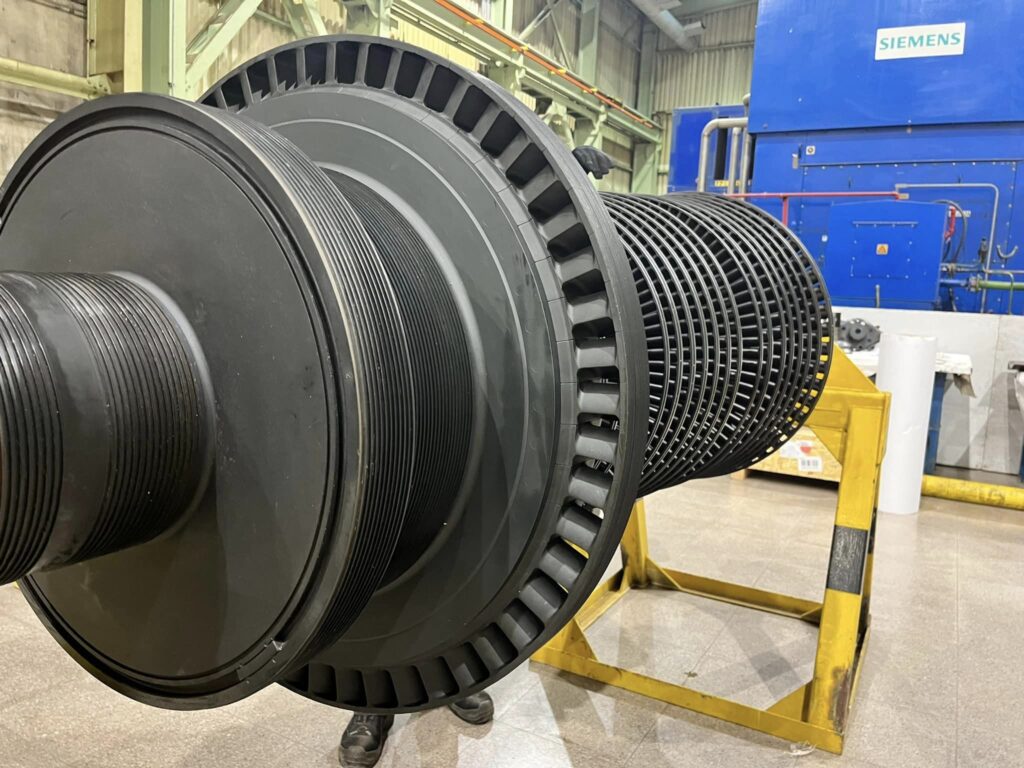
Rotor der Dampfturbine: Die Welt ist ein Ort, der ständig in Bewegung ist und sich verändert. Jeden Tag passieren unzählige Dinge, die unsere Umwelt beeinflussen und unser Leben bereichern. Ob es sich um technologische Innovationen, politische Ereignisse oder kulturelle Veränderungen handelt – die Art und Weise, wie wir die Welt wahrnehmen, wird ständig neu gestaltet.
In den letzten Jahrzehnten hat sich die Technologie auf vielen Gebieten rasant entwickelt. Insbesondere die digitale Transformation hat die Art und Weise, wie wir kommunizieren, arbeiten und uns unterhalten, revolutioniert. Dank des Internets und der zunehmenden Vernetzung ist es möglich, Informationen in Echtzeit auszutauschen und auf eine riesige Wissensquelle zuzugreifen. Das hat nicht nur Auswirkungen auf den privaten Bereich, sondern auch auf die Wirtschaft und die Art und Weise, wie Unternehmen arbeiten.
Doch nicht nur die Technologie hat sich verändert. Auch die gesellschaftlichen Werte und Normen haben sich im Laufe der Jahre gewandelt. Themen wie Nachhaltigkeit, Umweltschutz und soziale Gerechtigkeit sind heutzutage von großer Bedeutung. Immer mehr Menschen setzen sich dafür ein, den Planeten für zukünftige Generationen zu bewahren und ein besseres, gerechteres Miteinander zu schaffen. Diese Entwicklungen zeigen, wie wichtig es ist, dass wir unsere Verantwortung als Teil der globalen Gemeinschaft wahrnehmen.
In einer zunehmend globalisierten Welt ist es zudem von entscheidender Bedeutung, dass wir interkulturelle Kompetenzen entwickeln und respektvoll miteinander umgehen. Der Austausch zwischen verschiedenen Kulturen und Nationen fördert das Verständnis und die Zusammenarbeit und kann dabei helfen, globale Herausforderungen zu bewältigen. Gerade in Zeiten von Krisen, sei es durch Naturkatastrophen oder politische Konflikte, zeigt sich, wie wichtig es ist, solidarisch zu handeln und die Vielfalt zu schätzen.
Abschließend lässt sich sagen, dass wir in einer spannenden Zeit leben, die viele Herausforderungen, aber auch zahlreiche Chancen mit sich bringt. Es liegt an uns, diese Chancen zu nutzen und aktiv an der Gestaltung einer besseren Zukunft zu arbeiten. Indem wir unsere Ressourcen schonen, uns für soziale Gerechtigkeit einsetzen und die Vielfalt in der Welt anerkennen, können wir einen wichtigen Beitrag zu einer positiven Veränderung leisten.
Die Zukunft wird stark von den Entscheidungen geprägt, die wir heute treffen. Unsere Verantwortung erstreckt sich über viele Bereiche, sei es die Entwicklung neuer Technologien, die Förderung von Bildung oder der Schutz unserer natürlichen Ressourcen. Besonders in einer Zeit des Klimawandels, der globalen Erwärmung und der Ausbeutung natürlicher Rohstoffe müssen wir uns bewusst machen, dass unsere Handlungen langfristige Auswirkungen auf den Planeten haben können.
Ein zentraler Aspekt der modernen Welt ist der Zugang zu Bildung. Bildung ist der Schlüssel, um Menschen zu befähigen, eigenständig zu denken, kritisch zu hinterfragen und Lösungen für die Herausforderungen der Zukunft zu entwickeln. Sie fördert Innovationen und Kreativität, die notwendig sind, um den sich ständig wandelnden Anforderungen gerecht zu werden. Der Fokus sollte darauf liegen, Bildung für alle zugänglich zu machen und sicherzustellen, dass niemand aufgrund von Herkunft, Geschlecht oder sozialem Status benachteiligt wird.
In Bezug auf die Technologie wird erwartet, dass sie weiterhin ein treibender Faktor für den gesellschaftlichen und wirtschaftlichen Wandel bleibt. Künstliche Intelligenz, Robotik und das Internet der Dinge sind nur einige Beispiele für Technologien, die die Art und Weise, wie wir leben und arbeiten, grundlegend verändern. Doch auch hier ist es wichtig, ethische Fragestellungen zu berücksichtigen. Wie stellen wir sicher, dass diese Technologien im Dienste des Gemeinwohls eingesetzt werden und nicht zu einer weiteren Spaltung der Gesellschaft führen? Es ist eine Herausforderung, den technologischen Fortschritt mit den Bedürfnissen und Werten der Menschen in Einklang zu bringen.
In dieser komplexen und schnelllebigen Welt wird es zunehmend wichtiger, Resilienz zu entwickeln – sowohl auf individueller als auch auf gesellschaftlicher Ebene. Resilienz bedeutet, in der Lage zu sein, mit Krisen umzugehen, sich schnell an neue Umstände anzupassen und trotz Widrigkeiten weiter voranzukommen. In einer global vernetzten Welt können Herausforderungen oft über Ländergrenzen hinweg wirken, weshalb internationale Zusammenarbeit und gegenseitige Unterstützung unerlässlich sind.
Schließlich spielt auch die Förderung von Kreativität und Kultur eine bedeutende Rolle in der Weiterentwicklung der Gesellschaft. Kunst, Literatur, Musik und andere kulturelle Ausdrucksformen tragen nicht nur zur individuellen Entfaltung bei, sondern fördern auch das kollektive Verständnis und die Solidarität. Sie bieten einen Raum für Reflexion und Inspiration und erinnern uns daran, dass wir alle Teil einer größeren Geschichte sind.
Insgesamt zeigt sich, dass die kommenden Jahre eine Zeit der Anpassung, des Wachstums und der Transformation sein werden. Die Art und Weise, wie wir als Gesellschaft auf die Herausforderungen reagieren, wird maßgeblich darüber entscheiden, welche Richtung wir einschlagen und wie die Welt der Zukunft aussehen wird. Es liegt an uns allen, mit Mut, Weitsicht und Verantwortung zu handeln und die Weichen für eine bessere Zukunft zu stellen.
Um eine nachhaltige Zukunft zu gestalten, müssen wir unsere Herangehensweise an Wirtschaft und Konsum fundamental überdenken. Die traditionelle Wirtschaftsweise, die auf ungebremstem Wachstum und Ressourcenverbrauch basiert, ist nicht mehr tragbar. Ein Umdenken hin zu einer Kreislaufwirtschaft, in der Ressourcen effizient genutzt, wiederverwertet und Abfall minimiert wird, könnte der Schlüssel sein. Diese Veränderung erfordert nicht nur technologische Innovationen, sondern auch ein Bewusstsein in der Gesellschaft, das den Wert von Nachhaltigkeit und verantwortungsvollem Konsum verankert.
Ein weiterer wichtiger Aspekt für die Zukunft ist die Integration von Diversität und Inklusion in allen Bereichen des Lebens. Gesellschaften, die Vielfalt als Stärke erkennen, sind besser in der Lage, innovative Lösungen zu entwickeln und Herausforderungen aus unterschiedlichen Perspektiven zu betrachten. Es ist entscheidend, dass alle Stimmen Gehör finden, besonders diejenigen, die in der Vergangenheit marginalisiert wurden. Eine inklusive Gesellschaft ist eine gerechtere Gesellschaft, in der jeder Mensch die Möglichkeit hat, sein Potenzial voll auszuschöpfen.
Technologische Fortschritte bieten dabei Chancen, aber auch Risiken. Künstliche Intelligenz, Automatisierung und andere disruptive Technologien könnten viele Arbeitsplätze verändern oder sogar überflüssig machen. Es ist wichtig, dass wir uns frühzeitig mit den Auswirkungen auf die Arbeitswelt auseinandersetzen und Lösungen finden, um Menschen zu unterstützen, die von diesen Veränderungen betroffen sind. Weiterbildung, Umschulung und lebenslanges Lernen werden entscheidend sein, um sicherzustellen, dass niemand zurückgelassen wird.
Im Bereich der Gesundheit wird die Digitalisierung ebenfalls eine zentrale Rolle spielen. Die Möglichkeit, medizinische Daten zu analysieren und individuelle Behandlungen maßzuschneidern, hat das Potenzial, die Gesundheitsversorgung zu revolutionieren. Gleichzeitig stellt sich die Frage, wie der Datenschutz und die ethischen Implikationen solcher Technologien gewahrt werden können. Es gilt, eine Balance zu finden zwischen der Nutzung neuer Technologien zur Verbesserung des Lebens und dem Schutz der Privatsphäre und der individuellen Rechte.
In einer Welt, die zunehmend durch Unsicherheiten geprägt ist – sei es durch politische Spannungen, wirtschaftliche Instabilität oder Umweltkrisen – ist es auch wichtig, dass wir die Resilienz unserer Gesellschaften stärken. Das bedeutet nicht nur, auf Krisen vorbereitet zu sein, sondern auch, Vertrauen und Zusammenarbeit zu fördern. Nur durch gemeinsame Anstrengungen können wir Lösungen finden, die über kurzfristige Interessen hinausgehen und das langfristige Wohl aller im Blick behalten.
Die Welt wird sich weiterhin verändern, aber die Verantwortung, wie diese Veränderungen gestaltet werden, liegt bei uns allen. Es ist die kollektive Anstrengung, die unsere Zukunft prägen wird. Jeder Beitrag zählt, sei es durch kleine, alltägliche Entscheidungen oder durch große gesellschaftliche Initiativen. Was wir heute tun, wird die Welt von morgen beeinflussen – es liegt an uns, diese Welt aktiv und verantwortungsvoll mitzugestalten.
Ein weiterer bedeutender Aspekt, der die Zukunft prägen wird, ist die Frage der globalen Gerechtigkeit. In einer Welt, in der Ungleichheiten weiterhin bestehen, sei es in Bezug auf Wohlstand, Bildung oder Zugang zu Ressourcen, müssen wir als globale Gemeinschaft nach Lösungen suchen, die Fairness und Chancengleichheit fördern. Es ist wichtig, die sozialen und wirtschaftlichen Kluften zu überbrücken, die Menschen in vielen Teilen der Welt nach wie vor von der Teilnahme an einer prosperierenden Gesellschaft ausschließen. Internationale Zusammenarbeit und Entwicklungsprogramme sind notwendig, um Benachteiligungen zu bekämpfen und die Lebensbedingungen für alle zu verbessern.
Auch die politische Landschaft wird weiterhin eine entscheidende Rolle spielen. Angesichts wachsender Spannungen zwischen Nationen und zunehmender geopolitischer Unsicherheit ist es unerlässlich, dass Länder Wege finden, konstruktiv zusammenzuarbeiten. Die Stärkung internationaler Institutionen und die Förderung von Dialog und Diplomatie sind notwendig, um Konflikte zu vermeiden und stabile, friedliche Verhältnisse zu schaffen. In einer Zeit, in der der Klimawandel und globale Gesundheitskrisen keine nationalen Grenzen kennen, muss der internationale Zusammenhalt gestärkt werden, um globalen Herausforderungen effektiv zu begegnen.
Im Hinblick auf den Klimawandel ist es von entscheidender Bedeutung, dass wir unsere Anstrengungen zur Verringerung der CO2-Emissionen intensivieren und die Auswirkungen des bereits eingetretenen Wandels abmildern. Dies erfordert eine enge Zusammenarbeit zwischen Regierungen, Unternehmen und der Zivilgesellschaft, um nachhaltige Lösungen zu finden, die sowohl ökologisch als auch wirtschaftlich tragfähig sind. Der Übergang zu erneuerbaren Energien, die Förderung von grünen Technologien und der Schutz von natürlichen Ökosystemen sind wesentliche Schritte in diese Richtung.
Ein bedeutendes Ziel ist auch, die Ernährungssicherheit weltweit zu gewährleisten. Angesichts wachsender Bevölkerungen und zunehmender Umweltveränderungen müssen innovative Lösungen entwickelt werden, um die Nahrungsmittelproduktion zu steigern, gleichzeitig jedoch die natürlichen Ressourcen zu schonen und die biologische Vielfalt zu bewahren. Der Fokus auf nachhaltige Landwirtschaft und die Förderung von lokaleren, faireren Lieferketten könnte dazu beitragen, die Herausforderungen in der Nahrungsmittelversorgung zu meistern und globale Hungerprobleme zu lindern.
Darüber hinaus wird es in den kommenden Jahren notwendig sein, die digitale Kluft zu überwinden. Während in vielen entwickelten Ländern der Zugang zum Internet und digitalen Technologien weit verbreitet ist, haben zahlreiche Menschen in weniger entwickelten Regionen der Welt noch immer keinen Zugang zu grundlegenden digitalen Ressourcen. Der Ausbau der digitalen Infrastruktur, die Förderung von digitalen Kompetenzen und der Zugang zu modernen Kommunikationsmitteln sind entscheidend, um Chancengleichheit und eine inklusive Entwicklung zu fördern.
Nicht zuletzt müssen wir uns auch der Frage stellen, wie wir als Individuen und als Gesellschaft mit dem Thema Glück und Wohlstand umgehen. In vielen westlichen Ländern ist der Fokus auf materiellen Wohlstand und Konsum immer noch weit verbreitet, doch immer mehr Menschen erkennen, dass wahres Wohlstand auch in immateriellen Aspekten wie Beziehungen, persönlicher Erfüllung und der Verbindung mit der Umwelt liegt. Es wird zunehmend anerkannt, dass es notwendig ist, neue Indikatoren für Wohlstand zu entwickeln, die nicht nur auf wirtschaftlichem Wachstum basieren, sondern auch auf sozialer Gerechtigkeit, Nachhaltigkeit und der Förderung des menschlichen Wohlbefindens.
Insgesamt geht es darum, eine Gesellschaft zu schaffen, die nicht nur auf kurzfristigen Gewinn, sondern auf langfristige, nachhaltige Werte setzt. Die Herausforderungen, vor denen wir stehen, sind groß, aber sie bieten auch enorme Chancen, eine gerechtere, inklusivere und nachhaltigere Welt zu gestalten. Der Weg dorthin mag schwierig sein, aber er erfordert Mut, Zusammenarbeit und eine gemeinsame Vision für eine bessere Zukunft – eine Zukunft, in der jeder Mensch die Möglichkeit hat, zu gedeihen und in Harmonie mit der Welt um ihn herum zu leben.
Diese Zukunft, die wir uns erträumen, kann nur erreicht werden, wenn wir in allen Bereichen unseres Lebens bewusst und vorausschauend handeln. Es ist entscheidend, dass wir uns nicht von kurzfristigen Interessen leiten lassen, sondern langfristige Ziele verfolgen, die das Wohl der kommenden Generationen sichern. Dies bedeutet auch, dass wir bereit sein müssen, uns von alten Denkmustern und Gewohnheiten zu lösen, die nicht mehr mit den globalen Bedürfnissen und Herausforderungen vereinbar sind. Der Wandel wird nicht immer einfach oder komfortabel sein, aber er ist notwendig, um die gesellschaftlichen, ökologischen und wirtschaftlichen Ziele zu erreichen, die wir uns gesetzt haben.
Ein Aspekt dieses Wandels ist die Neudefinition von Wohlstand. Wie bereits angesprochen, muss Wohlstand nicht nur materiellen Reichtum umfassen, sondern auch das Wohlbefinden, die soziale Verbundenheit und die Gesundheit der Menschen. Es wird zunehmend erkannt, dass das Streben nach unendlichem Wachstum auf einem begrenzten Planeten keine langfristige Lösung darstellt. Stattdessen müssen wir Konzepte wie Gemeinwohl, soziale Innovation und Lebensqualität stärker in den Mittelpunkt stellen.
Ein weiterer wichtiger Bereich, der die Zukunft prägen wird, ist die Art und Weise, wie wir mit Technologie umgehen. Zwar bietet der technologische Fortschritt enorme Chancen, doch er bringt auch Herausforderungen mit sich, insbesondere im Hinblick auf den Datenschutz, die künstliche Intelligenz und die Automatisierung von Arbeitsplätzen. Es wird zunehmend notwendig, ethische Leitlinien zu entwickeln, um sicherzustellen, dass technologische Entwicklungen im Einklang mit den Werten der Gesellschaft stehen. Wir müssen sicherstellen, dass Technologie nicht nur den Reichen und Mächtigen zugutekommt, sondern allen Menschen gleichermaßen zugänglich ist und dazu beiträgt, die Lebensqualität zu verbessern, ohne soziale Ungleichheiten zu verschärfen.
Die Rolle der Bildung in dieser Transformation kann nicht hoch genug eingeschätzt werden. In einer sich schnell verändernden Welt ist lebenslanges Lernen unerlässlich, um die Fähigkeiten und das Wissen zu erwerben, die für den Umgang mit neuen Herausforderungen notwendig sind. Bildung sollte nicht nur den Erwerb von Fachwissen vermitteln, sondern auch kritisches Denken, Problemlösungsfähigkeiten und eine starke ethische Grundlage fördern. Nur so können wir sicherstellen, dass die nächsten Generationen in der Lage sind, mit den komplexen und dynamischen Problemen unserer Zeit umzugehen.
Die Rolle der Politik wird ebenfalls entscheidend sein, um den nötigen Wandel voranzutreiben. Regierungen müssen die Verantwortung übernehmen, klare und faire Rahmenbedingungen zu schaffen, die nachhaltiges Wachstum und soziale Gerechtigkeit fördern. Dabei ist es wichtig, dass politische Entscheidungen nicht nur auf kurzfristige Wählerinteressen ausgerichtet sind, sondern auf langfristige Ziele, die das Gemeinwohl und die Zukunft der gesamten Menschheit im Blick haben. Die Zusammenarbeit auf internationaler Ebene wird zunehmend notwendig, um globale Probleme wie den Klimawandel, die Flüchtlingskrise oder die weltweite Armut zu bewältigen.
Natürlich sind auch die Unternehmen gefragt, ihren Teil zu diesem Wandel beizutragen. Unternehmen müssen erkennen, dass sie nicht nur als Profitmaschinen agieren, sondern auch eine Verantwortung gegenüber der Gesellschaft und der Umwelt haben. Nachhaltigkeit, soziale Verantwortung und ethisches Handeln sollten genauso im Fokus stehen wie wirtschaftlicher Erfolg. Diejenigen Unternehmen, die diesen Wandel aktiv gestalten, werden langfristig nicht nur als führend in ihrem Sektor angesehen, sondern auch als Vorbilder für eine neue Art des Wirtschaftens, die auf Nachhaltigkeit und Verantwortung basiert.
Letztlich wird es auf das Handeln jedes Einzelnen ankommen. Jede Entscheidung, die wir treffen – sei es im Konsumverhalten, in der Art und Weise, wie wir unsere Zeit verbringen oder in den Werten, die wir unseren Kindern vermitteln – hat Einfluss auf die Zukunft. Der Wandel beginnt bei uns allen, in unseren täglichen Handlungen und den Prinzipien, die wir vertreten. Nur durch eine kollektive Anstrengung können wir die Herausforderungen bewältigen, vor denen wir als Gesellschaft stehen, und eine Zukunft schaffen, die für alle gerecht, nachhaltig und lebenswert ist.
Es ist eine Zeit des Umbruchs, aber auch der Chancen. Wenn wir uns gemeinsam auf den Weg machen, die Welt für uns und die kommenden Generationen zu verbessern, können wir ein neues Zeitalter einläuten, in dem Zusammenarbeit, Respekt und Verantwortung die treibenden Kräfte sind. Die Welt ist nicht festgelegt – sie ist formbar. Und es liegt an uns, sie zu gestalten.
Mikro Dampfturbine

Mikrodampfturbinen sind eine spezielle Art von Dampfturbinen, die für kleinere Anwendungen und dezentrale Energieerzeugung konzipiert sind. Im Vergleich zu großen industriellen Dampfturbinen, die in Kraftwerken verwendet werden, sind Mikrodampfturbinen kompakter und für niedrigere Leistungsbereiche optimiert. Diese Turbinen finden zunehmend Anwendung in Bereichen, in denen kleinere, flexible und umweltfreundliche Energiequellen benötigt werden.
Anwendungsgebiete
Mikrodampfturbinen werden oft in sogenannten „Mikro-Kraft-Wärme-Kopplung“-Systemen (Mikro-KWK) eingesetzt, bei denen sowohl Strom als auch Wärme gleichzeitig erzeugt werden. Diese Systeme sind besonders in der Industrie, in kleineren Produktionsstätten, in Gebäuden oder bei dezentraler Energieversorgung von Vorteil. Besonders in abgelegenen Gebieten oder bei kritischer Infrastruktur können Mikrodampfturbinen als zuverlässige und effiziente Energiequelle dienen.
Ein weiteres interessantes Anwendungsfeld ist die Nutzung von Abwärme aus industriellen Prozessen. In vielen Industrien entstehen große Mengen an Abwärme, die häufig ungenutzt bleiben. Mikrodampfturbinen können diese Abwärme nutzen, um Strom zu erzeugen und so die Energieeffizienz zu steigern. Beispiele dafür sind die Lebensmittelindustrie, die chemische Industrie oder die Abfallverwertung.
Funktionsweise
Wie bei größeren Dampfturbinen basiert die Funktionsweise einer Mikrodampfturbine auf der Umwandlung von thermischer Energie in mechanische Energie, die anschließend in elektrische Energie umgewandelt wird. Dazu wird Wasser erhitzt, um Dampf zu erzeugen. Der Dampf strömt dann mit hohem Druck in die Turbine, wodurch die Turbine in Rotation versetzt wird. Die mechanische Energie wird über einen Generator in elektrische Energie umgewandelt. Mikrodampfturbinen können mit einer Vielzahl von Brennstoffen betrieben werden, darunter fossile Brennstoffe, Biomasse oder auch erneuerbare Energien wie Solar- oder Geothermieenergie.
Vorteile
- Hohe Effizienz: Mikrodampfturbinen sind in der Lage, Abwärme und Restenergie aus Prozessen oder Systemen effektiv zu nutzen. Das steigert die Gesamtenergieeffizienz und verringert den Bedarf an zusätzlichen Energiequellen.
- Dezentrale Energieversorgung: Diese Turbinen bieten eine dezentrale Lösung für die Energieerzeugung, was insbesondere in ländlichen oder abgelegenen Gebieten von Vorteil ist, in denen der Zugang zum Stromnetz begrenzt oder unzuverlässig ist.
- Kompakte Bauweise: Mikrodampfturbinen sind deutlich kleiner als ihre großen Pendants, was die Installation und Wartung erleichtert. Sie können in engeren Räumen und bei begrenztem Platzangebot eingesetzt werden.
- Umweltfreundlichkeit: Durch die Nutzung von Abwärme oder erneuerbaren Brennstoffen können Mikrodampfturbinen zu einer Reduktion der CO2-Emissionen beitragen und eine umweltfreundlichere Energieerzeugung fördern.
Herausforderungen
Trotz ihrer Vorteile gibt es auch einige Herausforderungen bei der Nutzung von Mikrodampfturbinen:
- Kosten: Die Anfangsinvestition in Mikrodampfturbinen kann relativ hoch sein, obwohl die Einsparungen durch die hohe Effizienz und die Nutzung von Abwärme langfristig die Kosten ausgleichen können.
- Betriebsbedingungen: Mikrodampfturbinen benötigen eine konstante Wärmequelle, und ihre Leistung kann von der Art und Temperatur der zur Verfügung stehenden Wärmequelle abhängen. Dies kann die Flexibilität in bestimmten Anwendungen einschränken.
- Wartung und Lebensdauer: Obwohl Mikrodampfturbinen in der Regel eine lange Lebensdauer haben, erfordern sie regelmäßige Wartung, um die hohe Effizienz aufrechtzuerhalten und Ausfälle zu vermeiden. Insbesondere bei der Nutzung von Abwärme muss auf Verunreinigungen und Verschmutzungen in der Turbine geachtet werden.
Zukunftsperspektiven
Mit der zunehmenden Nachfrage nach nachhaltiger und dezentraler Energieerzeugung wird erwartet, dass Mikrodampfturbinen eine größere Rolle spielen werden. Ihre Fähigkeit, Abwärme und erneuerbare Energien zu integrieren, macht sie zu einer wichtigen Technologie für eine nachhaltige Zukunft. Besonders in Bereichen wie der Industrie, dem Gewerbe und der privaten Haushaltsenergieversorgung könnten Mikrodampfturbinen in den kommenden Jahren weiter an Bedeutung gewinnen.
Ein weiterer vielversprechender Aspekt ist die Weiterentwicklung der Technologie. Durch die Forschung an effizienteren Materialien, besseren Wärmetauschern und optimierten Turbinengeometrien könnten Mikrodampfturbinen künftig noch leistungsfähiger und kostengünstiger werden. Auch die Integration in Smart-Grid-Systeme könnte die Flexibilität und Effizienz von Mikrodampfturbinen weiter verbessern und sie zu einer noch attraktiveren Lösung für die dezentrale Energieversorgung machen.
Insgesamt bieten Mikrodampfturbinen eine vielversprechende Möglichkeit, Energie effizienter zu nutzen, insbesondere in dezentralen und industriellen Anwendungen. Sie tragen dazu bei, die Energiewende voranzutreiben, indem sie saubere, effiziente und flexible Lösungen für die Energieerzeugung bieten.
Die Weiterentwicklung von Mikrodampfturbinen wird voraussichtlich auch durch technologische Innovationen im Bereich der Materialien und Fertigungstechnik beeinflusst werden. Fortschritte in der Werkstofftechnik, wie etwa die Entwicklung hochtemperaturbeständiger und korrosionsbeständiger Materialien, könnten die Effizienz und Langlebigkeit von Mikrodampfturbinen weiter erhöhen. Zudem könnten innovative Fertigungstechniken, wie 3D-Druck, zur Herstellung von Turbinenteilen mit komplexeren Geometrien und verbesserten Leistungseigenschaften führen. Solche Technologien könnten die Produktionskosten senken und die Anpassungsfähigkeit der Turbinen an verschiedene Anwendungen und Betriebsbedingungen verbessern.
Integration in Smart Grids und IoT
Ein besonders spannender Trend in der Weiterentwicklung von Mikrodampfturbinen ist die Integration in Smart Grids und das Internet der Dinge (IoT). In einem intelligenten Stromnetz können Mikrodampfturbinen Teil eines dynamischen, interaktiven Systems werden, das es ermöglicht, die Energieerzeugung und -verteilung effizient zu steuern. Sensoren und Kommunikationssysteme könnten kontinuierlich den Betrieb der Turbinen überwachen und die erzeugte Energie in Echtzeit an das Netz anpassen, um Schwankungen in der Energieversorgung auszugleichen.
Darüber hinaus könnten Mikrodampfturbinen in Kombination mit anderen dezentralen Energiequellen wie Solar- oder Windkraftwerken als Teil eines hybriden Energiesystems betrieben werden. In einem solchen System könnten Mikrodampfturbinen nicht nur zur Energieerzeugung, sondern auch zur Stabilisierung des Netzwerks beitragen, indem sie überschüssige Energie speichern oder in Zeiten hoher Nachfrage zusätzlich Energie liefern.
Mikrodampfturbinen in der mobilen Energieversorgung
Ein weiterer wachsender Markt für Mikrodampfturbinen könnte die mobile Energieversorgung sein. In Bereichen wie dem Transportwesen, in der Schifffahrt oder in abgelegenen militärischen Einrichtungen könnten Mikrodampfturbinen eine zuverlässige Energiequelle darstellen, die mit relativ kleinen, transportablen Systemen betrieben werden kann. In diesen Szenarien könnten Mikrodampfturbinen genutzt werden, um Fahrzeuge, Schiffe oder mobile Einrichtungen mit Strom zu versorgen, während gleichzeitig Wärme und Abwärme genutzt werden können, um den Betrieb zu optimieren.
Kombination mit Brennstoffzellen
Eine vielversprechende Technologie, die Mikrodampfturbinen ergänzen könnte, ist die Brennstoffzelle. In einigen Konzepten könnten Mikrodampfturbinen mit Brennstoffzellen kombiniert werden, um die Energieerzeugung effizienter und flexibler zu gestalten. Brennstoffzellen sind in der Lage, Strom mit hoher Effizienz aus Wasserstoff oder anderen Brennstoffen zu erzeugen, während Mikrodampfturbinen die Abwärme aus dem Prozess nutzen können. Eine solche Kombination könnte nicht nur die Effizienz weiter steigern, sondern auch eine nahezu emissionsfreie Energiequelle für spezielle Anwendungen bieten.
Wirtschaftliche und politische Perspektiven
Ein weiterer Faktor, der die Entwicklung und den Einsatz von Mikrodampfturbinen beeinflussen könnte, ist die politische und wirtschaftliche Unterstützung für grüne Technologien und nachhaltige Energiequellen. Regierungen auf der ganzen Welt haben begonnen, die Nutzung erneuerbarer Energien und die Reduzierung von CO2-Emissionen zu fördern. Dies könnte zu einer verstärkten Nachfrage nach Mikrodampfturbinen und anderen dezentralen, effizienten Energieerzeugungstechnologien führen. Subventionen, Steuererleichterungen oder andere finanzielle Anreize könnten den Einstieg in den Markt erleichtern und die Rentabilität solcher Systeme erhöhen.
In vielen Ländern gibt es bereits Bestrebungen, die Energieproduktion und -verteilung zu dezentralisieren, was Mikrodampfturbinen zu einer attraktiven Option macht. Dies könnte insbesondere in Regionen mit unzuverlässiger Stromversorgung oder in Entwicklungsländern von großer Bedeutung sein, wo der Zugang zu zentralisiertem Stromnetz begrenzt ist. Mikrodampfturbinen könnten in diesen Fällen eine zuverlässige, kostengünstige und umweltfreundliche Lösung bieten.
Fazit
Mikrodampfturbinen bieten eine Vielzahl von Vorteilen, insbesondere in Anwendungen, die eine dezentrale, effiziente und flexible Energieerzeugung erfordern. Ihre Fähigkeit, Abwärme zu nutzen, und ihre Kompaktheit machen sie zu einer attraktiven Lösung für verschiedene industrielle, gewerbliche und private Anwendungen. Die Technologie hat das Potenzial, nicht nur zur Steigerung der Energieeffizienz beizutragen, sondern auch einen wichtigen Beitrag zur Reduzierung von CO2-Emissionen und zur Förderung einer nachhaltigen Energiezukunft zu leisten.
Mit der Weiterentwicklung der Technologie und der zunehmenden Integration in intelligente Netzwerke, mobile Systeme und hybride Energiestrukturen ist zu erwarten, dass Mikrodampfturbinen in den kommenden Jahren eine noch größere Rolle in der globalen Energieversorgung spielen werden. Die Kombination aus technologischem Fortschritt, politischer Unterstützung und wachsendem Umweltbewusstsein könnte dazu führen, dass Mikrodampfturbinen zu einer Schlüsseltechnologie für die Energiewende und den Übergang zu einer nachhaltigeren, dezentraleren Energiezukunft werden.
Die zukünftige Entwicklung von Mikrodampfturbinen könnte noch vielseitiger werden, insbesondere durch den verstärkten Fokus auf die Nutzung von erneuerbaren Energiequellen und die Implementierung von modernen, flexiblen Energiesystemen. Mikrodampfturbinen bieten nicht nur Vorteile im Hinblick auf die Energieerzeugung, sondern können auch mit anderen innovativen Technologien kombiniert werden, um die Effizienz und Nachhaltigkeit weiter zu maximieren.
Integration mit Wärmespeichersystemen
Ein weiterer vielversprechender Bereich für Mikrodampfturbinen ist die Integration in Wärmespeichersysteme. Die Nutzung von thermischer Energie und deren Speicherung für die spätere Verwendung ist ein wachsendes Forschungsthema im Bereich der Energieeffizienz. Mikrodampfturbinen könnten mit verschiedenen Formen von Wärmespeichern kombiniert werden, wie etwa thermochemischen, thermischen oder Phasenwechselmaterialien, die die erzeugte Wärme speichern und bei Bedarf wieder freisetzen. Diese Systeme könnten in verschiedenen Bereichen, von industriellen Prozessen bis hin zu Gebäuden, zur Optimierung des gesamten Energieverbrauchs und zur Reduzierung von Energieverlusten beitragen.
Mikrodampfturbinen und die Nutzung von Abwärme aus geothermischen Quellen
Die geothermische Energieerzeugung ist ein weiteres faszinierendes Gebiet, auf dem Mikrodampfturbinen zum Einsatz kommen könnten. Geothermische Anlagen erzeugen häufig Abwärme, die nicht immer vollständig genutzt wird. Mikrodampfturbinen können diese überschüssige Energie in Strom umwandeln, wodurch die Gesamtenergieeffizienz des geothermischen Systems verbessert wird. Diese Technologie könnte insbesondere in Regionen mit geothermischem Potenzial eine wichtige Rolle spielen und zu einer besseren Nutzung der vorhandenen Ressourcen beitragen.
Mikrodampfturbinen und die Kombination mit Wasserstofftechnologie
Die Wasserstofftechnologie ist ein weiterer aufkommender Bereich, der das Potenzial hat, die Energieerzeugung grundlegend zu verändern. Mikrodampfturbinen könnten in Kombination mit Wasserstoffbrennstoffzellen oder Wasserstoff als Brennstoffquelle verwendet werden. Die Mikroturbine könnte den Wasserstoff in einem kleinen, kompakten System verbrennen, um sowohl Strom als auch Wärme zu erzeugen. Diese Form der dezentralen Energieerzeugung könnte besonders für Anwendungen in abgelegenen Gebieten oder in Fahrzeugen von Interesse sein, bei denen Platz und Energieeffizienz entscheidend sind.
Wirtschaftliche Chancen und Marktentwicklung
In den kommenden Jahren könnte die Nachfrage nach Mikrodampfturbinen insbesondere in Märkten steigen, die sich stark auf Energieeffizienz und die Nutzung erneuerbarer Energiequellen konzentrieren. Der zunehmende Fokus auf die Reduzierung von CO2-Emissionen und die Förderung von grünen Technologien durch Regierungen und Unternehmen wird das Wachstum von Mikrodampfturbinen weiter vorantreiben. Mikro-KWK-Systeme, die Strom und Wärme kombinieren, könnten in Wohngebäuden, Hotels, Krankenhäusern und kleinen Industrieanlagen immer populärer werden. Auch die Elektrifizierung von ländlichen Regionen in Entwicklungsländern könnte durch Mikrodampfturbinen als dezentrale Energiequelle unterstützt werden, da diese Technologie nicht nur zuverlässig ist, sondern auch schnell in bestehenden Infrastrukturen eingesetzt werden kann.
In den letzten Jahren haben sich Mikrodampfturbinen als ein tragfähiges Konzept für die dezentrale Energieerzeugung etabliert, und mit dem Fokus auf Nachhaltigkeit, Kreislaufwirtschaft und Emissionsreduktion wird erwartet, dass ihre Bedeutung weiter wächst. Die potenziellen Marktchancen für Mikrodampfturbinen erstrecken sich über viele Sektoren, einschließlich der Industrie, dem Bauwesen, der Landwirtschaft und sogar dem Transportwesen. Die Fähigkeit, überschüssige Wärme und Abwärme aus industriellen Prozessen zu nutzen, wird zunehmend als wirtschaftlich sinnvoll erkannt, da Unternehmen und Gemeinden nach Möglichkeiten suchen, ihre Energiekosten zu senken und gleichzeitig umweltfreundlicher zu werden.
Verbesserung der Skalierbarkeit und Flexibilität
Ein weiterer Bereich, in dem Mikrodampfturbinen an Bedeutung gewinnen könnten, ist ihre Skalierbarkeit und Flexibilität. Die Möglichkeit, Mikroturbinen in unterschiedlichen Größen und für verschiedene Leistungsanforderungen zu konfigurieren, bietet große Vorteile in Bezug auf die Anpassungsfähigkeit. Diese Flexibilität ermöglicht es, Mikrodampfturbinen in einer Vielzahl von Szenarien einzusetzen, von der Notstromversorgung über die industrielle Nutzung bis hin zur Integration in komplexere, hybride Energiesysteme.
Mit der zunehmenden Nachfrage nach flexiblen, robusten und skalierbaren Energiesystemen, die sich sowohl in großen als auch in kleinen Anwendungen bewähren, könnten Mikrodampfturbinen zu einer zentralen Technologie für die zukünftige Energieinfrastruktur werden. Sie bieten nicht nur eine Lösung für die direkte Energieerzeugung, sondern können auch als integraler Bestandteil größerer, komplexerer Systeme fungieren, die mehrere erneuerbare Quellen kombinieren, um eine stabile und nachhaltige Energieversorgung zu gewährleisten.
Fazit
Die Zukunft der Mikrodampfturbinen scheint vielversprechend, da sie ein enormes Potenzial zur Verbesserung der Energieeffizienz und zur Förderung nachhaltiger Energieerzeugung bieten. Ihre Anwendungsmöglichkeiten sind breit gefächert, von der Nutzung von Abwärme und erneuerbaren Quellen bis hin zur Integration in dezentrale, hybride Energiesysteme. Die zunehmende politische und gesellschaftliche Unterstützung für grüne Energietechnologien und die fortschreitende Entwicklung in den Bereichen Materialien, Fertigung und Digitalisierung werden dazu beitragen, dass Mikrodampfturbinen eine bedeutende Rolle auf dem Weg zu einer nachhaltigeren Energiezukunft spielen.
Die Zukunft von Mikrodampfturbinen wird von mehreren Schlüsselfaktoren geprägt sein, die ihre Anwendungsmöglichkeiten erweitern und ihre Effizienz steigern werden. Dazu gehören die fortschreitende Entwicklung neuer Materialien, die Integration in fortschrittliche Energiesysteme und die enge Zusammenarbeit mit anderen erneuerbaren Technologien. Insbesondere die Kombination von Mikrodampfturbinen mit anderen dezentralen Energiequellen wie Solarenergie oder Windkraft könnte zu einer effektiveren Nutzung von Energie führen. In solchen Systemen würde die Mikroturbine nicht nur Strom erzeugen, sondern auch als eine Art Stabilisierungseinheit fungieren, die überschüssige Energie aufnimmt und bei Bedarf in das Netz einspeist oder speichert.
Ein weiterer wichtiger Punkt ist die Miniaturisierung und der Fortschritt in der Fertigungstechnik. Fortschritte im 3D-Druck und in der computergestützten Designtechnik könnten dazu beitragen, die Kosten für Mikrodampfturbinen zu senken, ihre Herstellung zu vereinfachen und eine größere Flexibilität bei der Anpassung an spezifische Anforderungen zu ermöglichen. Dies könnte insbesondere in Nischenanwendungen von Bedeutung sein, bei denen maßgeschneiderte Lösungen benötigt werden.
Die Möglichkeit, Mikrodampfturbinen in verschiedenen Betriebsumgebungen zu verwenden, stellt ebenfalls einen Vorteil dar. In Kombination mit Wärmespeichersystemen könnten Mikrodampfturbinen in der Lage sein, nicht nur kontinuierliche Energie zu liefern, sondern auch temporäre Spitzen abzudecken. Dies ist besonders wichtig, wenn die Energieerzeugung durch intermittierende Quellen wie Wind- oder Solarenergie schwankt.
Die Implementierung von Mikrodampfturbinen in vernetzte, intelligente Energiesysteme wird ebenfalls eine wichtige Rolle spielen. Diese Systeme könnten eine präzisere Steuerung der Energieproduktion und -verteilung ermöglichen und eine bessere Anpassung an die variablen Anforderungen von Haushalten und Industrieunternehmen bieten. Indem Mikrodampfturbinen mit anderen Geräten und Systemen im Energiesektor kommunizieren, können sie optimal in das größere Energienetz integriert werden und so zur Versorgungssicherheit beitragen.
Außerdem könnte die zunehmende Nutzung von Mikrodampfturbinen dazu beitragen, die Energieautarkie von Einzelhaushalten und kleinen Betrieben zu erhöhen. In abgelegenen Regionen ohne zuverlässigen Zugang zum zentralen Stromnetz oder in Gebieten, in denen die Stromversorgung aufgrund von Naturkatastrophen oder anderen Gründen unzuverlässig ist, könnten Mikrodampfturbinen eine wertvolle Alternative darstellen. In solchen Szenarien könnten sie nicht nur als Notstromversorgung, sondern auch als primäre Energiequelle dienen, indem sie lokal erzeugte Wärme und Abwärme in Energie umwandeln.
Langfristig gesehen könnte die breitere Einführung von Mikrodampfturbinen als Teil eines globalen Übergangs zu nachhaltigeren Energiesystemen entscheidend sein. Mit ihrer Fähigkeit, verschiedene Formen von Abwärme und erneuerbare Energien zu integrieren, bieten Mikrodampfturbinen eine umweltfreundliche und flexible Lösung für die Energieproduktion. Indem sie die Notwendigkeit zentralisierter, großskaliger Kraftwerke verringern, könnten sie dazu beitragen, die Abhängigkeit von fossilen Brennstoffen weiter zu reduzieren und die Reduktion von Treibhausgasemissionen zu beschleunigen.
Zusammenfassend lässt sich sagen, dass Mikrodampfturbinen eine Schlüsseltechnologie für die Zukunft der dezentralen Energieerzeugung darstellen könnten. Ihre Vielseitigkeit und Effizienz ermöglichen es, verschiedene Energiequellen zu integrieren und gleichzeitig den Energieverbrauch zu optimieren. Mit der fortschreitenden Weiterentwicklung der Technologie und ihrer zunehmenden Integration in intelligente Energiesysteme könnten Mikrodampfturbinen zu einem zentralen Bestandteil der globalen Energiewende werden.
Was ist Sattdampf

Sattdampf ist eine Form von Dampf, bei dem der Dampf in einem thermodynamischen Zustand vorliegt, in dem er gerade im Gleichgewicht mit Wasser existiert. Das bedeutet, dass der Dampf die maximale Menge an Wärmeenergie enthält, die er bei einer bestimmten Temperatur und einem bestimmten Druck aufnehmen kann, ohne dabei zusätzliche Phasenänderungen durchlaufen zu müssen. Sattdampf wird oft als “gesättigter Dampf” bezeichnet und ist eine der grundlegenden Formen von Dampf in thermodynamischen Systemen, besonders in der Energietechnik.
Im thermodynamischen Diagramm für Wasser (z. B. im p-T-Diagramm oder T-s-Diagramm) befindet sich Sattdampf an der Grenze der Flüssigkeit-Dampf-Gleichgewichtslinie, die als Sättigungslinie bezeichnet wird. Diese Linie trennt den Bereich, in dem Wasser flüssig ist, von dem Bereich, in dem es verdampft oder verdampfen kann.
Ein Beispiel ist, wenn Wasser in einem geschlossenen Behälter erhitzt wird und dabei Dampf entsteht. Wenn das Wasser genau den Punkt erreicht, an dem es vollständig verdampft ist, ohne dass zusätzliche Wärme zugeführt wird, handelt es sich um Sattdampf. In diesem Zustand bleibt die Temperatur des Dampfes konstant, selbst wenn weiter Wärme zugeführt wird, bis der gesamte Wasseranteil in Dampf umgewandelt wurde.
