter, um Schäden durch übermäßige thermische Belastung zu vermeiden.
Während des Betriebs treten an den Turbinenkomponenten, insbesondere an den Schaufeln und Gehäusen, thermische Gradienten auf, die zu thermischen Spannungen führen können. Dies geschieht aufgrund der unterschiedlichen Ausdehnungskoeffizienten der Materialien bei Erwärmung und Abkühlung. Wenn die Turbine einem schnellen Temperaturwechsel ausgesetzt wird, können diese Spannungen zu Rissen, Materialermüdung oder sogar zu einem Versagen der Bauteile führen. Um thermische Belastungen zu minimieren, müssen Turbinenkonstrukteure fortschrittliche Werkstoffe verwenden, die hohe Temperaturen und wechselnde Wärmezyklen gut überstehen. Diese Materialien müssen sowohl hitzebeständig als auch fest genug sein, um den mechanischen Belastungen durch die hohe Drehzahl und den Dampfdruck standzuhalten.
Zudem müssen die Konstruktion und der Betrieb der Dampfturbine so optimiert werden, dass die Turbine gleichmäßig erwärmt wird, um unerwünschte Spannungen zu minimieren. Eine wichtige Rolle spielen auch die Kühlungssysteme, die dafür sorgen, dass kritische Turbinenkomponenten, insbesondere die Schaufeln, nicht überhitzen und die Temperatur innerhalb sicherer Grenzen bleibt. Die thermische Belastung beeinflusst auch die Lebensdauer der Turbine. Langfristig können wiederholte thermische Zyklen, die durch das Ein- und Ausschalten oder durch Lastwechsel verursacht werden, zu Materialermüdung und einem vorzeitigen Verschleiß führen. Um die Lebensdauer der Turbine zu verlängern und Ausfälle zu vermeiden, werden fortschrittliche Materialwissenschaften angewendet, um hitzebeständige Legierungen zu entwickeln, die beständig gegenüber den extremen Temperaturen sind.
Ebenso wichtig sind moderne Überwachungstechniken, wie Temperatursensoren und thermische Bildgebung, die es ermöglichen, die Temperaturentwicklung in Echtzeit zu überwachen und potenzielle Probleme frühzeitig zu erkennen. Auf diese Weise können präventive Wartungsmaßnahmen ergriffen werden, bevor es zu schwerwiegenden Schäden kommt. Zusammenfassend lässt sich sagen, dass die thermische Belastung in Dampfturbinen eine entscheidende Herausforderung für deren Konstruktion und Betrieb darstellt. Sie erfordert den Einsatz innovativer Materialien, fortschrittlicher Konstruktionsmethoden und präziser Steuerungstechniken, um die Turbine effizient und zuverlässig zu betreiben, ohne dass thermische Belastungen zu einer Verringerung der Lebensdauer oder Leistung führen.
Die thermische Belastung in Dampfturbinen beeinflusst nicht nur die Materialwahl und Konstruktion, sondern auch die Betriebsstrategien und Wartungspläne. Turbinen müssen in der Lage sein, sich schnell und sicher an wechselnde Lasten und Betriebsbedingungen anzupassen, um thermische Schocks zu vermeiden. Dies ist besonders relevant, wenn die Turbine zwischen verschiedenen Betriebszuständen umschaltet, beispielsweise beim Anfahren oder Abfahren des Systems. Diese Übergangsphasen können enorme thermische Spannungen erzeugen, da die Turbinenkomponenten schnell erwärmt oder abgekühlt werden. Hierbei kann es zu ungleichmäßigen Temperaturen innerhalb der Turbine kommen, was die Gefahr von Rissen und Verformungen erhöht. Deshalb sind spezielle Verfahren zur Kontrolle des Temperaturanstiegs, wie das langsame Erhöhen der Dampftemperatur und das Vermeiden von abrupten Temperaturänderungen, notwendig, um thermische Schäden zu minimieren.
Zudem hat die Thermodynamik der Dampfturbine direkten Einfluss auf die Wärmeübertragung und damit auf die thermische Belastung. Bei hohen Dampftemperaturen steigt der Druck, was die mechanischen Anforderungen an die Turbinenkomponenten weiter verstärkt. Der Dampf muss sich effizient durch die Turbine bewegen, ohne dass es zu übermäßigen Temperaturverlusten oder zu einem unregelmäßigen Temperaturprofil kommt. Dies erfordert eine präzise Konstruktion der Leitschaufeln und Laufschaufeln, um eine gleichmäßige Wärmeverteilung und Strömung zu gewährleisten, was wiederum dazu beiträgt, die thermische Belastung auf die einzelnen Teile der Turbine zu minimieren. Eine unregelmäßige Wärmeverteilung kann zu Hotspots führen, die das Risiko einer Materialversprödung oder sogar eines Versagens von Komponenten erhöhen.
Auch die Langzeitstabilität der Dampfturbinen wird durch thermische Belastungen beeinflusst. Wiederholte Zyklen von Erwärmung und Abkühlung, die über Jahre hinweg auftreten, führen zu einer kontinuierlichen Belastung des Materials, was schließlich zu einer Verringerung der Festigkeit führen kann. Dieser Prozess wird als thermische Ermüdung bezeichnet, und er tritt besonders häufig an Stellen auf, an denen Turbinenkomponenten großen Temperatur- und Druckschwankungen ausgesetzt sind, wie zum Beispiel an den Schaufeln und den Turbinengelenken. Um diesem Effekt entgegenzuwirken, wird in der Forschung intensiv daran gearbeitet, Materialien mit höherer Hitzebeständigkeit und besserer Ermüdungsresistenz zu entwickeln. Neue Legierungen und Verbundmaterialien, die mit hochmodernen Fertigungstechniken wie 3D-Druck hergestellt werden, könnten in Zukunft helfen, die Auswirkungen thermischer Belastung zu verringern, indem sie die Widerstandsfähigkeit der Turbinenkomponenten gegen Temperaturwechsel und mechanische Spannungen erhöhen.
In vielen modernen Dampfturbinen wird zusätzlich eine integrierte Kühlungstechnik eingesetzt, die dazu dient, die Temperatur der kritischen Komponenten konstant zu halten und so die thermische Belastung zu kontrollieren. Beispielsweise können Kühlsysteme, die mit fortschrittlichen Flüssigkeiten oder Gasen arbeiten, in die Turbinenstruktur integriert werden, um gezielt Wärme von den besonders belasteten Bereichen abzuleiten. Diese Systeme tragen dazu bei, die Bildung von Hotspots zu verhindern und die Temperatur in einem sicheren Bereich zu halten. Allerdings erfordert diese Technologie präzise Steuerung und regelmäßige Wartung, um ihre Effektivität aufrechtzuerhalten.
Ein weiterer wichtiger Aspekt ist die Kühlung des Gehäuses und der Dichtungen der Turbine. Diese Bauteile sind besonders anfällig für thermische Belastungen, da sie direkten Kontakt mit dem Dampf haben und gleichzeitig mechanische Kräfte aufnehmen müssen. Eine übermäßige Erwärmung dieser Komponenten kann zu einer Verringerung der Dichtleistung und zu einer Erhöhung der Leckage führen, was wiederum die Effizienz der Turbine beeinträchtigt und zu einer verstärkten Belastung der restlichen Turbinenkomponenten führen kann.
Die thermische Belastung kann außerdem zu einem sogenannten “Thermischen Schock” führen, bei dem sich die Turbinenmaterialien aufgrund von ungleichmäßiger Erwärmung plötzlich stark verformen oder reißen. Um diese Gefahr zu verringern, werden in der Konstruktion der Turbine sogenannte “Thermal-Stress-Tests” durchgeführt. Diese Tests simulieren extreme Temperaturbedingungen, um die Auswirkungen auf das Material und die Struktur der Turbine zu überprüfen und sicherzustellen, dass sie den erwarteten Belastungen standhält. Solche Tests sind entscheidend für die Entwicklung langlebiger Turbinen, da sie nicht nur die sofortigen Auswirkungen thermischer Belastung berücksichtigen, sondern auch den langfristigen Einfluss auf die Festigkeit und Stabilität der Komponenten.