Eigenschaften von Sattdampf
- Temperatur und Druck: Die Temperatur und der Druck des Sattdampfes hängen miteinander zusammen und sind für jede Substanz spezifisch. Für Wasser gibt es bei jedem bestimmten Druck eine spezifische Temperatur, bei der das Wasser in den Sattdampfzustand übergeht. Dies wird als Sättigungstemperatur bezeichnet.
- Verdampfungsenthalpie: Der Sattdampf enthält die gesamte Energie, die benötigt wird, um das Wasser von seinem flüssigen Zustand in den gasförmigen Zustand zu überführen, ohne die Temperatur zu verändern. Diese Energie wird als Verdampfungsenthalpie bezeichnet.
- Volumen: Der Sattdampf hat ein größeres Volumen als die Flüssigkeit, da sich die Moleküle im gasförmigen Zustand weiter voneinander entfernen. Das Volumen von Sattdampf ist abhängig von Temperatur und Druck und wird durch die ideale Gasgleichung oder spezifizierte Dampftabellen beschrieben.
- Energiegehalt: Sattdampf ist eine sehr wichtige Form von Energieübertragung in thermischen Systemen wie Dampfkraftwerken, Heizsystemen und industriellen Prozessen. Die Wärme, die im Sattdampf enthalten ist, kann zur mechanischen Arbeit (z. B. in Dampfturbinen) oder zur Wärmeversorgung verwendet werden.
Verwendung von Sattdampf in der Technik
Sattdampf spielt eine entscheidende Rolle in vielen industriellen Prozessen, insbesondere in Dampfkraftwerken und bei der Energieerzeugung. Dampfturbinen in Kraftwerken, die Strom erzeugen, nutzen typischerweise Sattdampf, um durch den Druck und die Temperatur des Dampfes mechanische Energie zu gewinnen. Der Sattdampf wird in die Turbine geleitet, und seine Ausdehnung und Bewegung treiben die Turbine an, die mit einem Generator verbunden ist.
In vielen Fällen wird der Sattdampf auch in Heizsystemen genutzt, da seine Temperatur und Energieübertragungseigenschaften es ermöglichen, Wärme effizient zu übertragen. Beispielsweise wird in der Gebäudetechnik oft Sattdampf verwendet, um in Heizsystemen, wie Dampfkesseln oder Heizkörpern, Wärme bereitzustellen.
Fazit
Sattdampf ist eine besonders wichtige Form von Dampf in der thermodynamischen Energieübertragung. Er zeichnet sich durch einen Zustand aus, in dem Dampf und Wasser im thermodynamischen Gleichgewicht sind, was ihn zu einer idealen Quelle für Wärme und Energie macht. Das Verständnis von Sattdampf ist für die Entwicklung von effizienten Heizsystemen, Dampfkraftwerken und vielen anderen thermischen Prozessen entscheidend.
Sattdampf hat auch eine zentrale Bedeutung in der Thermodynamik, da er hilft, den Energiegehalt von Dampfsystemen zu verstehen und zu berechnen. Die Enthalpie des Sattdampfs ist entscheidend für die Bestimmung der Arbeit, die in thermischen Maschinen wie Dampfturbinen erzeugt werden kann. In Dampfkraftwerken beispielsweise wird Sattdampf durch die Verbrennung von Brennstoffen oder die Nutzung anderer Wärmequellen erzeugt, um mechanische Arbeit zu leisten. Der Dampf wird in Turbinen geleitet, wo seine Temperatur und Druck verringert werden, wobei die Umwandlung von thermischer in mechanische Energie stattfindet.
Ein weiteres Beispiel für den Einsatz von Sattdampf ist in der Lebensmittelindustrie, wo er für die Sterilisation oder Pasteurisierung von Produkten verwendet wird. In diesen Prozessen wird Sattdampf genutzt, um eine gleichmäßige und kontrollierte Wärmeübertragung auf die Produkte zu gewährleisten. Da der Sattdampf eine konstante Temperatur hat, sorgt er für eine präzise und effiziente Erhitzung.
In der chemischen Industrie wird Sattdampf häufig eingesetzt, um Reaktionen bei hohen Temperaturen zu ermöglichen, bei denen eine stabile Wärmequelle benötigt wird. Auch in der Verfahrenstechnik ist der Einsatz von Sattdampf weit verbreitet, zum Beispiel in Destillationskolonnen, bei der Dampfdestillation oder in Prozessen, die die Wärmeenergie aus dem Dampf für chemische Reaktionen nutzen.
Zusätzlich zum Einsatz in der Industrie kann Sattdampf auch in Heiz- und Kühlsystemen eingesetzt werden. In vielen industriellen und gewerblichen Anwendungen wird die Abwärme von Sattdampf durch Wärmeübertrager weiterverwendet, um einen Teil der Energie zurückzugewinnen oder sie für andere Prozesse zu nutzen. Dies trägt zur Effizienzsteigerung in Systemen bei, die hohe Mengen an Energie verbrauchen.
Ein weiterer Bereich, in dem Sattdampf von großer Bedeutung ist, ist die Wärmespeicherung und -übertragung in Fernwärmenetzen. Hier wird Sattdampf als Träger der Wärmeenergie genutzt, die über weite Entfernungen transportiert werden kann. Die hohe Temperatur und der Druck des Sattdampfs ermöglichen es, große Mengen an Energie zu übertragen und so die Heizbedürfnisse von Haushalten und Industriegebäuden effizient zu decken.
Die thermodynamische Analyse von Sattdampf ist auch in der Ausbildung und Forschung von großer Bedeutung. Wissenschaftler und Ingenieure verwenden Sattdampfdaten, um die Leistung von Dampfkraftwerken zu optimieren, die Effizienz von Wärmesystemen zu verbessern und innovative Technologien zu entwickeln, die auf den Eigenschaften von Dampf und Flüssigkeit basieren. Sattdampf ist somit nicht nur eine praktische Komponente in verschiedenen Industrien, sondern auch ein wertvolles Konzept, das tiefgehende Einblicke in die Mechanismen von Energieumwandlung und Wärmeübertragung bietet.
Die Berechnung und Analyse von Sattdampf erfolgt häufig unter Verwendung von Dampftabellen oder durch thermodynamische Formeln, die spezifische Werte für Temperatur, Druck, Enthalpie und Entropie bei gegebenen Zuständen liefern. Diese Tabellen sind ein unverzichtbares Werkzeug für Ingenieure, die mit Dampfsystemen arbeiten, da sie eine schnelle und präzise Bestimmung der relevanten thermodynamischen Eigenschaften ermöglichen. In diesen Tabellen sind sowohl die Eigenschaften von Sattdampf als auch von gesättigtem Wasser (also Wasser bei der gleichen Temperatur und dem gleichen Druck, das noch nicht verdampft ist) aufgeführt. Auf Grundlage dieser Daten können Ingenieure die Menge an Energie berechnen, die in einem Dampfsystem enthalten ist, und die für die Dampferzeugung benötigte Wärme ermitteln.
Darüber hinaus können in modernen Anlagen auch digitale Tools und Software verwendet werden, um die Eigenschaften von Sattdampf zu bestimmen und die Effizienz von Dampfanlagen in Echtzeit zu überwachen. Diese Technologien ermöglichen eine präzisere Steuerung und eine Anpassung der Betriebsbedingungen, um die maximale Effizienz zu erzielen. Die fortschrittliche Simulation von Dampfsystemen, bei der Sattdampf als wichtige Grundlage dient, ist ein wesentlicher Bestandteil von Optimierungsprozessen in der Energiewirtschaft.
Ein Aspekt, der ebenfalls nicht zu vernachlässigen ist, ist die Energieerzeugung aus erneuerbaren Quellen. Sattdampf kann nicht nur durch fossile Brennstoffe erzeugt werden, sondern auch durch geothermische Energiequellen oder Biomasse. In geothermischen Anlagen wird Wasser in heißen Gesteinsschichten erhitzt, sodass es als Sattdampf an die Oberfläche tritt und zur Stromerzeugung oder für industrielle Prozesse genutzt werden kann. Biomasseanlagen nutzen ebenfalls Sattdampf, der durch die Verbrennung organischer Materialien erzeugt wird, um Elektrizität zu produzieren oder industrielle Wärme bereitzustellen. Solche erneuerbaren Quellen tragen dazu bei, den CO2-Ausstoß zu reduzieren und eine nachhaltigere Energieversorgung zu schaffen.
Die Nutzung von Sattdampf in Hybrid- oder kombinierten Wärme- und Kraftsystemen (KWK) ist ebenfalls ein wachsender Bereich. Diese Systeme sind darauf ausgelegt, sowohl Strom als auch Wärme gleichzeitig zu erzeugen, was die Gesamtenergieeffizienz deutlich erhöht. Sattdampf ist in diesen Systemen ein wichtiger Bestandteil, da er sowohl für die Stromerzeugung als auch für die Wärmebereitstellung genutzt wird. In KWK-Anlagen kann der Sattdampf direkt zur Erzeugung von Strom in Turbinen verwendet werden, während die Abwärme für Heizungs- oder Kühlprozesse genutzt wird.
Zusammenfassend lässt sich sagen, dass Sattdampf eine Schlüsselrolle in vielen thermischen Prozessen und Technologien spielt. Seine Fähigkeit, Energie zu transportieren und in mechanische Arbeit umzuwandeln, macht ihn zu einer unverzichtbaren Ressource in der Energieerzeugung und -verwendung. Von der Industrie über die Energiewirtschaft bis hin zu umweltfreundlicheren, erneuerbaren Anwendungen – Sattdampf bleibt ein zentrales Element in der Entwicklung effizienter und nachhaltiger Energiesysteme.
Ein weiterer bemerkenswerter Aspekt der Nutzung von Sattdampf ist seine Rolle bei der Verbesserung der Effizienz von Heizungs-, Lüftungs- und Klimaanlagen (HVAC). In vielen industriellen Prozessen, wie etwa in der chemischen Produktion, in Raffinerien oder in der Lebensmittelverarbeitung, wird Sattdampf verwendet, um eine konstante Temperatur zu gewährleisten und eine effiziente Wärmeübertragung zu ermöglichen. In diesen Anwendungen kann die Fähigkeit des Sattdampfes, Wärme schnell und gleichmäßig zu übertragen, helfen, die Prozessstabilität zu erhöhen und gleichzeitig den Energieverbrauch zu optimieren. Zudem reduziert die Verwendung von Sattdampf in Heizsystemen den Bedarf an elektrisch betriebenen Heizgeräten, was zu geringeren Betriebskosten führt.
Ein weiterer interessanter Bereich, in dem Sattdampf zunehmend Bedeutung erlangt, ist die Nutzung in thermischen Speichertechnologien. Sattdampf kann als Träger von Wärmeenergie dienen, die in einem thermischen Energiespeicher gespeichert und bei Bedarf wieder abgegeben wird. Solche Systeme sind besonders nützlich, um die Schwankungen bei der Energieproduktion aus erneuerbaren Quellen wie Wind- oder Solarenergie auszugleichen. In Zeiten hoher Energieproduktion kann überschüssige Wärme in Form von Sattdampf gespeichert und später genutzt werden, wenn die Nachfrage nach Energie steigt oder die Produktion schwankt. Diese Speichertechnologien tragen zur Stabilisierung von Energiesystemen bei und erhöhen die Flexibilität bei der Nutzung erneuerbarer Energiequellen.
Die Verwendung von Sattdampf ist auch entscheidend für die Effizienz von Dampfkraftwerken, die zu den ältesten und weit verbreitetsten Methoden der Stromerzeugung gehören. In solchen Kraftwerken wird Wasser in einem Boiler erhitzt, sodass es zu Sattdampf wird, der anschließend in einer Dampfturbine verwendet wird, um mechanische Energie in elektrische Energie umzuwandeln. Durch die Optimierung der Sättigungsbedingungen und den Einsatz moderner, hochentwickelter Dampfturbinen können Dampfkraftwerke eine hohe thermische Effizienz erreichen und somit einen größeren Anteil an der Energieproduktion liefern. Dies ist besonders relevant im Hinblick auf den globalen Bedarf an zuverlässiger und stabiler Energie.
Zusätzlich zu den klassischen Anwendungen zeigt sich ein wachsender Trend hin zu innovativen Lösungen, bei denen Sattdampf in Verbindung mit fortschrittlichen Technologien zur CO2-Abscheidung und -Speicherung eingesetzt wird. In solchen Systemen kann Sattdampf genutzt werden, um Abgase zu behandeln und CO2 aus industriellen Prozessen zu entfernen, wodurch die Umweltauswirkungen der Energieerzeugung reduziert werden. Diese Technologien könnten eine wichtige Rolle bei der Erreichung der Klimaziele spielen, da sie es ermöglichen, fossile Brennstoffe weiterhin zu nutzen, während gleichzeitig die Emissionen minimiert werden.
Die Weiterentwicklung von Mikroturbinen, die auf Sattdampf basieren, eröffnet neue Perspektiven für die dezentrale Energieversorgung. Mikrodampfturbinen können in kleinen, lokalen Energiesystemen eingesetzt werden, um sowohl Wärme als auch Strom zu erzeugen. Diese Turbinen sind besonders geeignet für industrielle Anwendungen, in denen hohe Mengen an Abwärme anfallen und Sattdampf effizient zur Stromerzeugung genutzt werden kann. Darüber hinaus bieten sie eine kostengünstige Lösung für die Energieversorgung in abgelegenen Gebieten oder in Situationen, in denen der Anschluss an ein zentralisiertes Stromnetz schwierig oder teuer ist.
Abschließend lässt sich sagen, dass Sattdampf eine sehr vielseitige und leistungsfähige Energiequelle ist, die in vielen Bereichen der Industrie und Energietechnik eine zentrale Rolle spielt. Die fortschreitende Entwicklung neuer Technologien und die verstärkte Integration erneuerbarer Energiequellen dürften die Anwendungsmöglichkeiten von Sattdampf in den kommenden Jahren weiter ausbauen. Sei es in großen Dampfkraftwerken, kleinen dezentralen Mikroturbinen oder in innovativen Wärmespeicher- und CO2-Reduktionssystemen – Sattdampf wird zweifellos auch in der Zukunft eine wichtige Rolle in der globalen Energieversorgung und der nachhaltigen Nutzung von Ressourcen spielen.
Sattdampf, auch als gesättigter Dampf bezeichnet, ist ein Zustand von Dampf, bei dem die Menge an Wärmeenergie, die der Dampf bei einer bestimmten Temperatur und einem bestimmten Druck enthalten kann, genau der maximalen Energiemenge entspricht, die der Dampf aufnehmen kann, ohne in einem weiteren Phasenübergang (z. B. Überhitzung) überzugehen. Sattdampf ist das Ergebnis des Verdampfungsprozesses von Wasser, bei dem es von der flüssigen Phase in die gasförmige Phase übergeht, ohne dabei die Temperatur oder den Druck zu verändern.
Definition von Sattdampf
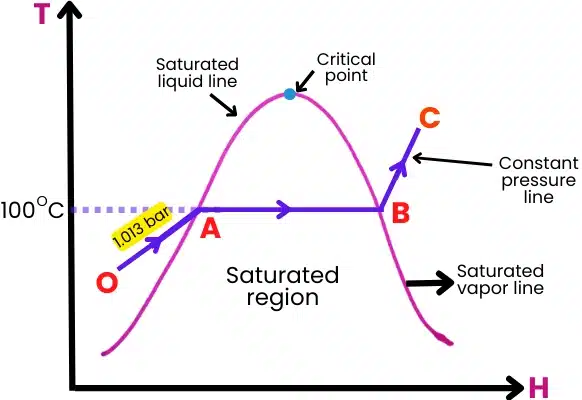
Sattdampf befindet sich auf der sogenannten Sättigungslinie in einem p-T-Diagramm (Druck-Temperatur-Diagramm). Auf dieser Linie existiert ein thermodynamisches Gleichgewicht zwischen der Flüssigkeit und ihrem Dampf. Das bedeutet, dass bei dieser Temperatur und diesem Druck der Dampf und das Wasser gleichzeitig existieren können. Sobald der Dampf auf der Sättigungslinie vorliegt, hat er die maximale Menge an Wärmeenergie aufgenommen, die er bei diesem Druck und dieser Temperatur aufnehmen kann.
In einem Zustand des Sattdampfs sind die Moleküle des Wassers in einem gasförmigen Zustand, aber sie sind in direktem Kontakt mit der Flüssigkeit, aus der sie verdampft sind. Ein weiteres wichtiges Merkmal von Sattdampf ist, dass er im Vergleich zu Unterkühltem Dampf oder Überhitztem Dampf nur so viel Energie enthält, wie notwendig ist, um den Phasenübergang zu vollziehen.
Eigenschaften von Sattdampf
- Temperatur und Druck: Sattdampf hat eine klare Beziehung zwischen Temperatur und Druck. Für jede Kombination von Temperatur und Druck existiert ein spezifischer Wert für den Sattdampf. Wenn man also den Druck kennt, kann man die Sättigungstemperatur ablesen. Diese Beziehung ist in Dampftabellen dokumentiert und wird in der Praxis oft verwendet, um den Zustand von Dampf in Dampfkraftwerken oder Heizsystemen zu analysieren.
- Enthalpie: Die Enthalpie von Sattdampf ist die Energiemenge, die der Dampf enthält. Diese Energiemenge setzt sich aus der spezifischen Verdampfungsenthalpie (die Energie, die benötigt wird, um eine Einheit Flüssigkeit in Dampf zu verwandeln) und der spezifischen Enthalpie des gesättigten Dampfes zusammen. Sattdampf enthält also nicht nur die Energie, die für den Phasenübergang erforderlich ist, sondern auch die zusätzliche Energie, die er als Dampf trägt.
- Volumen: Das Volumen von Sattdampf ist deutlich größer als das von Flüssigwasser. Dies liegt daran, dass die Moleküle im gasförmigen Zustand weiter voneinander entfernt sind. Das Volumen des Sattdampfs wird durch den spezifischen Gaszustand und die Temperatur bestimmt.
- Enthalpieunterschied zwischen Wasser und Dampf: Der Unterschied zwischen der Enthalpie von gesättigtem Wasser (Wasser bei Sättigungstemperatur) und gesättigtem Dampf (Dampf bei gleicher Temperatur) ist die Verdampfungsenthalpie. Diese zeigt die Energiemenge, die notwendig ist, um die Flüssigkeit vollständig in Dampf umzuwandeln.
Thermodynamische Grundlagen des Sattdampfs
Sattdampf wird häufig in thermodynamischen Systemen verwendet, um die Effizienz von Energieumwandlungsprozessen zu maximieren. In einem klassischen Dampfkraftwerk wird Sattdampf erzeugt, indem Wasser in einem Kessel erhitzt wird. Sobald der Wasserstoff den Sättigungszustand erreicht hat, wird er in eine Dampfturbine geleitet. In der Turbine expandiert der Dampf, und seine Temperatur und sein Druck sinken, wobei die Energie, die im Dampf gespeichert ist, in mechanische Arbeit umgewandelt wird.
Die Umwandlung von Wärmeenergie in mechanische Energie, bei der Sattdampf verwendet wird, beruht auf den Eigenschaften des Dampfes als Arbeitsmedium in der Turbine. Die Effizienz dieser Umwandlung ist eng mit der Qualität des Dampfes und seiner spezifischen Enthalpie verbunden.
Sattdampf in Dampfanlagen
In Dampfanlagen, insbesondere in Kraftwerken, spielt Sattdampf eine entscheidende Rolle in der Energieerzeugung. Der Prozess der Dampferzeugung beginnt mit der Erhitzung von Wasser, das dann in den Zustand des Sattdampfs übergeht. Sobald der Sattdampf erzeugt wird, wird er in Dampfturbinen eingesetzt, die mechanische Arbeit erzeugen. Der Sattdampf wird dabei durch Expansion in der Turbine abgekühlt, wobei die Wärmeenergie des Dampfes genutzt wird, um die Turbine anzutreiben. Diese Umwandlung von thermischer Energie in mechanische Energie ist ein zentraler Bestandteil der Stromerzeugung in Kraftwerken.
Das Verfahren, bei dem Sattdampf in Dampfturbinen genutzt wird, ist jedoch nur so effizient, wie die Temperatur- und Druckbedingungen des Dampfs. Ein System, das mit Sattdampf arbeitet, muss genau auf die richtigen Temperaturen und Drücke abgestimmt sein, um maximal effizient zu arbeiten. In der Praxis wird dies oft durch den Einsatz von Überhitzern erreicht, die den Dampf weiter erhitzen, um die thermodynamische Effizienz zu verbessern und das Entstehen von Kondensat zu vermeiden.
Anwendungen von Sattdampf
Sattdampf findet Anwendung in verschiedenen Industrien, darunter in der chemischen, petrochemischen und Lebensmittelindustrie. In der Lebensmittelverarbeitung wird Sattdampf häufig zur Sterilisation und Pasteurisierung von Produkten verwendet, da er eine konstante Temperatur aufrechterhält und so eine zuverlässige Wärmeübertragung gewährleistet.
In der petrochemischen Industrie wird Sattdampf für verschiedene Reaktionen und als Lösungsmittel in der chemischen Verarbeitung eingesetzt. Auch in der Papierindustrie wird Sattdampf genutzt, um den Trocknungsprozess zu beschleunigen und die Effizienz der Maschinen zu steigern.
Ein weiteres Beispiel ist die Nutzung von Sattdampf in Heizsystemen und Fernwärmesystemen. In diesen Systemen wird Sattdampf als Träger der Wärmeenergie verwendet, um große Mengen an Wärme über weite Entfernungen zu transportieren und so die Heizbedürfnisse von Gebäuden oder Industrieanlagen zu decken.
Fazit
Sattdampf ist eine fundamentale thermodynamische Größe, die eine Schlüsselrolle in der Energieerzeugung und in vielen industriellen Prozessen spielt. Als Arbeitsmedium in Dampfanlagen und in der chemischen Verarbeitung bietet Sattdampf eine effiziente Möglichkeit, Wärme und mechanische Arbeit zu übertragen. Die genaue Kontrolle und Nutzung von Sattdampf ermöglicht eine Optimierung der Energieerzeugung, sei es in großen Dampfkraftwerken oder in kleinen dezentralen Systemen. Angesichts der vielen praktischen Anwendungen und seiner zentralen Bedeutung in der Thermodynamik bleibt Sattdampf ein unverzichtbares Konzept für Ingenieure und Techniker in der gesamten Energiewirtschaft.
Sattdampf ist nicht nur für die Energieerzeugung in Dampfkraftwerken von Bedeutung, sondern hat auch eine wichtige Rolle in der Optimierung von Industriebetrieben und modernen Energieversorgungssystemen. Der Zustand des Sattdampfs, der in vielen Fällen als Träger von Wärmeenergie dient, macht ihn zu einem wesentlichen Bestandteil für effiziente thermische Prozesse. Besonders in Systemen, die auf die Nutzung von Abwärme angewiesen sind, kann Sattdampf als ideales Arbeitsmedium dienen, da er eine hohe Energiedichte aufweist und sich problemlos durch Rohre und Leitungen über große Entfernungen transportieren lässt.
In der praktischen Anwendung wird Sattdampf oft als Grundlage für sogenannte kombinierte Wärme- und Kraftsysteme (KWK) genutzt. Diese Systeme sind darauf ausgelegt, sowohl Strom als auch Wärme gleichzeitig zu erzeugen. Ein solcher Prozess maximiert die Nutzung der erzeugten Energie und trägt zu einer erheblichen Effizienzsteigerung bei. Sattdampf wird hier verwendet, um sowohl mechanische Energie in Form von Strom zu produzieren als auch überschüssige Wärme für industrielle Prozesse oder zur Fernwärmeversorgung bereitzustellen. In vielen modernen KWK-Anlagen wird dabei ein hoher Druck und eine hohe Temperatur des Sattdampfs aufrechterhalten, um die thermodynamische Effizienz des Systems zu maximieren. Insbesondere in großen städtischen Gebieten oder Industriekomplexen, die einen hohen Bedarf an sowohl Strom als auch Wärme haben, ist die Anwendung solcher Systeme von entscheidender Bedeutung.
Ein weiterer Bereich, in dem Sattdampf eine wichtige Rolle spielt, ist die dezentrale Energieerzeugung, bei der kleinere, lokal betriebene Dampfturbinen Mikrosysteme bilden. Diese Mikrosysteme, die unter anderem in Industrieanlagen oder abgelegenen Gebieten eingesetzt werden, können mit Sattdampf betrieben werden, der aus Biomasse, geothermischer Energie oder anderen erneuerbaren Quellen erzeugt wird. Durch die Nutzung von Sattdampf in solchen Systemen können lokale, nachhaltige Lösungen zur Energieversorgung bereitgestellt werden, die die Notwendigkeit für große, zentralisierte Kraftwerke verringern und den CO2-Ausstoß reduzieren. Die Flexibilität von Sattdampf als Energiequelle ermöglicht es, sowohl in großen, energieintensiven Industrieanlagen als auch in kleineren, auf spezifische Anwendungen zugeschnittenen Lösungen eine effiziente Nutzung von Energie zu gewährleisten.
In den letzten Jahren hat sich auch der Einsatz von Sattdampf zur CO2-Abscheidung und -Speicherung weiterentwickelt. Insbesondere in Kraftwerken, die weiterhin fossile Brennstoffe nutzen, wird Sattdampf verwendet, um Abgase zu behandeln und Kohlendioxid effizient zu extrahieren. Diese Technologien, die als “Carbon Capture and Storage” (CCS) bekannt sind, haben das Potenzial, die Umweltbelastung durch die Verbrennung fossiler Brennstoffe zu verringern, indem CO2 aus den Abgasen entfernt und sicher in geologischen Formationen unter der Erde gespeichert wird. Der Sattdampf hilft in diesem Prozess, indem er die Energie liefert, die für den Betrieb der Abscheideanlagen erforderlich ist, und gleichzeitig sicherstellt, dass die notwendigen thermodynamischen Bedingungen für die CO2-Abscheidung aufrechterhalten werden.
Sattdampf wird nicht nur zur Energieerzeugung und Wärmeübertragung genutzt, sondern spielt auch eine entscheidende Rolle in der Forschung und Entwicklung neuer Technologien. Durch die Untersuchung von Sattdampf und seiner Eigenschaften können Ingenieure und Forscher Wege finden, die Effizienz von Dampfsystemen zu verbessern und die Technologie der Wärmeübertragung weiter zu optimieren. In der thermodynamischen Forschung wird Sattdampf verwendet, um verschiedene Aspekte von Energieumwandlung und -speicherung zu analysieren. Dies umfasst sowohl die Untersuchung der Dynamik von Dampfströmen in Turbinen als auch die Entwicklung von neuen Materialien und Techniken, die die Leistung von Dampfanlagen weiter steigern können. Durch fortschrittliche Simulationstechniken und experimentelle Forschung können genauere Vorhersagen über das Verhalten von Sattdampf unter verschiedenen Betriebsbedingungen gemacht werden, was letztlich zu einer besseren Planung und einem effizienteren Betrieb von Dampfanlagen führt.
In der Industrie spielt Sattdampf auch eine entscheidende Rolle bei Prozessen, die eine gleichmäßige und kontrollierte Wärmeübertragung erfordern, wie etwa in der Lebensmittelverarbeitung. Der Einsatz von Sattdampf in der Sterilisation und Pasteurisierung von Lebensmitteln gewährleistet eine zuverlässige und gleichmäßige Erwärmung der Produkte, was zu einer besseren Produktqualität und einer längeren Haltbarkeit führt. Auch in der chemischen Industrie wird Sattdampf verwendet, um Reaktionen bei hohen Temperaturen zu ermöglichen, wobei die kontrollierte Zufuhr von Wärme entscheidend für den Erfolg der Reaktionen ist. In der Papierindustrie wird Sattdampf eingesetzt, um Trocknungsprozesse effizienter zu gestalten und den Energieverbrauch zu senken, während gleichzeitig die Produktionsgeschwindigkeit erhöht wird.
Ein weiteres innovatives Anwendungsgebiet für Sattdampf ist die Nutzung in der geothermischen Energieerzeugung. In geothermischen Kraftwerken wird Sattdampf direkt aus heißen geothermischen Quellen entnommen und in Dampfturbinen verwendet, um elektrische Energie zu erzeugen. Der Vorteil dieser Methode liegt darin, dass geothermische Energie eine erneuerbare und nahezu unerschöpfliche Energiequelle darstellt, die unabhängig von äußeren Wettereinflüssen zuverlässig Energie liefern kann. Durch die Kombination von geothermischer Energie und Sattdampf wird die Energiegewinnung umweltfreundlicher und nachhaltiger, da keine fossilen Brennstoffe benötigt werden und die Emissionen von Treibhausgasen minimiert werden.
Zusammenfassend lässt sich sagen, dass Sattdampf aufgrund seiner vielseitigen Eigenschaften in einer Vielzahl von Anwendungen in der Industrie und Energietechnik eine zentrale Rolle spielt. Von der effizienten Energieerzeugung in Dampfkraftwerken bis hin zur Nutzung erneuerbarer Energiequellen wie Geothermie und Biomasse bietet Sattdampf eine effektive und flexible Lösung für die Bedürfnisse der modernen Energieversorgung und industriellen Prozesse. Die kontinuierliche Forschung und Entwicklung in diesem Bereich wird dazu beitragen, die Nutzung von Sattdampf weiter zu optimieren und neue, umweltfreundlichere Technologien zu erschließen.
Ein bedeutender Aspekt der Zukunft von Sattdampf in der Energieerzeugung und -nutzung ist die Entwicklung sogenannter “Advanced Power Cycles”, die den Sattdampf auf eine noch effizientere Weise nutzen. In diesen innovativen Technologien wird der Dampf nicht nur in traditionellen Dampfturbinen verwendet, sondern auch in neuartigen Kombinationssystemen, die verschiedene thermodynamische Zyklen miteinander verbinden, um die Energieumwandlung zu optimieren. Hierbei wird Sattdampf als Medium genutzt, das in mehreren Stadien verarbeitet wird, um sowohl elektrische Energie als auch Wärme in verschiedenen Temperaturbereichen zu liefern. Diese fortschrittlichen Zyklen ermöglichen eine bessere Nutzung der Abwärme und tragen zu einer signifikanten Effizienzsteigerung bei, wodurch der Gesamtwirkungsgrad von Energieanlagen erhöht wird.
Ein besonders vielversprechendes Konzept, das mit Sattdampf in Verbindung steht, ist das sogenannte “Supercritical CO2 Power Cycle” (sCO2), das in den letzten Jahren zunehmend an Bedeutung gewonnen hat. In diesem innovativen Konzept wird anstelle von herkömmlichem Wasser als Arbeitsmedium überkritisches Kohlendioxid verwendet, das sich bei höheren Drücken und Temperaturen ähnlich wie Sattdampf verhält. Der Vorteil dieses Systems liegt in der höheren thermischen Effizienz und der besseren Fähigkeit, die Abwärme aus dem Dampferzeugungsprozess zu nutzen. Da sCO2 bei höheren Temperaturen und Drücken effizient arbeitet, können Anlagen mit diesem System potenziell kleineren und kostengünstigeren Anlagen betrieben werden, die gleichzeitig weniger Material erfordern und geringere Betriebskosten verursachen. Obwohl das sCO2-System noch in der Entwicklung ist, könnte es eine bahnbrechende Technologie für die zukünftige Nutzung von Sattdampf und anderen Hochtemperatur-Dampfprozessen darstellen.
Ein weiterer Fortschritt in der Dampftechnologie ist die zunehmende Nutzung von Sattdampf in sogenannten hybriden Energieerzeugungsanlagen, bei denen erneuerbare Energien wie Solarenergie oder Windenergie mit traditionellen thermischen Prozessen kombiniert werden. In diesen Systemen wird überschüssige Energie aus erneuerbaren Quellen in Form von Wärme gespeichert und in Form von Sattdampf für die Stromerzeugung genutzt, wenn die Nachfrage nach Energie steigt oder die erneuerbare Energieproduktion schwankt. Diese Hybridlösungen bieten eine flexible Möglichkeit, die Nutzung erneuerbarer Energien zu maximieren, indem sie die Integration von Sattdampf mit den vorhandenen Dampfsystemen optimieren.
Neben der Rolle von Sattdampf in der Energieerzeugung wird seine Anwendung auch in der Industrie durch die Integration fortschrittlicher Überwachungssysteme und digitaler Technologien weiter verbessert. In modernen Dampfanlagen werden zunehmend digitale Zwillingsmodelle und Echtzeit-Überwachung eingesetzt, um den Zustand des Sattdampfs und anderer Betriebsparameter ständig zu analysieren. Diese Systeme ermöglichen eine präzisere Steuerung der Dampfturbinen und erhöhen die Flexibilität der Anlagen. Durch die Nutzung von Daten aus Sensoren und fortschrittlichen Algorithmen können Anlagenbetreiber sofort auf Änderungen im Betrieb reagieren und Maßnahmen zur Effizienzsteigerung oder Fehlerbehebung ergreifen, noch bevor Probleme auftreten. Diese Technologien bieten nicht nur eine höhere betriebliche Effizienz, sondern tragen auch zur Reduzierung von Ausfallzeiten und Wartungskosten bei.
Sattdampf wird in vielen industriellen Prozessen nicht nur als reine Energiequelle verwendet, sondern auch als Mittel zur Verbesserung der Produktqualität. Besonders in der Lebensmittelindustrie, der Pharmaindustrie und der Textilindustrie ist die präzise Kontrolle von Temperatur und Feuchtigkeit durch Sattdampf entscheidend für die Herstellung hochwertiger Produkte. In der Lebensmittelverarbeitung wird Sattdampf beispielsweise verwendet, um Produkte durch Dampfsterilisation oder Pasteurisierung zu konservieren. Diese Verfahren ermöglichen es, die Haltbarkeit von Lebensmitteln zu verlängern, ohne den Nährwert zu beeinträchtigen. In der Textilindustrie wird Sattdampf genutzt, um Fasern zu behandeln und Stoffe zu glätten oder zu färben. Auch in der chemischen Industrie wird Sattdampf verwendet, um Reaktionen bei kontrollierten Temperaturen zu ermöglichen, die für bestimmte Prozesse erforderlich sind.
Ein weiteres Beispiel für die fortschreitende Nutzung von Sattdampf ist die Kombination von Dampftechnologie mit CO2-Abscheidung und -Speicherung (CCS). Diese Technologie wird zunehmend als eine der vielversprechendsten Lösungen zur Reduzierung von CO2-Emissionen in der Energieerzeugung betrachtet. Sattdampf wird in den CO2-Abscheideanlagen eingesetzt, um den Prozess zu unterstützen und sicherzustellen, dass die benötigte thermische Energie effizient genutzt wird. Diese Integration von Sattdampf in CO2-Managementsysteme hilft nicht nur, die Emissionen zu verringern, sondern auch, die Effizienz der gesamten Anlage zu steigern, indem Abwärme aus den CO2-Abscheidungsprozessen genutzt wird.
Zusätzlich zu diesen technologischen Entwicklungen wird auch die Forschung an Sattdampf unter extremen Bedingungen weitergeführt. Ein Bereich, in dem dies von Bedeutung ist, ist die Entwicklung von Dampfturbinen und anderen Dampfsystemen, die unter besonders hohen Drücken und Temperaturen arbeiten, wie sie in der Kerntechnik oder in geothermischen Kraftwerken vorkommen. Die Verbesserung der Materialien und Turbinentechnologie, die für solche Anwendungen erforderlich sind, könnte die Effizienz von Dampfsystemen erheblich steigern und die Nutzung von Sattdampf als thermisches Arbeitsmedium noch weiter ausbauen.
Zusammengefasst lässt sich sagen, dass Sattdampf in der Energieerzeugung und in industriellen Prozessen weiterhin eine zentrale Rolle spielt. Seine vielseitige Anwendung in der Stromerzeugung, in industriellen Heizsystemen, in der CO2-Abscheidung sowie in neuen, fortschrittlichen Technologien zeigt, dass die Bedeutung von Sattdampf auch in der Zukunft nicht nur bestehen bleibt, sondern noch weiter wachsen wird. Die kontinuierliche Verbesserung der Effizienz und Integration von Sattdampf in neue Systeme und die zunehmende Nutzung digitaler Technologien zur Überwachung und Steuerung von Dampfanlagen werden dazu beitragen, die Energieproduktion und industrielle Prozesse noch ressourcenschonender und nachhaltiger zu gestalten.
Ein weiteres spannendes Thema, das mit der Nutzung von Sattdampf zusammenhängt, ist die zunehmende Implementierung von Energieeffizienz- und Nachhaltigkeitsstrategien in bestehenden Dampfanlagen. Insbesondere in Industrien, die große Mengen an Dampf benötigen, wie die Chemie-, Lebensmittel-, Papier- und Textilindustrie, wird zunehmend darauf geachtet, den Energieverbrauch zu optimieren. Hier kommen moderne Regelungstechnik und thermische Energiespeicher ins Spiel. Die Kombination von Sattdampf mit thermischen Energiespeichern ermöglicht es, überschüssige Wärme, die während weniger intensiver Produktionszeiten erzeugt wird, zu speichern und zu einem späteren Zeitpunkt zu nutzen, wenn die Nachfrage nach Wärme steigt. Diese Speicherung von Wärmeenergie hilft nicht nur, den Gesamtenergieverbrauch zu reduzieren, sondern auch, die Effizienz von Dampfsystemen zu maximieren.
In kraftwerkstechnischen Anwendungen ist die Entwicklung von modularen und flexiblen Dampfkraftwerken ein weiteres Beispiel für die fortschreitende Nutzung von Sattdampf. Hierbei wird nicht nur die Energieerzeugung verbessert, sondern auch die Möglichkeit eröffnet, solche Anlagen schneller und kostengünstiger zu errichten. Diese modularen Kraftwerke sind besonders in abgelegenen oder sich schnell entwickelnden Regionen von Interesse, da sie relativ einfach an lokale Bedürfnisse angepasst werden können. Der modulare Ansatz ermöglicht es, die Dampfturbinen und den Sattdampf effizient in verschiedenen Leistungsbereichen zu betreiben, was die Anpassungsfähigkeit der gesamten Energieerzeugung verbessert.
Zusätzlich zur Flexibilität in der Stromerzeugung bieten modulare Dampfanlagen auch Vorteile im Hinblick auf die Integration von erneuerbaren Energiequellen. In Kombination mit solarthermischen Anlagen kann Sattdampf als thermisches Speichermedium dienen, das die durch Sonnenkollektoren erzeugte Wärme speichert und bei Bedarf wieder in Dampf umwandelt. Diese Technologie verbessert nicht nur die Ausnutzung von Solarenergie, sondern hilft auch, die intermittierenden Produktionszeiten der Solarenergie zu überbrücken, wenn die Sonne nicht scheint. Ein solches System erhöht die Gesamtleistung und Zuverlässigkeit von Solarenergieanlagen und trägt zur Optimierung von Sattdampf-basierten Kraftwerken bei.
Ein weiterer Bereich, in dem Sattdampf zunehmend eine Rolle spielt, ist die Wärme- und Kältespeicherung. Insbesondere in der Kältetechnologie sind innovative Anwendungen von Sattdampf relevant, wenn es darum geht, Wärmepumpen und Kältemaschinen mit thermischen Dampfspeichern zu kombinieren. In modernen Kombikraftwerken oder in der Fernwärmeversorgung wird Sattdampf als das ideale Medium verwendet, um überschüssige Wärme für den späteren Gebrauch zu speichern. In diesen Systemen wird der Sattdampf zur Wärmeübertragung in Fernwärmenetze eingesetzt, wo er eine konstante und verlässliche Wärmequelle für Haushalte und Unternehmen bietet. Solche Anwendungen sind besonders in urbanen Zentren oder in großen Industriekomplexen von Vorteil, die konstanten Wärmebedarf haben und die Energieeffizienz maximieren wollen.
Die Kombination von Sattdampf mit modernen digitale Steuerungssystemen bietet außerdem enorme Potenziale für die Optimierung des Betriebs von Dampfanlagen. Digitale Zwillinge, die den Zustand von Dampfsystemen in Echtzeit simulieren, ermöglichen es den Betreibern, präzisere Vorhersagen über den zukünftigen Energiebedarf zu treffen und entsprechende Anpassungen vorzunehmen. Diese Technologie nutzt Daten aus einer Vielzahl von Sensoren, um Betriebsparameter wie Druck, Temperatur und Enthalpie des Sattdampfes kontinuierlich zu überwachen. So lassen sich Ineffizienzen schnell identifizieren und Anpassungen vornehmen, die den Gesamtbetrieb der Dampfanlage effizienter und kostengünstiger gestalten. Diese Echtzeit-Datenanalyse und -optimierung führt zu einer verbesserten Lebensdauer der Dampfanlagen und zu erheblichen Einsparungen bei den Betriebskosten.
In Bezug auf nachhaltige Entwicklung und den Übergang zu einer klimafreundlicheren Energieerzeugung stellt der Einsatz von Sattdampf auch im Rahmen von Kreisprozessen und Kreislaufwirtschaft eine vielversprechende Möglichkeit dar. Durch die Rückführung von Sattdampf in geschlossene Systeme, in denen der Dampf nach der Energieabgabe kondensiert und wieder in den Dampferzeugungsprozess eingespeist wird, kann der Gesamtenergieverbrauch erheblich gesenkt werden. Solche Kreislaufsysteme helfen, die Ressourcennutzung zu minimieren und die Energieverluste zu reduzieren. In einem idealen Kreislaufsystem würde nahezu die gesamte erzeugte Energie wiederverwendet werden, wodurch der Bedarf an primären Energiequellen sinkt.
Die Integration von Sattdampf in verteilte Energiesysteme stellt ebenfalls eine wichtige Innovation dar. In Regionen, die nicht an zentrale Energieversorgungsnetze angeschlossen sind, können kleine, modulare Dampfanlagen, die mit erneuerbaren Energiequellen wie Biomasse, Geothermie oder Solarthermie betrieben werden, genutzt werden, um die lokale Energieversorgung zu sichern. Diese kleineren Systeme, die mit Sattdampf betrieben werden, können nicht nur Strom, sondern auch Wärme für Haushalte oder Industrien liefern, wodurch sie eine ganzheitliche Lösung für die lokale Energieversorgung bieten.
Ein weiteres interessantes Feld ist die Entwicklung von hybriden Energiesystemen, bei denen Sattdampf mit anderen Technologien kombiniert wird, um eine nachhaltigere und stabilere Energieversorgung zu gewährleisten. In solchen Systemen könnte beispielsweise Sattdampf als “Puffer” für Strom aus erneuerbaren Quellen wie Wind oder Sonne dienen, um Zeiten niedriger Produktion zu überbrücken. Diese Art von Systemen könnte in Zukunft eine wichtige Rolle spielen, wenn es darum geht, den Anteil erneuerbarer Energien am globalen Energiemix weiter zu erhöhen, ohne dass es zu einer Instabilität im Stromnetz kommt.
Ein besonders wachsendes Anwendungsgebiet für Sattdampf ist die Integration in moderne Wasseraufbereitungsprozesse. Sattdampf wird in der Entsalzung von Meerwasser oder in der Wasseraufbereitung für industrielle Anwendungen zunehmend verwendet, um Wasser mit hoher Effizienz zu erzeugen. Dieser Prozess nutzt den hohen Druck und die Temperatur des Sattdampfes, um Verunreinigungen im Wasser zu verdampfen und so sauberes Wasser zu gewinnen. Solche Technologien sind besonders in Regionen von Interesse, die unter Wasserknappheit leiden und gleichzeitig Zugang zu Küstengebieten oder anderen Wasservorkommen haben, die entsalzt werden können.
Zusammengefasst zeigt sich, dass die kontinuierliche Entwicklung von Sattdampftechnologien ein bedeutendes Potenzial für die Zukunft der Energieerzeugung und -nutzung bietet. Ob in der verbesserten Integration von erneuerbaren Energien, der Optimierung von Dampfanlagen oder der Schaffung nachhaltiger Kreislaufsysteme, die effiziente Nutzung von Sattdampf trägt maßgeblich dazu bei, den weltweiten Energieverbrauch zu senken, die CO2-Emissionen zu reduzieren und eine nachhaltigere und umweltfreundlichere Energiezukunft zu schaffen.
Dampfturbine Schiff

Dampfturbinen auf Schiffen haben eine lange Geschichte und sind nach wie vor in einigen modernen Schiffen und großen Handelsschiffen zu finden. Sie spielen eine entscheidende Rolle in der Schiffsantriebstechnik, insbesondere bei größeren Schiffen wie Passagierschiffen, Frachtern, Kriegsschiffen und Ölplattformen. Dampfturbinen bieten eine hohe Leistung bei vergleichsweise geringem Gewicht und ermöglichen eine hohe Geschwindigkeit sowie einen effizienten Betrieb auf langen Strecken. Die Anwendung von Dampfturbinen auf Schiffen hat sich im Laufe der Jahre weiterentwickelt, und sie sind auch heute noch eine wichtige Technologie, insbesondere in bestimmten Schiffsklassen.
Funktionsweise der Dampfturbine im Schiffsbetrieb
Die Dampfturbine auf einem Schiff funktioniert grundsätzlich ähnlich wie in landbasierten Kraftwerken, jedoch angepasst an die spezifischen Anforderungen von Schiffen. Der Dampfantrieb umfasst mehrere wesentliche Schritte:
- Erzeugung von Dampf: Der Brennstoff (meist Öl oder Gas) wird in einem Kessel verbrannt, um Wasser zu erhitzen und Dampf zu erzeugen. In modernen Schiffen werden oft Kombikessel verwendet, die sowohl für die Dampferzeugung für die Turbine als auch für andere Wärmeanwendungen wie Heizung und Klimaanlage des Schiffes genutzt werden können.
- Dampf in der Turbine: Der erzeugte Sattdampf wird unter hohem Druck und hoher Temperatur in die Dampfturbine geleitet. Der Dampf strömt auf die Turbinenschaufeln und bringt die Turbine zum Drehen. Die mechanische Energie, die durch die Turbine erzeugt wird, wird dann über eine Welle auf den Propeller des Schiffes übertragen, was die Schiffsbewegung antreibt.
- Dampfexpansion: Der Dampf durchläuft in der Dampfturbine mehrere Stadien, in denen er expandiert und dabei seine Energie an die Schaufeln der Turbine abgibt. Diese Expansion von Dampf ermöglicht eine sehr effiziente Umwandlung von Wärmeenergie in mechanische Energie.
- Kondensation: Nach der Expansion des Dampfes wird der Dampf in einem Kondensator abgekühlt und kondensiert wieder zu Wasser. Dieses Wasser wird dann in den Kessel zurückgeführt, um den Kreislauf zu schließen und den Prozess zu wiederholen.
Vorteile der Dampfturbinen auf Schiffen
Dampfturbinen bieten einige wesentliche Vorteile, die sie besonders für große Schiffe attraktiv machen:
- Hohe Leistungsdichte: Dampfturbinen bieten eine hohe Leistung in Relation zum Gewicht, was für den Schiffsverkehr wichtig ist. Besonders bei großen Schiffen, die über weite Strecken hinweg hohe Geschwindigkeiten erreichen müssen, sind Dampfturbinen von Vorteil.
- Zuverlässigkeit: Dampfturbinen sind in der Regel sehr robust und zuverlässig. Sie können über lange Zeiträume ohne größere Wartung laufen, was sie ideal für den Einsatz auf Schiffen macht, die oft mehrere Wochen oder Monate auf See sind.
- Energieeffizienz: Dampfturbinen können sehr effizient arbeiten, insbesondere in großen Systemen wie denen, die auf Passagier- oder Frachtschiffen verwendet werden. Sie können große Mengen an Energie aus relativ kleinen Brennstoffmengen erzeugen.
- Flexibilität im Betrieb: Dampfturbinen können verschiedene Brennstoffe nutzen, was sie für verschiedene Schiffstypen attraktiv macht, insbesondere wenn alternative Brennstoffe wie LNG oder Biomasse verwendet werden.
Herausforderungen und Entwicklung
Trotz ihrer Vorteile haben Dampfturbinen auf Schiffen auch einige Herausforderungen:
- Komplexität und Kosten: Dampfturbinen und ihre zugehörigen Systeme, wie Kessel und Kondensatoren, sind technisch anspruchsvoll und können teuer in der Herstellung und Wartung sein. Zudem erfordern sie eine qualifizierte Crew, die mit dem Betrieb der Turbinen und der Überwachung des Dampfkessels vertraut ist.
- Brennstoffverbrauch: Dampfturbinen erfordern einen konstanten und stabilen Brennstofffluss, um effizient arbeiten zu können. In modernen Schiffen, die häufig auf erneuerbare Energien oder gasbetriebene Motoren umstellen, kann der Brennstoffverbrauch der Dampfturbinen ein Faktor sein, der den Betriebskosten und der Emissionsbilanz des Schiffs beeinflusst.
- Platzbedarf: Dampfturbinen und Kessel benötigen einen relativ großen Raum, was bei der Planung und Konstruktion von Schiffen berücksichtigt werden muss. Daher sind Dampfturbinen vor allem auf größeren Schiffen vorteilhaft, bei denen der Platzbedarf für die Antriebstechnik weniger kritisch ist.
Moderne Anwendungen
Trotz der Einführung von Dieselmotoren und Gasturbinen in der Schiffsindustrie sind Dampfturbinen immer noch auf vielen großen Schiffen in Betrieb, insbesondere bei Flugzeugträgern und großen Passagierschiffen. Ein prominentes Beispiel sind die Queen Elizabeth 2 und andere Luxusliner, die in der Vergangenheit Dampfturbinen für ihre Antriebsmechanismen verwendeten. Dampfturbinen werden auch in Flugzeugträgern der Marine eingesetzt, da sie eine hohe Zuverlässigkeit und Energieeffizienz bieten, die für militärische Anwendungen entscheidend sind.
In Kombination mit Gasturbinen kommen Dampfturbinen zunehmend in Kombinierten Dampfturbinen-Gasturbinen-Anlagen (Combined Cycle) zum Einsatz. Diese Systeme kombinieren die Vorteile der Dampfturbine mit denen der Gasturbine, was zu einer deutlich höheren Gesamtleistung und Effizienz führt. In einigen modernen Schiffsdesigns werden solche kombinierten Zyklen verwendet, um sowohl den mechanischen Antrieb als auch die Stromerzeugung für den Schiffsbetrieb zu optimieren.
Fazit
Die Dampfturbine bleibt ein leistungsstarker Antrieb in der Schiffsindustrie, vor allem auf großen Schiffen, die eine hohe Leistung und Zuverlässigkeit erfordern. Während moderne Alternativen wie Gasturbinen und Dieselmotoren in vielen Bereichen populärer geworden sind, bleibt die Dampfturbine aufgrund ihrer Effizienz, ihrer Fähigkeit zur Nutzung verschiedener Brennstoffe und ihrer langen Tradition in der Schiffsindustrie ein wichtiger Bestandteil des Schiffsantriebs. Die kontinuierliche Weiterentwicklung in der Dampfturbinen- und Kesseltechnologie trägt dazu bei, diese Technologie auch im 21. Jahrhundert zu einer zukunftsfähigen Lösung für den Schiffsverkehr zu machen.
Ein weiterer wichtiger Bereich, in dem Dampfturbinen auf Schiffen immer relevanter werden, ist die Integration von Umwelt- und Emissionsvorgaben. Im Zuge der zunehmenden Regulierung von Emissionen im maritimen Sektor, wie den Vorgaben der International Maritime Organization (IMO) und den nationalen Umweltvorschriften, sind Schiffsbetreiber gezwungen, die Emissionen von Schiffen zu minimieren und die Energieeffizienz zu verbessern. Dampfturbinen können dabei durch den Einsatz von LNG (Flüssigerdgas) oder anderen weniger emissionsintensiven Brennstoffen in Kombination mit modernen CO2-Abscheidungstechnologien zur Verringerung von Treibhausgasemissionen beitragen.
Verwendung von alternativen Brennstoffen und CO2-Reduktion
Da Dampfturbinen relativ flexibel in Bezug auf den Brennstoff sind, werden zunehmend umweltfreundliche Brennstoffe wie LNG, Wasserstoff oder Bioöl als Alternativen zum herkömmlichen Schweröl und Diesel in Betracht gezogen. LNG hat sich besonders in der Schifffahrt als attraktiver Brennstoff etabliert, da er im Vergleich zu herkömmlichen Schweröl- und Dieselbrennstoffen deutlich weniger CO2, Stickoxide (NOx) und Schwefeloxide (SOx) emittiert. In Kombination mit Dampfturbinen bieten diese Brennstoffe eine Möglichkeit, den CO2-Ausstoß und die Luftverschmutzung im Schiffsverkehr erheblich zu reduzieren.
Darüber hinaus wird an der Entwicklung von CO2-Abscheidungssystemen gearbeitet, die zusammen mit Dampfturbinen auf Schiffen eingesetzt werden könnten. Diese Systeme fangen das CO2, das bei der Verbrennung von Brennstoffen entsteht, ab und speichern es sicher, um die Treibhausgasemissionen zu verringern. Solche Technologien sind noch in der Entwicklungsphase, aber sie könnten in Zukunft eine wichtige Rolle dabei spielen, den ökologischen Fußabdruck der Schifffahrt weiter zu verringern.
Nutzung von Abwärme – Dampfturbinen und die Kreislaufwirtschaft
Die Abwärme von Dampfturbinen ist ein weiteres Thema, das zunehmend an Bedeutung gewinnt. Schiffe, die mit Dampfturbinen betrieben werden, erzeugen eine erhebliche Menge an Abwärme, die oft nicht optimal genutzt wird. In der Vergangenheit wurde diese Abwärme in vielen Fällen einfach durch Kühlsysteme abgeführt, was einen ineffizienten Einsatz von Energie zur Folge hatte.
In modernen Dampfturbinenantrieben wird jedoch zunehmend auf die Wärmerückgewinnung gesetzt. Dabei wird die Abwärme der Dampfturbine nicht einfach abgeführt, sondern in einem Wärmetauscher zurückgewonnen und in andere Prozesse auf dem Schiff integriert. Zum Beispiel kann die Rückgewinnung von Abwärme verwendet werden, um Klimaanlagen, Kochsysteme oder Entsalzungsanlagen zu betreiben. In einigen modernen Schiffen wird sogar die Abwärme der Turbine verwendet, um zusätzlich Strom zu erzeugen und so die Effizienz der Dampfturbine zu steigern.
Diese Kreislaufwirtschaftsansätze, bei denen die Abwärme als Ressource betrachtet wird, tragen nicht nur zur Effizienzsteigerung bei, sondern auch zur Verringerung des Brennstoffverbrauchs und der CO2-Emissionen. Durch die Implementierung dieser Technologien wird die Gesamtenergieeffizienz des Schiffs erhöht, und gleichzeitig wird weniger Energie für sekundäre Systeme wie Kühlung und Klimatisierung benötigt.
Hybridisierung von Dampfturbinen mit Gasturbinen
Ein weiteres innovatives Konzept, das in der Schifffahrt immer mehr Anwendung findet, ist die Hybridisierung von Dampfturbinen mit Gasturbinen. Diese Kombination, auch als Combined Cycle bezeichnet, nutzt sowohl die Vorteile der Dampfturbine als auch die der Gasturbine, um eine noch höhere Gesamtenergieeffizienz zu erzielen.
Gasturbinen haben eine höhere Effizienz bei hohen Drehzahlen und können sehr schnell auf Veränderungen in der Leistung reagieren, was sie ideal für Schiffe macht, die auf schnelle Geschwindigkeitsänderungen angewiesen sind, wie etwa Militärschiffe oder Passagierfähren. Dampfturbinen hingegen bieten eine konstante und zuverlässige Energiequelle bei längeren Fahrten, insbesondere bei konstanten Reisegeschwindigkeiten.
Durch die Kombination beider Technologien können Schiffe die Vorteile beider Systeme nutzen: Die Gasturbine kann in Situationen eingesetzt werden, in denen schnelle Anpassungen erforderlich sind, während die Dampfturbine für konstanten, effizienten Betrieb bei längeren Fahrten sorgt. Diese Hybridisierungstechnologien tragen dazu bei, den Brennstoffverbrauch zu optimieren und die CO2-Emissionen zu minimieren, während gleichzeitig die Gesamtleistung und Zuverlässigkeit des Schiffes verbessert werden.
Zukunftsperspektiven für Dampfturbinen in der Schifffahrt
Mit Blick auf die Zukunft wird erwartet, dass Dampfturbinen auf Schiffen weiterhin eine Rolle spielen, insbesondere bei großen und hochspezialisierten Schiffen. Die kontinuierliche Weiterentwicklung der Dampfturbinen- und Kesseltechnologien, insbesondere durch den Einsatz von fortschrittlichen Materialien und intelligente Steuerungssysteme, wird dazu beitragen, die Effizienz weiter zu steigern und die Wartungskosten zu senken.
Zudem könnten Dampfturbinen in verteilten Energieversorgungssystemen auf Schiffen eine zunehmend wichtige Rolle spielen, insbesondere bei der Integration von erneuerbaren Energien wie Wind- und Solarenergie. Die Nutzung dieser erneuerbaren Energien in Kombination mit Dampfturbinen könnte helfen, den gesamten Energiebedarf von Schiffen nachhaltiger zu gestalten.
Ein weiterer vielversprechender Bereich ist die Entwicklung von vollautomatischen Dampfturbinenanlagen, bei denen die Überwachung und Steuerung der Dampfanlage durch fortschrittliche IoT-Technologien und KI-basierte Algorithmen erfolgt. Diese Systeme könnten nicht nur die Effizienz verbessern, sondern auch dazu beitragen, den Betrieb sicherer zu gestalten, indem sie frühzeitig auf potenzielle Probleme hinweisen und Wartungsbedarf erkennen, bevor größere Ausfälle auftreten.
Fazit
Obwohl die Dampfturbine auf Schiffen nicht mehr die einzige Antriebstechnologie ist, hat sie sich aufgrund ihrer Effizienz, Zuverlässigkeit und Flexibilität auch in modernen Schiffsdesigns als wertvolle Antriebslösung etabliert. Die kontinuierliche Weiterentwicklung der Dampfturbinen- und Kesseltechnologien, gepaart mit der Integration von erneuerbaren Energiequellen, CO2-Reduktionstechnologien und Abwärmerückgewinnung, wird dafür sorgen, dass Dampfturbinen auch in Zukunft eine zentrale Rolle in der Schifffahrt spielen. Insbesondere auf großen Schiffen, bei denen eine hohe Leistung, Zuverlässigkeit und Effizienz erforderlich sind, wird die Dampfturbine weiterhin eine der bevorzugten Antriebstechnologien bleiben.
In der Schifffahrt bieten Dampfturbinen auch eine wertvolle Möglichkeit zur Verbesserung der Energieversorgung und des Brennstoffmanagements. Eine der größten Herausforderungen in der modernen Schifffahrt ist die ständige Notwendigkeit, Brennstoffeffizienz zu maximieren und gleichzeitig den CO2-Ausstoß zu minimieren. Der Einsatz von Dampfturbinen in kombinierten Energiesystemen, bei denen diese mit anderen Technologien wie Gasturbinen oder Elektromotoren kombiniert werden, ermöglicht es Schiffen, ihre Energiequellen dynamisch anzupassen und so den Brennstoffverbrauch und die Emissionen zu optimieren. Solche hybriden Systeme sorgen für eine bessere Lastverlagerung, sodass je nach Betriebsbedingungen entweder die Dampfturbine oder eine alternative Antriebsquelle den größten Teil der benötigten Energie liefert.
Ein weiterer Aspekt, der in den letzten Jahren zunehmend an Bedeutung gewonnen hat, ist die Frage nach alternativen Antriebstechnologien wie elektrischen Antrieben oder Brennstoffzellen, die ebenfalls für den Schiffsverkehr relevant werden. In bestimmten Anwendungen, vor allem bei kürzeren Reisen und Nischenanwendungen, können diese Technologien eine Möglichkeit darstellen, den Betrieb von Dampfturbinen zu ergänzen oder sogar zu ersetzen. Dennoch bleibt die Dampfturbine aufgrund ihrer hohen Leistungsdichte und ihrer Fähigkeit, große Schiffsgrößen zuverlässig anzutreiben, nach wie vor eine der bevorzugten Lösungen für Langstreckenfahrten und für Schiffe, die hohe Geschwindigkeiten erreichen müssen, wie etwa Kreuzfahrtschiffe oder Flugzeugträger.
Auch die Wartungsstrategien und die Lebensdauer von Dampfturbinen spielen eine wichtige Rolle im Schiffsbetrieb. Die technologische Weiterentwicklung von Wartungssoftware und Fehlerdiagnosesystemen ermöglicht eine präzisere Fehlererkennung und Frühwarnsysteme, die helfen, den Betrieb der Dampfturbinen effizient zu überwachen und unvorhergesehene Ausfälle zu verhindern. In Kombination mit der Digitalisierung und der Integration von IoT-Technologien auf Schiffen können Daten in Echtzeit gesammelt und analysiert werden, um präventive Wartungsmaßnahmen zu ergreifen und die Lebensdauer der Anlagen zu verlängern. Die smartphone-gestützte Wartung und die Integration von AI-Algorithmen für die Überwachung von Dampfturbinen und zugehörigen Systemen verbessern die Betriebsabläufe und helfen dabei, Stillstandzeiten zu minimieren.
Im Hinblick auf die Zukunft der Dampfturbinen auf Schiffen könnte die Technologie weiterhin eine bedeutende Rolle spielen, insbesondere in Bezug auf den globalen Trend zu nachhaltiger Schifffahrt. Die Umstellung auf grünere Brennstoffe wie Bio-Diesel, LNG oder Wasserstoff bietet Potenzial, den CO2-Ausstoß der Dampfturbinen weiter zu reduzieren und die Umweltbelastung zu minimieren. Gleichzeitig wird erwartet, dass der technologische Fortschritt die Wartungskosten und Betriebszeit weiter senken wird, was die Wettbewerbsfähigkeit von Dampfturbinen im Vergleich zu anderen Antriebssystemen stärken könnte.
Der integrierte Einsatz von Dampfturbinen mit anderen fortschrittlichen Energiesystemen wie Wärmespeichertechnologien oder Windkraftantrieben könnte langfristig eine Lösung sein, die Brennstoffverbrauch und Emissionswerte weiter reduziert, während gleichzeitig die Effizienz und die Leistung von Schiffen gesteigert werden. Solche Konzepte, die auf Erneuerbaren und intelligenter Energienutzung basieren, könnten die Schifffahrt noch nachhaltiger gestalten und gleichzeitig den Bedürfnissen nach globaler Mobilität und Transport gerecht werden.
Zusammenfassend lässt sich sagen, dass die Dampfturbine, obwohl sie nicht die einzige Lösung in der modernen Schifffahrt ist, nach wie vor eine wichtige Technologie darstellt. Ihre hohe Effizienz, Zuverlässigkeit und Flexibilität machen sie zu einem unersetzlichen Teil der Schiffsantriebstechnologie, insbesondere bei großen, leistungsstarken Schiffen. Die kontinuierliche Innovation in Bezug auf Brennstoffe, Hybridtechnologien und Wärmerückgewinnung stellt sicher, dass Dampfturbinen auch in Zukunft eine bedeutende Rolle in der Schifffahrt spielen werden, während die Branche gleichzeitig auf eine zunehmend nachhaltigere und umweltfreundlichere Zukunft hin arbeitet.
Ein weiterer wichtiger Aspekt für die Zukunft der Dampfturbinen auf Schiffen ist die Zunahme der Automatisierung und der intelligente Betrieb. Mit dem Fortschritt in der digitalen Technologie und der Industrie 4.0 ist es zunehmend möglich, Dampfturbinenanlagen mit hochentwickelten automatischen Steuerungs- und Überwachungssystemen auszustatten. Diese Systeme nutzen Künstliche Intelligenz (KI), Maschinelles Lernen (ML) und Big Data, um den Betrieb der Dampfturbinen zu optimieren und sofortige Anpassungen an sich ändernde Betriebsbedingungen vorzunehmen. So können Systeme die Leistung der Dampfturbine in Echtzeit überwachen, Effizienzverluste identifizieren und sofortige Anpassungen an den Betriebsparametern vornehmen, um den Brennstoffverbrauch und die Emissionen zu minimieren.
Diese intelligente Automatisierung ermöglicht es auch, den Wartungsbedarf genauer zu prognostizieren und vorherzusagen. So werden Wartungsarbeiten und Reparaturen nicht mehr nach festen Zeitintervallen, sondern basierend auf der tatsächlichen Leistung und dem Zustand der Turbine durchgeführt. Dies verbessert die Kostenkontrolle und reduziert den Risiko eines plötzlichen Ausfalls, was besonders in der Schifffahrt, wo Ausfallzeiten enorme Kosten verursachen können, von entscheidender Bedeutung ist.
Durch die **Verbindung von Dampfturbinen mit umfassenden Überwachungssystemen können die Lebenszykluskosten gesenkt und die Effizienz des gesamten Schiffsbetriebs gesteigert werden. Ein Beispiel für eine solche Technologie ist der Einsatz von vorausschauender Wartung, bei der über Sensoren und Datenanalyse potenzielle Probleme in der Dampfturbine bereits vor ihrem Auftreten erkannt werden. Diese Technologie ist bereits in vielen industriellen Anwendungen weit verbreitet und wird zunehmend auch in der Schifffahrt eingesetzt, um die Lebensdauer von Dampfturbinen und anderen Maschinen zu verlängern und ungeplante Ausfälle zu vermeiden.
Die Integration von Dampfturbinen in sogenannte “Smart Ships” ist eine weitere Entwicklung, die das Potenzial hat, die Effizienz und Leistung von Schiffen erheblich zu steigern. Diese „intelligenten Schiffe“ nutzen modernste Kommunikationssysteme, Datenanalytik und Automatisierung, um alle Aspekte des Schiffsbetriebs zu koordinieren, einschließlich der Dampfturbinen und anderer Maschinen. Ein intelligentes System könnte beispielsweise in Echtzeit den optimalen Betriebsmodus für die Dampfturbine berechnen, basierend auf den aktuellen Brennstoffkosten, Wetterbedingungen, Reisegeschwindigkeit und anderen Faktoren. Diese fortschrittliche Steuerung würde nicht nur den Energieverbrauch optimieren, sondern auch zur Reduktion der CO2-Emissionen beitragen.
Darüber hinaus könnte die Interaktion zwischen Dampfturbinen und anderen Schiffsmechanismen in Zukunft noch stärker automatisiert werden. Beispielsweise könnten Dampfturbinen mit Brennstoffzellen oder LNG-Verbrennungssystemen kombiniert werden, um den Energiebedarf effizient zu decken. Wenn die Dampfturbine aufgrund einer geänderten Betriebsumgebung (z. B. einem plötzlichen Wechsel der Geschwindigkeit oder eine Änderung der Lastanforderung) nicht mehr optimal arbeitet, könnte das System automatisch auf eine alternative Energiequelle umschalten, um den Betrieb des Schiffs aufrechtzuerhalten.
Die Nachhaltigkeit und Energieeffizienz sind ebenfalls zentrale Themen, die die Entwicklung der Dampfturbinentechnologie vorantreiben. In den kommenden Jahren wird der Fokus verstärkt auf die Kombination von Dampfturbinen mit erneuerbaren Energiequellen wie Wind- und Solarenergie gelegt werden. Einige Schiffe experimentieren bereits mit Windkraftanlagen, die zusätzlich zur Dampfturbine eine Teilmenge des benötigten Antriebs liefern. Auch die Nutzung von Solarzellen auf den Schiffsdächern könnte helfen, den Strombedarf des Schiffs für nicht-antriebsbezogene Funktionen wie Beleuchtung, Klimaanlage und Elektronik zu decken. Diese Technologien könnten die Gesamtemissionen und den Brennstoffverbrauch deutlich reduzieren, was zu einer umweltfreundlicheren Schifffahrt führt.
Der Einsatz von Hybridantriebssystemen – die Dampfturbinen mit Elektromotoren oder Brennstoffzellen kombinieren – könnte eine weitere Möglichkeit darstellen, die Nachhaltigkeit zu fördern. Diese Systeme könnten es ermöglichen, den Dampfturbinenbetrieb in ruhigen Gewässern oder auf kürzeren Strecken zu minimieren, um den Brennstoffverbrauch weiter zu senken und gleichzeitig den CO2-Ausstoß zu verringern. Elektromotoren, die mit Batterien oder Brennstoffzellen betrieben werden, könnten als primäre Energiequelle auf kurzen Strecken dienen, während die Dampfturbinen auf längeren Strecken bei höheren Geschwindigkeiten und größerer Leistung wieder zum Einsatz kommen.
Letztlich könnte auch die fortschreitende Forschung an alternativen Materialien dazu beitragen, die Dampfturbinen noch effizienter und langlebiger zu machen. Die Entwicklung von hochfesten, korrosionsbeständigen Materialien könnte den Verschleiß von Dampfturbinenkomponenten verringern und ihre Lebensdauer verlängern, was zu einer Reduktion der Betriebskosten und der Wartungsanforderungen führen würde.
Zusammengefasst lässt sich sagen, dass die Dampfturbine auch in der Zukunft eine Schlüsselrolle im Schiffsverkehr spielen wird, sowohl durch technologische Innovationen als auch durch die Integration von grünen Energiequellen und modernen Automatisierungstechnologien. Ihre Zuverlässigkeit, Effizienz und Brennstoffflexibilität werden weiterhin von Bedeutung sein, insbesondere bei großen Schiffsgrößen, die hohe Antriebsleistungen erfordern. Während neue Technologien und umweltfreundliche Brennstoffe auf den Markt kommen, wird die Dampfturbine auch weiterhin als wesentlicher Bestandteil des Schiffsantriebs in einer zunehmend nachhaltigen und technologisch fortschrittlichen Schifffahrtsindustrie bestehen.
Wie ist ein kohlekraftwerk aufgebaut
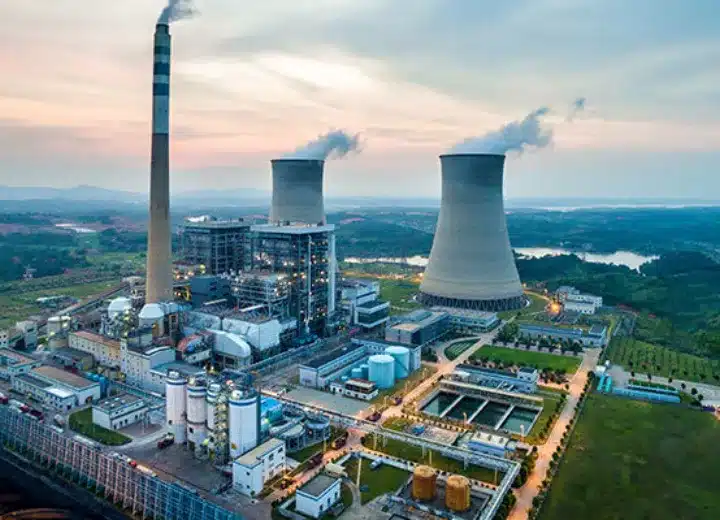
Ein Kohlekraftwerk ist eine Anlage, die Kohle als Brennstoff nutzt, um Elektrizität zu erzeugen. Der Aufbau eines Kohlekraftwerks kann je nach Technologie und Größe variieren, aber im Allgemeinen besteht es aus mehreren Hauptkomponenten, die zusammenarbeiten, um die in der Kohle gespeicherte Energie in Strom umzuwandeln. Hier ist ein Überblick über die wichtigsten Elemente eines typischen Kohlekraftwerks:
1. Kohlebunker und -lagerung
Zunächst wird die Kohle im Kohlebunker oder Lagerbereich gelagert, der oft eine große Kapazität hat, um sicherzustellen, dass eine kontinuierliche Brennstoffversorgung gewährleistet ist. Die Kohle wird entweder in Felsformationen abgebaut oder von Schiffen, Zügen oder Lastwagen zu einem Kohlekraftwerk transportiert. Die Kohle wird dort zwischengelagert, bevor sie in den Verbrennungsprozess eintritt.
2. Kohlenzerkleinerung
Bevor die Kohle verbrannt wird, muss sie zerkleinert und vermahlen werden, um die Oberfläche zu vergrößern und die Verbrennungseffizienz zu erhöhen. Kohlenzerkleinerungsanlagen, wie Mühlen oder Kohlemühlen, mahlen die Kohle in feines Pulver, das dann mit Luft gemischt wird, um eine bessere Verbrennung zu ermöglichen. Diese pulverisierte Kohle wird durch Rohrleitungen zum Brenner geführt.
3. Kessel (Dampferzeuger)
Im Kessel findet die eigentliche Verbrennung statt. Der Kessel ist ein großer, isolierter Bereich, in dem die pulverisierte Kohle verbrannt wird. Die Verbrennung von Kohle erzeugt extrem hohe Temperaturen, die Wasser in Dampf umwandeln. Der Kessel ist oft mit Wärmetauschern ausgestattet, die die Wärme der Abgase dazu nutzen, Wasser in verschiedenen Phasen zu erwärmen, bis es schließlich als hochdruckdampf den Kessel verlässt. In diesem Prozess entstehen auch Abgase, die Schadstoffe wie Schwefeldioxid (SO₂) und Stickoxide (NOₓ) enthalten.
4. Dampfturbine
Der Dampf aus dem Kessel wird in eine Dampfturbine geleitet, die durch die hohe Druck- und Temperaturenergie des Dampfes in Bewegung gesetzt wird. Der Dampf trifft auf die Schaufeln der Turbine, wodurch diese sich dreht und mechanische Energie erzeugt. Diese mechanische Energie wird in Rotationsenergie umgewandelt. Die Dampfturbine ist in der Regel mit einem Generator verbunden, der die mechanische Energie in elektrische Energie umwandelt. Der Generator erzeugt durch die Drehbewegung der Turbine Wechselstrom.
5. Kondensator
Nachdem der Dampf die Dampfturbine durchlaufen hat und seine Energie abgegeben wurde, gelangt er in den Kondensator. Der Kondensator hat die Aufgabe, den Dampf wieder zu Wasser zu kondensieren. Hier wird der Dampf durch Kühlwasser oder Kühlmittel abgekühlt, was dazu führt, dass der Dampf kondensiert und als heißes Wasser wieder in den Kessel zurückgeführt werden kann, um erneut verdampft zu werden (dies wird als geschlossenes Kreislaufsystem bezeichnet). Der Kondensator hilft also, den Kreislauf des Dampfsystems aufrechtzuerhalten.
6. Abgasreinigung
Die bei der Kohlenverbrennung entstehenden Abgase, die giftige Stoffe wie Schwefeldioxid, Stickoxide, Kohlenmonoxid und Feinstaub enthalten, müssen gereinigt werden, um die Umwelt zu schützen. Dazu kommen mehrere Reinigungs- und Filtertechnologien zum Einsatz:
- Entschwefelungsanlagen (Desulfurierung): Diese entfernen Schwefeldioxid (SO₂) aus den Abgasen, meist durch den Einsatz von Kalk oder Kalkstein, um Schwefelverbindungen zu neutralisieren.
- Stickoxidreduktion: Spezielle Katalysatoren oder Wasserdampf werden verwendet, um die Bildung von Stickoxiden (NOₓ) zu reduzieren.
- Feinstaubfilter: Diese fangen Staubpartikel und andere feste Partikel aus den Abgasen ab und verhindern, dass sie in die Atmosphäre gelangen.
7. Wärmetauscher und Kühlung
Da bei der Stromerzeugung erhebliche Mengen an Wärme entstehen, müssen diese effizient abgeführt werden. In Kohlekraftwerken wird dazu oft ein Wärmetauscher oder ein Kühlturm eingesetzt. Der Wärmetauscher leitet die überschüssige Wärme aus dem Dampf, bevor er in den Kondensator gelangt, an Kühlwasser weiter, das dann entweder in einen Fluss, ein Meer oder einen Kühlturm abgegeben wird. In Kühltürmen verdunstet das Kühlwasser, wodurch die überschüssige Wärme an die Atmosphäre abgegeben wird.
8. Elektrische Energieerzeugung und -verteilung
Die elektrische Energie, die vom Generator erzeugt wird, wird dann durch Transformatoren auf die benötigte Spannung gebracht und über das Stromnetz verteilt. Kohlekraftwerke müssen sicherstellen, dass die erzeugte Energie stabil und zuverlässig ist, was durch Spannungsregelung und Notstromsysteme gewährleistet wird.
9. Ascheentsorgung
Bei der Verbrennung von Kohle entstehen feste Rückstände in Form von Flugasche und Schlacke. Diese werden in speziellen Aschelagern oder Aschebunkern gesammelt und anschließend entweder in speziellen Anlagen weiterverarbeitet oder in geeigneten Deponien entsorgt. Moderne Kohlekraftwerke setzen zunehmend auf Ascheverwertung, um die Umweltbelastung durch Abfälle zu minimieren.
Fazit:
Zusammengefasst besteht der Aufbau eines Kohlekraftwerks aus mehreren wesentlichen Komponenten, die die Umwandlung von Kohle in elektrische Energie ermöglichen. Dabei spielen neben der eigentlichen Verbrennungstechnik und der Dampfturbine auch die Abgasreinigung, Wärmerückgewinnungssysteme und Kühlmechanismen eine entscheidende Rolle für die Effizienz und Umweltfreundlichkeit des Kraftwerks. In der heutigen Zeit werden immer wieder neue Technologien und Verbesserungen in Kohlekraftwerken implementiert, um die Emissionen zu verringern und die Energieeffizienz zu steigern.
Ein weiterer wichtiger Aspekt des Kohlekraftwerks ist die kontinuierliche Überwachung und Steuerung der Prozesse. Um eine hohe Betriebsstabilität und eine optimale Effizienz zu gewährleisten, müssen alle Schritte von der Kohleanlieferung über die Verbrennung bis hin zur Energieerzeugung präzise überwacht werden. Dies erfolgt über ein Leitsystem, das alle wichtigen Daten in Echtzeit sammelt, analysiert und an die Betriebsleiter weiterleitet. Moderne Kohlekraftwerke nutzen hierfür Automatisierung und digitale Steuerungssysteme, die es ermöglichen, die Leistung des gesamten Kraftwerks anzupassen, indem sie die Dampfdruck– und Temperaturbedingungen optimieren, die Kohlendioxid-Emissionen überwachen und die Abgasreinigungssysteme steuern. Dieses intelligente Management ist nicht nur wichtig für die Effizienz, sondern auch für die Sicherheit des Kraftwerks.
Die Umweltauswirkungen eines Kohlekraftwerks sind ebenfalls ein zentraler Punkt. Kohlekraftwerke sind einer der größten Verursacher von Treibhausgasemissionen, insbesondere CO₂, was in vielen Ländern zu einer starken Kritik und der Entwicklung von Emissionsbegrenzungen geführt hat. Um diesen Herausforderungen zu begegnen, wird zunehmend an CO₂-Abscheidung und Speicherungstechnologien (CCS) gearbeitet. Dabei wird CO₂ aus den Abgasen abgespalten, bevor es in die Atmosphäre gelangt, und in unterirdischen Lagerstätten gespeichert. Diese Technologien sind jedoch nach wie vor teuer und technisch herausfordernd, was ihre breite Anwendung bislang einschränkt. Darüber hinaus setzen immer mehr Kohlekraftwerke auf die Integration von erneuerbaren Energiequellen, wie Wind- oder Solarenergie, um den CO₂-Ausstoß zu verringern und den Anteil grüner Energie zu steigern.
Die Wirtschaftlichkeit eines Kohlekraftwerks wird ebenfalls durch den Brennstoffpreis beeinflusst. Kohle als Brennstoff ist häufig günstiger als Gas oder Öl, jedoch haben sich die Energiekosten durch die steigende Nachfrage nach umweltfreundlicheren Alternativen verändert. Marktveränderungen, wie etwa die Einführung von Emissionszertifikaten oder die Förderung erneuerbarer Energien, haben den Betrieb von Kohlekraftwerken weniger rentabel gemacht, was viele Betreiber dazu veranlasst, auf Modernisierungen oder Abriss umzuschwenken. Zudem setzen einige Länder auf Dekarbonisierung und Erneuerbare-Energien-Politiken, die Kohlekraftwerke langfristig aus dem Energiemix verbannen sollen. Trotzdem gibt es Regionen, in denen Kohlekraftwerke aufgrund der günstigen Brennstoffpreise und der bestehenden Infrastruktur weiterhin eine wichtige Rolle in der Energieversorgung spielen.
Ein weiterer Punkt betrifft die Lebensdauer eines Kohlekraftwerks. In der Regel beträgt die Lebensdauer einer solchen Anlage zwischen 30 und 50 Jahren, wobei regelmäßige Wartungsarbeiten, Reparaturen und Modernisierungen notwendig sind, um die Leistungsfähigkeit aufrechtzuerhalten. In den letzten Jahren ist die Entwicklung neuer Technologien und verbesserter Materialien, die Korrosion und Verschleiß reduzieren, ein wichtiger Faktor, um die Lebensdauer von Kohlekraftwerken zu verlängern und gleichzeitig die Brennstoffeffizienz zu steigern.
Zusammenfassend lässt sich sagen, dass der Aufbau eines Kohlekraftwerks zwar in vielen Fällen relativ standardisiert ist, jedoch durch technologische Innovationen und politische Rahmenbedingungen ständig weiterentwickelt wird. Kohlekraftwerke bleiben trotz der Herausforderungen im Bereich der Umweltfreundlichkeit und Kohlenstoffemissionen ein bedeutender Bestandteil der globalen Energieinfrastruktur, besonders in Ländern, die auf fossile Brennstoffe angewiesen sind. Der Übergang zu einer nachhaltigen Energiezukunft wird jedoch mit zunehmender Forschung an grünen Technologien, Energieeffizienz und Hybridlösungen vorangetrieben, sodass Kohlekraftwerke auch weiterhin in den globalen Energiemix integriert werden können.
Die Zukunft der Kohlekraftwerke wird in vielerlei Hinsicht von der Entwicklung neuer Technologien und politischer Maßnahmen beeinflusst. Ein wichtiger Trend ist die zunehmende Elektrifizierung von Sektoren, die traditionell auf fossile Brennstoffe angewiesen sind, wie die Industrie und der Verkehr. Kohlekraftwerke können eine Schlüsselrolle spielen, indem sie Grünstrom für den Energiebedarf dieser Sektoren bereitstellen, insbesondere in Regionen, in denen erneuerbare Energien aufgrund von Wetterabhängigkeit oder geografischen Gegebenheiten nicht immer zuverlässig verfügbar sind.
Die steigende Nachfrage nach Speichertechnologien, wie Batterien oder Pumpspeicherkraftwerke, könnte auch den Betrieb von Kohlekraftwerken in einer zunehmend dekarbonisierten Welt unterstützen. Kohlekraftwerke könnten dann als Backup-Kraftwerke oder zur Spitzenlastabdeckung fungieren, wenn erneuerbare Energiequellen wie Wind und Solar keine ausreichende Energie liefern. In diesem Szenario könnte das Kohlekraftwerk mit Flexibilitätsanforderungen arbeiten, die es ihm ermöglichen, sich schnell an veränderte Netzbedingungen anzupassen, ohne den Betrieb vollständig aufzugeben.
Ein weiteres bedeutendes Entwicklungspotential liegt in der Kombination von Kohlekraftwerken mit Technologien zur Nutzung von Wasserstoff. Diese sogenannten Power-to-X-Anwendungen könnten es Kohlekraftwerken ermöglichen, neben der Stromerzeugung auch grünen Wasserstoff zu produzieren. Der Wasserstoffmarkt wächst, da Wasserstoff als sauberer Brennstoff für den Verkehr und andere Sektoren zunehmend nachgefragt wird. Ein Kohlekraftwerk könnte in Zukunft mit einem Elektrolyseur ausgestattet werden, der Strom aus der Kohlenverbrennung zur Herstellung von Wasserstoff nutzt. Diese Power-to-Gas-Technologien könnten nicht nur zur CO₂-Reduktion beitragen, sondern auch als Energiespeicher fungieren, indem überschüssiger Strom aus Kohle in Wasserstoff umgewandelt wird, der bei Bedarf wieder in Energie zurückverwandelt werden kann.
Auch die Integrationsmöglichkeiten von Kohlekraftwerken in sogenannte “Smart Grids” – intelligente Stromnetze, die eine dynamische Anpassung der Energieversorgung und -nachfrage ermöglichen – könnten eine neue Ära für den Kohlekraftwerksbetrieb einläuten. Diese Netze könnten den Lastenwechsel zwischen verschiedenen Kraftwerkstypen effizienter gestalten, indem sie den Kohlekraftwerken ermöglichen, ihre Leistung je nach Bedarf des Netzes anzupassen. In einem solchen intelligenten System könnten Kohlekraftwerke so betrieben werden, dass sie nur dann aktiv werden, wenn Spitzenlasten entstehen, wodurch die Gesamtleistung des Netzes verbessert und der CO₂-Ausstoß minimiert wird.
Trotz dieser innovativen Ansätze bleibt die CO₂-Emission von Kohlekraftwerken jedoch ein zentrales Thema, das nicht unbeachtet bleiben kann. Einige Regierungen und Unternehmen setzen zunehmend auf den Ausbau von CO₂-Abscheidungs- und Speichersystemen (CCS), um Kohlenstoffemissionen zu reduzieren. Diese Technologien werden jedoch durch hohe Investitionskosten und technologische Herausforderungen gebremst. Während CCS als vielversprechende Technologie gilt, wird weiterhin an der Energieeffizienz und den Kostenmodellen gearbeitet, um ihre breite Anwendung zu ermöglichen. Sollte es gelingen, diese Technologien zur kommerziellen Reife zu bringen, könnten sie die Lebensdauer von Kohlekraftwerken in einer dekarbonisierten Welt erheblich verlängern.
Ein weiterer interessanter Ansatz ist die Umstellung auf biogene Brennstoffe. Einige Kohlekraftwerke experimentieren bereits mit der Verwendung von Biomasse, wie Holzpellets oder landwirtschaftliche Abfälle, als Ergänzung zur Kohle oder als vollständiger Ersatz. Diese Biomasse kann als CO₂-neutral betrachtet werden, da das CO₂, das bei der Verbrennung freigesetzt wird, zuvor von den Pflanzen aus der Atmosphäre aufgenommen wurde. Der Einsatz von Biomasse anstelle von fossiler Kohle könnte den CO₂-Ausstoß eines Kohlekraftwerks erheblich verringern und gleichzeitig die Energieversorgung aufrechterhalten. Einige Kohlekraftwerke haben bereits begonnen, ihre Technologie auf diese Brennstoffe anzupassen, was eine langsame Transition zu nachhaltigeren Betriebsmodellen darstellt.
Die politischen Rahmenbedingungen werden ebenfalls eine Schlüsselrolle bei der Zukunft von Kohlekraftwerken spielen. Internationale Klimaziele, wie das Pariser Abkommen, zwingen viele Länder dazu, ihre Emissionen drastisch zu reduzieren, was Kohlekraftwerke unter Druck setzt. Einige Länder setzen auf den Ausbau erneuerbarer Energien und den Ausstieg aus der Kohleverstromung, während andere weiterhin auf Kohle angewiesen sind, insbesondere in Entwicklungs- und Schwellenländern. Es wird erwartet, dass Internationale Emissionshandelsysteme und CO₂-Steuern die Wirtschaftlichkeit von Kohlekraftwerken weiter beeinflussen und den Umstieg auf saubere Energiequellen beschleunigen.
Zusammengefasst lässt sich sagen, dass Kohlekraftwerke in ihrer traditionellen Form zwar eine wichtige Rolle in der globalen Energieversorgung spielen, aber mit den richtigen Technologien und politischen Maßnahmen in eine nachhaltigere Zukunft geführt werden können. Der Übergang zu grüner Energie, die Integration neuer Technologien wie CCS, Wasserstoffproduktion und Biomasse sowie die Förderung von Speichertechnologien bieten zahlreiche Möglichkeiten, um die negativen Auswirkungen von Kohlekraftwerken zu reduzieren. In den kommenden Jahren wird sich zeigen, wie Kohlekraftwerke in einer zunehmend dekarbonisierten Welt weiterentwickelt werden können.
Die Zukunft der Kohlekraftwerke hängt also nicht nur von technologischen Innovationen, sondern auch von einer gezielten politischen Steuerung und der globale Zusammenarbeit ab. Die Integration von erneuerbaren Energien wie Solar- und Windkraft, kombiniert mit Speichertechnologien und flexiblen Kohlekraftwerkslösungen, könnte dazu beitragen, den CO₂-Ausstoß deutlich zu senken, während die Versorgungssicherheit weiterhin gewährleistet wird.
Ein zentraler Punkt hierbei ist, dass Stromnetze in Zukunft viel flexibler und intelligenter werden müssen, um mit der zunehmenden Fluktuation der erneuerbaren Energien umzugehen. Während erneuerbare Energien wie Solar- und Windkraft wetterabhängig sind und daher nicht immer gleichmäßig zur Verfügung stehen, könnte ein hybrides System aus traditionellen Kohlekraftwerken und erneuerbaren Energiequellen eine stabile Energieversorgung sichern. Die Herausforderung besteht darin, den Übergang zu saubereren und erneuerbaren Energiequellen zu schaffen, ohne dabei die Netzstabilität oder die Energiepreise zu gefährden.
Ein weiteres zukunftsträchtiges Konzept ist die Kohlenstoffnutzung (Carbon Utilization), bei der das aus Kohlekraftwerken abgespaltene CO₂ nicht nur gespeichert, sondern auch industriell genutzt wird. Das CO₂ könnte beispielsweise in der Chemieindustrie zur Herstellung von Kunststoffen, Düngemitteln oder sogar synthetischen Kraftstoffen verwendet werden. Solche Technologien würden den CO₂-Ausstoß minimieren und gleichzeitig einen wirtschaftlichen Nutzen aus den Emissionen ziehen. Diese Form der Kreislaufwirtschaft könnte die Umweltbelastung durch Kohlekraftwerke weiter senken und gleichzeitig zur Wirtschaftlichkeit beitragen.
Die Forschung und Entwicklung in Bezug auf CO₂-freie Brennstoffe ist ebenfalls ein wichtiger Bestandteil der Zukunft von Kohlekraftwerken. Einige Unternehmen und Forschungsinstitute konzentrieren sich auf die Entwicklung von synthetischen Brennstoffen, die aus erneuerbaren Energiequellen hergestellt werden, aber eine ähnliche chemische Struktur wie fossile Brennstoffe aufweisen. Diese grünen Brennstoffe könnten in bestehenden Kohlekraftwerken verbrannt werden, wodurch die Infrastruktur weiterhin genutzt werden kann, ohne CO₂-Emissionen zu erzeugen. Solche grüne Kohleersatzstoffe könnten es ermöglichen, den Betrieb bestehender Kohlekraftwerke noch über Jahrzehnten hinweg fortzusetzen, ohne die Umwelt zu belasten.