Insgesamt ist die thermische Belastung ein unvermeidlicher Bestandteil des Betriebs von Dampfturbinen, der jedoch durch eine Vielzahl von ingenieurtechnischen Maßnahmen kontrolliert und minimiert werden kann. Die kontinuierliche Forschung im Bereich der Materialwissenschaften, Kühlungstechniken und Turbinenkonstruktion hat das Ziel, die Turbinen so zu gestalten, dass sie den extremen thermischen Bedingungen standhalten und gleichzeitig die Effizienz und Lebensdauer maximieren. Gleichzeitig ist es von entscheidender Bedeutung, dass Betreiber und Ingenieure moderne Überwachungs- und Wartungsstrategien einsetzen, um thermische Belastungen frühzeitig zu erkennen und Schäden vorzubeugen. Nur so kann die langfristige Leistungsfähigkeit von Dampfturbinen gewährleistet werden.
Um die thermische Belastung weiter zu reduzieren und die Effizienz von Dampfturbinen zu maximieren, wird verstärkt an fortschrittlichen Thermomanagement-Technologien gearbeitet. Eine vielversprechende Entwicklung in diesem Bereich ist die Nutzung von Nanomaterialien und anderen innovativen Stoffen für die Schaufeln und Gehäuse der Turbine. Nanomaterialien bieten außergewöhnliche Wärmeleitfähigkeit und eine höhere Beständigkeit gegen thermische Deformation, was es ermöglicht, die Temperaturen innerhalb der Turbine besser zu kontrollieren. Solche Materialien könnten helfen, die Temperaturunterschiede zwischen den verschiedenen Turbinenkomponenten auszugleichen und so die thermische Belastung gleichmäßiger zu verteilen.
Ein weiterer wichtiger Schritt ist die Verbesserung der Wärmeabfuhr durch optimierte Turbinengeometrien und -designs. Neue Strömungssimulationen und -modelle ermöglichen es, die Wärmeverteilung in der Turbine präziser zu analysieren und so das Design so anzupassen, dass die Wärme effizienter abgeführt wird. Dies ist besonders wichtig in Bereichen, in denen hohe Temperaturspitzen auftreten, wie etwa in den Schaufeln und an den Turbinenrändern. Durch die Implementierung von Technologien wie aktiven Kühlsystemen, die mit Flüssigkeiten oder Gasen durchzogen sind, können Hotspots vermieden werden, die zu strukturellen Schäden führen könnten.
Neben den strukturellen und materialtechnischen Verbesserungen spielt die präzise Steuerung der Betriebskonditionen eine entscheidende Rolle bei der Minderung thermischer Belastungen. Hierbei wird eine kontinuierliche Überwachung und Anpassung der Betriebsparameter an die tatsächlichen Lastbedingungen immer wichtiger. Durch den Einsatz moderner Sensortechnologie und Echtzeit-Überwachungssysteme lassen sich Temperatur- und Druckspitzen frühzeitig erkennen und gegebenenfalls Gegenmaßnahmen ergreifen, um Schäden an der Turbine zu vermeiden. Dies ermöglicht es, die Turbine nicht nur effizienter zu betreiben, sondern auch unvorhergesehene thermische Belastungen zu verhindern.
Darüber hinaus gewinnt die Forschung an neuen Kühltechnologien zunehmend an Bedeutung. Eine vielversprechende Entwicklung ist die Integration von Mikrokanälen in die Turbinenstruktur, durch die ein Kühlfluid zirkulieren kann, um gezielt Wärme von kritischen Bereichen der Turbine abzuleiten. Diese Mikrokanäle können durch die Turbinenbauteile wie Schaufeln und Gehäuse geführt werden und sorgen so für eine direkte Kühlung der am stärksten belasteten Teile. Der Vorteil dieser Technologie liegt in ihrer hohen Effizienz und der gezielten Wärmeabfuhr an den Stellen, an denen sie am dringendsten benötigt wird.
Ein weiterer Aspekt in der Minderung thermischer Belastungen ist der zunehmende Einsatz von Hochleistungsisolierungen in Turbinen. Durch den Einsatz fortschrittlicher Dämmmaterialien kann verhindert werden, dass Wärme von außen in die Turbine eindringt, wodurch die Temperaturdifferenzen zwischen den Komponenten verringert werden. Diese Isolierung reduziert nicht nur die thermische Belastung der Turbine, sondern hilft auch, die Effizienz des gesamten Systems zu steigern, da weniger Energie durch Wärmeverluste verloren geht.