Trotz der potenziellen innovative Lösungen für Kohlekraftwerke bleibt ein wichtiger Aspekt die gesellschaftliche Akzeptanz und der Widerstand gegen fossile Brennstoffe. In vielen Ländern gibt es zunehmend Proteste und Politikentscheidungen, die Kohlekraftwerke und andere fossile Brennstoffe in Frage stellen. Der Klimawandel und seine Auswirkungen auf die Umwelt sind zu einem der drängendsten Themen geworden, und viele Bürger und Organisationen fordern schnellere Maßnahmen zur Reduzierung des CO₂-Ausstoßes. Infolgedessen müssen Kohlekraftwerksbetreiber und Regierungen möglicherweise große Anstrengungen unternehmen, um den Übergang zu saubereren Energiequellen zu beschleunigen und dabei eine sozial gerechte Lösung zu finden.
In vielen Ländern und Regionen, die stark auf Kohle angewiesen sind, könnte der Übergang zu einem nachhaltigen Energiesystem auch wirtschaftliche und soziale Herausforderungen mit sich bringen. Kohlekraftwerke beschäftigen viele Menschen, und der Umstieg auf erneuerbare Energien könnte zu Arbeitsplatzverlusten führen. Daher ist es wichtig, dass Regierungen Umbauprogramme und Schulungsinitiativen entwickeln, um Arbeitskräfte in grüne Industrien oder erneuerbare Energiesektoren zu integrieren, um den sozialen und wirtschaftlichen Übergang zu erleichtern.
Abschließend lässt sich sagen, dass Kohlekraftwerke in einer zunehmend dekarbonisierten Welt einer fundamentalen Veränderung unterzogen werden müssen. Die Fossilbrennstoffnutzung wird von vielen Ländern nach und nach reduziert, aber in vielen Regionen sind Kohlekraftwerke nach wie vor ein wichtiger Bestandteil der Energieversorgung. Der Übergang zu erneuerbaren Energiequellen, die Einführung von CO₂-Abscheidungstechnologien und die Wasserstoffproduktion bieten vielversprechende Ansätze, um Kohlekraftwerke umweltfreundlicher und nachhaltiger zu machen. Gleichzeitig muss der Umbau sozial und wirtschaftlich begleitet werden, um sicherzustellen, dass keine Regionen oder Bevölkerungsgruppen zurückgelassen werden.
In den kommenden Jahren wird die Entwicklung von Kohlenstofftechnologien, die Implementierung grüner Brennstoffe, die Elektromobilität und Hybridlösungen in Kohlekraftwerken sowie die globale Zusammenarbeit zur Bekämpfung des Klimawandels entscheidend sein, um Kohlekraftwerke in eine umweltfreundlichere und nachhaltigere Zukunft zu führen.
Schmierölsystem der Dampfturbine
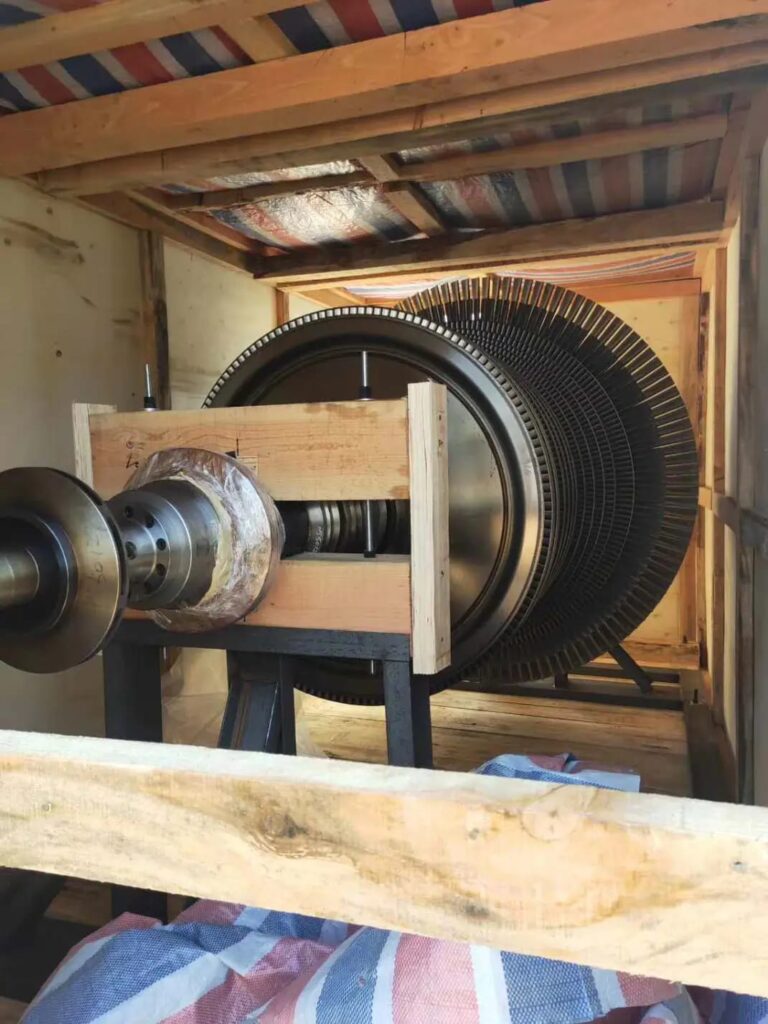
Das Schmierölsystem einer Dampfturbine ist entscheidend für den reibungslosen Betrieb und die Langlebigkeit der Turbine. In einem Dampfturbinenkraftwerk werden die Turbinen durch hochdrehende Rotoren und lagern mit hohen Geschwindigkeiten betrieben, wodurch eine exzellente Schmierung erforderlich ist, um den mechanischen Verschleiß zu minimieren und die Effizienz des gesamten Systems aufrechtzuerhalten.
Hauptfunktionen des Schmierölsystems
- Reduzierung der Reibung: Das Schmieröl bildet einen dünnen Film zwischen den beweglichen Teilen der Turbine, wie zum Beispiel den Lagerwellen und Dichtungen, um die Reibung zu verringern. Dies minimiert den Verschleiß und erhöht die Lebensdauer der Komponenten.
- Kühlung: Schmieröl hat auch eine Kühlfunktion. Da die Turbine während des Betriebs erheblichen Kräften und Temperaturen ausgesetzt ist, hilft das Öl, die entstehende Wärme abzuleiten, besonders von den Lagerstellen. Ein effektives Kühlsystem ist entscheidend, um eine Überhitzung zu vermeiden, die zu Schäden an den Lagern und anderen Bauteilen führen könnte.
- Korrosionsschutz: Das Schmieröl schützt Metalloberflächen vor Korrosion durch die Bildung einer schützenden Schicht. Dies ist besonders wichtig, da Dampfturbinen oft mit Feuchtigkeit und Salzen in Kontakt kommen, die die Metallteile angreifen könnten.
- Sauberkeit: Schmierölsysteme tragen dazu bei, Verunreinigungen wie Staub, Metallspäne oder andere Fremdpartikel aus dem Bereich der Turbine zu entfernen. Das Öl wird durch Filter geführt, um diese Verunreinigungen zu entfernen und die Turbine sauber zu halten.
Aufbau eines Schmierölsystems
Ein typisches Schmierölsystem für eine Dampfturbine umfasst mehrere Hauptkomponenten:
- Ölbehälter (Ölreservoir): Der Öltank speichert das Schmieröl und sorgt dafür, dass eine ausreichende Menge zur Verfügung steht. Der Tank muss so konstruiert sein, dass das Öl sauber und frei von Verunreinigungen bleibt. Oft sind diese Behälter beheizt, um das Öl auf eine optimale Betriebstemperatur zu bringen und die Viskosität zu kontrollieren.
- Ölpumpe: Die Ölpumpe fördert das Schmieröl vom Tank zu den Lagern und anderen kritischen Turbinenkomponenten. Sie sorgt für einen konstanten Druck und eine gleichmäßige Ölversorgung. In einigen Fällen kommen auch Zahnradpumpen oder Kolbenpumpen zum Einsatz, um eine hohe Förderleistung und Druckstabilität zu gewährleisten.
- Ölfilter: Um eine kontaminationsfreie Schmierung sicherzustellen, durchläuft das Schmieröl vor dem Eintritt in die Turbine Filtereinheiten, die Verunreinigungen wie Staub, Rostpartikel oder kleine Metallspäne aus dem Öl entfernen. Diese Filter müssen regelmäßig gewartet und ausgetauscht werden, um eine kontinuierliche Ölqualität zu gewährleisten.
- Kühlsystem: Das Öl-Kühlsystem ist wichtig, um die Temperatur des Schmieröls innerhalb eines optimalen Bereichs zu halten. Wenn das Öl zu heiß wird, verliert es seine Schmierfähigkeit und könnte die Turbine beschädigen. Deshalb werden Wärmetauscher oder Kühlaggregate eingesetzt, die überschüssige Wärme abführen und das Öl auf einer konstanten Temperatur halten.
- Ölüberwachungs- und Steuerungssystem: Modernere Dampfturbinen sind mit Sensoren und Steuerungen ausgestattet, die den Ölzustand überwachen. Diese Systeme messen die Öltemperatur, den Öldruck, die Ölmenge und die Viskosität des Schmieröls. Wenn einer dieser Parameter außerhalb des normalen Bereichs liegt, wird ein Alarm ausgelöst, um einen möglichen Fehler frühzeitig zu erkennen und Reparaturen zu vermeiden.
- Lager: Die Lager der Dampfturbine, die sich in der Regel an den Rotorgehäusen befinden, sind die Hauptkomponenten, die das Schmieröl benötigen. Sie sind so konzipiert, dass sie mit Hilfe des Schmieröls ständig geschmiert werden, um die Reibung zu verringern und den Verschleiß zu minimieren. Es gibt auch Hydrodynamische Lager, bei denen sich das Öl zwischen Lager und Welle so verhält, dass es die Rotation der Welle ohne direkten Kontakt ermöglicht, was den Verschleiß weiter reduziert.
- Ölleitungen und -ventile: Das Öl wird durch Leitungen und Ventile zu den jeweiligen Turbinenkomponenten transportiert. Die Ventile dienen dazu, den Ölfluss zu regulieren und sicherzustellen, dass jede Turbinenkomponente ausreichend mit Schmieröl versorgt wird.
Wartung des Schmierölsystems
Die Wartung des Schmierölsystems ist entscheidend, um den ordnungsgemäßen Betrieb und die Betriebsdauer der Dampfturbine zu gewährleisten. Hierzu gehören:
- Ölwechsel: Das Schmieröl muss regelmäßig gewechselt werden, um seine Schmierfähigkeit zu erhalten und zu verhindern, dass sich Ablagerungen und Verunreinigungen ansammeln. In vielen Fällen werden Ölproben entnommen, um die Qualität des Öls zu überprüfen und zu entscheiden, wann ein Wechsel erforderlich ist.
- Filterreinigung: Die Ölfilter müssen ebenfalls regelmäßig gewartet und gereinigt oder ausgetauscht werden, um sicherzustellen, dass das Öl frei von Verunreinigungen bleibt.
- Überwachung der Ölqualität: Moderne Schmierölsysteme sind oft mit Systemen zur Ölanalyse ausgestattet, die den Zustand des Schmieröls überwachen. Diese Analysen umfassen die Prüfung auf Viskosität, Feuchtigkeit, Metallpartikel und andere Indikatoren, die auf mögliche Probleme hinweisen könnten.
- Dichtungen und Leitungen: Es ist wichtig, die Dichtungen und Leitungen regelmäßig auf Lecks oder Schäden zu überprüfen, um sicherzustellen, dass das Öl effizient und ohne Verlust zu den Turbinenkomponenten gelangt.
Arten von Schmierölen
Für Dampfturbinen werden unterschiedliche Schmieröle verwendet, je nach Betriebsbedingungen und den Anforderungen der Turbine. Es gibt zwei Haupttypen von Schmierölen:
- Mineralölbasierte Schmieröle: Diese werden traditionell in Dampfturbinen eingesetzt. Sie bieten gute Schmiereigenschaften und sind für viele Anwendungen geeignet, da sie kostengünstig sind und zuverlässig arbeiten.
- Synthetische Schmieröle: Diese bieten eine verbesserte Hitzebeständigkeit und Oxidationsbeständigkeit, was sie besonders für Hochleistungsturbinen geeignet macht. Synthetische Öle können bei höheren Temperaturen betrieben werden und haben eine längere Lebensdauer als mineralölbasierte Öle.
In einigen modernen Turbinen werden auch biologisch abbaubare Schmierstoffe eingesetzt, um die Umweltauswirkungen bei Leckagen zu minimieren.
Fazit
Das Schmierölsystem einer Dampfturbine spielt eine Schlüsselrolle bei der Aufrechterhaltung der Effizienz, der Minimierung des Verschleißes und der Maximierung der Lebensdauer der Turbine. Durch regelmäßige Wartung, moderne Überwachungssysteme und die Verwendung hochwertiger Schmierstoffe kann der Betrieb einer Dampfturbine optimiert und die Notwendigkeit von Reparaturen und Ausfällen minimiert werden.
Ein wichtiger Aspekt bei der Effizienz des Schmierölsystems ist die genaue Abstimmung der Ölversorgung auf die unterschiedlichen Betriebsbedingungen der Dampfturbine. Da eine Dampfturbine nicht konstant unter den gleichen Lasten und Betriebsbedingungen arbeitet, muss das Schmierölsystem in der Lage sein, auf verschiedene Betriebsmodi zu reagieren. Besonders in der Anlaufphase und bei Schwankungen im Lastbereich können sich die Anforderungen an die Schmierung ändern, weshalb das System dynamisch reagieren muss, um eine gleichmäßige Ölversorgung sicherzustellen. Ein flexibles und gut dimensioniertes Schmierölsystem verhindert somit Überhitzung und Verschleiß, die durch unzureichende Schmierung entstehen könnten.
Eine der Herausforderungen beim Schmierölsystem ist die kontinuierliche Verunreinigung des Schmieröls. Im Laufe der Zeit können Verschleißpartikel aus den Lagern oder von den Rotoren selbst in das Öl gelangen. Diese Partikel müssen entfernt werden, da sie zu einer verringerte Schmierleistung führen und den Verschleiß der Turbinenkomponenten beschleunigen können. Die Integration fortschrittlicher Filtertechnologien und Ölaufbereitungssysteme ist entscheidend, um das Öl kontinuierlich zu reinigen und sicherzustellen, dass nur sauberes Öl zu den Lagern gelangt. In einigen Fällen werden auch magnetische Filter oder Zentrifugen verwendet, um feinste Partikel zu entfernen.
Ein weiterer Aspekt, der die Leistung des Schmierölsystems beeinflusst, ist die Öltemperatur. Zu niedrige Temperaturen können dazu führen, dass das Öl zu viskos wird und die Schmierung nicht mehr optimal funktioniert. Andererseits kann eine zu hohe Temperatur die Ölqualität beeinträchtigen und zu einer schnelleren Oxidation des Öls führen. Ein gut dimensioniertes Heizsystem sorgt dafür, dass das Öl schnell auf die erforderliche Betriebstemperatur gebracht wird, während gleichzeitig ein effektives Kühlsystem verhindert, dass das Öl überhitzt. Die Temperaturregelung ist dabei eng mit den Betriebsbedingungen der Turbine verknüpft, da die Wärme, die durch den Betrieb der Turbine entsteht, das Ölsystem ebenfalls beeinflusst.
Die Langlebigkeit des Schmieröls und des Schmierölsystems wird auch durch die Vermeidung von Ölverlusten sichergestellt. Ölverluste durch Leckagen oder undichte Stellen in den Ölkreisläufen können nicht nur zu einem unzureichenden Schmierfluss führen, sondern auch zur Umweltbelastung beitragen, wenn das Öl in die Umgebung gelangt. Daher wird bei der Konstruktion des Schmierölsystems besonders auf dichte Verbindungen, hochwertige Dichtungen und regelmäßige Überprüfungen der Leitungen geachtet. In modernen Turbinen werden oft auch Ölauffangsysteme integriert, die eventuelle Leckagen auffangen und verhindern, dass Öl in die Umwelt gelangt.
Zusätzlich ist die Integration von Überwachungssystemen in das Schmierölsystem von wachsender Bedeutung. Diese Systeme überwachen nicht nur die Öltemperatur, den Öldruck und die Ölqualität, sondern können auch Frühwarnsysteme bieten, wenn eine Anomalie im Betrieb des Schmierölsystems erkannt wird. Bei Anzeichen von Problemen, wie etwa einem plötzlichen Anstieg der Öltemperatur oder einem Druckabfall, können sofortige Maßnahmen eingeleitet werden, um Schäden an der Turbine zu verhindern. Diese Überwachungssysteme sind zunehmend mit predictive maintenance-Technologien gekoppelt, die auf Basis von Datenanalysen mögliche zukünftige Probleme vorhersagen und vorbeugende Wartungsmaßnahmen empfehlen.
Darüber hinaus ist der Energieverbrauch des Schmierölsystems ein weiterer wichtiger Faktor. Das Schmierölsystem muss nicht nur eine ausreichende Schmierung und Kühlung gewährleisten, sondern auch effizient arbeiten, um den Energieverbrauch zu minimieren. Dies wird durch den Einsatz von hoch effizienten Pumpen und Optimierung des Ölkreislaufs erreicht. In einigen Fällen kommen auch frequenzgesteuerte Pumpen zum Einsatz, die den Ölfluss in Abhängigkeit vom Bedarf anpassen, um den Energieverbrauch zu reduzieren und gleichzeitig den Betrieb zu maximieren.
In der Zukunft könnte die Automatisierung und Digitalisierung des Schmierölsystems weiter zunehmen. Die Integration von IoT-Sensoren, die in Echtzeit Daten über den Zustand des Schmierölsystems liefern, könnte eine noch präzisere Steuerung und Wartung ermöglichen. Diese Systeme könnten automatisch Anpassungen vornehmen oder Wartungsbedarf erkennen, noch bevor es zu einem Ausfall kommt, und somit die Betriebszeit und Verfügbarkeit der Dampfturbine weiter steigern.
Insgesamt spielt das Schmierölsystem eine zentrale Rolle für den sicheren und effizienten Betrieb einer Dampfturbine. Durch die Kombination aus effektiver Schmierung, Kühlung, Verunreinigungskontrolle und kontinuierlicher Überwachung wird sichergestellt, dass die Turbine unter allen Betriebsbedingungen zuverlässig funktioniert und eine lange Lebensdauer hat.
Ein weiterer wichtiger Aspekt, der das Schmierölsystem einer Dampfturbine betrifft, ist die Anpassung an verschiedene Betriebsmodi und Betriebsbedingungen. Bei Teillastbetrieb oder Schwankungen in der Last muss das Schmierölsystem in der Lage sein, auf unterschiedliche Anforderungen zu reagieren. Dies erfordert ein hohes Maß an Flexibilität, insbesondere bei der Anpassung des Ölflusses und der Öldruckregelung. In Zeiten hoher Belastung müssen die Lagertemperaturen konstant gehalten werden, was eine präzise Steuerung des Öldrucks und der Ölzufuhr erfordert. Andererseits, wenn die Turbine mit einer geringeren Last arbeitet, muss das Schmieröl effizient eingesetzt werden, ohne unnötige Verschwendung.
Die Flexibilität des Systems wird zunehmend durch den Einsatz von intelligenten Steuerungen und sensorbasierten Systemen erreicht, die automatisch die Ölversorgung in Abhängigkeit vom Betriebspunkt der Turbine regulieren. So wird eine Überversorgung oder Unterversorgung mit Schmieröl vermieden, was sowohl den Energieverbrauch des Systems optimiert als auch die Schmierungsqualität während des gesamten Betriebszyklus aufrechterhält.
Zudem ist es von Bedeutung, dass das Schmierölsystem eng mit anderen wichtigen Baugruppen der Dampfturbine wie den Kondensatoren, Dampfreglern und den Kühlkreisläufen zusammenarbeitet. Diese Komponenten erzeugen Wärme, die auch das Schmierölsystem beeinflussen kann. Eine gute Zusammenarbeit zwischen den Systemen sorgt dafür, dass keine ungünstigen Temperaturen oder Druckverhältnisse entstehen, die den Turbinenbetrieb beeinträchtigen könnten. Insbesondere beim Übergang zwischen verschiedenen Betriebszuständen (z. B. Wärmeaufbau und Abkühlphase) ist es entscheidend, dass das Schmierölsystem reagiert, um eine gleichmäßige Schmierung und Temperaturregelung zu gewährleisten.
Ein noch sehr wichtiger Bereich ist die Ölverschmutzung und wie sie das Schmierölsystem beeinflusst. Öl kann durch den Betrieb der Turbine verschiedenen Arten von Verunreinigungen ausgesetzt sein, wie etwa Feuchtigkeit (z. B. Wasserdampf), Schmutzpartikel oder Metallabrieb aus den Turbinenlagern. Feuchtigkeit im Öl kann zum Beispiel die Schmierwirkung beeinträchtigen und zur Bildung von Schlammmaterial führen, das die Effizienz des Schmierölsystems verringert und die Lebensdauer des Schmieröls selbst verkürzt. Um diesen negativen Auswirkungen entgegenzuwirken, ist es notwendig, dass das Öl nicht nur regelmäßig gefiltert wird, sondern auch Maßnahmen zur Feuchtigkeitsabsorption ergriffen werden.
Ein Trocknungs- und Entfeuchtungssystem im Schmierölsystem könnte beispielsweise dabei helfen, Feuchtigkeit zu entfernen und das Öl wieder in einen betriebsfähigen Zustand zu versetzen. In einigen Fällen werden spezielle Ölabscheider und Feuchtigkeitsfilter verwendet, die Wassertröpfchen aus dem Öl abscheiden, bevor sie in die Lagereinheiten gelangen. Moderne Technologien wie Filtrationseinheiten mit Aktivkohle oder membranbasierte Systeme bieten Möglichkeiten, chemische Verunreinigungen sowie organische Verbindungen zu beseitigen, die möglicherweise die Ölqualität beeinträchtigen könnten.
Für die Nachhaltigkeit des gesamten Schmierölsystems ist es wichtig, dass das Öl regelmäßig auf chemische Veränderungen oder Verschlechterung untersucht wird. Hier kommen moderne Öl-Überwachungsgeräte ins Spiel, die den Zustand des Schmieröls permanent überwachen und sofortige Alarmmeldungen bei unerwünschten Veränderungen wie Viskositätsverlust, Ölverschmutzung oder Temperaturerhöhung auslösen. Diese Geräte bieten nicht nur eine Echtzeitüberwachung, sondern auch die Möglichkeit, präventive Maßnahmen zur Ölpflege und Verlängerung der Lebensdauer des Systems zu ergreifen.
Die Wahl des Schmieröls spielt ebenfalls eine wichtige Rolle, da verschiedene Turbinen und ihre spezifischen Betriebsbedingungen unterschiedliche Anforderungen an die Ölviskosität und Temperaturstabilität stellen. Für Dampfturbinen mit besonders hohen Betriebstemperaturen werden daher hochwertige synthetische Schmierstoffe verwendet, die gegenüber normalen mineralischen Ölen eine weitaus höhere Wärmebeständigkeit und Oxidationsstabilität bieten. Ein solches Öl bietet zudem die Möglichkeit, auch bei extremen Betriebstemperaturen eine hervorragende Schmierung zu gewährleisten, ohne die Entstehung von Ablagerungen oder Korrosion zu begünstigen.
Zusätzlich zu den technischen Aspekten der Schmierung spielt auch die Ölmanagementstrategie eine Rolle. Die Wartung des Schmierölsystems muss nicht nur nach festgelegten Intervallen erfolgen, sondern auch in Übereinstimmung mit den spezifischen Anforderungen der Dampfturbine. So müssen Turbinenbetreiber regelmäßig Proben des Schmieröls entnehmen und eine chemische Analyse durchführen, um festzustellen, ob das Öl noch in gutem Zustand ist oder ersetzt werden muss. Diese Vorgehensweise hilft, potenzielle Probleme im Voraus zu erkennen und zu vermeiden, bevor sie zu ernsthaften Schäden oder einem Ausfall der Turbine führen.
Die Zukunft des Schmierölsystems könnte auch durch den Einsatz von KI und maschinellem Lernen beeinflusst werden. Mit fortschrittlichen Analysetools und automatisierten Wartungssystemen könnten in naher Zukunft innovative Möglichkeiten zur Überwachung und Steuerung des gesamten Schmierprozesses entwickelt werden. Die Erfassung und Analyse von Betriebsdaten und Ölparametern könnte zu einer noch präziseren Optimierung der Schmierstrategie führen, was die Effizienz des Schmierölsystems weiter steigert und gleichzeitig den Energieverbrauch minimiert.
Letztlich lässt sich sagen, dass das Schmierölsystem einer Dampfturbine eine kritische Komponente für den sicheren und effizienten Betrieb darstellt. Durch den Einsatz moderner Technologien zur Überwachung, Filterung, Feuchtigkeitskontrolle und Temperaturregelung können Dampfturbinenbetreiber sicherstellen, dass ihre Anlagen auch unter schwierigen Betriebsbedingungen zuverlässig und langfristig funktionieren.
Ein weiterer fortschreitender Bereich bei der Entwicklung von Schmierölsystemen für Dampfturbinen ist die Integration von IoT (Internet of Things) und vernetzten Sensoren. Diese Technologie ermöglicht eine nahtlose Datenübertragung und die Möglichkeit, Echtzeitinformationen über die Leistung des Schmierölsystems zu sammeln. Diese Informationen können dann in einer zentralen Steuerungseinheit analysiert und zur Fehlerdiagnose sowie für vorausschauende Wartungsstrategien genutzt werden.
Durch die Installation von sensorbasierten Systemen wird es möglich, die Ölqualität, Temperatur, Viskosität, Feuchtigkeit und den Druck des Schmieröls kontinuierlich zu überwachen und bei Bedarf sofortige Anpassungen vorzunehmen. Das schafft nicht nur eine höhere Betriebssicherheit, sondern auch eine verbesserte Effizienz im gesamten Betrieb der Dampfturbine, da potenzielle Probleme schneller identifiziert werden können, bevor sie den gesamten Turbinenbetrieb beeinträchtigen.
Ein Schritt in die Zukunft könnte die Automatisierung des Ölmanagements sein, bei dem intelligente Systeme automatisch die erforderlichen Ölparameter anpassen, basierend auf den gemessenen Betriebsbedingungen der Turbine. Dies könnte die Wartungskosten und den Energieverbrauch weiter senken und gleichzeitig die Betriebszeit maximieren, da die Turbine immer mit optimalen Schmierbedingungen betrieben wird.
Zusätzlich zur Digitalisierung könnten auch umweltfreundliche Alternativen im Bereich der Schmierstoffe weiter an Bedeutung gewinnen. Es wird zunehmend auf den Einsatz nachhaltigerer Schmieröle geachtet, die biologisch abbaubar sind und eine geringere Umweltauswirkung bei Leckagen oder Entsorgung haben. Ein wachsendes Interesse an grüneren Technologien hat auch dazu geführt, dass die Industrie nach alternative Schmierstoffe sucht, die weniger toxisch sind und eine geringere Kohlenstoffbelastung haben.
Einige Unternehmen setzen daher zunehmend auf biologische oder synthetische Öle, die die Umweltbelastung verringern, während sie gleichzeitig eine gute Schmierleistung bieten. Diese Schmierstoffe bieten Vorteile wie hohe Viskositätsstabilität, bessere Oxidationsbeständigkeit und weniger Ablagerungen, was zur Verringerung des Wartungsaufwands beiträgt.
Die Energieeffizienz des Schmierölsystems wird ebenfalls durch den Verzicht auf unnötige Heizungen oder durch den Einsatz von Energiespartechnologien optimiert. Bei modernen Dampfturbinen wird zunehmend darauf geachtet, dass nicht nur der Schmierölkreislauf effizient arbeitet, sondern auch der gesamte Antriebsmechanismus zur Verbesserung der Betriebswirtschaftlichkeit und Energieeffizienz der Anlage beiträgt.
Neben der Verwendung von grünen Schmierstoffen geht die Entwicklung auch in Richtung modularer und skalierbarer Systeme, die es ermöglichen, kleinere und flexiblere Turbinen für unterschiedliche Anwendungsbereiche zu integrieren. Hierbei können die Schmierölsysteme an die spezifischen Anforderungen des jeweiligen Einsatzes angepasst werden, sei es bei mobilen Anwendungen, Industrieanlagen oder auch Energieerzeugungsplattformen, die weniger Platz benötigen.
Ein Trend, der in den letzten Jahren ebenfalls zunehmend an Bedeutung gewonnen hat, ist die Integration von erweiterten Diagnosefunktionen im Rahmen des digitalen Zwillings. Ein digitaler Zwilling ist eine virtuelle Replik einer realen Dampfturbine, die alle relevanten Betriebsdaten in Echtzeit verfolgt und visualisiert. Mithilfe dieses Modells können Betreiber präzise Vorhersagen zu den Betriebsbedingungen treffen und potenzielle Fehlerquellen frühzeitig erkennen, was eine proaktive Wartung ermöglicht.
In einem solchen Szenario wird das Schmierölsystem nicht mehr nur als separate Komponente betrachtet, sondern als integraler Bestandteil eines umfassenden Überwachungssystems, das auch andere kritische Parameter wie die Vibrationen, Lagerzustände oder den Dampfverbrauch umfasst. Datenfusionstechniken und fortschrittliche Algorithmen tragen dazu bei, dass die Betriebsbedingungen der Turbine auf eine sehr präzise Weise überwacht und auf potenzielle Störungen reagiert werden kann, bevor sie einen Ausfall verursachen.
Diese vorausschauende Wartung auf Basis von Datenanalysen und Künstlicher Intelligenz (KI) bietet Turbinenbetreibern die Möglichkeit, den Betrieb ihrer Anlagen zu optimieren und gleichzeitig Kosten zu sparen. Es ist zu erwarten, dass solche Systeme die Lebensdauer und Verfügbarkeit von Dampfturbinen erheblich verbessern, da sie den Wartungsaufwand auf das wirklich Notwendige begrenzen.
Die Rolle des Schmierölsystems im Gesamtbetrieb von Dampfturbinen wird also immer vielseitiger und komplexer. Während das primäre Ziel weiterhin die Sicherstellung einer zuverlässigen Schmierung ist, spielen auch Energieeffizienz, Nachhaltigkeit, digitale Steuerungssysteme und präventive Wartung eine zunehmend zentrale Rolle in der Weiterentwicklung von Dampfturbinen. Dies führt zu einer langfristigen Verbesserung der Betriebsleistung, der Kostenkontrolle und der Umweltauswirkungen der Anlagen.
Kondensator der Dampfturbine
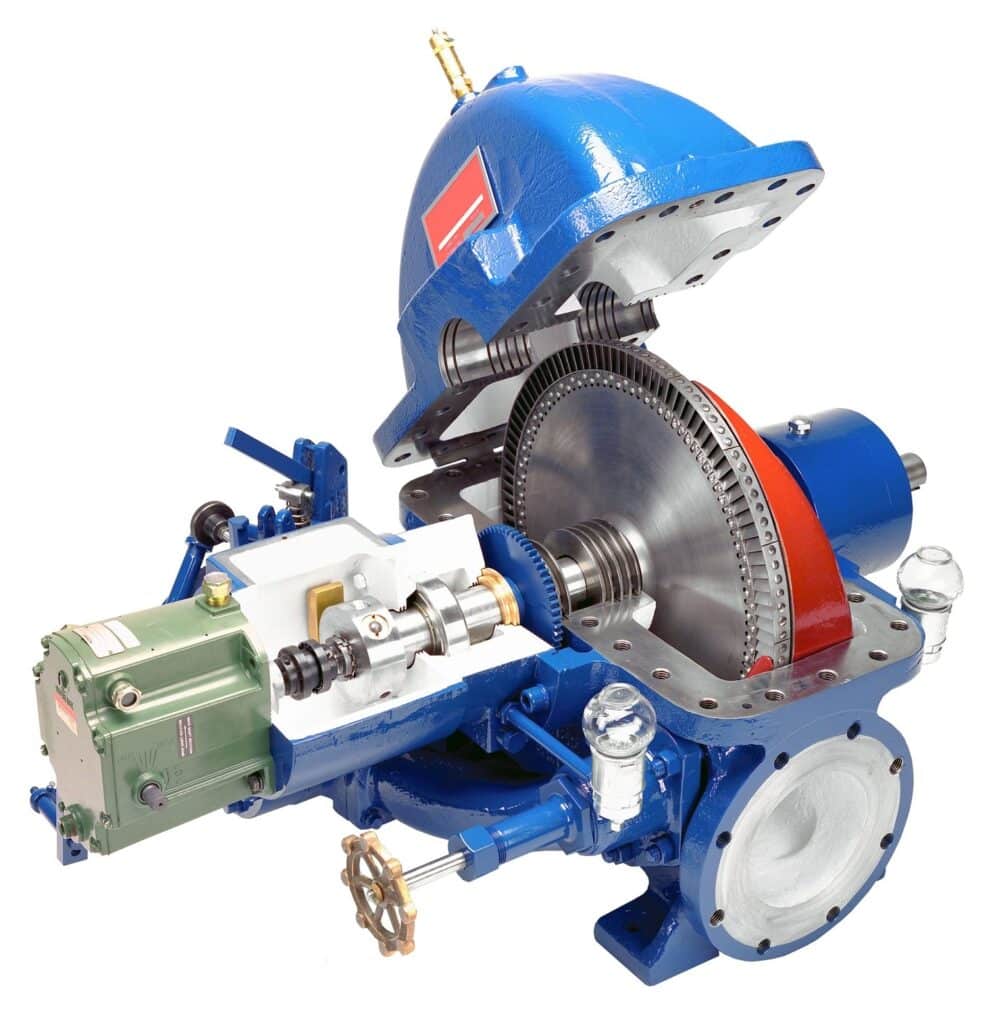
Der Kondensator in einer Dampfturbine spielt eine entscheidende Rolle im thermodynamischen Prozess, indem er den Dampf, der die Turbine verlassen hat, in Wasser zurückverwandelt. Dies ist ein wesentlicher Schritt im Rankine-Kreisprozess, der in Dampfkraftwerken verwendet wird, um mechanische Energie in elektrische Energie umzuwandeln.
Ein Kondensator sorgt dafür, dass der Dampf in einem niedrigen Druckbereich abgekühlt wird, sodass er wieder in den flüssigen Zustand übergeht und zurück zum Speisewasserkreislauf geleitet werden kann, um erneut im Dampferzeuger (Boiler) verdampft zu werden. Der Kondensator spielt daher eine Schlüsselrolle dabei, den gesamten Kreislauf effizient und nachhaltig zu gestalten.
Funktionsweise des Kondensators
Nachdem der Dampf die Dampfturbine durchlaufen hat, hat er viel Energie verloren, jedoch immer noch eine hohe Temperatur und einen gewissen Druck. Der Kondensator kühlt diesen Dampf ab, indem er ihn in Kontakt mit einem Kühlmedium bringt – typischerweise Kühlwasser aus einem Fluss, einem See oder aus einem Kühlturm. Dabei wird die Wärme aus dem Dampf an das Kühlwasser übertragen.
Der Wärmeübertragungsprozess erfolgt durch die Kondensationsphase, in der der Dampf seine latente Wärme abgibt und in Wasser umgewandelt wird. Dieser Vorgang erfolgt, wenn der Dampf auf eine Temperatur sinkt, bei der die Verdampfungsenthalpie (also die Energie, die nötig ist, um den Dampf zu verdampfen) abgegeben werden kann. Der Dampf kondensiert und wird zu Kondensat.
Aufbau eines Kondensators
Ein typischer Kondensator in einer Dampfturbine besteht aus mehreren Rohren, die durch ein Wärmetauscherprinzip arbeiten. Der Dampf wird in die Rohre geführt, die durch das Kühlwasserbad oder den Kühlturm verlaufen. Das Kühlwasser fließt in der Regel in gegenläufiger Strömung zum Dampf, um die Wärmeübertragung zu maximieren. Die Rohre können aus Kupfer oder Edelstahl bestehen, da diese Materialien eine gute Wärmeleitfähigkeit bieten und gleichzeitig korrosionsbeständig sind.
Ein Luftkondensator ist eine spezielle Variante, bei der anstelle von flüssigem Kühlwasser Luft verwendet wird, um den Dampf zu kondensieren. Diese Art von Kondensator wird oft in kleineren Anlagen oder in Gebieten eingesetzt, wo der Zugang zu großen Mengen an Kühlwasser begrenzt ist.
Kühlmedien und Effizienz
Die Wahl des Kühlmediums hat einen erheblichen Einfluss auf die Effizienz des Kondensators und des gesamten Dampfkraftwerks. Kühlwasser, das aus natürlichen Quellen stammt, hat in der Regel eine bessere Wärmeaufnahmefähigkeit als Luft und ermöglicht eine schnellere und effizientere Wärmeabgabe. Allerdings ist der Zugang zu solchen Quellen nicht immer gegeben, und in trockenen Gebieten oder bei Umweltschutzauflagen kann die Nutzung von Luftkühlern erforderlich sein.
Ein weiteres Konzept, das die Effizienz eines Kondensators verbessert, ist die Zwangskühlung, bei der das Kühlwasser durch Pumpsysteme in den Kondensator befördert wird, um eine kontinuierliche Zirkulation und eine konstante Abkühlung des Dampfes zu gewährleisten.
Druck- und Temperaturregelung
Der Druck im Kondensator sollte so niedrig wie möglich gehalten werden, um die Kondensationstemperatur des Dampfes zu maximieren und den Thermodynamischen Wirkungsgrad der Turbine zu verbessern. Ein niedriger Druck im Kondensator hilft dabei, den Dampf schneller zu kondensieren und den Betrieb der Dampfturbine zu optimieren. Der ideale Druck hängt jedoch von der Art des Dampfkraftwerks und den spezifischen Anforderungen ab.
In modernen Dampfturbinen werden Vakuumkondensatoren verwendet, bei denen ein Unterdruck erzeugt wird, um die Verdampfungstemperatur zu senken und eine effizientere Nutzung der Turbinenleistung zu ermöglichen. Ein solches Vakuum hilft dabei, den Dampfdruck nach der Turbine weiter zu senken und dadurch die Energiegewinnung zu maximieren.
Probleme und Herausforderungen
Obwohl der Kondensator eine effiziente Möglichkeit bietet, den Dampf in Wasser zurückzuverwandeln, gibt es eine Reihe von Herausforderungen, die im Betrieb beachtet werden müssen:
- Korrosion und Ablagerungen: Im Kondensator können sich mit der Zeit Korrosion und Ablagerungen von Mineralien und Schmutzpartikeln bilden, die die Wärmeübertragung verringern und die Effizienz des Systems beeinträchtigen. Dies wird in der Regel durch regelmäßige Reinigung und Wartung der Kondensatorrohre verhindert.
- Kühlwasserverfügbarkeit: In Regionen, in denen der Zugang zu Kühlwasser begrenzt ist oder Umweltvorschriften strenge Anforderungen an die Nutzung von Wasser stellen, kann der Kondensatorbetrieb eingeschränkt werden. Hier könnten Luftkondensatoren oder verdunstungsfreie Kühlsysteme eine sinnvolle Lösung sein, obwohl diese in der Regel weniger effizient als wassergekühlte Systeme sind.
- Betriebsstörungen: Ein weiteres Problem könnte durch den Eis- oder Schaumaufbau im Kondensator entstehen, der den Wasserfluss blockiert und die Wärmeübertragung beeinträchtigt. Auch Vibrationen durch den Dampfstrom oder durch Temperaturschwankungen können das System belasten.
- Umweltaspekte: Ein Kondensator, der große Mengen an Kühlwasser benötigt, kann negative Auswirkungen auf die lokale Umwelt haben, insbesondere wenn das Wasser erwärmt zurückgeführt wird und die ökologischen Bedingungen in den Gewässern beeinträchtigt. Um diesen Auswirkungen entgegenzuwirken, sind in vielen Fällen spezielle Kühlkreislaufsysteme erforderlich, die das Wasser nach der Verwendung wieder aufbereiten und in einem geschlossenen Kreislaufsystem wiederverwerten.
Zusammenfassung und Ausblick
Zusammenfassend lässt sich sagen, dass der Kondensator ein zentraler Bestandteil jedes Dampfturbinenkraftwerks ist. Durch die Umwandlung von Dampf in Wasser bei niedrigem Druck und niedriger Temperatur trägt er maßgeblich dazu bei, die Effizienz des gesamten Kraftwerks zu steigern. Technologische Innovationen wie Vakuumkondensation, verbesserte Materialien und digitale Überwachungssysteme könnten dazu beitragen, die Leistung und Zuverlässigkeit von Kondensatoren weiter zu optimieren, wodurch Dampfturbinenkraftwerke noch effizienter und umweltfreundlicher betrieben werden können.
Ein weiterer wichtiger Punkt bei der Weiterentwicklung von Kondensatoren in Dampfturbinen ist die Integration moderner Überwachungssysteme. Diese Technologien ermöglichen eine kontinuierliche Echtzeitüberwachung der Leistungsparameter des Kondensators, einschließlich Temperatur, Druck, Durchflussraten und der Qualität des Kühlwassers. Solche Systeme können frühzeitig auf Unregelmäßigkeiten reagieren, etwa bei Verstopfungen, Korrosion oder Temperaturabweichungen, und helfen so, Betriebsstörungen zu vermeiden. Durch prädiktive Wartungsstrategien können diese Systeme potenzielle Probleme erkennen, bevor sie zu ernsthaften Schäden oder Ausfällen führen.
Ein weiterer Innovationsschritt ist der Einsatz von fortschrittlichen Materialien für die Kondensatorrohre und -wände. Nanomaterialien und beschichtete Rohrsysteme könnten dazu beitragen, die Korrosionsbeständigkeit zu erhöhen und die Wärmeübertragung zu verbessern. Diese Technologien sind besonders in Umgebungen von Bedeutung, in denen aggressive Kühlmedien wie Salzwasser zum Einsatz kommen. Mit der Anwendung von antikorrosiven Beschichtungen oder der Verwendung von hochfesten Legierungen wird die Lebensdauer des Kondensators erheblich verlängert und die Wartungskosten gesenkt.
Die Kombination von nachhaltigen Technologien mit der Entwicklung von Kondensatordesigns hat auch das Ziel, den Wasserverbrauch zu reduzieren. In Regionen, in denen der Zugang zu Süßwasser begrenzt ist, können Technologien wie verdunstungsfreie Kühlsysteme oder Closed-Loop-Kreisläufe verwendet werden, bei denen das Kühlwasser nicht ständig durch externe Quellen ersetzt werden muss. Diese Systeme sind besonders vorteilhaft für den ökologischen Fußabdruck und reduzieren den Druck auf lokale Wasserressourcen.
Darüber hinaus können kombinierte Kühlungssysteme, die sowohl Luft- als auch Wassergekühlte Komponenten integrieren, eine Lösung für Gebiete mit begrenztem Zugang zu Kühlwasser darstellen. In solchen Hybridlösungen wird je nach den spezifischen Betriebsbedingungen des Kraftwerks entweder Luft- oder Wassergekühlte Kondensatoren bevorzugt. Eine solche Flexibilität kann dazu beitragen, die Effizienz zu maximieren, während gleichzeitig Umweltauswirkungen und Ressourcennutzung minimiert werden.
In den nächsten Jahren könnten auch digitale Zwillinge für Kondensatoren und Dampfturbinen weiterentwickelt werden. Ein digitaler Zwilling ist ein virtuelles Modell eines physischen Kondensators, das in Echtzeit mit dem tatsächlichen Gerät interagiert. Durch die kontinuierliche Datenanalyse des digitalen Zwillings können Betreiber nicht nur Betriebsdaten sammeln, sondern auch Simulationen durchführen, um die Leistung und Betriebsbedingungen des Kondensators zu optimieren und vorausschauend Anpassungen vorzunehmen.
Ein weiterer aufkommender Bereich ist die Optimierung der Kühlmittelzirkulation. Mit Hilfe von Künstlicher Intelligenz (KI) und Datenanalysen können automatisierte Systeme entwickelt werden, die die Zirkulationsgeschwindigkeit und Temperatur des Kühlwassers basierend auf den aktuellen Betriebsbedingungen dynamisch anpassen. Diese Technologie könnte zu einer höheren Energieeffizienz und einer verbesserten Gesamtleistung des Dampfkraftwerks führen, indem sie den Wärmeübertragungsprozess im Kondensator stets optimiert.
Die Energieeffizienz von Dampfturbinenkraftwerken könnte zusätzlich durch die Integration von Abwärmenutzung verbessert werden. Eine solche Nutzung würde die überschüssige Wärme aus dem Kondensator und anderen Anlagenteilen in wärmegeführte Prozesse oder sogar in Beheizungssysteme für benachbarte Industrien oder Wohngebäude umwandeln. Dies könnte nicht nur die Gesamteffizienz des Systems steigern, sondern auch zur Reduktion des Energieverbrauchs und der Betriebskosten beitragen.
Schließlich ist es von Bedeutung, dass die Betriebsbedingungen und technologischen Anforderungen der Dampfturbinen und ihrer Kondensatoren in den kommenden Jahren noch stärker auf eine nachhaltige Energieerzeugung ausgerichtet werden. Der Übergang zu umweltfreundlicheren Kühltechnologien, die Wasserverbrauch minimieren und gleichzeitig die Leistung und Effizienz der Dampfturbinen optimieren, wird eine Schlüsselrolle für die Zukunft der Energieerzeugung spielen.
Die Integration von erneuerbaren Energiequellen in Dampfkraftwerke, wie etwa die Nutzung von Solarenergie oder Geothermie, könnte auch Einfluss auf den Betrieb von Kondensatoren haben. In solchen hybridisierten Systemen könnte die Dampfturbine als ergänzende Technologie genutzt werden, um eine konstante und stabile Energiequelle bereitzustellen, die bei schwankender Leistung erneuerbarer Quellen wie Solar- oder Windenergie eine unterstützende Rolle übernimmt. In diesem Kontext würde der Kondensator weiterhin entscheidend dazu beitragen, die Flexibilität und Stabilität des Kraftwerks zu gewährleisten, indem er eine effiziente Rückführung von Wasser und Wärme ermöglicht.
Ein weiterer interessanter Aspekt ist die Rolle von abwärmeoptimierenden Systemen, die die Verwertung von Abwärme aus der Dampfturbine und dem Kondensator verbessern. So könnten in industriellen Anwendungen die Abwärmeprozesse mit Kraft-Wärme-Kopplung (KWK) kombiniert werden, um Zusatzenergie zu erzeugen, die für andere Produktionsprozesse oder zur Beheizung von Gebäuden genutzt wird. In einem solchen Szenario könnten Dampfturbinen und Kondensatoren nicht nur zur Stromerzeugung, sondern auch zur steigenden Energieeffizienz in der Industrie beitragen.
Technologische Entwicklungen im Bereich der Wärmerückgewinnungssysteme werden zunehmend effizienter, da neue Materialien wie Graphen und hochtemperaturbeständige Legierungen verwendet werden, um die Wärmeleitfähigkeit zu steigern und den Wärmeverlust zu minimieren. Diese Fortschritte helfen, die Gesamtenergieeffizienz von Dampfkraftwerken weiter zu verbessern, insbesondere wenn es darum geht, Abwärme in einem möglichst geschlossenen Kreislaufsystem zu nutzen.
Die Zukunft von Dampfturbinen und ihren Kondensatoren wird auch stark von der Digitalisierung und der intelligenten Steuerungstechnik geprägt sein. Hier kommen automatisierte Steuerungssysteme ins Spiel, die alle Betriebsparameter – von der Kondensattemperatur bis zur Wassertemperatur des Kühlmittels – in Echtzeit überwachen. Mithilfe von dynamischen Algorithmen und KI-gestützter Analyse können solche Systeme kontinuierlich die Betriebsweise des gesamten Systems optimieren, um eine maximale Energieeffizienz und einen optimierten Wartungsbedarf zu gewährleisten.
Darüber hinaus werden Abwärme-Systeme zunehmend als Teil des grünen Wirtschaftsansatzes gesehen. Die Nutzung von Kondensatorwärme oder Kraftwerksabwärme zur Beheizung von Nahwärmenetzen oder sogar zur Konditionierung von Industrieanlagen ist ein wachsender Trend, der zur Dekarbonisierung und Ressourcenschonung in der Energieproduktion beiträgt. Hierzu könnten besonders fortschrittliche Wärmepumpentechnologien eingesetzt werden, die es ermöglichen, die Abwärme auf höherer Temperatur zu nutzen und somit zusätzliche Energiepotenziale zu erschließen.
Die Weiterentwicklung von Kondensatoren könnte auch von der Forschung in der Kältetechnologie profitieren, insbesondere in Bezug auf die niedrigeren Betriebstemperaturen und die effiziente Entkondensation von Dampf. Technologische Innovationen im Bereich der Niedrigtemperatur-Wärmeübertragung könnten die Leistungsfähigkeit von Kondensatoren in Dampfturbinen erheblich steigern und dazu beitragen, die Thermodynamische Effizienz des gesamten Prozesses zu erhöhen.
Auswirkungen auf die Umwelt
Die Auswirkungen des Kondensatorbetriebs auf die Umwelt sind ein weiterer Bereich, der verstärkt in den Fokus rückt. Die Nutzung von umweltfreundlicheren Kühlmitteln und geringeren Wasserverbrauch durch effizientere Systeme zur Rückkühlung könnten eine erhebliche Reduktion des ökologischen Fußabdrucks von Dampfturbinenkraftwerken bedeuten. Besonders in Küstenregionen oder Gegenden mit Wassermangel ist es von großer Bedeutung, innovative Lösungen zur Minimierung des Wasserverbrauchs und zur Vermeidung von Wärmebelastungen für natürliche Gewässer zu entwickeln.
Der technologische Wandel hin zu nachhaltigeren Kühlmethoden, etwa durch den verstärkten Einsatz von luftgekühlten Kondensatoren oder geschlossenen Kreislaufsystemen, trägt zur Minderung der negativen Umwelteinflüsse bei und fördert eine umweltbewusste Energieerzeugung. Diese Technologien sind zwar in der Regel weniger effizient als wassergekühlte Systeme, jedoch werden kontinuierliche Entwicklungen in der Kühltechnologie dazu beitragen, dass auch diese Ansätze immer leistungsfähiger und umweltfreundlicher werden.
Ein weiterer entscheidender Aspekt ist die Reduzierung von Emissionen im Betrieb von Dampfturbinen und Kondensatoren. Durch die Anwendung von CO₂-absorbierenden Technologien und die Optimierung der Wärmerückgewinnung könnten Dampfkraftwerke als Teil einer dekarbonisierten Energieinfrastruktur eine tragende Rolle spielen. Hierbei ist auch die Integration von CO₂-Abscheidetechnologien wichtig, die dazu beitragen, die CO₂-Emissionen von Kraftwerken zu senken und die Nachhaltigkeit des gesamten Systems zu gewährleisten.
Fazit
Die Zukunft der Dampfturbinenkondensatoren wird geprägt sein von kontinuierlicher Forschung und Entwicklung im Bereich Kühltechnologien, Energieeffizienz und Nachhaltigkeit. Die Integration innovativer Materialien, die zunehmende Bedeutung von digitale Steuerungssysteme, sowie die Entwicklung effizienter Abwärme- und Kühltechnologien werden die Leistung und Umweltbilanz der Dampfturbinenkraftwerke weiter optimieren. Letztlich spielen die Kondensatoren eine Schlüsselrolle in der Schaffung einer effizienten, nachhaltigen und umweltfreundlichen Energieproduktion und sind damit eine essentielle Komponente des zukünftigen Energiesektors.
Die Zukunft der Dampfturbinenkondensatoren könnte auch von der verstärkten Integration in hybride Energiesysteme profitieren, die eine Kombination aus verschiedenen Energiequellen und -technologien umfassen. In solchen Systemen könnten Dampfturbinen neben Solar- und Windenergie auch mit Speichertechnologien wie Batterien oder Pumpspeicherkraftwerken kombiniert werden, um eine stabilere und effizientere Energieversorgung zu gewährleisten. In solchen Hybridlösungen würde der Kondensator weiterhin eine zentrale Rolle bei der Abkühlung und Rückgewinnung von Wasser spielen, während die Flexibilität des Gesamtsystems dazu beitragen würde, auf Schwankungen in der Energieerzeugung reagieren zu können.
Ein weiterer bedeutender Trend in der Weiterentwicklung von Dampfturbinenkondensatoren ist die verstärkte Forschung in Richtung systemübergreifender Optimierung. Hierbei wird nicht nur der Kondensator selbst optimiert, sondern auch die Wechselwirkungen zwischen allen Komponenten eines Dampfkraftwerks – vom Dampferzeuger über die Turbine bis hin zum Kondensator und den Nachwärmesystemen. Solche integrierten Lösungen würden die Gesamtenergieeffizienz des Kraftwerks erhöhen, indem Fehlanpassungen zwischen den Komponenten minimiert und Synergien zwischen den verschiedenen Teilen des Systems genutzt werden.
Die Verbesserung der Kondensatorleistung ist nicht nur auf technologische Innovationen angewiesen, sondern auch auf strategische Betriebsansätze. Der Betrieb und die Wartung von Dampfturbinenkondensatoren unterliegt einer zunehmenden Automatisierung und dem Einsatz von Robotertechnologien zur Inspektion und Wartung. Roboter könnten genutzt werden, um schwer zugängliche Bereiche des Kondensators zu überprüfen, Schadstellen zu identifizieren und sogar Reparaturen durchzuführen, ohne den Betrieb des Kraftwerks zu stören. Diese Technologien könnten dazu beitragen, die Betriebszeiten zu maximieren und gleichzeitig Ausfallzeiten zu minimieren.
Recyceln von Wärme und Wasser
Ein wachsender Bereich der Dampfturbinenforschung ist auch das Wärme- und Wasserrückgewinnungssystem, das darauf abzielt, die Abwärme des Kondensators für andere industrielle Anwendungen oder städtische Infrastrukturen zu nutzen. In Großstädten, die über umfangreiche Fernwärmenetze verfügen, könnte überschüssige Wärme aus dem Dampfkraftwerk zur Beheizung von Wohnungen und öffentlichen Einrichtungen genutzt werden. Ein geschlossenes Wasserkreislaufsystem würde dabei nicht nur den Wasserverbrauch minimieren, sondern auch die Kühlwasserqualität aufrechterhalten, wodurch das Risiko von Verunreinigungen oder Korrosion im System verringert wird.
Die Optimierung der Kühlung ist ein weiteres zentrales Thema der Forschung, insbesondere angesichts des globalen Trends zu Klimawandel und extremen Wetterbedingungen. Durch die Entwicklung von adaptiven Kühlsystemen, die ihre Kühlleistung dynamisch an die Umgebungstemperaturen anpassen können, ließen sich die Effizienz und Betriebsbedingungen eines Kondensators selbst unter extremen Wetterbedingungen stabil halten. Solche Systeme könnten die Wärmeabgabe auch bei steigenden Außentemperaturen aufrechterhalten und somit die Gesamtleistung des Dampfkraftwerks auch in heißen Sommermonaten sichern.
Nachhaltige Energietechnologien und der Weg in die Zukunft
Ein bedeutender Teil der Weiterentwicklung von Dampfturbinenkondensatoren wird auch die Verlagerung auf nachhaltige Energietechnologien sein. In der Zukunft könnte es zunehmend wichtig werden, dass Dampfkraftwerke und ihre Kondensatoren mit CO₂-freien oder CO₂-neutralen Brennstoffen betrieben werden. Beispielsweise könnte die Verwendung von Wasserstoff als Brennstoff für Dampfturbinen eine langfristige Lösung darstellen, um Treibhausgasemissionen drastisch zu reduzieren. Auch die Abscheidung und Speicherung von CO₂ (CCS) könnte eine Schlüsselrolle bei der Senkung der Emissionen von Dampfturbinenkraftwerken spielen, indem das CO₂ vor der Freisetzung in die Atmosphäre entfernt und in unterirdische Lagerstätten verbracht wird.
Gleichzeitig könnte der Einsatz von Biomasse oder anderen erneuerbaren Brennstoffen wie biogenen Abfällen zur Dampferzeugung einen wichtigen Beitrag zur Dekarbonisierung leisten und gleichzeitig die Notwendigkeit reduzieren, fossile Brennstoffe zu nutzen. Dampfturbinen, die mit diesen alternativen Brennstoffen betrieben werden, müssen jedoch speziell für diese Materialien angepasst werden, was auch neue Anforderungen an die Kondensatortechnologie mit sich bringt, insbesondere in Bezug auf die Verbesserung der Effizienz bei unterschiedlichen Brennstoffen.
Ein solcher Übergang zu nachhaltigen Kraftwerkslösungen wird nicht nur von der technologischen Entwicklung abhängen, sondern auch von politischen und wirtschaftlichen Faktoren. Subventionen für grüne Technologien, regulatorische Anforderungen zur Emissionsreduzierung und die Verfügbarkeit von Fördermitteln könnten die Weiterentwicklung von umweltfreundlichen Dampfturbinen und effizienten Kondensatorsystemen maßgeblich vorantreiben. Gleichzeitig könnte der internationale Austausch von Best Practices und Innovationen dazu beitragen, dass die neuesten Technologien auch in Entwicklungsländern und Schwellenländern zugänglich werden, was zu einer breiteren Umsetzung nachhaltiger Energielösungen führt.
Fazit
Zusammenfassend lässt sich sagen, dass die Zukunft der Dampfturbinenkondensatoren durch eine Vielzahl von Innovationen und Anpassungen geprägt sein wird. Die stetige Weiterentwicklung von Kühltechnologien, materialtechnischen Verbesserungen, intelligenten Steuerungssystemen und nachhaltigen Energielösungen wird dazu beitragen, dass Dampfturbinenkraftwerke effizienter, umweltfreundlicher und robuster gegenüber den Herausforderungen des Klimawandels werden. In Kombination mit den weltweit steigenden Anforderungen an Energieeffizienz und Umweltschutz werden Dampfturbinen und ihre Kondensatoren auch in der Zukunft eine zentrale Rolle bei der Stromerzeugung und Energieversorgung spielen.
Turbinenwelle der Dampfturbine

Die Turbinenwelle einer Dampfturbine ist ein zentrales mechanisches Bauteil, das die mechanische Energie, die durch den Dampfstrom erzeugt wird, auf den Generator oder andere gekoppelte Maschinen überträgt. Sie verbindet die Turbinenrotoren, die durch den Dampfdruck in Bewegung gesetzt werden, mit der Antriebsmaschine und ist damit für die Energieumwandlung von thermischer Energie zu mechanischer Energie verantwortlich. Im Allgemeinen ist die Turbinenwelle einer Dampfturbine ein hochbelastetes, rotierendes Bauteil, das einer Vielzahl von mechanischen und thermischen Belastungen ausgesetzt ist.
Materialanforderungen an die Turbinenwelle
Da die Turbinenwelle sowohl mechanischen als auch thermischen Belastungen ausgesetzt ist, müssen für ihre Herstellung hochfeste Legierungen verwendet werden, die sowohl eine hohe Zugfestigkeit als auch eine gute Korrosionsbeständigkeit aufweisen. Häufig werden Materialien wie Nickel- oder Kobaltbasis-Legierungen, rostfreie Stähle oder hochlegierte Stähle mit Chrom, Molybdän und Vanadium verwendet, die dafür sorgen, dass die Welle hohen Temperaturen und Drücken standhält. Zusätzlich müssen sie in der Lage sein, den kontinuierlichen Drehbewegungen und den mechanischen Schwingungen zu widerstehen.
Design und Konstruktion der Turbinenwelle
Die Konstruktion einer Turbinenwelle ist komplex und muss sicherstellen, dass sie nicht nur den mechanischen Anforderungen gerecht wird, sondern auch effizient und zuverlässig arbeitet. Sie besteht in der Regel aus mehreren Bereichen, die unterschiedliche Aufgaben übernehmen:
- Rotorbereich: Dieser Bereich der Welle trägt den Rotor der Turbine, der durch den Dampfdruck in Drehung versetzt wird. Der Rotorbereich muss eine hohe Drehzahl und Zentrifugalkräfte aushalten und ist oft mit Turbinenblättern ausgestattet, die die kinetische Energie des Dampfs aufnehmen und in mechanische Arbeit umwandeln.
- Tragerollenbereich: In diesem Abschnitt wird die Welle von Lagern oder Tragerollen gestützt, die den Rotorbereich stützen und die Welle in ihrer Drehbewegung stabilisieren. Die Lager müssen hohe Radial- und Axialkräfte aufnehmen können, die durch die Drehbewegung der Welle entstehen.
- Kopfbereich: Der Kopfbereich ist oft der Teil der Welle, der mit der Generatorwelle oder anderen Kopplungen verbunden ist, um die erzeugte mechanische Energie zu übertragen. In diesem Abschnitt sind häufig Verbindungen zur Kraftübertragung mit anderen Maschinen vorhanden, zum Beispiel durch Kupplungen oder Riemen.
Belastung und Materialermüdung
Die Turbinenwelle unterliegt während ihres Betriebs sowohl axialen als auch radialen Kräften, was zu einer hohen mechanischen Belastung führt. Diese Belastungen resultieren aus der Drehbewegung, den Dampfdruckänderungen und den Temperaturschwankungen, die während des Betriebs der Dampfturbine auftreten. Thermische Spannungen und Zyklen von Aufheizung und Abkühlung können die Materialstruktur der Welle zusätzlich belasten.
Ein kritischer Faktor für die Lebensdauer der Turbinenwelle ist die Materialermüdung. Diese tritt auf, wenn die Welle wiederholt hohen mechanischen oder thermischen Belastungen ausgesetzt wird, was zu Mikrorissen oder Strukturschäden führen kann. Um diesen zu begegnen, werden härtende Beschichtungen und Oberflächenbehandlungen wie Nitrieren oder Verchromen eingesetzt, um die Widerstandsfähigkeit der Welle gegenüber Abnutzung und Korrosion zu erhöhen.
Schmierung der Turbinenwelle
Die Turbinenwelle muss während des Betriebs in den Lagern ordnungsgemäß geschmiert werden, um Reibung und Verschleiß zu minimieren und die Lebensdauer der Welle zu verlängern. In modernen Dampfturbinen werden dafür hochwertige Schmieröle oder Schmierfette eingesetzt, die nicht nur eine reibungslosen Betrieb der Welle gewährleisten, sondern auch für Kühlung sorgen. Die Schmierung sorgt dafür, dass die Lager und Dichtungen effektiv arbeiten und die Welle vor übermäßiger Abnutzung und Überhitzung geschützt wird.
Auswuchten und Balancierung der Welle
Eine wichtige Maßnahme zur Vermeidung von mechanischen Erschütterungen und Vibrationen ist das Auswuchten der Turbinenwelle. Ungleichgewichte in der Welle können zu Vibrationen und unnötigen Belastungen führen, die nicht nur die Turbine selbst beschädigen, sondern auch die Betriebsstabilität und Effizienz beeinträchtigen können. Aus diesem Grund wird die Welle während ihrer Herstellung und nach der Montage in einem Auswuchtprozess geprüft, um sicherzustellen, dass sie während des Betriebs gleichmäßig und ohne zusätzliche Belastungen dreht.
Betriebsoptimierung und Innovationen
In der modernen Turbinenentwicklung wird intensiv an der Optimierung der Wellenkonstruktion gearbeitet, um die Betriebsbedingungen weiter zu verbessern. So werden z.B. neue computergestützte Simulationen eingesetzt, um die Struktur und Dynamik der Welle besser zu verstehen und Schwingungen sowie Temperaturanstiege zu minimieren. Auch die Verwendung von Leichtbauwerkstoffen und innovativen Fertigungstechniken wie 3D-Druck oder Kombinationen von Legierungen trägt dazu bei, dass die Turbinenwellen leichter, stabiler und leistungsfähiger werden.
Korrosionsschutz und Lebensdauer
Da Dampfturbinen in sehr feuchten und hochtemperierten Umgebungen arbeiten, ist der Korrosionsschutz der Turbinenwelle von höchster Bedeutung. Korrosionsbeständige Materialien und Beschichtungen werden eingesetzt, um die Welle vor aggressiven Dampf- und Wasserchemikalien zu schützen. Im Vergleich zu früheren Materialien sind die aktuellen Kombinationen aus rostfreien Stählen und Legierungen widerstandsfähiger gegen Korrosion und Oxidation, was die Lebensdauer der Welle erheblich verlängert.
Zusammenfassung
Die Turbinenwelle ist eine der wichtigsten Komponenten einer Dampfturbine und spielt eine entscheidende Rolle bei der Energieübertragung und Leistungsfähigkeit der gesamten Anlage. Die kontinuierliche Forschung und Entwicklung in Bezug auf Materialien, Schmierung, Temperaturbeständigkeit und Korrosionsschutz ermöglicht es, die Lebensdauer der Turbinenwelle zu verlängern und die Betriebsstabilität sowie Effizienz von Dampfturbinen weiter zu steigern.
Die Optimierung der Turbinenwelle umfasst nicht nur die Verbesserung der mechanischen Eigenschaften, sondern auch die Berücksichtigung von Umweltfaktoren und Betriebsbedingungen, die die Welle über ihre gesamte Lebensdauer hinweg beeinflussen können. Ein bedeutender Faktor hierbei ist die Temperaturbeständigkeit, da die Dampfturbine konstant hohen Temperaturen ausgesetzt ist, die in Verbindung mit hohen Drücken eine zusätzliche Herausforderung für die Langzeitstabilität der Welle darstellen. Um dieser Anforderung gerecht zu werden, kommen hochfeste Materialien mit einer hohen Schmelztemperatur zum Einsatz, die der Thermomechanischen Belastung standhalten können. Techniken wie die Verstärkung der Oberflächen durch thermische Beschichtungen oder Kaltverformung ermöglichen eine höhere Beständigkeit gegenüber diesen extremen Bedingungen und fördern gleichzeitig die Lebensdauer und Zuverlässigkeit der Turbinenwelle.
Ein weiterer wichtiger Aspekt in der Optimierung der Wellenkonstruktion ist die Minimierung von Wärmeverlusten und die Verbesserung der Wärmeleitfähigkeit, was zu einer besseren Energieeffizienz führt. Durch die Anwendung von thermodynamischen Simulationen und Computermodellen wird die Wärmeverteilung innerhalb der Welle genauestens analysiert. Dies ermöglicht es, die Dampftemperaturen und Druckverhältnisse entlang der Turbine zu überwachen und zu steuern, um eine maximale Energieausbeute zu gewährleisten. Auch die Kühlung der Welle wird zunehmend durch den Einsatz von Flüssigkeitskühlung oder innovativen Kühltechnologien optimiert, die dazu beitragen, eine Überhitzung der Welle und damit verbundene Schäden zu vermeiden.
Die Überwachung der Turbinenwelle hat in den letzten Jahren durch die Integration von sensorischen Technologien und digitaler Vernetzung stark zugenommen. Drehzahl- und Vibrationssensoren sowie Temperatur- und Druckmessgeräte ermöglichen eine kontinuierliche Überwachung des Betriebszustands der Welle. Diese intelligente Überwachung ermöglicht es, potenzielle Probleme frühzeitig zu erkennen und Wartungsmaßnahmen präzise und rechtzeitig zu ergreifen, bevor es zu einem Ausfall kommt. Predictive Maintenance (vorausschauende Wartung) ist eine Schlüsseltechnologie, die es ermöglicht, die Wartungsintervalle genau zu berechnen und nur dann einzugreifen, wenn es wirklich notwendig ist. Dies reduziert Betriebsunterbrechungen und Kosten und steigert gleichzeitig die Verfügbarkeit der Dampfturbine.
Die fortschreitende Entwicklung von Nanotechnologie und hochentwickelten Materialien könnte in Zukunft ebenfalls die Struktureigenschaften der Turbinenwelle weiter verbessern. Durch den Einsatz von nanostrukturierten Beschichtungen oder Nano-Legierungen kann die Korrosionsbeständigkeit und Festigkeit weiter erhöht werden, was der Welle zu einer noch längeren Lebensdauer und besseren Leistungsfähigkeit verhelfen könnte. Zusätzlich sind auch Reparaturtechniken wie Laserauftragschweißen und 3D-Druck von Ersatzteilen zunehmend relevant, da sie es ermöglichen, Beschädigungen oder Abnutzungsschäden direkt vor Ort zu beheben und somit die Betriebszeiten der Turbine weiter zu verlängern.
Ein weiterer Trend in der Entwicklung von Turbinenwellen ist die Integration von Leichtbau-Technologien. Durch die Verwendung von Leichtmetallen oder Kohlenstofffaserverstärkten Kunststoffen könnte die Gesamtmasse der Welle reduziert werden, was zu einer höheren Effizienz und einem verbesserten Ansprechverhalten führt. Leichtere Wellen benötigen weniger Energie, um sich zu beschleunigen, was zu einer höheren Dynamik und geringeren Vibrationsbelastungen führt. Diese Innovationen sind vor allem in der Entwicklung von kleineren, mobilen Dampfturbinen oder hybriden Energiesystemen von Bedeutung, in denen Gewicht und Kompaktheit eine größere Rolle spielen.
Abschließend lässt sich sagen, dass die Zukunft der Turbinenwelle durch kontinuierliche Innovationen in Materialwissenschaften, Fertigungstechnologien und Überwachungssystemen geprägt sein wird. Die zunehmende Verwendung von intelligenten und nachhaltigen Technologien in Verbindung mit effizienten Wartungsstrategien wird nicht nur die Leistungsfähigkeit und Lebensdauer von Turbinenwellen weiter steigern, sondern auch dazu beitragen, die Energieproduktion aus Dampfturbinen ökologisch und wirtschaftlich nachhaltiger zu gestalten.
Ein weiterer bedeutender Trend in der Entwicklung von Turbinenwellen ist die fortschreitende Energieeffizienz der Dampfturbinen insgesamt. Hierbei spielt die Welle eine Schlüsselrolle, da sie die mechanische Energie, die durch die Dampfturbine erzeugt wird, direkt in nutzbare Energie überträgt. Um die Effizienz weiter zu steigern, konzentriert sich die Forschung auf die Minimierung von Energieverlusten während der Übertragung und die Vermeidung von unnötigen Reibungsverlusten durch eine präzisere Lagerung und Auswuchtung der Welle. Fortschritte bei der Entwicklung von leichten Wellenmaterialien und der Integration von intelligenten Steuerungssystemen könnten dazu beitragen, die Energieübertragung zu optimieren und den Gesamtwirkungsgrad der Turbine zu erhöhen.
In Verbindung mit diesen technischen Fortschritten gibt es eine zunehmende Forderung nach flexibleren Dampfturbinen, die in der Lage sind, ihre Leistung je nach Bedarf anzupassen. Dies ist besonders wichtig im Hinblick auf den steigenden Anteil erneuerbarer Energien wie Wind und Solarenergie, die schwankende Erzeugungsmuster aufweisen. Eine dynamische Anpassung der Turbinenwelle und ihrer Betriebsparameter wird durch die Verwendung von intelligenten Sensornetzwerken und automatischen Steuerungssystemen erleichtert, die es der Turbine ermöglichen, sich schnell an wechselnde Bedingungen anzupassen und somit die Effizienz in spitzenlastbetriebene Szenarien zu maximieren.
Zusätzlich ist die Integration von Industrie 4.0 und digitaler Kommunikation von wachsender Bedeutung. Die Vernetzung der Turbinenwellen und der gesamten Dampfturbinenanlage ermöglicht die Sammlung von Echtzeitdaten zu Betriebsbedingungen, Temperaturen, Drehzahlen und Vibrationen. Diese Daten werden durch Cloud-basierte Analysen ausgewertet, was es den Betreibern ermöglicht, Leistungsdaten und verschleißbedingte Veränderungen sofort zu erkennen. Die Integration von Künstlicher Intelligenz (KI) in die Analyseprozesse ermöglicht es, Frühwarnsysteme zu entwickeln, die potenzielle Fehler oder Verschleißerscheinungen in der Turbinenwelle vorausschauend identifizieren. Dies führt zu einer erhöhten Zuverlässigkeit und einer Reduktion unerwarteter Ausfälle.
Ein wachsender Bereich der Turbinenentwicklung ist auch die nachhaltige Produktion und der Recyclingaspekt von Turbinenwellen. In der Zukunft könnte die Rückgewinnung von Materialen aus alten Wellen durch Recycling eine wichtige Rolle spielen, da dies nicht nur die Umweltbelastung reduziert, sondern auch die Kosten für die Herstellung neuer Wellenmaterialien verringert. Die Entwicklung von recycelbaren Legierungen und die Optimierung der Fertigungstechnologien können dazu beitragen, den ökologischen Fußabdruck der Dampfturbinenproduktion zu minimieren.
Die zunehmende Bedeutung von Sicherheitsaspekten in der Dampfturbinenindustrie führt ebenfalls dazu, dass die Turbinenwelle kontinuierlich verbessert wird, um Sicherheitsrisiken wie Überhitzung, Kavitation oder mechanische Ausfälle zu vermeiden. Fortgeschrittene Überwachungssysteme und automatische Notabschaltungen gewährleisten, dass die Welle niemals über ihre maximalen Betriebsgrenzen hinaus beansprucht wird, was die Betriebsbedingungen sicherer macht und das Risiko von Schäden an der Turbine minimiert. Weiterhin wird in der Forschung verstärkt an Fehlerdiagnosesystemen gearbeitet, die mit Machine Learning die Fehlerursachen in der Turbinenwelle erkennen und Wartungsintervalle entsprechend anpassen.
Ein weiterer Aspekt ist die zunehmende Modularität von Dampfturbinen und ihrer Wellenkomponenten. Durch den Einsatz modularer Systeme können einzelne Teile der Turbine, einschließlich der Welle, schneller gewartet oder ausgetauscht werden, was zu einer höheren Betriebsflexibilität und reduzierten Ausfallzeiten führt. Diese Anpassungsfähigkeit wird besonders bei der Nachrüstung von Bestandsanlagen mit neuen, leistungsfähigeren Turbinenkomponenten wichtig, um die Effizienz und Leistungskapazitäten von bestehenden Dampfkraftwerken zu steigern.
Die Zukunft der Turbinenwelle in Dampfturbinen ist stark von der Innovation in der Materialwissenschaft, der digitalen Vernetzung, der Energieeffizienz und der Nachhaltigkeit geprägt. Fortschritte in diesen Bereichen werden dazu beitragen, dass Dampfturbinen künftig noch effizienter, flexibler und langlebiger arbeiten, wodurch sie weiterhin eine zentrale Rolle in der Energieerzeugung spielen können, insbesondere im Hinblick auf die Herausforderungen der Energiewende und die zunehmende Integration erneuerbarer Energien in das globale Stromnetz.
Ein weiterer wichtiger Trend in der Dampfturbinenentwicklung ist die zunehmende Automatisierung der Betriebs- und Wartungsprozesse. Dies schließt sowohl die Überwachung der Turbinenwelle als auch den Betriebsablauf der gesamten Dampfturbine ein. Automatisierte Systeme können die Effizienz der Turbine erheblich steigern, indem sie Daten in Echtzeit sammeln und auswerten, sodass Anpassungen schnell und präzise vorgenommen werden können, um die Leistungsfähigkeit der Turbine zu maximieren. Die Anwendung von KI zur Steuerung und Optimierung von Betriebsparametern wie Dampfdruck, Temperatur und Drehzahl sorgt dafür, dass die Turbine in jedem Betriebszustand den optimalen Wirkungsgrad erreicht.
Automatisierung hilft auch bei der frühzeitigen Erkennung von Anomalien oder Fehlern im Betrieb der Turbinenwelle, wodurch potenzielle Schäden oder Ausfälle frühzeitig erkannt werden können. Dies führt zu einer besseren Fehlerdiagnose und reduziert die Notwendigkeit für manuelle Inspektionen, die oft zeitaufwendig und fehleranfällig sind. So können Wartungs- und Reparaturmaßnahmen gezielt und ohne unnötige Verzögerungen eingeplant werden, was zu einer reduzierten Stillstandszeit und höherer Anlagenverfügbarkeit führt.
Ein weiterer wachsender Bereich betrifft die Integration von erneuerbaren Energiequellen in Dampfturbinenanlagen. In vielen modernen Kraftwerken wird die Dampfturbine nicht nur mit fossilen Brennstoffen, sondern auch mit Biomasse, Abfallstoffen oder sogar mit Geothermie betrieben. Diese Umstellung erfordert eine Anpassung der Turbinenwelle und der gesamten Turbinenkonstruktion, um mit den unterschiedlicheren und häufig fluktuierenden Brennstoffen umgehen zu können. Die Flexibilität der Dampfturbinenwelle, die sich an die verschiedenen Betriebsbedingungen anpasst, wird zu einem entscheidenden Faktor für die Zukunftsfähigkeit dieser Anlagen.
Ein weiteres Augenmerk liegt auf der Entwicklung von Hybrid-Systemen, bei denen Dampfturbinen mit anderen Formen der Energieerzeugung, wie Gasturbinen oder Solarkraftwerken, kombiniert werden. Solche hybriden Systeme können die Vorteile der Dampfturbine, wie ihre hohe Effizienz und Zuverlässigkeit, mit den Vorteilen von erneuerbaren Quellen verbinden. Hierbei spielt die Turbinenwelle eine entscheidende Rolle, da sie in der Lage sein muss, sich mit verschiedenen Energiequellen und Betriebsmodi zu kombinieren und den Anforderungen eines hybriden Systems gerecht zu werden.
In einer grüneren Zukunft wird ein Fokus auch auf die Nachhaltigkeit der gesamten Dampfturbinenproduktion gelegt. Neben der Reduzierung der CO2-Emissionen und der Steigerung der Energieeffizienz wird immer mehr Wert auf umweltfreundliche Materialien und recyclingfähige Komponenten gelegt. Eine zunehmend wichtige Rolle spielen dabei biobasierte Schmierstoffe und umweltfreundliche Kühlmittel, die die Umweltauswirkungen der Dampfturbinenbetrieb reduzieren sollen. Auch die Forschung an nachhaltigen Herstellungsverfahren, die den Materialeinsatz optimieren und den Abfall minimieren, gewinnt zunehmend an Bedeutung.
Ein weiterer innovativer Bereich betrifft die Integration von digitalen Zwillingen in die Turbinenwellenentwicklung. Ein digitaler Zwilling ist eine virtuelle Kopie der Dampfturbine, einschließlich der Turbinenwelle, die alle relevanten Daten und Parameter des realen Systems in Echtzeit widerspiegelt. Diese Technologie ermöglicht eine simulierte Nachbildung des Betriebs, wodurch die Turbinenwelle unter verschiedenen Betriebsbedingungen getestet und optimiert werden kann, ohne das echte System gefährden zu müssen. Darüber hinaus kann die Lebensdauer der Turbine simuliert und vorausschauend geplant werden, um die Wartung und Reparatur effektiver und effizienter durchzuführen.
Die zunehmende Forderung nach flexiblen Energiequellen für die Industrie und die Herausforderungen durch den steigenden Anteil erneuerbarer Energiequellen verlangen eine verstärkte Energieintegration und Lastverlagerung in bestehenden Dampfturbinenanlagen. Die Turbinenwelle und ihre Steuerung müssen in der Lage sein, diese wechselnden Lasten effektiv zu handhaben und gleichzeitig die Betreiberkosten zu minimieren. Damit gewinnt die Dynamik der Turbine, also die Fähigkeit, sich schnell an veränderte Lastanforderungen anzupassen, immer mehr an Bedeutung.
Nicht zuletzt ist die Sicherheitsüberwachung der Turbinenwelle ein wichtiger Bestandteil der modernen Dampfturbinenentwicklung. Neben der Überwachung von Vibrationen und Temperatur sind auch die Stabilität und Integrität der Welle zu jeder Zeit zu gewährleisten. Sensoren und Überwachungstechnologien werden immer weiter ausgebaut, um Risse oder Abnutzungserscheinungen frühzeitig zu erkennen und zu verhindern, dass diese zu katastrophalen Schäden führen. So wird auch die Sicherheit der Betreiber und die Langlebigkeit der gesamten Turbine erhöht.
Insgesamt wird die Zukunft der Dampfturbinenwelle durch technologische Innovationen und neue Anforderungen an Energieeffizienz, Flexibilität und Nachhaltigkeit geprägt. Die Integration von fortschrittlichen Materialien, intelligenten Überwachungs- und Steuerungssystemen sowie neuen Betriebsstrategien wird die Dampfturbinen zu einem noch wichtigeren Element in der globalen Energieerzeugung machen. Die ständige Weiterentwicklung dieser Technologie wird sicherstellen, dass Dampfturbinen auch weiterhin eine wesentliche Rolle in der nachhaltigen Energieproduktion der Zukunft spielen.
Laufschaufeln der Dampfturbine

Die Laufschaufeln einer Dampfturbine spielen eine zentrale Rolle bei der Umwandlung von Dampfenergie in mechanische Energie, die über die Turbinenwelle weitergeleitet wird. Diese Schaufeln sind speziell konstruiert, um den Dampfstrom optimal zu lenken und die kinetische Energie des Dampfes in eine Drehbewegung umzuwandeln. Sie sind entscheidend für die Effizienz und Leistungsfähigkeit der Dampfturbine, da die Gestaltung der Laufschaufeln direkten Einfluss auf die Energieumwandlungsrate und den Wirkungsgrad der gesamten Turbine hat.
Materialien der Laufschaufeln
Die Laufschaufeln einer Dampfturbine sind extrem hohen Temperaturen und Druckverhältnissen ausgesetzt, weshalb sie aus hochleistungsfähigen Legierungen bestehen müssen. Häufig werden Nickelbasierte Superlegierungen oder Titan-Legierungen verwendet, die eine hohe Hitzebeständigkeit, Korrosionsbeständigkeit und mechanische Festigkeit aufweisen. Diese Materialien sind so gewählt, dass sie auch unter extremen Bedingungen wie Thermal- und mechanischen Spannungen ihre Form und Funktion über einen langen Zeitraum bewahren können.
Ein weiterer wichtiger Aspekt ist die Oxidation und Korrosion der Laufschaufeln, die durch die hohen Temperaturen und den Kontakt mit feuchtem Dampf verstärkt werden. Um diesem Problem zu begegnen, werden die Schaufeln häufig mit hochgradigen Beschichtungen versehen, wie zum Beispiel Kromlegierungen, die den Schutz vor Korrosion und Abrieb erhöhen. In einigen Fällen kommen auch Keramikbeschichtungen zum Einsatz, die eine zusätzliche Wärmeisolierung bieten und die Temperaturbelastung der Schaufeln reduzieren.
Geometrie und Design der Laufschaufeln
Die Geometrie der Laufschaufeln ist entscheidend für die Effizienz und Leistungsfähigkeit einer Dampfturbine. Sie müssen so gestaltet sein, dass sie den Dampf mit minimalen Verlusten lenken und gleichzeitig die Drehbewegung der Turbine effizient erzeugen. Die Schaufeln werden in der Regel in verschiedene Sektionen unterteilt, die jeweils speziell auf den jeweiligen Druckbereich und die Dampfgeschwindigkeit abgestimmt sind.
Die Eingangsschaufeln (also die ersten Schaufeln, mit denen der Dampf in Kontakt kommt) sind meist so ausgelegt, dass sie den Dampfstrom gleichmäßig aufnehmen und die Strömungsgeschwindigkeit des Dampfes optimieren, um die mechanische Arbeit zu maximieren. Für die Ausgangsschaufeln, die am Ende des Turbinenprozesses arbeiten, ist es wichtig, den Dampf mit so wenig Energieverlust wie möglich zu entlassen, was durch eine angepasste Schaufelneigung und Strömungsführung erreicht wird.
Schaufelbelastung und -verschleiß
Ein besonders herausfordernder Aspekt der Laufschaufeln ist ihre Langlebigkeit unter extremen Betriebsbedingungen. Die Schaufeln sind während des Betriebs ständigen Schwingungen, Vibrationskräften und Thermomechanischen Belastungen ausgesetzt. Diese Belastungen können zu Verschleiß und Materialermüdung führen. Um dem vorzubeugen, werden die Schaufeln in modernen Dampfturbinen oft optimiert, um eine möglichst gleichmäßige Kraftverteilung zu gewährleisten und die Schwingungsanfälligkeit zu minimieren. Zusätzlich wird der Schaufelansatz (also der Bereich, in dem die Schaufel mit der Turbinenwelle verbunden ist) oft verstärkt, um der starken Kraftübertragung standzuhalten.
Die häufigste Art des Verschleißes ist der Erosionsverschleiß durch den Kontakt mit feinen Wassertropfen oder Staubpartikeln im Dampf, der über die Schaufeln zieht. Diese kleinen Partikel können die Oberfläche der Schaufeln im Laufe der Zeit abtragen und zu einer Verminderung der Leistung führen. Erosion und Korrosion können durch gezielte Designänderungen und Beschichtungen verringert werden, die den Kontakt mit abrasiven Materialien minimieren.
Ein weiteres Problem stellt die Thermomechanische Belastung dar. Der Temperaturgradient zwischen dem heißen Dampf und der kühleren Umgebung kann zu Verformungen und Rissen in den Schaufeln führen. Dies wird durch den Einsatz von hochfesten Materialien und konstruktiven Maßnahmen, wie zum Beispiel der Integration von Kühlkanälen innerhalb der Schaufeln, um die Temperatur zu regulieren, gemildert.
Dynamische und thermische Simulationen
Um die Belastungen auf die Laufschaufeln und ihre Lebensdauer zu maximieren, setzen Ingenieure auf dynamische und thermische Simulationen, die es ermöglichen, das Verhalten der Schaufeln unter realen Betriebsbedingungen zu modellieren. Diese Simulationen helfen dabei, die Schaufelgeometrie und Materialwahl zu optimieren und potenzielle Schwachstellen frühzeitig zu erkennen, die die Lebensdauer der Laufschaufeln beeinträchtigen könnten.
Die Anwendung von Computational Fluid Dynamics (CFD) ermöglicht eine präzise Berechnung der Strömungsdynamik des Dampfs, wodurch die Schaufelgeometrie im Hinblick auf die Dampftemperatur und -druck optimiert werden kann. Ebenso werden Finite-Elemente-Methoden (FEM) verwendet, um die mechanischen Spannungen und Deformationen der Schaufeln unter verschiedenen Lasten und Temperaturen zu simulieren und Schwachstellen zu identifizieren, die während des Betriebs zu Schäden führen könnten.
Wartung und Instandhaltung der Laufschaufeln
Die Wartung der Laufschaufeln umfasst regelmäßig Inspektionen auf Verschleiß, Risse und Korrosionsspuren. Dies erfolgt meist durch den Einsatz von ultraschallbasierten Verfahren oder endoskopischen Inspektionen, bei denen die Schaufeln auf unsichtbare Schäden überprüft werden. Bei Bedarf werden die Schaufeln dann repariert oder ausgetauscht, was eine regelmäßige Instandhaltung und Überholung der Dampfturbine erfordert, um ihre Betriebsfähigkeit zu gewährleisten.
Zukunftsorientierte Wartungstechnologien wie der Einsatz von Drohnen zur Inspektion schwer zugänglicher Teile oder die Anwendung von Smart Monitoring-Systemen zur kontinuierlichen Überwachung der Schaufeln während des Betriebs gewinnen zunehmend an Bedeutung. Solche Systeme sammeln Daten zur Schaufelbelastung und Vibration und können frühzeitig auf Fehler oder Verschleißerscheinungen hinweisen, sodass rechtzeitig Maßnahmen getroffen werden können.
Fazit
Die Laufschaufeln sind ein kritischer Bestandteil jeder Dampfturbine. Ihre Effizienz, Lebensdauer und Betriebsfähigkeit hängen von einer Kombination aus innovativen Materialien, präziser Geometrie und fortschrittlichen Simulationstechniken ab. Die ständige Weiterentwicklung in diesen Bereichen sorgt dafür, dass Dampfturbinen auch in Zukunft effizient und zuverlässig betrieben werden können, selbst unter extremen Bedingungen.
Die kontinuierliche Verbesserung der Laufschaufeln einer Dampfturbine ist entscheidend für die Reduzierung von Energieverlusten und die Maximierung des Gesamtwirkungsgrads der Turbine. Daher wird in der Forschung und Entwicklung immer stärker auf die Verbesserung der Oberflächenbeschaffenheit und der Hydrodynamik der Schaufeln geachtet, um die Strömungsverhältnisse des Dampfs zu optimieren und den Reibungswiderstand zu verringern. Eine präzise Formgebung der Laufschaufeln trägt dazu bei, die Turbinenleistung zu steigern und den Brennstoffverbrauch zu senken. Neue Fertigungstechnologien wie 3D-Druck könnten die Herstellung komplexerer und effizienterer Schaufelgeometrien in der Zukunft ermöglichen, was wiederum die Leistungsfähigkeit der Turbinen steigern würde.
Zusätzlich zur Energieeffizienz gewinnt die Langlebigkeit der Laufschaufeln immer mehr an Bedeutung, da sie die Wartungskosten und Ausfallzeiten verringern kann. Die Entwicklung von hochbelastbaren Legierungen und hochgradigen Schutzbeschichtungen wird weiter vorangetrieben, um den Auswirkungen von Korrosion und Erosion durch aggressive Dampfbedingungen entgegenzuwirken. In Verbindung mit fortschrittlicher Überwachungstechnologie, wie z.B. intelligente Sensoren, die die Vibrationen, Temperaturen und Verformungen der Schaufeln in Echtzeit überwachen, wird es möglich sein, Verschleißprozesse frühzeitig zu erkennen und so Fehler zu verhindern, bevor sie ernsthafte Schäden verursachen.
Ein weiterer Vorteil solcher smart-gesteuerten Wartungssysteme ist die präzise Planung der Wartungsintervalle und der Ersatz von Schaufeln, was die Gesamtbetriebskosten der Dampfturbine signifikant reduzieren kann. Diese Technologien, kombiniert mit der Anwendung von digitale Zwillinge, ermöglichen es den Betreibern, die Schaufeln virtuell zu testen und mögliche Schwächen oder Optimierungspotenziale zu identifizieren, bevor ein physischer Austausch erforderlich wird. Solche fortschrittlichen prädiktiven Wartungsstrategien tragen zu einer höheren Anlagenverfügbarkeit und einer verlängerten Lebensdauer der Dampfturbinen bei.