Die thermische Belastung in Dampfturbinen hat also direkte Auswirkungen auf die Leistungsfähigkeit, Lebensdauer und Sicherheit der Turbinen. Es ist daher unerlässlich, dass kontinuierlich neue Technologien entwickelt werden, die es ermöglichen, diese Belastung zu minimieren. Fortschritte in den Bereichen Materialwissenschaft, Thermomanagement, Kühlungstechnik und intelligenter Steuerung tragen dazu bei, die Effizienz von Dampfturbinen weiter zu erhöhen und ihre Betriebszeit zu maximieren. Dabei spielen auch regelmäßige Wartungs- und Inspektionsstrategien eine Schlüsselrolle, um potenzielle Probleme frühzeitig zu erkennen und Ausfälle zu vermeiden. Nur durch eine Kombination dieser innovativen Technologien und sorgfältiger Betriebsführung können Dampfturbinen auch unter extremen Bedingungen zuverlässig und effizient arbeiten.
Die fortlaufende Forschung im Bereich der thermischen Belastung von Dampfturbinen konzentriert sich zunehmend auf die Entwicklung von intelligenten Steuerungssystemen, die in der Lage sind, die Reaktion der Turbine auf sich ändernde Betriebsbedingungen in Echtzeit zu optimieren. Diese Systeme verwenden fortschrittliche Algorithmen und Künstliche Intelligenz (KI), um die thermischen Bedingungen kontinuierlich zu überwachen und automatisch Anpassungen vorzunehmen, um die Belastung gleichmäßig zu verteilen. Durch maschinelles Lernen können diese Systeme aus historischen Betriebsdaten lernen und vorhersehen, welche Komponenten einer Turbine am stärksten belastet werden, sodass rechtzeitig präventive Maßnahmen ergriffen werden können.
Ein innovativer Ansatz zur Verringerung der thermischen Belastung sind sogenannte “adaptive Materialien”, die ihre Eigenschaften in Abhängigkeit von Temperatur und Druck verändern. Solche Materialien könnten dazu beitragen, die thermische Expansion von Turbinenkomponenten zu kontrollieren und so die Bildung von Spannungen zu minimieren. Besonders im Bereich der Schaufeln wird an Materialien gearbeitet, die sich bei extremen Temperaturen flexibler verhalten, um Risse und Brüchen entgegenzuwirken. Diese sogenannten “Formgedächtnislegierungen” oder “smart materials” können durch eine gezielte Reaktion auf die Betriebstemperaturen und -drücke die strukturelle Integrität der Turbine während des gesamten Lebenszyklus verbessern.
Ein weiteres wichtiges Forschungsfeld ist die Verbesserung der Wärmeübertragungsmechanismen innerhalb der Dampfturbine. Spezielle Wärmeleitbeschichtungen, die auf Turbinenkomponenten aufgebracht werden, könnten helfen, die Wärme effizienter zu verteilen und lokalisierten Überhitzungen entgegenzuwirken. Diese Beschichtungen sind oft mit speziellen Nanopartikeln angereichert, die die Wärmeübertragung um ein Vielfaches erhöhen können. Diese Technologien könnten auch dazu beitragen, die Lebensdauer der Turbine zu verlängern, indem sie die Bildung von Hotspots verhindern und eine gleichmäßige Temperaturverteilung gewährleisten.
Zusätzlich wird in der Entwicklung von Dampfturbinen zunehmend Wert auf eine genauere Modellierung der thermischen Belastung im Zuge des gesamten Lebenszyklus der Turbine gelegt. Durch die Verwendung von hochentwickelten Finite-Elemente-Methoden (FEM) können Ingenieure simulieren, wie sich Temperaturveränderungen über die Lebensdauer der Turbine auswirken und welche Bauteile am meisten gefährdet sind. Dies ermöglicht eine genauere Vorhersage von Verschleißmustern und hilft, die Wartungsintervalle besser zu planen, um thermischen Schäden vorzubeugen. Mit diesen Simulationen können auch optimierte Designs entwickelt werden, die speziell auf die Minimierung thermischer Spannungen und die Maximierung der Effizienz abgestimmt sind.