Ein weiteres Augenmerk wird auf die Integration von nachhaltigen Materialien gelegt, die eine geringere Umweltbelastung aufweisen und gleichzeitig eine hohe Leistung bieten. Dies ist besonders relevant im Kontext der Energiewende, da die Industrie verstärkt nach Wegen sucht, die CO₂-Emissionen zu reduzieren. Forschungen zu biokompatiblen oder umweltfreundlichen Materialien, die in den Laufschaufeln verwendet werden können, könnten die Nachhaltigkeit von Dampfturbinen weiter verbessern und eine grünere Energieproduktion fördern.
Die Optimierung der Laufschaufeln in Bezug auf ihre Luft- und Dampfdurchflussverhältnisse sowie ihre thermischen und mechanischen Eigenschaften wird in Zukunft weiterhin ein wesentlicher Schwerpunkt der Dampfturbinenentwicklung bleiben. Die Kombination aus fortschrittlichen Materialien, innovativen Fertigungstechniken, präziser Geometrie und intelligenten Wartungsstrategien wird dafür sorgen, dass Dampfturbinen auch langfristig eine der effizientesten und zuverlässigsten Methoden der Energieerzeugung bleiben.
Die fortschreitende Automatisierung und die Entwicklung von digitalen Zwillingen spielen eine zunehmend bedeutende Rolle bei der Überwachung und Optimierung der Laufschaufeln in Dampfturbinen. Diese Technologien ermöglichen eine noch genauere Simulation und Überwachung der Schaufelverformungen und Belastungen in Echtzeit, was eine vorausschauende Wartung und frühzeitige Fehlererkennung ermöglicht. Digitalisierte Modelle der Dampfturbinen und ihrer Schaufeln bieten den Vorteil, dass Betriebsbedingungen simuliert werden können, um die Auswirkungen von unterschiedlichen Lasten, Temperaturen und Dampfgeschwindigkeiten auf die Laufschaufeln zu bewerten. So kann das Design kontinuierlich optimiert werden, um Lebensdauerverlängerung und Effizienzsteigerung zu gewährleisten.
Ein weiterer wichtiger Trend ist der verstärkte Fokus auf die Energieeffizienz der Dampfturbinen durch die Optimierung der Laufschaufeln. Durch die Verbesserung der Strömungsdynamik und der Turbinengeometrie können dynamische Verluste und Reibungsverluste reduziert werden, was die gesamtenergetische Ausbeute steigert. Ein präzises Design sorgt dafür, dass der Dampf möglichst gleichmäßig und mit minimalen Verlusten über die Schaufeln strömt, was zu einer besseren Arbeitserzeugung und geringeren Betriebskosten führt. Dies ist besonders wichtig in Zeiten steigender Energiepreise und zunehmender Energienachhaltigkeitsanforderungen, da die Betreiber bestrebt sind, die Betriebskosten zu minimieren und den CO₂-Ausstoß zu verringern.
Ein neues Forschungsgebiet beschäftigt sich mit der Untersuchung von multi-physikalischen Modellen, die alle relevanten Faktoren wie Strömung und Wärmeübertragung miteinander kombinieren, um die Funktionsweise der Laufschaufeln unter extremen Bedingungen noch präziser zu verstehen. Diese Modelle sind in der Lage, das Verhalten der Schaufeln in Bezug auf die komplexen Wechselwirkungen zwischen Temperaturgradienten, Thermospannungen, mechanischen Kräften und Strömungsdynamik zu simulieren und vorherzusagen. Dies ermöglicht eine noch bessere Abstimmung des Schaufeldesigns und eine optimierte Betriebsführung.
Ein weiteres Augenmerk liegt auf der Reduzierung der Wartungs- und Reparaturkosten durch innovative Schaufeldesigns und verbesserte Materialien, die weniger anfällig für Ermüdung und Verschleiß sind. Nanotechnologie und selbstheilende Materialien werden zunehmend als potenzielle Technologien für die Laufschaufeln betrachtet. Materialien, die sich selbst bei kleinen Schäden regenerieren oder ihre Festigkeit automatisch wiederherstellen können, könnten die Lebensdauer der Schaufeln erheblich verlängern und den Wartungsaufwand reduzieren. Diese Technologien sind noch in der Entwicklungsphase, aber sie versprechen eine vielversprechende Zukunft für die Kostensenkung und Nachhaltigkeit in der Dampfturbinenbranche.
Für die Zukunft der Dampfturbinen wird es auch entscheidend sein, wie die Laufschaufeln in Kombination mit anderen technologischen Innovationen wie künstlicher Intelligenz (KI) und Maschinellem Lernen (ML) zur kontinuierlichen Leistungsoptimierung beitragen können. Diese Technologien ermöglichen es, betriebliche Daten zu analysieren und Muster zu erkennen, die den Ingenieuren helfen, die Betriebsbedingungen und das Schaufeldesign kontinuierlich zu verbessern. So könnte die Turbine nicht nur optimal laufen, sondern sich auch selbst an veränderte Bedingungen anpassen und die Energieerzeugung in Echtzeit maximieren.
Zusammenfassend lässt sich sagen, dass die Laufschaufeln eine Schlüsselrolle in der Zukunft der Dampfturbinen spielen. Ihre kontinuierliche Optimierung in Bezug auf Materialien, Design, Überwachung und Wartung wird entscheidend dazu beitragen, dass Dampfturbinen auch in den kommenden Jahren eine der effizientesten und umweltfreundlichsten Technologien zur Energieerzeugung bleiben. Mit der Weiterentwicklung von intelligenten Systemen, neuen Werkstoffen und Fortschritten in der Simulationstechnik werden die Dampfturbinen mit optimierten Laufschaufeln ihre Leistung weiter steigern und somit auch zur globalen Energieoptimierung und Nachhaltigkeit beitragen.
Die kontinuierliche Weiterentwicklung der Laufschaufeln und der damit verbundenen Dampfturbinen trägt nicht nur zur Verbesserung der Betriebsleistung, sondern auch zur Sicherstellung der langfristigen Effizienz und Kosteneffektivität bei. Besonders im Kontext der zunehmenden Anforderungen an die Energieeffizienz und den Umweltschutz wird es zunehmend wichtiger, innovative Technologien und Materialien zu integrieren, um die Wirtschaftlichkeit und Nachhaltigkeit von Dampfturbinen zu erhöhen.
Ein weiterer vielversprechender Bereich für die Zukunft ist die Integration erneuerbarer Energien und deren Auswirkungen auf die Dampfturbinenindustrie. In einer zunehmend dekarbonisierten Welt, in der fossile Brennstoffe weniger genutzt werden, gewinnen Kraft-Wärme-Kopplungsanlagen (KWK) an Bedeutung, bei denen Dampfturbinen zur ganzheitlichen Nutzung von Abwärme und erneuerbare Energiequellen wie Biomasse oder Abfallprodukte verwendet werden. Dampfturbinen mit hochentwickelten Laufschaufeln sind besonders in der Lage, auch unter wechselnden und nicht konstanten Betriebsbedingungen, die mit der Nutzung erneuerbarer Energien verbunden sind, eine hohe Effizienz aufrechtzuerhalten.
Zusätzlich zu den Materialinnovationen wird auch die Systemintegration von Dampfturbinen zunehmend optimiert, um eine nahtlose Zusammenarbeit mit anderen Energieerzeugungstechnologien zu ermöglichen. Die Verbindung von Dampfturbinen mit Solarthermie, Geothermie oder Abwärme aus industriellen Prozessen könnte durch eine präzise Steuerung und Regelung von Schaufeldrehzahlen und Dampfströmen zu einer deutlichen Steigerung der Effizienz führen. In diesen Systemen wird es wichtig sein, dass Dampfturbinen mit der Fähigkeit ausgestattet sind, auf unterschiedliche Lastanforderungen dynamisch zu reagieren, was durch die ständige Verbesserung der Laufschaufeln und der Leistungssteuerung erreicht werden kann.
Ein weiteres Ziel ist die Erhöhung der Leistungsdichte von Dampfturbinen, also die Fähigkeit, mit weniger Material und bei höherer Kompaktheit größere Mengen an Leistung zu erzeugen. Dies erfordert eine verstärkte Forschung und Entwicklung an dünneren und leichteren Materialien, die trotzdem den extremen Belastungen standhalten, die während des Dampfturbinenbetriebs auftreten. Fortschritte in der Nanotechnologie, die Materialien mit noch besseren mechanischen und thermischen Eigenschaften ausstatten, könnten einen entscheidenden Beitrag zu dieser Entwicklung leisten.
Die Kombination von fortschrittlichen Materialien und modernen Fertigungstechniken wie dem 3D-Druck hat das Potenzial, die Produktion von Dampfturbinenlaufschaufeln noch präziser und effizienter zu gestalten. Mit 3D-Drucktechnologien können Schaufeln mit komplexeren Geometrien hergestellt werden, die eine optimierte Strömungsführung ermöglichen und die Belastung besser verteilen. Dies würde nicht nur zu einer Verbesserung der Leistung führen, sondern auch den Materialeinsatz reduzieren und so die Produktionskosten senken. Zudem bieten diese Technologien auch die Möglichkeit, maßgeschneiderte Lösungen zu entwickeln, die speziell auf die Anforderungen individueller Anlagen oder Einsatzbereiche abgestimmt sind.
Ein weiteres Entwicklungsfeld ist die integration von künstlicher Intelligenz (KI) und Machine Learning (ML) in den Betrieb und die Wartung von Dampfturbinen. Durch den Einsatz von KI-Algorithmen können präzise Vorhersagen über den Zustand der Laufschaufeln und der gesamten Turbine getroffen werden. Diese Technologien ermöglichen eine noch genauere Fehlerdiagnose, wodurch geplante Wartungsmaßnahmen optimiert und unvorhergesehene Ausfälle minimiert werden können. Die automatische Fehlererkennung und Optimierung der Betriebsparameter in Echtzeit trägt dazu bei, den Gesamtwirkungsgrad und die Lebensdauer von Dampfturbinen weiter zu steigern.
In der Zukunft wird es zudem von entscheidender Bedeutung sein, die Lebenszykluskosten von Dampfturbinen zu optimieren. Dies beinhaltet nicht nur die Herstellungskosten, sondern auch den Betrieb und die Wartung über die gesamte Lebensdauer der Turbine hinweg. Durch eine stärkere Lebensdauermodellierung und die Analyse von Betriebsdaten können Hersteller und Betreiber die Wartungsintervalle besser vorhersagen und gezielte Verbesserungen an den Laufschaufeln und anderen Turbinenkomponenten vornehmen. Diese Analyse umfasst auch die Untersuchung der Auswirkungen von alternativen Brennstoffen und Betriebsbedingungen, die in Zukunft möglicherweise eine größere Rolle spielen werden, etwa im Hinblick auf die Dekarbonisierung des Energiesektors.
Abschließend lässt sich sagen, dass die Dampfturbinenindustrie durch die stetige Weiterentwicklung von Laufschaufeln und deren fortschrittlichen Materialien, Designs und Überwachungstechniken weiterhin eine Schlüsselrolle in der globalen Energieerzeugung spielen wird. Der Weg zu effizienteren, nachhaltigeren und wirtschaftlicheren Dampfturbinen wird durch kontinuierliche Forschung, Innovationen und den Einsatz neuer Technologien wie digitale Zwillinge, KI und 3D-Druck geebnet, was die Leistung und Zuverlässigkeit dieser entscheidenden Energiequelle für die kommenden Jahre sichern wird.
Leitschaufeln der Dampfturbine
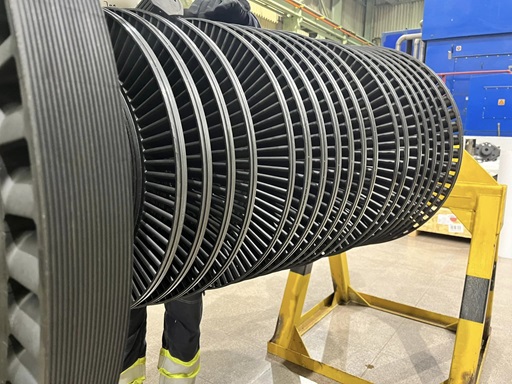
Die Leitschaufeln einer Dampfturbine spielen eine ebenso zentrale Rolle wie die Laufschaufeln, obwohl ihre Funktion unterschiedlich ist. Während die Laufschaufeln den Dampf direkt in mechanische Energie umwandeln, haben die Leitschaufeln die Aufgabe, den Dampf zu lenken und seine Strömung zu kontrollieren, bevor er auf die Laufschaufeln trifft. Ihre Hauptaufgabe ist es, den Dampfstrahl so zu lenken, dass er mit der optimalen Geschwindigkeit und Richtung auf die Laufschaufeln trifft, um die maximal mögliche Energieumwandlung zu erreichen.
Funktion und Aufbau der Leitschaufeln
Leitschaufeln befinden sich im Vorfeld der Laufschaufeln und sind strategisch so angeordnet, dass sie den Dampf aus dem Kessel oder dem Kondensator so umleiten, dass er optimal auf die Laufschaufeln trifft. Ihre Funktion ist entscheidend für den Gesamtwirkungsgrad der Dampfturbine, da sie die Strömungsgeschwindigkeit und den Dampfdruck des Dampfes beeinflussen, bevor dieser auf die Laufschaufeln trifft.
Im Allgemeinen besteht eine Dampfturbine aus mehreren Stufen, jede mit einem Satz von Leitschaufeln und Laufschaufeln. Die Leitschaufeln sind dabei so ausgelegt, dass sie den Dampf unter optimalen Bedingungen auf die nachfolgenden Laufschaufeln lenken. Sie helfen dabei, den Dampf zu beschleunigen und seine Strömungsrichtung so zu steuern, dass der Energieübertragungsprozess maximiert wird. Typischerweise wird der Dampf in jeder Stufe der Turbine durch einen Satz Leitschaufeln umgelenkt, bevor er auf die Laufschaufeln trifft.
Materialanforderungen
Da Leitschaufeln ständigen mechanischen Belastungen, hohen Temperaturen und oft auch Korrosionsbedingungen durch den Dampf ausgesetzt sind, müssen sie aus hochbelastbaren Materialien gefertigt werden. Häufig werden legierte Stähle oder Nickellegierungen verwendet, die sowohl eine hohe Festigkeit als auch eine gute Korrosionsbeständigkeit bieten. Der Einsatz fortschrittlicher Superlegierungen hat es ermöglicht, die Lebensdauer der Leitschaufeln zu verlängern und ihre Leistung zu steigern.
Ein weiteres wichtiges Merkmal ist, dass Leitschaufeln im Allgemeinen eine höhere thermische Belastung erfahren als die Laufschaufeln. Sie sind die ersten Komponenten, die mit dem heißen Dampf in Kontakt kommen, und müssen daher eine hohe Wärmebeständigkeit aufweisen, ohne sich zu verformen oder durch thermische Spannungen zu versagen. In einigen modernen Turbinen werden Leitschaufeln mit Spezialbeschichtungen versehen, um die Widerstandsfähigkeit gegen Temperaturschwankungen, Korrosion und Abrieb zu erhöhen.
Auswirkungen auf den Turbinenwirkungsgrad
Der Entwurf der Leitschaufeln hat einen direkten Einfluss auf den Gesamtwirkungsgrad der Dampfturbine. Eine optimale Geometrie der Leitschaufeln sorgt für eine maximale Dampfgeschwindigkeit und eine effiziente Umwandlung der Wärmeenergie in mechanische Arbeit. Die Winkelstellung und Krümmung der Schaufeln müssen so abgestimmt sein, dass der Dampfstrahl mit der besten Geschwindigkeit und Richtung auf die Laufschaufeln trifft, um die mechanische Arbeit zu maximieren.
Zu den jüngsten Entwicklungen gehören die variable Geometrie der Leitschaufeln, die es ermöglicht, den Winkel der Schaufeln während des Betriebs anzupassen. Dies kann helfen, die Effizienz der Turbine unter unterschiedlichen Lastbedingungen zu verbessern. Diese Anpassung ist besonders in Kombikraftwerken oder bei Turbinen, die mit unterschiedlichen Brennstoffen betrieben werden, von Vorteil, da sich die Dampfeigenschaften je nach Brennstoffzusammensetzung und Betriebsbedingungen ändern können.
Einfluss von Leitschaufeln auf den Betriebszustand der Turbine
Da Leitschaufeln den Dampf auf die Laufschaufeln lenken, wirken sie direkt auf die Dampfdurchflussrate und den Dampfdruck der Turbine. Eine falsche Ausrichtung oder Beschädigung der Leitschaufeln kann zu Verlusten bei der Energieumwandlung führen, da der Dampf nicht optimal auf die Laufschaufeln trifft. Im schlimmsten Fall kann dies zu Instabilitäten im Betrieb der Turbine oder sogar zu Schäden an anderen Turbinenkomponenten führen.
Um die Leistung der Leitschaufeln über die Lebensdauer der Dampfturbine hinweg zu optimieren, wird in modernen Anlagen zunehmend auf Überwachungstechnologien gesetzt, die durch den Einsatz von Sensoren und Echtzeit-Datenanalyse die Position und den Zustand der Leitschaufeln überwachen. Durch kontinuierliche Vibrationsmessungen, Temperaturüberwachung und Dampfdruckanalyse können potenzielle Probleme frühzeitig erkannt werden, bevor sie den Betrieb der Turbine beeinträchtigen.
Zukunftsperspektiven
Die Entwicklungen im Bereich der Leitschaufeln gehen über die reine Optimierung der Geometrie hinaus. Mit der zunehmenden Bedeutung der digitalen Simulation und der 3D-Drucktechnologie werden neue Designs von Leitschaufeln möglich, die noch effizientere Strömungsführung ermöglichen. Durch den 3D-Druck können komplexe Geometrien gefertigt werden, die den Dampfstrom noch besser lenken und die Strömungsverluste minimieren.
Forschungen konzentrieren sich auch auf den Einsatz von Nanomaterialien und fortschrittlichen Beschichtungen, die den Widerstand gegen Erosion und Korrosion weiter erhöhen und die Lebensdauer der Leitschaufeln verlängern. Diese Beschichtungen könnten nicht nur die Leistung der Schaufeln verbessern, sondern auch den Wartungsaufwand verringern, indem sie den Abnutzungsprozess verlangsamen.
Insgesamt wird die Weiterentwicklung der Leitschaufeln und ihre Integration in das Gesamtsystem der Dampfturbine einen wesentlichen Beitrag zur Energieeffizienz, Nachhaltigkeit und Zuverlässigkeit der Dampfturbinenindustrie leisten.
Ein weiterer bedeutender Aspekt in der Weiterentwicklung von Leitschaufeln ist die Integration von intelligenten Steuerungssystemen. Diese Systeme können in Echtzeit auf Veränderungen in den Betriebsbedingungen reagieren und die Geometrie der Leitschaufeln anpassen, um die Leistung der Turbine zu maximieren. Durch den Einsatz von Künstlicher Intelligenz (KI) und Maschinellem Lernen (ML) können diese Systeme kontinuierlich den optimalen Dampfstrom ermitteln, basierend auf den aktuellsten Betriebsdaten wie Dampfdruck, Temperatur und Lastbedingungen. Dies könnte eine weitere Verbesserung der Effizienz und Lebensdauer von Dampfturbinen ermöglichen, indem die Schaufeln dynamisch an die jeweiligen Betriebsbedingungen angepasst werden.
Zusätzlich wird zunehmend an der Entwicklung von selbstheilenden Materialien geforscht, die bei mechanischen Schäden oder Abnutzung von Leitschaufeln eine automatische Reparatur ermöglichen könnten. Diese Materialien könnten Mikrorisse oder kleine Beschädigungen, die durch den Kontakt mit Hochdruckdampf entstehen, reparieren, ohne dass eine umfassende Wartung erforderlich ist. Der Einsatz solcher Technologien würde die Notwendigkeit von geplanten Stillständen und Wartungsarbeiten weiter reduzieren und gleichzeitig die Betriebszeit und Verfügbarkeit der Dampfturbinen erhöhen.
Ein weiteres Zukunftsgebiet betrifft die Optimierung der aerodynamischen Eigenschaften von Leitschaufeln. Durch den Einsatz von fortschrittlichen Computermodellen und Computational Fluid Dynamics (CFD) können detaillierte Simulationen des Dampfstroms durchgeführt werden, um die Schaufeln noch präziser zu gestalten. Dies könnte zu einer drastischen Reduktion der Strömungsverluste und einer Verbesserung der gesamten Turbineneffizienz führen. Forscher versuchen, die aerodynamischen Verluste durch optimierte Schaufelgeometrien und Luftströmungsmanagementtechniken weiter zu minimieren.
Ein besonders spannender Bereich ist der Einsatz von Leitschaufeln in neuen Turbinentechnologien wie modularen Dampfturbinen oder in Kombination mit Gaskraftwerken in sogenannten Kombikraftwerken. In diesen hybriden Systemen kann die Dampfturbine mit Gaskraftwerken gekoppelt werden, um die Abwärme des Gasturbinenprozesses zu nutzen und so die Gesamteffizienz zu steigern. In solchen Anordnungen müssen die Leitschaufeln in der Lage sein, sich schnell an die sich ändernden Betriebsbedingungen der verschiedenen Energiequellen anzupassen, was durch eine weiterentwickelte Steuerungstechnik und flexible Materialeigenschaften ermöglicht wird.
Insgesamt lässt sich sagen, dass Leitschaufeln eine schlüsseltechnologische Rolle in der Dampfturbinenindustrie spielen und durch kontinuierliche Forschung und Entwicklung weiter optimiert werden. Mit der Fortschritten in der Werkstofftechnik, der automatisierten Fertigung und den intelligenten Steuerungssystemen könnte die Zukunft der Dampfturbinen mit einer noch höheren Energieeffizienz, einer verlängerten Lebensdauer der Komponenten und einer besseren Integration in moderne Energiesysteme gesichert werden.
Ein zusätzlicher Aspekt, der die Entwicklung von Leitschaufeln weiter prägen wird, ist die zunehmende Digitalisierung der Dampfturbinenindustrie. Echtzeit-Überwachung und Voraussagewartung sind Schlüsseltechnologien, die dazu beitragen, die Betriebsbedingungen der Dampfturbinen kontinuierlich zu optimieren. Mit Hilfe von Sensoren und Datenanalyse wird es möglich, präzise Vorhersagen über den Zustand der Leitschaufeln und der gesamten Turbine zu treffen. Solche Technologien könnten es den Betreibern ermöglichen, rechtzeitig auf Abnutzungserscheinungen, Materialfehler oder Leistungsabfälle zu reagieren, bevor sie zu ernsthaften Betriebsstörungen führen. Eine solche vorausschauende Wartung spart nicht nur Kosten, sondern verlängert auch die Lebensdauer der gesamten Turbine, da Leitschaufeln frühzeitig nachjustiert oder ausgetauscht werden können, bevor größere Schäden entstehen.
Ein innovativer Ansatz zur Steigerung der Energieeffizienz könnte die passive Kühlung der Leitschaufeln umfassen. In vielen modernen Dampfturbinen werden Leitschaufeln extremen Temperaturen ausgesetzt, was zu einer Überhitzung und damit zu einer Verringerung ihrer Lebensdauer führen kann. Thermische Beschichtungen oder Kühlsysteme, die eine gleichmäßige Temperaturverteilung und eine bessere Wärmeableitung ermöglichen, könnten eine längere Lebensdauer der Schaufeln fördern und gleichzeitig die Effizienz des gesamten Turbinenprozesses steigern. Ein weiterer Bereich der Forschung könnte sich mit Niedrigtemperaturtechnologien befassen, die die Belastung durch hohe Temperaturen verringern und so den Materialverschleiß minimieren.
Ein zusätzliches Potenzial zur Effizienzsteigerung liegt in der Optimierung des Dampfpfads. Die Gestaltung des gesamten Dampfpfads in einer Dampfturbine – von den Leitschaufeln über die Laufschaufeln bis hin zum Kondensator – beeinflusst maßgeblich die Dampfgeschwindigkeit und den Dampfdruck. Verbesserungen in der Strömungsdynamik und der Dampfführung können die Leistungsaufnahme und den Wirkungsgrad der Turbine erheblich steigern. Hier spielen die Leitschaufeln eine zentrale Rolle, da sie nicht nur die Strömung lenken, sondern auch dazu beitragen, den Dampf so effizient wie möglich durch die Turbine zu führen.
Ein weiterer Schritt könnte die Entwicklung von leichtgewichtigeren und kostengünstigeren Materialien für die Leitschaufeln sein. Momentan werden häufig hochlegierte Stähle oder Nickellegierungen verwendet, die sowohl sehr widerstandsfähig als auch teuer sind. Der Einsatz von Leichtbaumaterialien könnte dabei helfen, die Produktionskosten der Turbinen zu senken und gleichzeitig die strukturelle Integrität und Leistung der Leitschaufeln aufrechtzuerhalten. Hier könnten neue Legierungen oder sogar die Verwendung von hochfesten Verbundmaterialien eine Rolle spielen.
Ein besonders interessanter Bereich in Bezug auf die Anpassungsfähigkeit von Leitschaufeln könnte die Entwicklung von flexiblen Schaufeln sein. Diese Schaufeln könnten ihre Form während des Betriebs je nach den Druck- und Temperaturverhältnissen des Dampfes ändern, um den maximalen Energieübertrag zu erzielen. Die Forschung in diese Richtung könnte durch den Einsatz neuer smarter Materialien vorangetrieben werden, die in der Lage sind, auf Umweltbedingungen zu reagieren und ihre Form entsprechend anzupassen. Solche Technologien würden es ermöglichen, die Dampfturbine an eine breitere Palette von Betriebsbedingungen anzupassen und so den Betriebsbereich und Effizienz zu erweitern.
Schließlich könnte auch die Optimierung der Turbinenstufen durch den gezielten Einsatz von multi-stufigen Leitschaufeln ein interessanter Fortschritt sein. Anstatt mehrere Schaufelreihen für jede Turbinenstufe zu verwenden, könnten integrierte Leitschaufel-Designs entwickelt werden, die eine effizientere Dampfumlenkung und -beschleunigung ermöglichen. Dieser Ansatz würde nicht nur den Wirkungsgrad verbessern, sondern könnte auch den Bedarf an Platz und Material in der Turbine verringern, was besonders in kompakten oder mobilen Anwendungen wie auf Schiffen oder in kleineren Kraftwerken von Vorteil wäre.
Insgesamt zeigt sich, dass die Forschung und Entwicklung von Leitschaufeln eine Vielzahl an Möglichkeiten bietet, die Effizienz, Zuverlässigkeit und Nachhaltigkeit von Dampfturbinen weiter zu steigern. Mit einer Kombination aus fortschrittlichen Materialien, intelligenter Steuerungstechnik, 3D-Drucktechnologien und digitale Überwachungssystemen werden Leitschaufeln in den kommenden Jahren eine noch entscheidendere Rolle bei der Optimierung des gesamten Dampfturbinenbetriebs spielen.
Ein weiteres spannendes Entwicklungsfeld für Leitschaufeln ist die Integration von fortschrittlichen Fertigungstechniken, insbesondere der additiven Fertigung (3D-Druck). Diese Technologien ermöglichen es, komplexe und anpassbare Geometrien zu produzieren, die mit traditionellen Fertigungsmethoden möglicherweise nicht realisierbar wären. Durch den Einsatz von 3D-Druck können Leitschaufeln mit optimierten Strömungsprofilen und komplexen inneren Kühlkanälen ausgestattet werden, die die Wärmeeffizienz verbessern und gleichzeitig das Gewicht reduzieren. Diese innovativen Designs könnten die Leistung und Lebensdauer der Turbine weiter steigern, indem sie die Wärmeableitung optimieren und das Material effizienter nutzen.
Ein weiterer innovativer Ansatz könnte der Einsatz von hybriden Materialien sein. Dabei handelt es sich um Materialien, die verschiedene Eigenschaften kombinieren, wie zum Beispiel hohe Festigkeit, Korrosionsbeständigkeit und Thermalkapazität. Diese hybriden Materialien könnten speziell entwickelt werden, um den Anforderungen der Dampfturbinen, die extremen Temperatur- und Druckverhältnissen ausgesetzt sind, noch besser gerecht zu werden. Durch die Kombination verschiedener Werkstoffe in einer Schaufel können die einzelnen Schichten die unterschiedlichen Belastungen gezielt bewältigen und die gesamte Schaufel dadurch widerstandsfähiger und effizienter machen.
Ein weiteres Potential für die Zukunft liegt in der Erhöhung der Turbinentemperatur. Da der Wirkungsgrad einer Dampfturbine mit der Temperatur des Dampfs steigt, könnten hochtemperaturbeständige Leitschaufeln die Fähigkeit der Turbine erhöhen, mit höheren Dampftemperaturen zu arbeiten, ohne dass die Komponenten übermäßig verschleißen. Dies könnte durch den Einsatz hitzebeständiger Materialien wie keramische Beschichtungen oder hochlegierte Nickelbasislegierungen erfolgen. Höhere Temperaturen würden den Wirkungsgrad steigern, da mehr Energie aus dem Dampf extrahiert werden kann.
Ein weiterer innovativer Ansatz für die Optimierung von Leitschaufeln ist die Nutzung von Computersimulationen und Künstlicher Intelligenz für die dynamische Anpassung der Geometrie der Schaufeln im laufenden Betrieb. Diese Systeme könnten durch Maschinelles Lernen den idealen Winkel der Schaufeln und die optimale Geometrie basierend auf den aktuellen Betriebsdaten in Echtzeit berechnen und anpassen. So könnten Leitschaufeln noch präziser auf die aktuellen Betriebsbedingungen abgestimmt werden, wodurch der Wirkungsgrad der Turbine weiter gesteigert werden kann. Diese Technologie würde es ermöglichen, die Turbine unter einer breiteren Palette von Bedingungen zu betreiben und die Effizienz kontinuierlich zu maximieren.
Darüber hinaus könnten intelligente Materialien in die Entwicklung von Leitschaufeln integriert werden. Diese Materialien haben die Fähigkeit, ihre Eigenschaften als Reaktion auf Umwelteinflüsse wie Temperatur und Druck zu verändern. Ein Beispiel hierfür wären formveränderbare Materialien, die bei bestimmten Temperatur- oder Druckbedingungen ihre Form ändern und so die Strömung des Dampfes effizienter lenken könnten. Dies könnte besonders in variablen Betriebsumgebungen von Vorteil sein, in denen sich die Dampfeigenschaften schnell ändern können, wie zum Beispiel in Kombikraftwerken oder biomassebefeuerten Turbinen, die unterschiedliche Brennstoffe und somit unterschiedliche Dampfqualitäten verarbeiten.
Ein weiteres interessantes Forschungsgebiet ist die Verkürzung der Reaktionszeit der Turbine durch die Entwicklung von Leitschaufeln mit integriertem Turbulenzmanagement. Eine besser kontrollierte Turbulenz innerhalb der Dampfturbine kann zu einer stabileren Strömung führen, wodurch die Energieübertragung effizienter und gleichmäßiger abläuft. Solche Entwicklungen würden nicht nur den Effizienzgrad steigern, sondern auch den Lärmpegel der Turbine senken und den mechanischen Verschleiß durch weniger starke Vibrationen verringern.
Die fortschreitende Automatisierung der Fertigung und Wartung von Dampfturbinen wird ebenfalls die Entwicklung von Leitschaufeln beeinflussen. Robotertechnologien und drones könnten in Zukunft eine größere Rolle bei der Inspektion und Wartung von Leitschaufeln spielen. Besonders in schwer zugänglichen Bereichen der Turbine könnten solche Technologien dazu beitragen, Schäden frühzeitig zu erkennen, Wartungsarbeiten effizienter durchzuführen und die Lebensdauer der Leitschaufeln insgesamt zu verlängern.
Zusammenfassend lässt sich sagen, dass die Forschung und Entwicklung im Bereich der Leitschaufeln eine Vielzahl an technologischen Durchbrüchen verspricht, die nicht nur die Effizienz und Langlebigkeit von Dampfturbinen verbessern, sondern auch den Umwelteinfluss und die Betriebskosten senken können. Mit fortschrittlichen Materialien, intelligenten Steuerungssystemen und innovativen Fertigungstechniken wird die nächste Generation von Leitschaufeln nicht nur eine höhere Leistung ermöglichen, sondern auch die Tür zu einer nachhaltigeren und wirtschaftlicheren Energieproduktion öffnen.
Stator der Dampfturbine
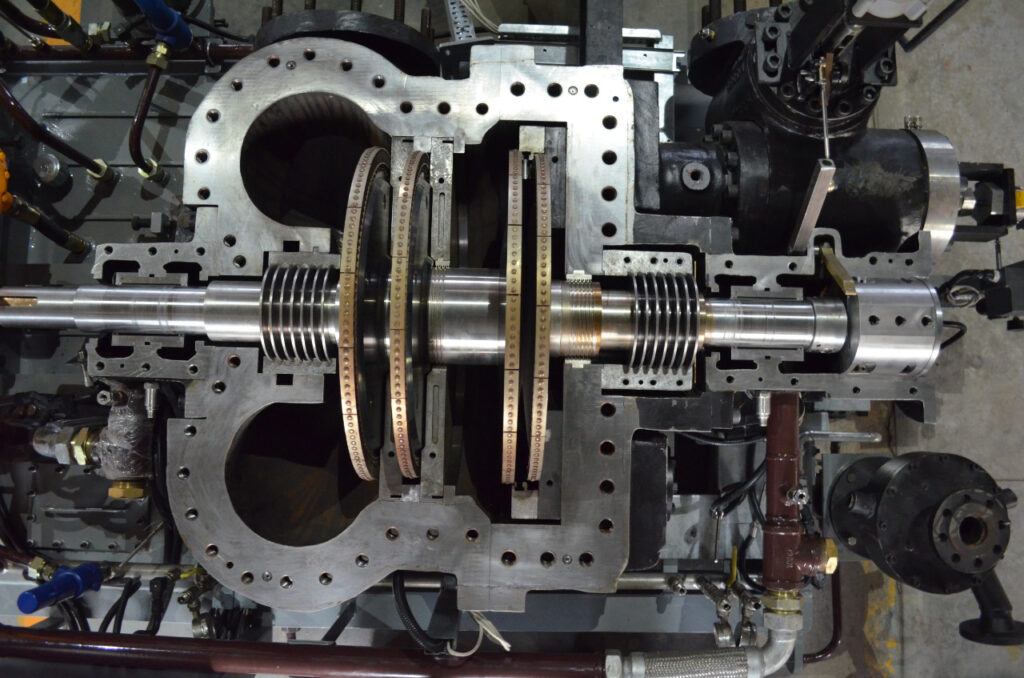
Der Stator einer Dampfturbine ist ein statisches Bauteil, das eine zentrale Rolle im Dampfturbinenprozess spielt. Während die Laufschaufeln rotieren und die Kinetische Energie des Dampfes in mechanische Energie umwandeln, dient der Stator dazu, den Dampf auf die Laufschaufeln zu lenken und so eine effiziente Umwandlung der Energie sicherzustellen. Der Stator ist daher ein entscheidendes Element der Dampfführung und sorgt für die präzise Kontrolle des Dampfstromes durch die Turbine.
Im Allgemeinen besteht der Stator aus einer Anordnung von Leitschaufeln und einer Reihe von Gehäusen, die den Dampf in einem optimierten Strömungsmuster leiten. Durch den Einsatz von Statoren wird der Dampf so gelenkt, dass er mit den Laufschaufeln optimal zusammenwirken kann, um den gewünschten Effekt auf die Turbinenwelle zu erzielen. Der Stator hilft, den Dampf so umzustrukturieren, dass seine Energieeffizienz maximiert und die Mechanik der Turbine optimal unterstützt wird.
Struktur des Stators
Der Stator besteht meist aus Leitschaufeln, die in ein statisches Gehäuse integriert sind, und die Dampfströmung auf den Rotor (die Laufschaufeln) vorbereiten. Der Statorbereich befindet sich vor den Laufschaufeln und übernimmt die Aufgabe, den Dampf zu beschleunigen und seine Druckenergie in kinetische Energie umzuwandeln. Dies geschieht durch eine gezielte Dampfumlenkung, bei der der Dampf durch die Leitschaufeln des Stators gelenkt wird, bevor er auf die Laufschaufeln trifft.
Ein wesentlicher Vorteil des Stators ist, dass er den Dampfstrom in vordefinierte Bahnen lenkt, was hilft, Turbulenz zu minimieren und den Strömungsverlauf gleichmäßiger zu gestalten. Dies wiederum reduziert Strömungsverluste und mechanische Belastungen auf die Laufschaufeln, da der Dampf mit weniger Widerstand auf die rotierenden Teile trifft.
Funktion des Stators in der Dampfturbine
Der Stator übernimmt die Energieumwandlung des Dampfes in mehreren Phasen, bevor dieser die Laufschaufeln erreicht. Bei einem typischen mehrstufigen Dampfturbinen-Design gibt es mehrere Stator-Abschnitte, die jeweils eine spezifische Funktion haben:
- Erster Statorabschnitt: Hier wird der Dampf mit einem hohen Dampfdruck und einer relativ niedrigen Dampftemperatur auf die Leitschaufeln gelenkt. Der Stator in diesem Abschnitt arbeitet daran, den Dampf zu beschleunigen, bevor er auf die erste Reihe Laufschaufeln trifft. Dabei kann der Dampfdruck reduziert werden, um eine höhere Strömungsgeschwindigkeit zu erreichen.
- Weitere Statorabschnitte: In den folgenden Abschnitten wird der Dampf weiter beschleunigt und durch die Laufschaufeln zunehmend verdichtet, bis er in den letzten Turbinenstufen nahezu bis zum Kondensator transportiert wird. Der Stator übernimmt die Funktion, die Richtung und Geschwindigkeit des Dampfs zu steuern, sodass er immer im optimalen Winkel auf die Laufschaufeln trifft.
Materialanforderungen
Da der Stator den Dampf in einem hochbelasteten Temperaturbereich lenkt, müssen die Materialien, aus denen er besteht, sehr widerstandsfähig gegen Hochtemperatur- und Hochdruckbedingungen sein. Typische Materialien für den Stator sind hochfeste Stähle, Nickellegierungen und hitzebeständige Legierungen, die eine hohe Korrosionsbeständigkeit und Strukturstabilität bei hohen Temperaturen gewährleisten. Diese Materialien tragen dazu bei, die Lebensdauer des Stators zu verlängern und die Effizienz der gesamten Turbine zu erhöhen.
Entwicklung und Innovationen im Bereich des Stators
Die Forschung im Bereich der Dampfturbinen hat sich in den letzten Jahren zunehmend auf die Optimierung der Statorgeometrie konzentriert. Durch den Einsatz von Computational Fluid Dynamics (CFD)-Simulationen werden die Strömungsbedingungen innerhalb des Stators detailliert modelliert, um den Dampfstrom präzise zu lenken und gleichzeitig Strömungsverluste zu minimieren. Weiterhin hat die additive Fertigung (3D-Druck) das Potenzial, die Geometrie von Statoren so anzupassen, dass sie komplexe Strömungsmuster noch effizienter handhaben können.
Die Integration von intelligenten Steuerungssystemen könnte es in Zukunft ermöglichen, den Dampfstrom in Echtzeit zu überwachen und den Stator dynamisch anzupassen. Dies könnte die Anpassung der Schaufelgeometrie oder die Umsteuerung von Dampfströmen in Echtzeit umfassen, um die Effizienz der Turbine während des Betriebs zu maximieren.
Stator im Kontext moderner Dampfturbinen
In modernen Dampfturbinen, insbesondere in Kombikraftwerken oder Gaskraftwerken, muss der Stator in der Lage sein, mit unterschiedlichen Brennstoffen und Betriebsbedingungen zu arbeiten. Diese Anlagen können stark variierende Dampfqualitäten und Betriebsprofile aufweisen, was den Bedarf an flexiblen und anpassungsfähigen Statoren erhöht. Forschung und Entwicklung in diesem Bereich zielen darauf ab, den Stator noch widerstandsfähiger und effizienter zu gestalten, um auch unter extremen Betriebsbedingungen eine hohe Leistung und Zuverlässigkeit zu gewährleisten.
Insgesamt bleibt der Stator eine kritische Komponente in der Dampfturbine, dessen Design und Materialauswahl maßgeblich für die Effizienz, Zuverlässigkeit und Lebensdauer der gesamten Turbine verantwortlich sind. Innovative Technologien und Fertigungsmethoden werden auch in diesem Bereich dazu beitragen, die Leistung von Dampfturbinen weiter zu steigern.
Der Stator in Dampfturbinen hat einen maßgeblichen Einfluss auf die Gesamtleistung der Turbine und spielt eine zentrale Rolle bei der Effizienz und Langlebigkeit des gesamten Systems. Eine entscheidende Entwicklung könnte die Integration von aktiven Leitschaufeln in den Statorbereich sein, die ihre Geometrie dynamisch ändern können, um sich an unterschiedliche Betriebsbedingungen anzupassen. Solche Systeme könnten die Strömung des Dampfs noch präziser lenken und so die Turbine unter verschiedenen Lastbedingungen immer im optimalen Betriebsbereich halten. Eine weitere Verbesserung könnte durch den Einsatz von Mikro- und Nanotechnologie zur Oberflächenverfeinerung erreicht werden. Durch die Anwendung spezieller Nanobeschichtungen auf den Statorkomponenten könnte die Reibung im Dampfpfad weiter gesenkt und der Materialverschleiß verringert werden. Diese Technologien könnten zudem eine bessere Korrosionsbeständigkeit und Wärmeleitfähigkeit bieten, was die Effizienz weiter steigern würde.
Ein weiteres Innovationsfeld ist die Verwendung von intelligenten Sensoren direkt im Statorbereich, die kontinuierlich Dampfparameter wie Temperatur, Druck und Strömungsgeschwindigkeit messen und die Daten in Echtzeit an die Steuerungssysteme der Turbine übermitteln. Auf dieser Basis könnten automatisierte Anpassungen des Dampfflusses vorgenommen werden, um den Wirkungsgrad zu optimieren und Abnutzungserscheinungen frühzeitig zu erkennen. Solche Sensoren könnten auch bei der Voraussagewartung von Turbinen eine wichtige Rolle spielen, indem sie frühzeitig auf Dampfleckagen oder Fehlfunktionen im Statorbereich hinweisen.
Des Weiteren könnten fortschrittliche Fertigungstechniken wie 3D-Druck auch für die Herstellung von Statoren von Bedeutung werden. Durch diese Technologie könnten nicht nur komplexere und optimierte Geometrien produziert werden, sondern auch das Gewicht der Statorbauteile reduziert werden. Dies wäre besonders in mobilen Anwendungen, wie bei Dampfturbinen in Schiffen oder Klein-Kraftwerken, von Vorteil, da geringeres Gewicht den Kraftstoffverbrauch reduziert und den gesamten Betriebsprozess kosteneffizienter gestaltet.
Die Kombination aus verbesserten Materialien, digitale Steuerung und fortschrittliche Fertigungstechnologien wird den Stator als ein zentrales Element weiter in den Mittelpunkt der Weiterentwicklungen im Bereich der Dampfturbinen stellen. Eine noch präzisere Steuerung des Dampfstroms, eine höhere Lebensdauer und eine bessere Energieausbeute werden dabei durch diese Innovationen in greifbare Nähe rücken. Solche Fortschritte werden nicht nur die Effizienz der Dampfturbinen steigern, sondern auch den gesamten Betrieb nachhaltiger und wirtschaftlicher gestalten.
Eine weitere interessante Entwicklung im Bereich des Stators von Dampfturbinen könnte die Verwendung von selbstheilenden Materialien sein. Diese Materialien haben die Fähigkeit, kleinere Risse oder Abnutzungserscheinungen automatisch zu reparieren, bevor sie zu größeren Problemen führen. In der Dampfturbinenindustrie könnten selbstheilende Materialien insbesondere bei hochbelasteten Bereichen wie den Leitschaufeln des Stators von Vorteil sein, die aufgrund der hohen Temperaturen und des Dampfdrucks einer kontinuierlichen Belastung ausgesetzt sind. Eine solche Technologie würde dazu beitragen, die Wartungsintervalle zu verlängern und die Notwendigkeit für regelmäßige, aufwendige Inspektionen und Reparaturen zu verringern.
Zusätzlich könnten thermoelektrische Materialien in den Stator integriert werden, um die überschüssige Abwärme der Turbine in nutzbare Energie umzuwandeln. Solche Materialien könnten die Effizienz weiter steigern, indem sie die Wärme, die sonst verloren gehen würde, recyceln und in zusätzliche elektrische Energie umwandeln. Diese Technologie wäre besonders in Kombikraftwerken nützlich, bei denen die Abwärme aus der Dampfturbine in einem zweiten Stromkreis genutzt wird.
Im Hinblick auf die optimierte Dampfumlenkung spielt die Strömungsdynamik im Stator eine wichtige Rolle, insbesondere in den Übergangsbereichen zwischen den verschiedenen Turbinenstufen. Hier könnten strukturelle Änderungen am Statorbauteil selbst zu einer besseren Dampfführung führen, indem die Strömung besser kontrolliert und gleichmäßiger verteilt wird. Ein präziserer Verlauf der Strömung würde den Wirkungsgrad erhöhen, da weniger Energie durch Turbulenzen oder unerwünschte Strömungsabweichungen verloren geht. Solche Entwicklungen könnten auch die Geräuschentwicklung der Turbine reduzieren, da stabilere Strömungsverhältnisse weniger Vibrationen und Schall erzeugen.