Die thermische Belastung beeinflusst zudem nicht nur die Bauteile der Turbine selbst, sondern auch die gesamte Energieerzeugungsanlage. In modernen Anlagen mit mehreren Turbinen oder in Kombination mit Gasturbinen muss die Wärmeabfuhr zwischen den einzelnen Maschinen optimiert werden, um ein effizientes Gesamtsystem zu gewährleisten. In sogenannten Kombikraftwerken, bei denen Dampfturbinen mit anderen Energiequellen wie Gasturbinen oder Brennstoffzellen kombiniert werden, ist es entscheidend, dass die thermische Belastung in allen Komponenten gleichmäßig verteilt wird, um einen effizienten Betrieb zu ermöglichen. Hierzu sind ausgeklügelte Steuerungssysteme erforderlich, die die Wärme zwischen den verschiedenen Komponenten optimal managen und somit eine Überhitzung einzelner Teile verhindern.
Neben den mechanischen und thermodynamischen Verbesserungen wird auch der Übergang von klassischen fossilen Brennstoffen zu regenerativen Energiequellen einen Einfluss auf die thermische Belastung der Dampfturbinen haben. In hybriden Kraftwerken, die erneuerbare Energiequellen wie Solar- oder Windenergie mit Dampfturbinen kombinieren, variiert die Temperatur des Dampfs je nach verfügbaren Energiequellen. Hier müssen die Turbinen so gestaltet sein, dass sie auch mit schwankenden Temperaturen umgehen können, ohne die thermische Belastung zu erhöhen. Diese Flexibilität erfordert neue Designstrategien und Materialien, die in der Lage sind, sich schnell an verändernde Betriebsbedingungen anzupassen.
Eine weitere interessante Entwicklung ist die Verwendung von Hochtemperatur-Dampfturbinen, die mit überkritischem oder sogar transkritischem CO₂ betrieben werden. In solchen Systemen entstehen Temperaturen und Drücke, die deutlich über denen herkömmlicher Dampfturbinen liegen, was neue Herausforderungen hinsichtlich der thermischen Belastung mit sich bringt. Diese sogenannten “superkritischen” Dampfturbinen erfordern die Entwicklung von speziellen Materialien, die den extremen thermischen Belastungen standhalten können, und von Kühlsystemen, die die Hitze effizient abführen, ohne die Bauteile zu überlasten.
Zusammenfassend lässt sich sagen, dass die thermische Belastung von Dampfturbinen ein äußerst komplexes Problem darstellt, das mehrere technische Disziplinen umfasst, von der Materialwissenschaft über die Thermodynamik bis hin zur Steuerungstechnik. Die kontinuierliche Forschung und Entwicklung auf diesem Gebiet wird entscheidend dazu beitragen, die Effizienz von Dampfturbinen weiter zu steigern und gleichzeitig die Lebensdauer und Betriebssicherheit der Anlagen zu erhöhen. Technologien wie intelligente Steuerungssysteme, adaptive Materialien, innovative Kühlungstechniken und fortschrittliche Wärmeübertragungsmechanismen werden in den kommenden Jahren voraussichtlich eine Schlüsselrolle dabei spielen, die thermische Belastung zu reduzieren und Dampfturbinen noch leistungsfähiger und zuverlässiger zu machen.