Ein weiterer Zukunftstrend könnte die Modularisierung von Dampfturbinen sein, bei dem Statorabschnitte als eigenständige Module konstruiert und bei Bedarf schnell ausgetauscht werden können. Dies würde nicht nur die Wartungszeiten erheblich verkürzen, sondern auch eine flexible Anpassung an verschiedene Betriebsbedingungen ermöglichen. Für Betreiber von Dampfturbinen würde dies eine erhöhte Betriebszeit und reduzierte Instandhaltungskosten mit sich bringen.
Simulationstechniken werden in der modernen Entwicklung von Dampfturbinen eine immer größere Rolle spielen. Durch den Einsatz von Künstlicher Intelligenz und Machine Learning könnten die Leistungskennwerte der Dampfturbine – insbesondere in Bezug auf die Strömungsdynamik im Stator – kontinuierlich überwacht und optimiert werden. Diese Systeme könnten automatisch erkennen, wenn die Turbine nicht mehr im optimalen Bereich arbeitet und dann entsprechende Anpassungen vornehmen, sei es durch Veränderung des Dampfdrucks, der Temperatur oder anderer betrieblicher Parameter. Dies würde nicht nur die Effizienz steigern, sondern auch die Lebensdauer der gesamten Turbine verlängern, da der Betrieb konstant auf einem optimalen Niveau gehalten werden kann.
Letztlich zeigt sich, dass der Stator einer Dampfturbine als eine zentrale Komponente des gesamten Systems eine Vielzahl von Innovationen und Weiterentwicklungen durchlaufen könnte. Die Kombination aus fortschrittlichen Materialien, intelligenten Überwachungssystemen, additiver Fertigung und dynamischen Anpassungen in Echtzeit könnte die Dampfturbinen der Zukunft nicht nur effizienter, sondern auch nachhaltiger und kostengünstiger machen. Diese Fortschritte könnten in einer neuen Ära von leistungsstarken, flexiblen und wartungsarmen Dampfturbinen münden, die den Herausforderungen der Energieproduktion in einer zunehmend grünen und ressourcenschonenden Welt gerecht werden.
Ein weiterer spannender Bereich der Weiterentwicklung von Statoren in Dampfturbinen betrifft die Interaktion zwischen verschiedenen Turbinenstufen. In modernen Dampfturbinen, insbesondere in Kombikraftwerken und Mehrstufenanlagen, wird der Dampf in mehreren Etappen durch die Turbine geleitet. Die Strömungsführung im Stator muss daher so optimiert werden, dass sie die Wechselwirkungen zwischen den verschiedenen Phasen und Druckbereichen berücksichtigt. Hier könnten neue strukturelle Designs helfen, die Effizienz der Strömung zwischen den Stufen zu verbessern und gleichzeitig den Energieverlust zu minimieren.
Ein wichtiger Trend in der Entwicklung der Turbinenstatoren könnte auch die Integration von Nachhaltigkeitsaspekten sein. Der zunehmende Fokus auf CO2-Reduktion und Umweltfreundlichkeit erfordert nicht nur die Entwicklung effizienterer Turbinen, sondern auch eine Betrachtung der Lebenszyklus-Analyse von Bauteilen wie dem Stator. Recyclingfähige Materialien und eine umweltfreundliche Produktion sind künftig verstärkt gefragt, um die Ökobilanz von Dampfturbinen zu verbessern. In diesem Zusammenhang könnte auch die Reparaturfähigkeit von Statoren eine Rolle spielen – Materialien und Designs, die sich besser reparieren lassen, könnten den Ressourcenverbrauch und die Produktionsabfälle reduzieren.
Auch in Bezug auf die Betriebsbedingungen könnten Statoren in der Zukunft flexibler gestaltet werden. Eine intelligente Anpassung der Geometrie und der Strömungsführung auf Basis von Echtzeit-Betriebsdaten wäre eine Möglichkeit, die Turbine nicht nur unter optimalen Bedingungen, sondern auch unter variablen Lasten oder bei unterschiedlichen Brennstoffen effektiv zu betreiben. Dies könnte besonders für Kraftwerke von Vorteil sein, die aufgrund von schwankenden Stromerzeugungskapazitäten (z. B. durch Wind oder Solarenergie) eine gewisse Flexibilität benötigen, um ihre Leistung an die Netzanforderungen anzupassen. Die dynamische Anpassung von Statoren würde es der Turbine ermöglichen, auch bei stark schwankenden Betriebsbedingungen eine hohe Energieeffizienz beizubehalten.
Darüber hinaus könnte auch die Integration von Kühltechnologien in den Stator eine wichtige Rolle spielen. In Dampfturbinen entstehen durch die hohe Temperatur und den hohen Dampfdruck in der Regel starke Wärmeentwicklungen. Innovative Kühlkanalsysteme und die Anwendung von fortschrittlichen Kühltechniken könnten dabei helfen, die Betriebstemperaturen zu stabilisieren und Thermaldifferenzen im Statorbereich zu verringern. Solche Technologien wären besonders in der Hochleistungs- und Hochtemperatur-Dampfturbinen relevant, die in der Energieerzeugung aus fossilen Brennstoffen oder auch in der geothermischen Energieerzeugung zum Einsatz kommen.
Insgesamt geht die Entwicklung des Stators einer Dampfturbine weit über die herkömmliche Konstruktion hinaus. Zukünftige Statoren könnten durch intelligente Materialien, adaptive Designs und die Nutzung von modernster Fertigungstechnologie nicht nur die Effizienz und Zuverlässigkeit der Turbine steigern, sondern auch deren Nachhaltigkeit und Anpassungsfähigkeit an unterschiedliche Betriebsanforderungen. Diese Innovationen könnten dazu beitragen, die Dampfturbinen als eine der wichtigsten Technologien der Energieerzeugung auch in einer zunehmend umweltbewussten und dynamischen Energiewelt weiterhin zu optimieren und eine Schlüsselrolle in der globalen Energiezukunft zu spielen.
Rotor der Dampfturbine
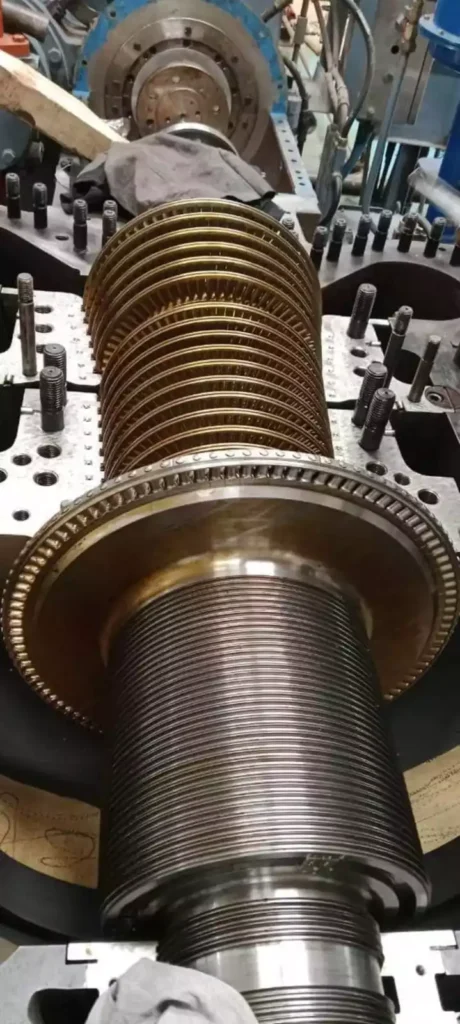
Der Rotor einer Dampfturbine ist eine der zentralen Komponenten des Systems und spielt eine wesentliche Rolle bei der Umwandlung der Energie des Dampfs in mechanische Energie. Während der Stator den Dampf strömt und lenkt, sorgt der Rotor für die eigentliche Energieumwandlung, indem er die kinetische Energie des Dampfs in Drehbewegung überträgt. Der Rotor ist in der Regel das rotierende Bauteil der Turbine und besteht aus einer Welle mit Schaufeln, die den Dampfdruck aufnehmen und in Bewegung versetzen.
Aufbau und Funktion des Rotors
Der Rotor besteht hauptsächlich aus Stahl oder Nickellegierungen, die aufgrund ihrer hohen Festigkeit und Korrosionsbeständigkeit in der Lage sind, den extremen Druck und hohe Temperaturen zu widerstehen, die während des Dampfbetriebs entstehen. Der Rotor ist in der Regel mit Schaufeln versehen, die sich um eine Welle drehen. Diese Schaufeln sind der eigentliche Mechanismus, der die Energie des Dampfes aufnimmt und in eine mechanische Drehbewegung umwandelt. Der Durchmesser und die Form der Rotorwelle sowie der Schaufeln sind so gestaltet, dass sie die maximale Energiemenge aus dem vorbeiströmenden Dampf gewinnen.
Im Betrieb wird der gesättigte oder überhitzte Dampf durch den Stator in die Rotorblätter geführt, die die Kinetische Energie des Dampfes auf die Rotorwelle übertragen. Diese Drehbewegung wird dann an Generatoren oder andere mechanische Systeme weitergeleitet, die die erzeugte mechanische Energie in elektrische Energie umwandeln.
Rotorblätter und Schaufeln
Die Rotorblätter, die sich um die Welle drehen, sind entscheidend für die Leistungsfähigkeit der Dampfturbine. Sie bestehen aus speziellen hochfesten Materialien, die nicht nur den Dampfdruck und die Temperaturen aushalten müssen, sondern auch einer hohen mechanischen Belastung durch die Zentrifugalkräfte standhalten müssen, die bei hoher Drehzahl auftreten. Im Allgemeinen werden für Rotorblätter legierte Stähle, Nickellegierungen und Titan verwendet, die eine hohe Korrosionsbeständigkeit, Wärmebeständigkeit und Festigkeit aufweisen.
Die Schaufelform ist entscheidend für die Effizienz der Dampfturbine. Moderne Rotorblätter sind so konstruiert, dass sie den Dampf in einer Art und Weise aufnehmen, die die Strömungsdynamik optimiert und den Dampf mit der geringstmöglichen Reibung durch die Turbine führt. Die Drehzahl des Rotors wird in den meisten Fällen so eingestellt, dass der Wirkungsgrad maximiert wird und die Umwandlung der Energie möglichst effizient erfolgt.
Zentrifugalkräfte und Thermische Belastung
Da der Rotor mit hoher Geschwindigkeit rotiert, unterliegt er extremen Zentrifugalkräften, die auf die Welle und die Rotorblätter wirken. Diese Kräfte können zu einer Dehnung und damit zu einer Veränderung der Form und Struktur der Rotorblätter führen, weshalb sie in der Regel prädestiniert für eine hohe Festigkeit und Biegefestigkeit sind. Die hohe Zentrifugalkraft erfordert, dass die Rotorblätter so konstruiert sind, dass sie gleichmäßig belastet werden, um eine Verformung oder gar ein Versagen der Struktur zu vermeiden.
Zudem muss der Rotor auch den thermischen Belastungen standhalten, die durch den Dampf entstehen. Während der Betrieb der Dampfturbine zu einer konstanten Erwärmung führt, muss der Rotor auch in der Lage sein, die Temperaturdifferenzen zu widerstehen, ohne dass er verzieht oder materialschwächer wird. Der Rotor und seine Schaufeln müssen in der Lage sein, hohe Temperaturen zu tolerieren, ohne dabei ihre strukturelle Integrität zu verlieren.
Rotorlager und Wellen
Der Rotor ist in der Dampfturbine über spezielle Lager gelagert, die es ihm ermöglichen, sich mit minimalem Widerstand zu drehen. Diese Lager sind so ausgelegt, dass sie sowohl die axialen als auch die radialen Kräfte, die während des Betriebs auftreten, effektiv abfangen. Dabei müssen die Lager extrem präzise und widerstandsfähig gegenüber den hohen Temperaturen und Belastungen sein, denen sie im Betrieb ausgesetzt sind.
Eine besondere Herausforderung für die Lagertechnik besteht in der Thermaldehnung. Da sich der Rotor während des Betriebs aufheizt und ausdehnt, müssen die Lager so konstruiert sein, dass sie diese Verformung mit minimalen Auswirkungen auf die Drehbewegung des Rotors aufnehmen können. In vielen Fällen kommen Schmierölsysteme zum Einsatz, die den Rotor mit einer ausreichenden Menge an Schmieröl versorgen, um den Reibungswiderstand zu minimieren und den Verschleiß der Lager zu verringern.
Fortschritte bei Rotor-Design und Materialtechnik
Moderne Dampfturbinen sind zunehmend darauf ausgelegt, höhere Betriebsdrücke und Temperaturen zu handhaben, was eine fortschrittliche Materialwissenschaft erforderlich macht. Forschungsarbeiten konzentrieren sich auf hochtemperaturbeständige Legierungen und komplexe Beschichtungen, die den Rotoren helfen, extremen Umgebungsbedingungen zu widerstehen und ihre Lebensdauer zu verlängern.
Zusätzlich wird in der Turbinentechnik vermehrt auf den Einsatz von computergestützten Simulationen gesetzt, um die Strukturdynamik der Rotoren unter verschiedenen Betriebsbedingungen zu optimieren. Diese Simulationen ermöglichen es, das Design der Rotorblätter und der Welle so anzupassen, dass sie die bestmögliche Leistung erbringen, ohne unnötige Vibrationen oder Überlastungen zu erzeugen.
Zusammenfassung
Der Rotor einer Dampfturbine ist das entscheidende Bauteil für die Umwandlung der Dampfkraft in mechanische Energie. Seine Schaufeln müssen speziell entwickelt werden, um den Dampf effizient zu nutzen und die mechanische Drehbewegung zu erzeugen. Dabei spielen die Materialwahl, die Strukturanpassung und die Fertigungstechniken eine entscheidende Rolle. Durch moderne Fertigungstechnologien, fortschrittliche Materialien und intelligente Überwachungssysteme wird der Rotor der Dampfturbine kontinuierlich verbessert, um sowohl die Effizienz als auch die Zuverlässigkeit der gesamten Turbine zu steigern.
Eine weitere bedeutende Entwicklung im Bereich der Rotoren von Dampfturbinen ist der optimierte Betrieb bei variablen Lasten. In modernen Energieerzeugungssystemen, insbesondere bei Kombikraftwerken, Erneuerbare-Energie-Anbindungen oder Flexible Kraftwerkssteuerung, ist die Fähigkeit, den Betrieb der Turbine unter schwankenden Lasten zu optimieren, zunehmend entscheidend. Hier könnten fortschrittliche Steuerungssysteme und adaptive Rotor-Designs eine Schlüsselrolle spielen. Ein dynamischer Rotor, der in der Lage ist, sich unter verschiedenen Lastbedingungen effizient zu verhalten, würde die Betriebsstabilität erhöhen und gleichzeitig die Energieausbeute maximieren. Diese Dynamik könnte durch die Anpassung der Rotorblätter oder den Einsatz von Rotoren mit variabler Geometrie erreicht werden, bei denen die Schaufeln automatisch an die wechselnden Betriebsbedingungen angepasst werden, um den Energiefluss zu maximieren.
Innovativer Rotorbau durch Additive Fertigung
Die Entwicklung von additiver Fertigung (3D-Druck) hat in den letzten Jahren auch das Design und die Herstellung von Dampfturbinenrotoren beeinflusst. Der 3D-Druck ermöglicht es, komplexe Rotorstrukturen herzustellen, die mit traditionellen Fertigungsmethoden nicht möglich sind. Insbesondere komplexe Kühlsysteme oder hochpräzise Geometrien innerhalb des Rotors können so konstruiert werden, dass sie eine bessere Temperaturverteilung und eine effizientere Energienutzung ermöglichen. Der 3D-Druck von Rotoren könnte es ermöglichen, weniger Material zu verwenden, ohne die strukturelle Integrität zu gefährden, was den Gewichtsunterschied verringert und die Effizienz verbessert.
Darüber hinaus könnte der 3D-Druck von Rotorblättern den Herstellungsprozess erheblich vereinfachen und die Produktionszeit verkürzen. Es könnte auch die Personalisierung von Rotoren für spezifische Anwendungen und Umgebungen fördern, da maßgeschneiderte Designs auf Kundenanforderungen angepasst werden können, ohne dass aufwändige Werkzeuge oder Maschinen erforderlich sind.
Erhöhung der Lebensdauer durch Korrosionsschutz und Wärmebeständigkeit
Da der Rotor und die Rotorblätter während des Betriebs extremen Temperaturen und Dampf-Chemikalien ausgesetzt sind, ist Korrosionsbeständigkeit ein weiterer wichtiger Aspekt in der Entwicklung von Rotoren. Fortschritte bei der Oberflächenbehandlung und der Korrosionsschutztechnologie tragen dazu bei, die Lebensdauer des Rotors signifikant zu erhöhen. Eine gängige Technologie sind Thermisch gesprühte Schichten oder PVD-Beschichtungen (Physical Vapor Deposition), die das Material vor chemischen Angriffen schützen und gleichzeitig die Wärmeleitung optimieren.
Außerdem gibt es weiterhin Fortschritte bei der Verwendung von hochtemperaturbeständigen Legierungen, die speziell für den Einsatz in hochbelasteten Bereichen der Dampfturbine entwickelt wurden. Die Verwendung von Nickel- und Kobalt-basierten Legierungen oder Keramikkomponenten kann den Rotor so gestalten, dass er auch bei extremen Betriebsbedingungen seine Form und Funktion über eine längere Zeit beibehält.
Rotorüberwachung und Intelligente Diagnosesysteme
Mit der Einführung von Internet der Dinge (IoT) und intelligenter Sensorik in Dampfturbinen werden die Überwachung und der Betrieb des Rotors zunehmend automatisiert. Sensoren, die an verschiedenen Stellen des Rotors und der Rotorwelle platziert sind, können Vibrationen, Temperaturen, Drehzahlen und Abnutzungsgrade in Echtzeit überwachen und die Daten an zentrale Überwachungsplattformen weitergeben. Dies ermöglicht es, mögliche Probleme frühzeitig zu identifizieren, bevor sie zu schwerwiegenden Schäden führen. Die Integration von Predictive Maintenance-Systemen kann dafür sorgen, dass Wartungsmaßnahmen genau dann durchgeführt werden, wenn sie erforderlich sind – und nicht basierend auf festen Intervallen.
Diese Echtzeit-Datenanalyse kann nicht nur dabei helfen, den Betriebszustand der Turbine in Echtzeit zu überwachen, sondern auch die Betriebsstrategien dynamisch anzupassen, um den Wirkungsgrad zu optimieren und die Lebensdauer der Rotoren zu verlängern. Ein weiteres potenzielles Entwicklungsgebiet ist die Verwendung von Künstlicher Intelligenz (KI), um Muster in den Betriebsdaten zu erkennen und zukünftige Fehlfunktionen vorherzusagen, was die Wartung noch effizienter gestalten würde.
Optimierung der Rotorgeometrie durch Computergestützte Simulationen
Ein weiterer Bereich der Innovation ist die Simulation und Modellierung von Rotoren durch Computergestützte Fluiddynamik (CFD). Mit fortschrittlichen Softwaretools können Rotoren mit äußerst präzisen 3D-Modellen simuliert werden, um ihre Dampfströme und Energieübertragung zu optimieren. Diese Computersimulationen ermöglichen es Ingenieuren, die Rotorgeometrie zu verfeinern und die Schaufeln für verschiedene Betriebsbedingungen genau abzustimmen. Es ist sogar möglich, die Wirkungsgrade verschiedener Rotorformen in verschiedenen Betriebsmodi zu simulieren und zu vergleichen, ohne physische Prototypen herstellen zu müssen.
Ein Beispiel für diese Technologie ist die optimierte Schaufelgeometrie in Rotorturbinen, bei der die Schaufeln mit speziellen Lufteinlässen und Kühlkanälen ausgestattet werden, um die Wärme effizienter abzuführen und gleichzeitig die Strömungseffizienz zu erhöhen. Diese Technologie wird kontinuierlich verfeinert, um den dynamischen Betrieb und die Lebensdauer des Rotors zu maximieren.
Zusammenfassung und Ausblick
Der Rotor einer Dampfturbine ist eine Schlüsselkomponente für die effiziente Umwandlung von Dampfkraft in mechanische Energie. Durch fortschrittliche Materialien, innovative Fertigungstechniken wie 3D-Druck, verbesserte Korrosionsschutztechnologien und den Einsatz von intelligenter Sensorik und Künstlicher Intelligenz wird der Rotor nicht nur langlebiger und leistungsfähiger, sondern kann auch flexibler und effizienter betrieben werden. Die ständige Optimierung der Rotorgeometrie durch Computergestützte Simulationen und die Einführung von dynamischen Anpassungen für variable Lasten zeigen, dass der Rotor in der Zukunft eine noch größere Rolle in der Maximierung der Effizienz und Nachhaltigkeit von Dampfturbinen spielen wird.
Ein weiterer bedeutender Aspekt bei der Weiterentwicklung von Rotoren in Dampfturbinen ist die Integration von Hybridtechnologien und Kombinationssystemen. Insbesondere in einer Zeit, in der Erneuerbare Energien immer stärker an Bedeutung gewinnen, könnte der Rotor in der Dampfturbine auch eine adaptive Funktion übernehmen, um auf die schwankende Energieerzeugung aus Solar und Windenergie reagieren zu können. Dampfturbinen, die in Kombikraftwerken oder Hybridkraftwerken eingesetzt werden, können durch den flexiblen Betrieb von Rotoren und Turbinen die Lastschwankungen in Echtzeit ausgleichen und so eine stabile Energieversorgung gewährleisten.
Hybrid- und Kombinationstechnologien
Kombikraftwerke, die sowohl fossile Brennstoffe als auch erneuerbare Energien nutzen, stellen hohe Anforderungen an die Flexibilität der Dampfturbinen. Die Rotoren solcher Turbinen müssen nicht nur den Druck und die Temperatur des Dampfs in unterschiedlichen Betriebszuständen effizient nutzen, sondern auch schnell auf wechselnde Betriebsbedingungen reagieren. Das bedeutet, dass der Rotor in der Lage sein muss, sich bei schwankendem Dampfdruck und Temperaturen zu adaptieren, ohne an Effizienz zu verlieren.
In einem Hybridkraftwerk, das mit einer Kombination aus Fossilbrennstoffen und Geothermie betrieben wird, kann der Rotor dabei helfen, die Thermaldynamik zu managen, indem er die Kraftstoffwirtschaftlichkeit optimiert und gleichzeitig die Umweltauswirkungen minimiert. In solchen Anlagen ist der Rotor auch dafür verantwortlich, die Leistung so zu regulieren, dass die Turbine nicht nur als Spitzenlastkraftwerk, sondern auch als Lastverteilungswerk fungieren kann, was zu einer kontinuierlichen Versorgungssicherheit führt.
Drehzahlregelung und Variabilität
Ein weiteres zukunftsweisendes Merkmal für die Rotoren von Dampfturbinen ist die Fähigkeit zur dynamischen Drehzahlregelung. In modernen Dampfturbinen ist die Drehzahl nicht mehr statisch, sondern wird je nach den Anforderungen des Netzbetreibers und den aktuellen Brennstoffpreismodellen angepasst. Dies erfordert eine präzise Steuerung der Rotoren, da eine plötzliche Veränderung der Drehzahl Auswirkungen auf die gesamte Turbine und ihre Leistung hat.
Verstellbare Rotoren, bei denen die Drehzahl in Echtzeit gesteuert wird, könnten es ermöglichen, die Turbine je nach Bedarf an die Betriebsbedingungen anzupassen. Diese dynamische Anpassung der Schaufelwinkel in Kombination mit einer Intelligente Steuerungseinheit würde es der Dampfturbine ermöglichen, auf plötzliche Schwankungen der Dampfparameter zu reagieren und dabei stets eine optimale Energieumwandlungseffizienz zu erzielen.
Rotoroptimierung für Hochtemperaturanwendungen
In speziellen Anwendungsbereichen, wie der geothermischen Energieerzeugung oder der Kernkraft, müssen Dampfturbinen-Rotoren extrem hohen Temperaturen standhalten. Die Temperaturgrenzen der traditionellen Materialien für Rotoren müssen dabei überschritten werden, weshalb hochtemperaturbeständige Legierungen und Keramikbeschichtungen zunehmend von Bedeutung sind. Die Entwicklungen in der Materialwissenschaft fokussieren sich auf neue Legierungen, die nicht nur hohen Temperaturen standhalten, sondern auch eine längere Lebensdauer ermöglichen und den Wartungsaufwand reduzieren.
Zusätzlich können aktuelle Beschichtungsverfahren wie Plasmabeschichtungen und Laserstrahlauftragsverfahren dazu beitragen, die Oberfläche des Rotors besonders widerstandsfähig gegenüber Thermalshock und Korrosion zu machen, die in Bereichen mit extrem heißen Dampftemperaturen auftreten.
Energiegewinnung aus Überschussdampf
Ein innovativer Ansatz zur Optimierung der Rotoren von Dampfturbinen könnte die Energiegewinnung aus Überschussdampf sein. Bei vielen Dampfturbinen, insbesondere in großen Industrieanlagen oder in Chemieparks, entsteht regelmäßig überschüssiger Dampf, der nicht unmittelbar für die Energieerzeugung verwendet wird. Durch energetische Zusatzsysteme, wie spezialisierte Rotoren, die überschüssigen Dampf effizient nutzen, könnte diese verschwendete Energie wieder in den Prozess zurückgeführt werden. So könnten Unternehmen von einer deutlich besseren Ressourcennutzung und einer Kostenreduzierung profitieren.
Diese Technologie könnte auch in der Abwärmenutzung von Industrieanlagen zur Anwendung kommen. Der Rotor könnte durch Abwärmerückgewinnungssysteme arbeiten, bei denen der überschüssige Dampf nicht nur für die Energieerzeugung, sondern auch für die Konditionierung von Kühlsystemen oder die Prozessdampfversorgung verwendet wird.
Zukünftige Herausforderungen und Ausblick
Die Rotoren von Dampfturbinen werden auch weiterhin einer Reihe von Herausforderungen gegenüberstehen, darunter:
- Materialtechnologie: Die fortschreitende Entwicklung von hochfesten, temperaturbeständigen und korrosionsresistenten Materialien wird weiterhin eine zentrale Herausforderung darstellen.
- Flexibilität: Die Fähigkeit der Rotoren, bei variablen Lasten und unterschiedlichen Betriebsbedingungen effizient zu arbeiten, wird zunehmend wichtiger.
- Langlebigkeit: Die Lebensdauer der Rotoren muss durch fortschrittliche Fertigungstechniken und verbesserte Wartungsstrategien erhöht werden.
- Energieeffizienz: Der Rotor muss ständig optimiert werden, um eine möglichst hohe Energieumwandlungseffizienz bei minimalen Verlusten zu gewährleisten.
Insgesamt lässt sich sagen, dass der Rotor einer Dampfturbine in den kommenden Jahren eine Schlüsselrolle spielen wird, um Energieerzeugungstechnologien nicht nur effizienter, sondern auch umweltfreundlicher und flexibler zu gestalten. Mit Hilfe von fortschrittlichen Materialien, intelligenter Steuerung, hybriden Technologien und innovativen Fertigungsmethoden werden Rotoren zunehmend in der Lage sein, sich den sich wandelnden Anforderungen der globalen Energieversorgung anzupassen und gleichzeitig die Zuverlässigkeit und Langfristigkeit der Dampfturbinen zu sichern.
Ein weiteres interessantes Forschungsgebiet im Bereich der Dampfturbinenrotoren ist die Integration von Wärmespeicherungssystemen und die Erweiterung von Speicherkapazitäten. Angesichts der Schwankungen in der Energieerzeugung, besonders durch erneuerbare Energiequellen, spielt die Möglichkeit, überschüssige Energie zu speichern und später abzurufen, eine immer größere Rolle. In diesem Zusammenhang könnte der Rotor durch den Einsatz von thermischen Energiespeichern und Wärmespeichermaterialien noch weiter optimiert werden.
Wärmespeichersysteme und Rotoren
Die Idee hinter der Integration von Wärmespeichersystemen in Dampfturbinen ist die Zwischenspeicherung von überschüssiger Wärme, die nicht sofort genutzt werden kann, aber später für die Stromerzeugung in Zeiten hoher Nachfrage verwendet wird. Diese Wärmespeicherung könnte durch Flüssigsalzsysteme, Thermoakkumulatoren oder sogar feststoffbasierte Energiespeichermethoden erfolgen. In Verbindung mit den Rotoren von Dampfturbinen könnte diese gespeicherte Wärme genutzt werden, um die Turbine auch bei schwankendem Dampfangebot kontinuierlich zu betreiben und den Kraftwerksbetrieb zu stabilisieren.
Zum Beispiel könnte überschüssige Wärme, die während des normalen Betriebs der Dampfturbine erzeugt wird, in einem thermischen Speicher gespeichert werden. Wenn die Dampfquelle später nachlässt oder die Nachfrage schwankt, könnte der Rotor diese gespeicherte Energie nutzen, um weiterhin Energie zu erzeugen. Diese Technologie ist besonders in Systemen relevant, in denen Solarthermie oder geothermische Energiequellen genutzt werden, die wetterbedingt oder aus anderen Gründen variieren können.
Rotoren in Hybridkraftwerken: Effizienzsteigerung und Flexibilität
Die Effizienz von Dampfturbinen kann durch die Integration von Hybridkraftwerken weiter gesteigert werden. In Hybridkraftwerken werden mehrere Energiequellen kombiniert, um eine stabile, zuverlässige Energieversorgung zu gewährleisten. Besonders in Kombination mit Wind- und Solarenergie können Dampfturbinen und ihre Rotoren eine wertvolle Rolle bei der Speicherung und effizienten Umwandlung von Energie spielen. Der Rotor muss hierbei in der Lage sein, mit unterschiedlichen Dampfquellen und -drücken zu arbeiten und dabei effizient die mechanische Energie zu erzeugen.
Die Hybridtechnologie könnte auch die Kombination von Dampfturbinen mit Brennstoffzellen oder Biomassekraftwerken beinhalten, was eine größere Flexibilität bei der Energieerzeugung bietet. In solchen Szenarien müsste der Rotor des Dampfturbinenmoduls in der Lage sein, sowohl mit klassischen fossilen Brennstoffen als auch mit erneuerbaren Energiequellen zu arbeiten, um den gesamten Wirkungsgrad zu optimieren und gleichzeitig die CO2-Emissionen zu verringern.
Automatisierung und Digitalisierung der Rotorüberwachung
Die zunehmende Automatisierung und Digitalisierung von Dampfturbinen eröffnen neue Möglichkeiten für eine intelligente Rotorüberwachung. Hier kommen moderne Sensoren und Echtzeit-Überwachungssysteme ins Spiel, die eine kontinuierliche Überwachung des Zustands der Rotoren ermöglichen. Die Verwendung von künstlicher Intelligenz (KI) und maschinellem Lernen zur Vorhersage von Fehlern oder Verschleißerscheinungen ist bereits ein heiß diskutiertes Thema.
Sensoren, die direkt auf den Rotoren installiert sind, können Vibrationen, Temperaturen, Drehzahlen und Verschleiß in Echtzeit messen. Dies liefert wertvolle Daten, die zur Verbesserung der Wartungsstrategien und zur Optimierung des Betriebs genutzt werden können. Insbesondere können präventive Wartungsmaßnahmen durch Predictive Maintenance eingeführt werden, wodurch ungeplante Ausfälle reduziert und die Lebensdauer der Rotoren verlängert wird.
Ein weiterer Vorteil dieser digitalen Integration ist die Möglichkeit, Betriebsparameter in Echtzeit anzupassen. Wenn die Betriebsbedingungen von außen Einfluss auf die Leistung des Rotors nehmen, können steuerbare Variablen wie die Schaufelwinkel in Echtzeit angepasst werden, um eine optimale Effizienz zu gewährleisten. Diese Dynamik in der Steuerung des Rotors ist besonders in Variablen Lastbedingungen von Bedeutung, die bei flexiblen Energiesystemen auftreten.
Herausforderungen der Rotorenentwicklung im Hinblick auf Nachhaltigkeit
Trotz der zahlreichen Innovationen und Verbesserungen stehen die Entwickler von Dampfturbinenrotoren vor einer Reihe von Herausforderungen in Bezug auf die Nachhaltigkeit. Die Reduzierung der CO2-Emissionen ist heute eine der zentralen Aufgaben für den gesamten Energiesektor. Bei Dampfturbinen ist dies insbesondere durch die Wahl der verwendeten Materialien und den Betrieb unter geringerem CO2-Ausstoß möglich.
Um die Nachhaltigkeit zu verbessern, werden zunehmend recycelbare Materialien und umweltfreundliche Fertigungsprozesse erforscht. Auch die Energieeffizienz des Rotors spielt eine große Rolle: Ein Rotor, der den Dampf effizienter nutzt und damit weniger Brennstoff benötigt, trägt direkt zu einer Reduzierung der Emissionen bei.
Darüber hinaus gibt es Bestrebungen, den Ressourcenverbrauch bei der Herstellung und dem Betrieb von Dampfturbinen zu reduzieren. Dies umfasst nicht nur den Energieverbrauch der Rotoren, sondern auch die Ressourcenintensität in Bezug auf den Materialverbrauch und die Lebenszyklusbewertung der Komponenten. Durch die Weiterentwicklung von Rotoren, die mit weniger Material und durch effizientere Prozesse hergestellt werden, könnte der CO2-Fußabdruck der Dampfturbine deutlich gesenkt werden.
Ausblick auf die Zukunft der Rotoren in Dampfturbinen
Die Entwicklungen in der Dampfturbinen-Technologie, insbesondere im Bereich der Rotoren, bieten einen vielversprechenden Ausblick auf eine zukunftsfähige Energieerzeugung. Mit der fortschreitenden Optimierung der Rotoren durch fortschrittliche Materialwissenschaften, digitale Technologien und hybride Energiesysteme könnte der Rotor eine zentrale Rolle im Übergang zu einer grüneren, nachhaltigeren Energieversorgung spielen. Die Integration von Flexibilität, Automatisierung und effizienten Energienutzungsmethoden wird den Rotoren in den kommenden Jahren zu einer Schlüsseltechnologie für die moderne Energiewirtschaft machen.
Die Herausforderung wird darin bestehen, nicht nur die Effizienz und die Lebensdauer der Rotoren zu maximieren, sondern auch deren Auswirkungen auf die Umwelt zu minimieren, während gleichzeitig die zunehmende Nachfrage nach flexiblen und robusten Energiesystemen bedient wird.
Turbinengehäuse

Das Turbinengehäuse ist eine zentrale Komponente in der Dampfturbine, die eine wichtige Rolle bei der Stabilität und Effizienz der gesamten Turbine spielt. Es dient nicht nur als physikalische Struktur, die die anderen Teile der Turbine zusammenhält, sondern trägt auch wesentlich zur Kontrolle der Dampfdynamik und zur Verhinderung von Leckagen bei. Im Folgenden werden die wichtigsten Aspekte des Turbinengehäuses im Detail erläutert:
Funktion und Aufbau des Turbinengehäuses
Das Turbinengehäuse, oft auch als Turbinengehäuse oder Turbinenmantel bezeichnet, bildet den äußeren Rahmen der Dampfturbine. Es wird so konstruiert, dass es die inneren mechanischen Komponenten, wie Rotor, Schaufeln und Leitschaufeln, sicher umschließt und deren Bewegung ermöglicht. Das Gehäuse stellt sicher, dass der Dampf, der in die Turbine eintritt, richtig kanalisiert wird, um die Maximierung der Energieumwandlung zu gewährleisten. Es ist in der Regel aus robusten Metallen wie Stahl, Edelstahl oder speziellen Legierungen gefertigt, die hohe Temperaturen und Druckverhältnisse aushalten können, ohne zu versagen.
Einige der wichtigsten Funktionen des Turbinengehäuses sind:
- Dampfleitung: Es leitet den Dampfstrom in die Turbine und sorgt dafür, dass der Dampf gleichmäßig und ohne größere Verluste auf die Schaufeln trifft.
- Druckaufrechterhaltung: Das Gehäuse hält den inneren Druck der Turbine aufrecht, um eine optimale Energieübertragung zwischen Dampf und mechanischen Komponenten zu gewährleisten.
- Schutz der Komponenten: Es schützt die empfindlichen inneren Komponenten wie Rotor und Schaufeln vor äußeren Einflüssen, wie z. B. Staub, Schmutz oder chemischen Angriffen.
Materialien für das Turbinengehäuse
Da das Turbinengehäuse extrem hohen Temperaturen und Druckverhältnissen ausgesetzt ist, sind die Materialien, aus denen es besteht, von entscheidender Bedeutung. Die Materialwahl beeinflusst nicht nur die Betriebsleistung der Dampfturbine, sondern auch ihre Langlebigkeit und Sicherheitsmerkmale. Zu den gängigsten Materialien gehören:
- Stähle mit hoher Festigkeit: Diese Materialien bieten eine gute Druckbeständigkeit und sind für die meisten Anwendungen in Dampfturbinen geeignet. Sie können hohen Temperaturen standhalten, ohne ihre mechanischen Eigenschaften zu verlieren.
- Edelstahl: Besonders in Bereichen, in denen die Turbine mit aggressiven oder korrosiven Dampfströmen arbeitet, werden Edelstahllegierungen verwendet, da sie eine höhere Korrosionsbeständigkeit bieten.
- Legierungen: In Hochleistungsanwendungen, wie Kernkraftwerken oder geothermischen Anlagen, kommen speziell entwickelte Legierungen zum Einsatz, die eine noch bessere Temperaturbeständigkeit und Festigkeit aufweisen.
Ein weiteres interessantes Material, das in modernen Turbinengehäusen zunehmend zum Einsatz kommt, ist Titan. Titan hat hervorragende Korrosions- und Temperaturbeständigkeitseigenschaften und ist daher ideal für besonders anspruchsvolle Umgebungen. Titanlegierungen werden aufgrund ihrer geringeren Dichte auch häufig in Hochleistungs- und militärischen Anwendungen verwendet.
Design und Struktur des Turbinengehäuses
Das Design des Turbinengehäuses muss so optimiert sein, dass es sowohl die strukturellen Anforderungen als auch die dynamischen Anforderungen im Betrieb berücksichtigt. Es gibt verschiedene Designaspekte, die berücksichtigt werden müssen:
- Stabilität und Festigkeit: Das Gehäuse muss die mechanischen Belastungen der Drehbewegungen des Rotors und der Thermaldynamik des Dampfsystems standhalten können. Dabei wird darauf geachtet, dass das Gehäuse keine verformungen oder Risse aufweist, die die Funktionsweise der Turbine beeinträchtigen könnten.
- Kompakte Bauweise: Dampfturbinen sind in vielen Anwendungen auf Platzersparnis angewiesen, insbesondere in Schiffs- und Offshore-Anwendungen. Daher ist das Turbinengehäuse oft so konstruiert, dass es möglichst kompakt und dennoch leistungsfähig ist.
- Wärmeableitung: Das Gehäuse muss eine ausreichende Wärmeableitung gewährleisten, um Überhitzung und die Bildung von thermischen Spannungen zu vermeiden. Einige Turbinengehäuse sind daher mit Wärmeabführsystemen ausgestattet, die die Temperatur innerhalb des Gehäuses konstant halten.
Turbinengehäuse in verschiedenen Turbinentypen
Je nach Einsatzgebiet und Turbinentyp gibt es Unterschiede im Aufbau und Design des Turbinengehäuses:
- Kondensationsturbinen: In einer Kondensationsturbine, bei der der Dampf am Ende des Prozesses kondensiert und als Flüssigkeit zurückgeführt wird, ist das Gehäuse so konstruiert, dass es den gesamten Dampfvorgang bis hin zum Vakuumzustand ermöglicht.
- Heißdampfturbinen: Bei Heißdampfturbinen, die mit sehr hohen Dampftemperaturen betrieben werden, müssen die Gehäuse aus hochbeständigen Materialien gefertigt werden, die den extremen Temperatur- und Druckanforderungen standhalten.
- Backpressure-Turbinen: Diese Turbinen arbeiten bei hohem Dampfdruck, weshalb das Gehäuse entsprechend verstärkt und optimiert wird, um den erzeugten Druck zu halten und den Dampfkondensationsprozess zu steuern.
Verfahren zur Herstellung des Turbinengehäuses
Die Herstellung eines Turbinengehäuses erfordert präzise Fertigungstechniken, um sowohl die strukturelle Integrität als auch die Thermaldynamik der Turbine zu gewährleisten. Zu den häufig verwendeten Verfahren gehören:
- Gießen: Das Gießen ist eine der gängigsten Methoden, um die komplexe Form eines Turbinengehäuses zu erzeugen. Spezielle Gussverfahren, wie Feingießen oder Schleudergießen, werden verwendet, um eine gleichmäßige Materialverteilung zu erzielen und gleichzeitig Verzug oder Lunker zu vermeiden.
- Schweißen und Fügeverfahren: Moderne Turbinengehäuse sind häufig aus mehreren Teilen zusammengesetzt, die durch Schweißen, Boden- oder Kaltumformung miteinander verbunden werden.
- Wärmebehandlung: Nach der Herstellung des Gehäuses erfolgt in der Regel eine Wärmebehandlung, um die mechanischen Eigenschaften des Materials zu verbessern und eine bessere Korrosionsbeständigkeit zu erzielen.
Wartung und Lebensdauer des Turbinengehäuses
Die Wartung des Turbinengehäuses ist entscheidend für den langfristigen Betrieb der Dampfturbine. Da das Gehäuse während des Betriebs extremen Temperaturen und Druckverhältnissen ausgesetzt ist, ist eine regelmäßige Inspektion und Frühdiagnose von Verschleiß oder Beschädigungen unerlässlich. Häufige Wartungsmaßnahmen umfassen:
- Drucktests: Diese Tests helfen, Undichtigkeiten oder Schwachstellen im Gehäuse frühzeitig zu erkennen.
- Überprüfung auf Risse und Korrosion: Insbesondere bei Anlagen, die mit korrosiven Dampfarten arbeiten, ist die Überprüfung auf Korrosionsschäden von entscheidender Bedeutung.
- Thermografie: Die Wärmebildtechnik kann helfen, Temperaturunregelmäßigkeiten im Gehäuse zu erkennen, die auf Probleme mit der Wärmeableitung oder auf Überhitzung hinweisen.
Zusammenfassend lässt sich sagen, dass das Turbinengehäuse eine unverzichtbare Rolle für die Funktion, Effizienz und Lebensdauer einer Dampfturbine spielt. Durch kontinuierliche Forschung und Technologieentwicklungen wird das Gehäusedesign immer weiter verbessert, um die Betriebsbedingungen in modernen Energieanlagen zu optimieren und Umweltauswirkungen zu minimieren.
Das Turbinengehäuse ist nicht nur für die strukturelle Integrität der Dampfturbine verantwortlich, sondern spielt auch eine wichtige Rolle bei der Dampfströmung. Es sorgt dafür, dass der Dampf gleichmäßig und unter optimalen Bedingungen in den Rotor und die Schaufeln der Turbine gelangt. Das Gehäuse kann verschiedene Dampfdruckbereiche kontrollieren und ermöglicht eine präzise Steuerung der Dampfdurchflussraten. Dies ist besonders wichtig für die Energieumwandlung in der Turbine, da die Energieeffizienz direkt von der Art und Weise abhängt, wie der Dampf auf die Schaufeln trifft.
Ein weiterer Aspekt des Turbinengehäuses ist seine Rolle in Bezug auf den Lärm und die Vibrationen. Dampfturbinen erzeugen während ihres Betriebs signifikante Vibrationen und Schallwellen, die nicht nur die Turbine selbst, sondern auch die Umgebung beeinträchtigen können. Das Turbinengehäuse hilft dabei, diese Schwingungen zu minimieren und die Lärmemissionen zu reduzieren. Dies wird durch speziell entwickelte Dämpfungssysteme und die Verwendung von geräuschdämpfenden Materialien im Gehäuse erreicht.
Die Lebensdauer des Turbinengehäuses hängt maßgeblich von den Betriebsbedingungen und den verwendeten Materialien ab. In Hochtemperaturumgebungen, in denen der Dampf sehr heiß ist, kann sich das Material des Gehäuses mit der Zeit verziehen oder verschleißen, was die Leistung der Turbine beeinträchtigen könnte. Durch den Einsatz von hochwertigen Legierungen und die regelmäßige Wartung kann jedoch die Lebensdauer des Gehäuses maximiert werden. Es wird auch zunehmend auf Reparaturtechniken und Modifikationen zurückgegriffen, um das Gehäuse auch nach längerer Nutzung weiterhin funktionsfähig zu halten.
Eine der größten Herausforderungen bei der Herstellung und dem Betrieb von Turbinengehäusen ist die Thermische Expansion. Dampfturbinen arbeiten mit enormen Temperaturunterschieden, und das Gehäuse muss in der Lage sein, diese Schwankungen ohne Verformung oder Materialversagen zu tolerieren. Moderne Gehäuse werden deshalb so konzipiert, dass sie thermisch stabil bleiben und sich während des Betriebs nur minimal ausdehnen oder zusammenziehen. Dazu kommen auch thermische Isolierungen und Aktivkühlungssysteme, die den Temperaturunterschied ausgleichen.
Die kontinuierliche Forschung und Entwicklung im Bereich der Turbinengehäuse fokussiert sich nicht nur auf die Optimierung der Leistung, sondern auch auf die Reduzierung der Betriebskosten und die Verbesserung der Umweltbilanz. Durch die Optimierung des Materialeinsatzes und die Entwicklung von nachhaltigeren Herstellungsverfahren wird versucht, die Umweltbelastung der Turbinengehäuse zu minimieren. Dies umfasst auch die Verwendung von recycelbaren Materialien und die Verbesserung der Energieeffizienz des gesamten Systems.