EMS Kraftmaschinen – Ihr Partner für Hochleistungs-Dampfturbinen
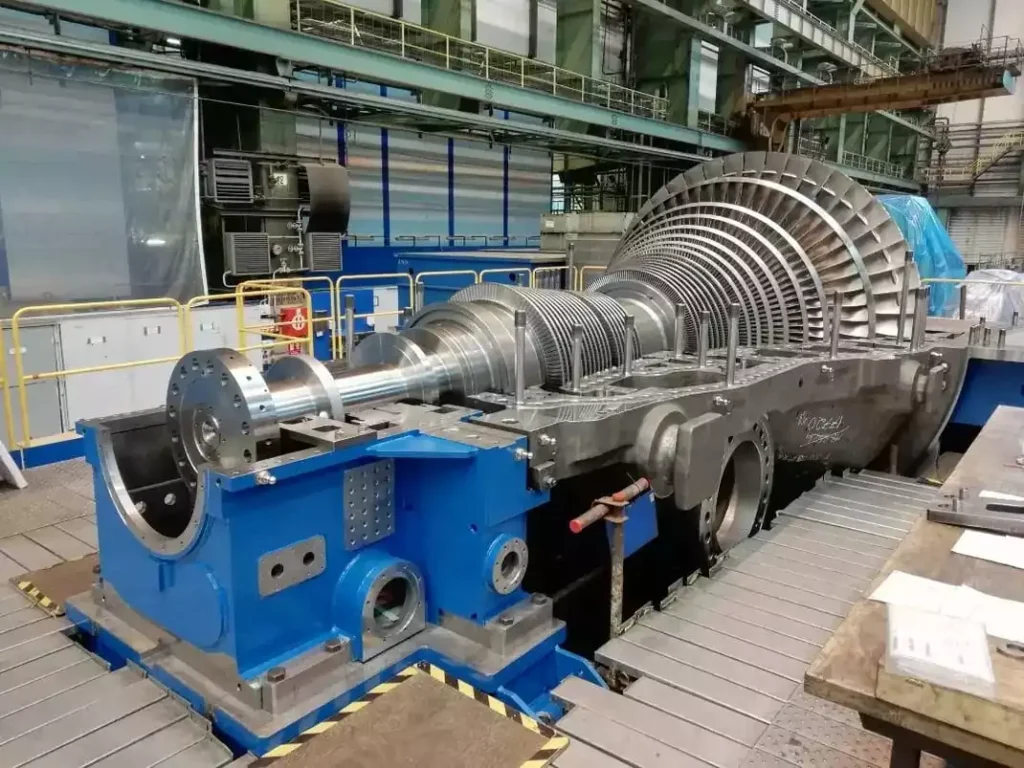
EMS Kraftmaschinen ist ein führendes Unternehmen in der Entwicklung und Herstellung hochwertiger und effizienter Dampfturbinen. Mit jahrzehntelanger Erfahrung und technischem Know-how hat sich EMS Kraftmaschinen als zuverlässiger Partner für Kunden in unterschiedlichsten Industriebereichen etabliert.
Hochwertige Dampfturbinen für jede Anwendung
Die Dampfturbinen von EMS Kraftmaschinen sind ein Synonym für Präzision und Effizienz. Sie werden aus erstklassigen Materialien gefertigt und nach den höchsten industriellen Standards entwickelt, um eine lange Lebensdauer und maximale Leistung zu garantieren. Dank der flexiblen Konstruktionsweise können die Maschinen individuell an die spezifischen Anforderungen jedes Projekts angepasst werden.
Ob in der Energieerzeugung, in der chemischen Industrie, im Schiffsbau oder in der Papier- und Zellstoffindustrie – die Dampfturbinen von EMS Kraftmaschinen bieten zuverlässige Lösungen für jeden Einsatzbereich.
Warum EMS Kraftmaschinen?
- Innovative Technologien: EMS investiert kontinuierlich in Forschung und Entwicklung, um die Effizienz und Umweltfreundlichkeit seiner Produkte zu steigern.
- Maßgeschneiderte Lösungen: Jedes Projekt wird individuell geplant, um den Anforderungen der Kunden gerecht zu werden.
- Zuverlässigkeit: Mit einem erstklassigen Service und langlebigen Produkten hat EMS das Vertrauen von Unternehmen weltweit gewonnen.
- Nachhaltigkeit: Moderne Dampfturbinen von EMS tragen zur Reduzierung von Energieverlusten bei und fördern eine umweltfreundliche Nutzung von Ressourcen.
Effizienz und Nachhaltigkeit im Fokus
In einer Zeit, in der Energieeffizienz und Nachhaltigkeit an oberster Stelle stehen, bietet EMS Kraftmaschinen die perfekte Lösung. Die Dampfturbinen zeichnen sich durch einen hohen Wirkungsgrad aus, der nicht nur Betriebskosten senkt, sondern auch die Umweltbelastung minimiert.
Ihr zuverlässiger Partner
Mit EMS Kraftmaschinen setzen Sie auf innovative Technologien, höchste Qualität und einen starken Fokus auf Kundenzufriedenheit. Kontaktieren Sie uns, um mehr über unsere Dampfturbinen und deren Anwendungsmöglichkeiten zu erfahren – wir entwickeln die Lösung, die perfekt zu Ihren Bedürfnissen passt.
EMS Kraftmaschinen – Effizienz trifft auf Präzision.