Insgesamt ist das Turbinengehäuse also nicht nur eine einfache Umhüllung, sondern eine hochkomplexe Komponente, die in direkter Wechselwirkung mit vielen anderen Aspekten der Dampfturbine steht. Vom Design über die Materialwahl bis hin zu Wartungsstrategien und Innovationen in der Produktion spielt das Turbinengehäuse eine Schlüsselrolle in der Effizienz, Langlebigkeit und Nachhaltigkeit von Dampfturbinen.
Neben den bereits erwähnten Aspekten wie der Strukturfestigkeit und Wärmeableitung hat das Turbinengehäuse auch Einfluss auf die Sicherheitsaspekte der Dampfturbine. Ein fehlerhaftes oder beschädigtes Gehäuse kann zu gefährlichen Dampfaustritten, Explosionen oder Überdrucksituationen führen, die sowohl für die Turbine selbst als auch für das gesamte Kraftwerk gefährlich sein können. Daher wird bei der Konstruktion und Wartung des Gehäuses großer Wert auf die Sicherheitsstandards gelegt. Moderne Turbinengehäuse sind mit Sicherheitsventilen und Überdrucksicherungen ausgestattet, die im Falle eines Druckanstiegs oder einer Funktionsstörung den Dampf sicher ableiten oder die Turbine abschalten, um eine Gefährdung zu vermeiden.
Ein zusätzliches Sicherheitsmerkmal ist die Überwachungstechnologie. Moderne Dampfturbinen werden mit Sensoren ausgestattet, die den Zustand des Gehäuses in Echtzeit überwachen. Diese Sensoren können Temperaturen, Druckverhältnisse, Vibrationen und Kondition des Materials messen und ermöglichen es den Ingenieuren, Anomalien frühzeitig zu erkennen. Ein Beispiel für eine solche Technologie ist die dynamische Monitoring-Technologie, bei der die Schwingungen des Gehäuses überwacht werden, um potenzielle Strukturschwächen oder Risse rechtzeitig zu identifizieren.
Die Integration von modernen Fertigungstechniken und additiven Fertigungsmethoden hat auch das Design und die Produktion von Turbinengehäusen revolutioniert. 3D-Druck und Laserschmelzen ermöglichen es, Turbinengehäuse mit komplexen, optimierten Strukturen zu fertigen, die mit traditionellen Fertigungstechniken schwer zu realisieren wären. Diese Technologien können helfen, Materialabfälle zu reduzieren, die Kosteneffizienz zu steigern und gleichzeitig die Leistungsfähigkeit der Turbine zu verbessern. Durch die präzise Kontrolle von Materialverteilung und -dichte lässt sich das Turbinengehäuse so gestalten, dass es genau den Anforderungen an Festigkeit, Temperaturbeständigkeit und Druckresistenz gerecht wird.
Ein weiterer innovativer Ansatz bei der Entwicklung von Turbinengehäusen ist die digitale Simulation. Ingenieure nutzen moderne Computermodelle und Simulationstechniken, um das Verhalten von Turbinengehäusen unter verschiedenen Betriebsbedingungen zu testen. Dadurch können sie mögliche Schwachstellen und Fehlerquellen im Design frühzeitig identifizieren und entsprechende Anpassungen vornehmen. Dies reduziert nicht nur die Entwicklungszeit, sondern sorgt auch dafür, dass die Betriebsbedingungen optimal berücksichtigt werden, was die Lebensdauer der Turbine insgesamt verlängert.
Durch all diese Entwicklungen wird das Turbinengehäuse zunehmend effizienter, sicherer und widerstandsfähiger. Gleichzeitig trägt es dazu bei, dass Dampfturbinen in einer Vielzahl von Industrien und Energieanlagen effektiv arbeiten können. Die Energieerzeugung mit Dampfturbinen ist ein zentraler Bestandteil der globalen Energieinfrastruktur, und die fortlaufende Optimierung des Turbinengehäuses stellt sicher, dass diese Technologie auch in Zukunft ihren Beitrag zur nachhaltigen Energieproduktion leisten kann.
Ein weiterer bedeutender Aspekt bei der Weiterentwicklung von Turbinengehäusen ist der Umweltschutz. Im Kontext der wachsenden globalen Bemühungen um Energieeffizienz und Nachhaltigkeit spielt das Design von Turbinengehäusen eine Schlüsselrolle bei der Reduktion von Emissionen und Energieverlusten. Das Gehäuse hilft nicht nur dabei, den Dampfstrom effizient zu leiten, sondern trägt auch dazu bei, dass die Turbine als Ganzes mit minimalen Verlusten arbeitet. Eine gut optimierte Dampfturbine, bei der das Gehäuse perfekt mit den anderen Komponenten zusammenarbeitet, kann den Brennstoffverbrauch senken und die CO2-Emissionen verringern. Durch den Fokus auf effiziente Wärmeübertragung und den ganzheitlichen Betrieb der gesamten Anlage wird die Energieeffizienz maximiert.
Ein weiterer Umweltfaktor, der durch das Design von Turbinengehäusen adressiert wird, ist die Abfallminimierung. Das moderne Design und die Materialauswahl für Turbinengehäuse berücksichtigen zunehmend die Recyclingfähigkeit der verwendeten Materialien. Einige Hersteller setzen auf Metalle und Legierungen, die nicht nur eine lange Lebensdauer besitzen, sondern auch am Ende ihrer Betriebszeit wiederverwertet werden können. Diese Kreislaufwirtschaft sorgt dafür, dass die Umweltbelastung durch den Betrieb von Dampfturbinen langfristig reduziert wird.
Die Technologie zur Überwachung und Wartung von Turbinengehäusen wird ebenfalls weiter verfeinert, was eine präventive Wartung ermöglicht. Traditionell musste die Turbine regelmäßig heruntergefahren werden, um Wartungsarbeiten am Gehäuse vorzunehmen. Heute können moderne Überwachungssysteme jedoch eine genauere Vorausschau ermöglichen, indem sie den Zustand des Gehäuses kontinuierlich überwachen und nur dann Wartungsmaßnahmen erfordern, wenn sie wirklich notwendig sind. Dies führt nicht nur zu Kostenersparnissen, sondern auch zu einer höheren Verfügbarkeit der Turbine, da diese weniger oft stillgelegt werden muss.
Darüber hinaus beeinflusst das digitale Zwillingstechnologie-System die Gestaltung und den Betrieb des Turbinengehäuses. Durch die Erfassung und Auswertung von Echtzeitdaten über Sensoren und intelligente Steuerungssysteme können Ingenieure ein genaues Abbild des Gehäuses und seiner Betriebszustände in der digitalen Welt erstellen. Diese virtuellen Modelle ermöglichen es, den Zustand der Turbine jederzeit zu überwachen und sofortige Anpassungen vorzunehmen, um die Effizienz zu maximieren und den Betrieb sicherzustellen. Dieses System bietet nicht nur Vorteile in der Fehlerdiagnose und Wartung, sondern ermöglicht es auch, vorausschauende Wartungsstrategien zu entwickeln, um Ausfälle und unvorhergesehene Reparaturen zu minimieren.
Die kontinuierliche Forschung im Bereich der materialwissenschaftlichen Entwicklungen für Turbinengehäuse führt auch dazu, dass immer neue, leistungsstärkere und umweltfreundlichere Materialien entwickelt werden. Dies betrifft sowohl die Hitzebeständigkeit als auch die Korrosionsbeständigkeit, da die Turbine in vielen Fällen mit extrem aggressiven Dampfbedingungen arbeiten muss. Materialien, die sich durch höhere Festigkeit bei gleichzeitig geringerem Gewicht auszeichnen, gewinnen zunehmend an Bedeutung. Hierbei handelt es sich oft um nanostrukturierte oder hochfeste Legierungen, die dazu beitragen, die Lebensdauer des Gehäuses zu verlängern und die Betriebsicherheit weiter zu steigern.
Die Entwicklung von intelligenten Turbinengehäusen wird in Zukunft ebenfalls eine zentrale Rolle spielen. Diese Gehäuse werden mit Künstlicher Intelligenz (KI) ausgestattet, die in der Lage ist, musterbasierte Vorhersagen zu treffen. KI-Algorithmen könnten in der Lage sein, die optimale Betriebsweise der Turbine zu ermitteln und Anomalien zu erkennen, die auf verschiedene Betriebsstörungen hinweisen. Auf diese Weise kann das Turbinengehäuse nicht nur als physikalische Barriere, sondern auch als aktiver Bestandteil eines intelligenten Überwachungsnetzwerks agieren, das den Betrieb in Echtzeit optimiert.
Ein weiterer Vorteil einer kontinuierlich weiterentwickelten Smart-Turbinengehäuse-Technologie ist, dass sie auch energieautonome Systeme ermöglichen könnte. Diese Gehäuse könnten in der Lage sein, durch integrierte Energieerzeugungssysteme ihre eigene Betriebsenergie zu erzeugen, was eine zusätzliche Reduzierung der Betriebskosten zur Folge hätte. Hierzu könnten beispielsweise thermische Solartechnologien oder piezoelektrische Systeme eingesetzt werden, um den Betrieb weiter zu optimieren.
Abschließend lässt sich sagen, dass das Turbinengehäuse eine der wichtigsten Komponenten in der Dampfturbine darstellt und einen direkten Einfluss auf Effizienz, Lebensdauer, Sicherheit und Umweltfreundlichkeit hat. Mit der fortschreitenden Entwicklung neuer Materialien, intelligenter Überwachungssysteme und innovativer Fertigungstechniken wird das Turbinengehäuse der Zukunft noch leistungsfähiger und umweltfreundlicher. Diese Fortschritte werden nicht nur die Betriebsleistung der Dampfturbinen verbessern, sondern auch einen positiven Beitrag zu den globalen Zielen für Nachhaltigkeit und Klimaschutz leisten.
Funktionsweise Dampfturbine
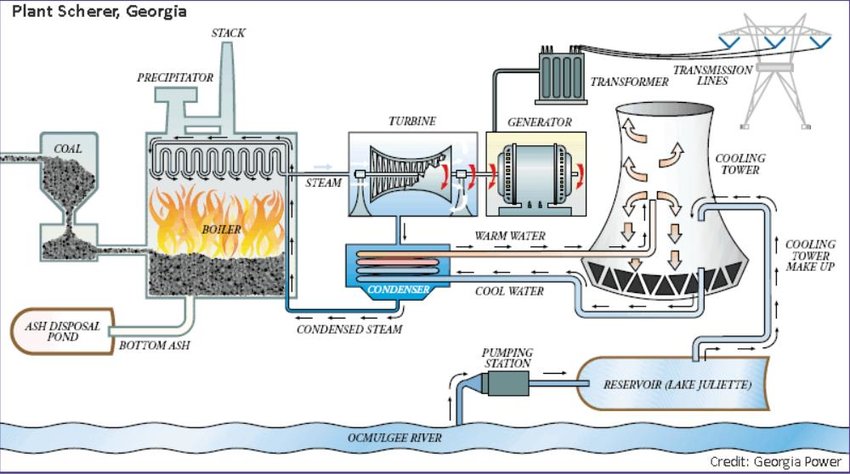
Die Funktionsweise einer Dampfturbine basiert auf der Umwandlung von thermischer Energie, die in gesättigtem Dampf oder überhitztem Dampf gespeichert ist, in mechanische Energie. Dies geschieht durch die Interaktion des Dampfes mit den Turbinenblättern oder Schaufeln, die den Rotor der Turbine in Bewegung setzen. Um diesen Prozess genauer zu verstehen, lassen sich die verschiedenen Phasen und Mechanismen der Dampfturbine folgendermaßen beschreiben:
1. Dampfeintritt (Dampfaufbereitung und -eintritt)
Der Prozess beginnt mit der Erzeugung von Dampf in einem Kessel oder Dampferzeuger. Hier wird Wasser durch die Verbrennung von Brennstoffen wie Kohle, Erdgas, Öl oder durch nukleare Reaktionen stark erhitzt. Der erzeugte Dampf wird dann mit hohem Druck und hoher Temperatur in die Dampfturbine geleitet. Es gibt verschiedene Dampfarten, die in Turbinen verwendet werden, darunter gesättigter Dampf und überhitzter Dampf.
Der Dampf wird in die Turbinengehäuse geleitet, und das Gehäuse sorgt dafür, dass der Dampf gleichmäßig verteilt und in die richtigen Kanäle gelenkt wird. Diese Kanäle führen den Dampf zu den Leitschaufeln, die ihn vorbereiten, um auf die Laufschaufeln zu treffen.
2. Leitschaufeln – Steuerung der Dampfströmung
Leitschaufeln sind fest im Gehäuse montiert und dienen dazu, den einströmenden Dampf in die richtige Richtung zu lenken, sodass er auf die Laufschaufeln trifft. Dabei wird der Dampf in Geschwindigkeit und Richtung optimiert, um den maximalen Energieübertrag auf die Rotorblätter zu erzielen. Die Leitschaufeln steuern also die Dampfströmung, bevor der Dampf in den Rotorbereich gelangt.
In modernen Dampfturbinen können die Leitschaufeln sogar verstellbar sein, sodass die Strömung des Dampfes je nach Betriebsbedingungen und Leistungsanforderungen dynamisch angepasst werden kann. Dies erhöht die Flexibilität und Effizienz der Turbine.
3. Lauf- oder Rotorschaufeln – Energieübertragung
Nach der Leitung durch die Leitschaufeln trifft der Dampf auf die Laufschaufeln oder Rotorblätter der Turbine. Diese Schaufeln sind auf der Turbinenwelle montiert und verbunden. Der Dampf übt einen Druck und eine Kraft auf die Schaufeln aus, was zu einer Drehbewegung des Rotors führt.
Der Dampfdruck wird auf die Schaufeln übertragen und erzeugt eine Drehmomentkraft, die die Turbinenwelle in Bewegung setzt. Die Energie, die durch den Dampf auf die Schaufeln übertragen wird, wird in mechanische Energie umgewandelt. Diese mechanische Energie kann dann genutzt werden, um Strom zu erzeugen, indem die Turbinenwelle mit einem Generator verbunden ist, der die Drehbewegung in elektrischen Strom umwandelt.
4. Dampfexpansion – Druck- und Temperaturabfall
Während der Dampf die verschiedenen Schaufelstufen der Turbine durchläuft, verliert er kontinuierlich an Druck und Temperatur. Dieser Prozess wird als Dampfexpansion bezeichnet. Der Dampf dehnt sich beim Übergang von einer Schaufel zur nächsten aus, was mit einer Abnahme des Drucks und der Temperatur einhergeht. Der Konditionierungsprozess des Dampfes erfolgt schrittweise, da der Dampf durch die verschiedenen Turbinenstufen (oft als Hochdruck-, Mitteldruck- und Niederdruckstufen bezeichnet) strömt.
Die Druckabnahme bei gleichzeitiger Beschleunigung des Dampfes sorgt dafür, dass der Dampfmechanismus kontinuierlich Arbeit verrichtet und eine stabile Energieproduktion gewährleistet ist.
5. Kondensation des Dampfs
Nachdem der Dampf in den verschiedenen Schaufelstufen der Turbine seine Energie abgegeben hat, wird er in der Regel in einem Kondensator zu Wasser zurückverwandelt. Dies erfolgt, indem der Dampf durch Abkühlung seine Wärme verliert und wieder zu flüssigem Wasser kondensiert.
Das kondensierte Wasser wird in den Kessel oder den Wasseraufbereitungskreislauf zurückgeführt, wo es wieder verdampft und der Zyklus von Neuem beginnt. In einigen Systemen, wie etwa bei Heißdampfturbinen oder Dampfkraftwerken mit Kreuz-Überhitzung, kann der Dampf auch in verschiedenen Druckstufen verarbeitet werden, bevor er in den Kondensator gelangt.
6. Mechanische Arbeit und Stromerzeugung
Die mechanische Energie, die durch die Rotation der Turbinenwelle erzeugt wird, wird verwendet, um einen Generator anzutreiben. Dieser Generator wandelt die mechanische Energie der Welle in elektrische Energie um. Die erzeugte elektrische Energie wird über ein Stromnetz an die Verbraucher weitergeleitet. In Industriellen Anwendungen oder Kraftwerken wird diese Energie genutzt, um große Mengen Strom zu erzeugen, die für verschiedene Anwendungen genutzt werden können, wie etwa die Stromversorgung von Haushalten, Industrieanlagen oder Fabriken.
7. Turbinenwellenlager und Schmierung
Um die Reibung zwischen den beweglichen Teilen der Turbine zu minimieren und eine langfristige Betriebsfähigkeit sicherzustellen, ist die Turbinenwelle in speziellen Wellenlagern gelagert. Diese Lager sind in der Regel mit Schmieröl versorgt, das die Reibung verringert und eine Kühlung der Wellenlager ermöglicht. Die Schmierung erfolgt in der Regel über ein Zentralschmiersystem, das dafür sorgt, dass die Wellenlager und andere bewegliche Teile in der Turbine kontinuierlich mit Öl versorgt werden.
Zusammenfassung der Dampfturbinen- Funktionsweise
Insgesamt basiert die Funktionsweise der Dampfturbine auf dem Prinzip der Dampfexpansion und der Energieübertragung von thermischer Energie auf mechanische Energie. Der Dampf, der unter hohem Druck und hoher Temperatur in die Turbine eintritt, gibt während seiner Expansion einen Großteil seiner Energie an die Turbinenblätter ab. Diese Energie wird dann in mechanische Energie umgewandelt und schließlich in elektrische Energie durch den Generator. Der gesamte Zyklus ist darauf ausgelegt, eine möglichst hohe Energieausbeute bei gleichzeitiger Minimierung von Energieverlusten zu erzielen.
Die Dampfturbine ist ein äußerst effizientes System zur Umwandlung von thermischer Energie in mechanische Energie, wobei der gesamte Prozess von der Dampferzeugung bis hin zur Stromerzeugung eng miteinander verknüpft ist. Während der Dampf durch die Turbine strömt, nimmt er kontinuierlich an Energie ab, wobei ein erheblicher Teil der Energie in Form von mechanischer Drehbewegung in die Turbinenwelle übertragen wird. Diese Welle ist mit einem Generator gekoppelt, der die mechanische Energie in elektrische Energie umwandelt.
Die kontinuierliche Expansion des Dampfs sorgt dabei für eine fortlaufende Umwandlung von Wärme in mechanische Energie, was den gesamten Prozess sehr effektiv macht. Ein entscheidender Aspekt für die Effizienz des Systems ist die kontinuierliche Überwachung und Anpassung der Betriebsbedingungen der Turbine, die durch moderne Steuerungs- und Überwachungssysteme ermöglicht wird. Diese Systeme sorgen dafür, dass die Dampfturbine immer unter optimalen Bedingungen arbeitet und so die bestmögliche Leistung erzielt wird. Der Druckabfall und die Temperaturabnahme des Dampfs während des Durchgangs durch die Turbine sind unvermeidlich, aber gut ausgelegte Turbinen mit mehreren Stufen sorgen dafür, dass der Dampf in jeder Phase seine Arbeit effizient abgibt.
Der Kondensator spielt ebenfalls eine wesentliche Rolle, indem er den Dampf nach seiner Energieabgabe wieder in Wasser umwandelt, das in den Kessel zurückgeführt wird. Diese Schließung des Kreislaufs sorgt für eine hohe Ressourceneffizienz, da Wasser wiederverwendet und erneut erhitzt werden kann. Die kontinuierliche Weiterentwicklung von Materialien und Technologien zur Optimierung der Turbinenkomponenten, wie etwa der Turbinenblätter, die immer widerstandsfähiger gegen Korrosion und thermische Belastung werden, trägt dazu bei, die Lebensdauer der Turbine zu verlängern und gleichzeitig die Effizienz und Sicherheit zu steigern. Ein weiterer wichtiger Bestandteil der Dampfturbine ist das Schmier- und Kühlsystem, das dafür sorgt, dass alle beweglichen Teile optimal laufen und vor übermäßiger Abnutzung oder Überhitzung geschützt sind. So bleibt die Dampfturbine auch über viele Jahre hinweg ein zuverlässiger Bestandteil der Energieproduktion, sei es in großen Kraftwerken, in Marinenanwendungen oder auch in industriellen Prozessen.
Ein weiterer wichtiger Punkt bei der Funktionsweise von Dampfturbinen ist die Betriebsoptimierung. Dampfturbinen sind in der Regel auf eine kontinuierliche Leistung ausgelegt, aber in realen Anwendungen, wie etwa in Kraftwerken, können sich die Betriebsbedingungen ändern. Faktoren wie Laständerungen, Außentemperaturen oder der Brennstoffverbrauch können die Effizienz und den Betrieb der Turbine beeinflussen. Moderne Steuerungssysteme mit automatisierten Regelmechanismen sorgen dafür, dass die Turbine dynamisch auf diese Änderungen reagiert. Die Regelung erfolgt häufig über die Dampfdruckkontrolle, die Leitschaufeln anpasst und so den Dampfdurchfluss und die Drehzahl der Turbine optimiert.
Ein weiterer technologischer Fortschritt in der Dampfturbinentechnologie ist die Integration von hybriden Energiesystemen, bei denen die Dampfturbine mit anderen Formen der Energieerzeugung kombiniert wird. Beispiele sind Kombikraftwerke, bei denen eine Dampfturbine mit einer Gasturbine gekoppelt wird. Diese Kombination aus Gasturbine und Dampfturbine wird als GuD-Anlage (Gas- und Dampfturbinenkraftwerk) bezeichnet. In solchen Systemen wird der Abgasstrom der Gasturbine genutzt, um zusätzlich Dampf zu erzeugen, der dann die Dampfturbine antreibt. Dieser Prozess erhöht die Gesamtwirkungsgrad und senkt die CO2-Emissionen, da die Abwärme aus der Gasturbine effizient genutzt wird.
Zusätzlich zur verbesserten Energieeffizienz tragen auch innovative Materialien zur Leistungssteigerung von Dampfturbinen bei. Fortschritte in der Legierungstechnologie haben dazu geführt, dass hochtemperaturbeständige Materialien immer häufiger in Turbinenkomponenten wie den Laufschaufeln und den Leitschaufeln eingesetzt werden. Diese Materialien können höhere Temperaturen und Dampfdrucke aushalten, was es ermöglicht, die Thermodynamische Effizienz der Turbine weiter zu steigern, indem der Dampf bei höheren Temperaturen und Drücken betrieben wird. Dies ist besonders wichtig für die Effizienz von Hochleistungsanlagen und Industriekraftwerken, bei denen es auf maximale Wärmenutzung ankommt.
Eine weitere Verbesserung der Dampfturbinen erfolgt durch den Einsatz von digitale Steuerungssysteme und vorausschauende Wartung. Moderne Überwachungstechnologien wie IoT-basierte Systeme (Internet der Dinge) und Künstliche Intelligenz ermöglichen eine präzisere und zuverlässigere Fehlerdiagnose. Durch die kontinuierliche Messung von Parametern wie Temperatur, Druck, Schwingungen und Vibrationen können potenzielle Probleme frühzeitig erkannt und behoben werden, bevor sie zu einem Ausfall führen. Diese Technologien erlauben es auch, Wartungszyklen zu optimieren, was nicht nur Betriebsunterbrechungen minimiert, sondern auch die Lebensdauer der Turbine verlängert.
In Bezug auf die Umweltverträglichkeit gewinnt die Nutzung von Dampfturbinen ebenfalls zunehmend an Bedeutung. Dampfturbinen werden nicht nur in klassischen Kohlekraftwerken eingesetzt, sondern auch in Kraft-Wärme-Kopplungsanlagen (KWK-Anlagen), die gleichzeitig Strom und Wärme erzeugen. Diese Anlagen können zur Energieeffizienzsteigerung in industriellen Prozessen beitragen und Abwärme sinnvoll nutzen. Zudem werden Dampfturbinen zunehmend in Kombination mit erneuerbaren Energien wie Geothermie und Biomasse verwendet, um die CO2-Emissionen zu senken. Der Einsatz von biogenem Brennstoff in Dampfkraftwerken trägt zur Schaffung einer nachhaltigen und umweltfreundlicheren Energieversorgung bei.
Die Betriebsdauer einer Dampfturbine ist stark von der regelmäßigen Wartung und dem Betriebsmanagement abhängig. Turbinen werden oft jahrelang ohne größere Probleme betrieben, wenn sie regelmäßig gewartet und ihre Komponenten überprüft werden. Insbesondere die Laufschaufeln, Leitschaufeln und Rotoren müssen regelmäßig auf Abnutzung oder Korrosion überprüft werden, um sicherzustellen, dass die Turbine effizient läuft und keine Funktionsstörungen auftreten. Die Überwachung des Schmierölsystems ist ebenso wichtig, da es eine entscheidende Rolle bei der Reduzierung von Reibung und Wärmeentwicklung spielt, die zu Verschleiß führen können.
Ein besonders vielversprechendes Zukunftsprojekt im Bereich Dampfturbinen ist der Einsatz von Superkritischem Dampf. Bei superkritischem Dampf handelt es sich um Dampf, der bei einem Druck und einer Temperatur oberhalb des kritischen Punktes betrieben wird. Dieser Dampf hat sowohl Eigenschaften von Flüssigkeiten als auch von Gasen, was die Energieumwandlung effizienter macht und die Wärmeverluste reduziert. Superkritische Dampfturbinen könnten in Zukunft in der Lage sein, Wärme aus verschiedenen Quellen noch effizienter zu nutzen und dabei den CO2-Ausstoß weiter zu senken.
Zusammengefasst lässt sich sagen, dass die Funktionsweise der Dampfturbine weit mehr ist als nur ein mechanischer Prozess der Energieumwandlung. Sie ist das Ergebnis jahrzehntelanger Innovation und kontinuierlicher Optimierung in den Bereichen Materialtechnik, Energieeffizienz, Umweltschutz und Betriebsführung. Zukünftige Entwicklungen werden sich weiter auf die Nachhaltigkeit und Flexibilität von Dampfturbinen konzentrieren, wobei die Integration von erneuerbaren Energien und die Verbesserung der digitalen Steuerungssysteme im Vordergrund stehen werden. Die Dampfturbine bleibt also auch in einer zunehmend grünen und digitalisierten Energiezukunft ein zentraler Bestandteil der globalen Energieinfrastruktur.
Ein weiterer interessanter Aspekt der Dampfturbinenentwicklung ist die Optimierung des thermodynamischen Zyklus. Der thermodynamische Zyklus in Dampfturbinen basiert oft auf dem Rankine-Kreisprozess, der die Energieübertragung von Wärme auf mechanische Arbeit beschreibt. Durch verschiedene Technologien zur Leistungssteigerung kann der Wirkungsgrad dieses Zyklus jedoch verbessert werden. Ein Beispiel dafür ist der Reheat-Zyklus, bei dem der Dampf nach einer ersten Expansion in der Turbine erneut aufgeheizt wird, bevor er weiter expandiert. Dies ermöglicht es, eine höhere Temperatur und damit eine bessere Energieumwandlung zu erreichen, was zu einer insgesamt höheren Betriebsleistung führt.
Zusätzlich zu klassischen Technologien gibt es in der Dampfturbinentechnologie auch eine Reihe von innovationsgetriebenen Ansätzen, die sich zunehmend durchsetzen. Ein interessantes Beispiel ist der Einsatz von Abwärmenutzung. In vielen Industrien, die Dampfturbinen betreiben, fällt Abwärme an, die häufig ungenutzt bleibt. Allerdings gibt es mittlerweile zunehmend Technologien zur Abwärmenutzung, wie z.B. Rankine-Kreisprozesse mit organischen Arbeitsflüssigkeiten (ORC – Organic Rankine Cycle), bei denen auch bei niedrigen Temperaturen Wärme in Energie umgewandelt wird. Solche Systeme können durch den Anschluss an die Dampfturbine eine gesamtheitliche Effizienzsteigerung und zusätzliche Energieproduktion bieten.
Ein weiteres aufkommendes Konzept ist die integrierte Dampfturbine in hybride Systeme. Wärmepumpen oder Gasturbinen können mit Dampfturbinen kombiniert werden, um die Effizienz noch weiter zu steigern. Solche hybriden Systeme ermöglichen eine verbesserte Nutzung von Wärmequellen, die in der Vergangenheit als weniger effizient galten, insbesondere in Systemen, die bereits eine hohe Abwärmeproduktion aufwiesen. Diese Kombination von Wärmequellen und -technologien führt zu einer maximalen Effizienz und einer Verringerung der CO2-Emissionen, was einen weiteren Schritt in Richtung nachhaltiger Energiegewinnung darstellt.
Die Entwicklung und Optimierung von modernen Materialien sind ebenfalls ein Schlüsselfaktor für die Zukunft der Dampfturbinen. Der Einsatz von hochtemperaturbeständigen Materialien für Turbinenblätter und andere kritische Komponenten ermöglicht es, die Betriebstemperaturen weiter zu erhöhen, was wiederum die Effizienz der Turbine steigert. Dies wird vor allem durch die Verwendung von keramischen Beschichtungen oder hochfesten Nickellegierungen erreicht, die auch unter extremen Temperaturbedingungen ihre Festigkeit bewahren und den Verschleiß der Bauteile reduzieren. Ein weiterer technologischer Fortschritt betrifft die additive Fertigung (3D-Druck), bei der Turbinenkomponenten wie Leitschaufeln mit äußerst komplexen Geometrien hergestellt werden können, um die Strömungseigenschaften zu optimieren und den Druckverlust zu minimieren.
Auf der Betriebsebene wird die Automatisierung der Dampfturbinenbetriebsführung zunehmend wichtiger. Der Einsatz von Künstlicher Intelligenz (KI) und Maschinellem Lernen (ML) ermöglicht eine optimierte Betriebsführung und eine Fehlerprognose. Durch kontinuierliche Datenanalysen und Echtzeitüberwachung können Störungen vorhergesagt werden, bevor sie eintreten, was nicht nur die Wartungskosten reduziert, sondern auch die Verfügbarkeit der Turbine maximiert. KI-gestützte Systeme können zudem dabei helfen, die Betriebsbedingungen ständig anzupassen und die Effizienz der Turbine in Echtzeit zu optimieren.
Die fortschreitende Digitalisierung und Vernetzung von Dampfturbinen ermöglicht auch die Einführung von Fernüberwachung und Fernwartung. Diese Technologien erlauben es Betreibern, Turbinen aus der Ferne zu überwachen und notwendige Wartungsmaßnahmen oder Einstellungen in Echtzeit vorzunehmen. Dies reduziert den Bedarf an physischer Präsenz und manuellen Eingriffen und stellt sicher, dass die Turbine auch dann effizient läuft, wenn der Betrieb in abgelegenen oder schwer zugänglichen Gebieten stattfindet.
Ein weiterer Schritt in der Zukunft der Dampfturbinen ist die Integration von Wasserstoff als Brennstoffquelle. Wasserstoff gilt als einer der vielversprechendsten Energieträger der Zukunft, da er bei der Verbrennung keine CO2-Emissionen erzeugt. In Kombination mit Dampfturbinen könnte Wasserstoff dazu beitragen, die CO2-Emissionen in der Energieproduktion deutlich zu senken. Insbesondere in Kraftwerken, die derzeit auf fossile Brennstoffe angewiesen sind, könnte der Umstieg auf Wasserstoff als Brennstoffquelle eine der effektivsten Methoden zur Dekarbonisierung der Energieerzeugung darstellen.
Ein weiteres Forschungsgebiet betrifft die Dampfturbinen in der Schiffsindustrie. Der Einsatz von Dampfturbinen auf Schiffen ist traditionell weit verbreitet, vor allem bei großen Passagierschiffen, Frachtern und Kriegsschiffen, die hohe Geschwindigkeiten oder große Reichweiten benötigen. Doch die Anforderungen an die Effizienz und Umweltverträglichkeit werden immer strenger. Gaskraftwerke, die mit Dampfturbinen kombiniert werden, und die Nutzung von LNG (Flüssigerdgas) oder Wasserstoff als Kraftstoff stellen neue Möglichkeiten dar, den CO2-Ausstoß von Schiffen zu reduzieren und gleichzeitig die Energieeffizienz der Dampfturbinen zu maximieren. Dies könnte langfristig dazu beitragen, dass auch in der Schifffahrt eine nachhaltige Energieversorgung durch Dampfturbinen erreicht wird.
Zusammenfassend lässt sich sagen, dass Dampfturbinen, trotz ihrer langen Geschichte, durch fortlaufende Innovationen und Anpassungen an die modernen Anforderungen der Energieproduktion und -verwertung immer relevanter werden. Die Integration von erneuerbaren Energien, digitaler Intelligenz, hybriden Systemen und fortschrittlichen Materialien wird eine zentrale Rolle dabei spielen, die Effizienz weiter zu steigern und die CO2-Emissionen zu reduzieren. Die Dampfturbine bleibt somit ein technologisches Rückgrat der globalen Energieversorgung, das sich kontinuierlich an die Herausforderungen der Zukunft anpasst.
Überwachungs- und Steuerungssystem der Dampfturbine

Das Überwachungs- und Steuerungssystem einer Dampfturbine ist entscheidend, um die Betriebsbedingungen zu optimieren, eine sichere Funktionsweise zu gewährleisten und eine höchstmögliche Effizienz zu erzielen. Solche Systeme bestehen aus verschiedenen Sensoren, Aktoren, Reglern und Computern, die zusammenarbeiten, um die Dampfturbine in Echtzeit zu überwachen und die Leistung zu steuern. Sie tragen auch dazu bei, Wartungsbedarfe frühzeitig zu erkennen und den Betriebsablauf zu optimieren, was zu einer erhöhten Lebensdauer und geringeren Betriebskosten führt.
1. Überwachungssysteme – Datenerfassung und Monitoring
Die Überwachung einer Dampfturbine erfolgt über ein Netzwerk von Sensoren, die an verschiedenen kritischen Stellen der Turbine und ihrer Umgebung installiert sind. Diese Sensoren erfassen eine Vielzahl von Betriebsparametern, die für den sicheren Betrieb und die Effizienz entscheidend sind:
- Dampfdruck: Der Dampfdruck wird in verschiedenen Bereichen der Turbine überwacht, insbesondere im Einlassbereich, während der Expansion und im Abzweig zum Kondensator. Ein abnormaler Druckabfall könnte auf ein Problem in der Dampfturbine oder in der Dampferzeugung hindeuten.
- Temperatur: Die Temperatur des Dampfs wird sowohl im Einlass als auch an verschiedenen Punkten der Turbine gemessen. Überhitzung oder unterschiedliche Temperaturzonen im Turbinensystem können auf eine ineffiziente Wärmeübertragung oder mechanische Probleme hinweisen.
- Dampfstromrate: Die Menge an Dampf, die durch die Turbine strömt, muss überwacht werden, um eine gleichmäßige Leistung und die Einhaltung der Turbinenkapazität sicherzustellen. Eine Abweichung von der erwarteten Stromrate könnte auf Leckagen oder unzureichende Dampferzeugung hinweisen.
- Vibrationen: Sensoren, die die Schwingungen und Vibrationen der Turbinenwelle messen, sind essenziell, um mechanische Probleme wie Unwuchten oder lagermäßige Probleme frühzeitig zu erkennen. Anormale Vibrationen können auf strukturelle Schwächen oder fehlerhafte Lager hinweisen.
- Schmierung: Sensoren überwachen auch die Schmierung der Turbine, insbesondere die Schmierung der Wellenlager. Ein Öldruckabfall oder ein Anstieg der Öltemperatur kann auf Probleme mit dem Schmierölkreislaufsystem hinweisen.
- Betriebsstunden und Verschleiß: Das System erfasst die Betriebsstunden der Turbine und die kumulierten Lastzyklen. Dies hilft, den Verschleiß der kritischen Komponenten zu überwachen und Wartungsbedarfe besser abzuschätzen.
Die gesammelten Daten werden in Echtzeit an eine zentrale Steuerstation übermittelt, wo sie analysiert und visualisiert werden, um eine klare Übersicht über den Zustand der Turbine zu bieten.
2. Steuerungssysteme – Anpassung der Betriebsparameter
Das Steuerungssystem einer Dampfturbine verwendet die erfassten Daten, um Drehzahlen, Dampfdurchflussmengen, Dampfdruck und Temperaturen so zu steuern, dass die Turbine unter optimalen Bedingungen läuft. Das Steuerungssystem besteht in der Regel aus:
- Prozessreglern: Diese regeln die wichtigsten Betriebsparameter wie Dampfdruck und -temperatur. Sie stellen sicher, dass der Dampf die richtige Temperatur und den richtigen Druck hat, um maximale Effizienz zu erzielen. Die Regler verwenden Feedback-Mechanismen, um automatisch Anpassungen vorzunehmen, wenn die Werte außerhalb des gewünschten Bereichs liegen.
- Lastregelung: Das System überwacht die Lastanforderungen (die benötigte elektrische Leistung) und passt die Brennstoffzufuhr, den Dampfdruck und die Turbinenleistung an, um die Leistung der Dampfturbine zu optimieren. In einem Kraftwerk mit mehreren Dampfturbinen sorgt das Steuerungssystem dafür, dass alle Turbinen aufeinander abgestimmt sind, um eine gleichmäßige Verteilung der Last zu gewährleisten.
- Ventilsteuerung: Das Steuerungssystem regelt auch die Stellventile, die den Dampfdurchfluss in die Turbine und zu den verschiedenen Turbinenstufen regulieren. Diese Ventile sind entscheidend, um den Dampffluss je nach Betriebsbedingungen optimal zu steuern.
- Kondensatsteuerung: Die Menge und der Druck des Kondensats, das den Kondensator verlässt, müssen ständig überwacht und reguliert werden, um die Effizienz der Turbine zu maximieren. Zu viel Kondensat kann zu einem Überdruck im System führen, während zu wenig Kondensat die Kühlleistung beeinträchtigen könnte.
- Sicherheitssteuerung: Falls kritische Werte überschritten werden – etwa bei zu hohem Druck oder zu hoher Temperatur – aktiviert das Steuerungssystem Sicherheitsmechanismen wie Dampfabschaltungen, Notventile oder Überdrucksicherungssysteme, um die Turbine vor Beschädigungen zu schützen.
3. Automatisierung und intelligente Steuerung
Moderne Dampfturbinen sind zunehmend mit Automatisierungssystemen ausgestattet, die durch Künstliche Intelligenz (KI) und Maschinelles Lernen (ML) den Betrieb optimieren. Diese Systeme gehen über die herkömmliche Regelung hinaus und ermöglichen eine dynamische Anpassung der Betriebsparameter basierend auf Echtzeitdaten und historischen Betriebsdaten. Solche intelligenten Systeme können:
- Anomalien vorhersagen: KI-gestützte Systeme erkennen Muster in den gesammelten Betriebsdaten und können potenzielle Fehlfunktionen oder Störungen vorhersagen, noch bevor sie auftreten. Dadurch können präventive Wartungsmaßnahmen eingeleitet werden, um Ausfälle zu vermeiden.
- Leistung optimieren: Basierend auf den Betriebsbedingungen und der Nachfrage passt das System automatisch die Brennstoffzufuhr, den Dampfdruck und die Betriebsbedingungen an, um eine maximale Energieausbeute bei minimalen Betriebskosten zu erzielen.
- Fehlerdiagnose und Wartungsprognose: Anhand von Datenanalysen und Predictive Maintenance (vorausschauende Wartung) werden die komplexen Mechanismen der Dampfturbine überwacht, sodass Probleme frühzeitig erkannt werden können. Dadurch können Wartungsmaßnahmen effizient geplant werden, um Ausfälle zu minimieren und die Lebensdauer der Turbine zu verlängern.
4. Fernüberwachung und -steuerung
Die Fernüberwachung und Fernsteuerung von Dampfturbinen wird zunehmend verbreitet, vor allem bei großen Anlagen oder in Bereichen, in denen der Betrieb an abgelegenen Standorten erfolgt. Mit modernen Cloud-basierten Plattformen können Techniker und Betriebsleiter in Echtzeit auf Daten zugreifen und die Turbine aus der Ferne überwachen und steuern. Diese Art der Fernsteuerung ermöglicht es, Eingriffe sofort vorzunehmen, ohne dass eine physische Präsenz vor Ort erforderlich ist.
- Cloud-basierte Systeme ermöglichen eine kontinuierliche Datenübertragung und -speicherung, was eine detaillierte historische Analyse und Trendprognose erlaubt. Diese Daten können genutzt werden, um langfristige Wartungsstrategien zu entwickeln und Betriebsbedingungen zu optimieren.
- Mobile Apps und remote Dashboards geben Ingenieuren und Betreibern auch die Möglichkeit, Alarme und Warnmeldungen sofort auf ihren mobilen Geräten zu erhalten, was eine schnelle Reaktion auf potenzielle Probleme ermöglicht.
5. Integration mit anderen Systemen
Das Überwachungs- und Steuerungssystem einer Dampfturbine ist in der Regel nicht isoliert, sondern Teil eines größeren Leitsystems eines Kraftwerks oder einer Industrieanlage. Es ist eng mit anderen Systemen wie Kesselsteuerungen, Generatorsteuerungen, Kondensatoren und Kühlwassersystemen verbunden. Diese Systeme arbeiten zusammen, um den gesamten Prozessablauf zu optimieren und sicherzustellen, dass alle Komponenten harmonisch zusammenarbeiten.
Ein gutes Beispiel ist die Kombikraftwerkssteuerung, bei der Dampfturbinen mit Gasturbinen in einer GuD-Anlage (Gas- und Dampfturbinenkraftwerk) integriert sind. In solchen Systemen müssen die Abgasströme der Gasturbine überwacht und die Dampfproduktion auf Basis der Gasturbine optimiert werden. Die Lastregelung muss in beiden Systemen koordiniert werden, um die Gesamtleistung des Kraftwerks zu maximieren.
Zusammenfassung
Das Überwachungs- und Steuerungssystem einer Dampfturbine ist ein hochkomplexes und dynamisches System, das aus verschiedenen Sensortechnologien, Steuermechanismen und intelligenter Automatisierung besteht. Diese Systeme sorgen dafür, dass die Dampfturbine unter optimalen Bedingungen arbeitet, eine hohe Energieeffizienz erreicht und gleichzeitig Sicherheitsrisiken minimiert werden. Moderne Technologien wie KI, Predictive Maintenance und Fernüberwachung ermöglichen es, die Leistung der Dampfturbine kontinuierlich zu optimieren und ihre Lebensdauer zu verlängern, was sie zu einem wesentlichen Bestandteil der modernen Energieinfrastruktur macht.
Die Weiterentwicklung von Überwachungs- und Steuerungssystemen in Dampfturbinen geht immer mehr in Richtung intelligente Prozesssteuerung und automatisierte Fehlerbehebung. In modernen Anlagen ist das Ziel, nicht nur die Betriebsparameter zu überwachen, sondern auch die gesamte Prozesskette effizient zu gestalten. Ein wichtiger Bestandteil ist die Integration von Smart Sensors und Edge Computing, bei dem die Datenverarbeitung nicht nur zentral in einem Server stattfindet, sondern auch direkt an den Sensoren oder an Knotenpunkten im Netzwerk. Dies ermöglicht eine sofortige Analyse der erfassten Daten und eine schnellere Entscheidungsfindung. Ein Vorteil ist, dass die Kommunikationslatenz minimiert wird, sodass Probleme sofort lokal erkannt und behoben werden können, ohne dass eine Verzögerung durch zentrale Systeme entsteht.
Ein weiteres wichtiges Konzept in der modernen Überwachungstechnik ist die Zustandsüberwachung. Hierbei wird nicht nur der Betrieb der Dampfturbine selbst verfolgt, sondern auch der Zustand der Hauptkomponenten, wie Lagersysteme, Wellen, Turbinenblätter und Schaufeln. Die Überwachung der Komponenten wird durch Technologien wie ultraschallbasierte Sensoren, Schwingungsanalyse und thermografische Inspektionen ergänzt, um frühzeitig potenzielle Verschleißerscheinungen oder Fehlfunktionen zu identifizieren. Diese Technologien ermöglichen eine genauere Diagnose und bieten eine detailliertere Fehlerursachenanalyse, was es ermöglicht, Wartungsmaßnahmen gezielt und rechtzeitig durchzuführen.
Zukünftige Entwicklungen konzentrieren sich zunehmend auf vorausschauende Wartung (Predictive Maintenance). Hierbei wird das Verhalten der Dampfturbine über längere Zeiträume hinweg analysiert, um Verbrauchsdaten und Betriebsdaten zu nutzen, um den Verschleiß von Turbinenkomponenten zu prognostizieren. Maschinelles Lernen kann dabei helfen, komplexe Muster in den Datenströmen zu erkennen und so Wartungszyklen zu optimieren. Anstatt auf regelmäßige Wartungsintervalle angewiesen zu sein, werden diese Systeme so eingestellt, dass sie Wartungsmaßnahmen genau dann anstoßen, wenn sie am dringendsten erforderlich sind, was wiederum den Stillstand der Turbine minimiert und die Kosten für unnötige Wartungsarbeiten reduziert.
Ein weiterer innovativer Ansatz ist die Energieverbrauchsanalyse in Echtzeit. Überwachungssysteme können nicht nur den Betrieb der Dampfturbine steuern, sondern auch den Energieverbrauch der gesamten Anlage optimieren. In Kombination mit Energieverbrauchs-Managementsystemen (EMS) können diese Systeme den Gesamtwirkungsgrad der Anlage überwachen und Steuerungsmaßnahmen empfehlen, um die Energieeffizienz zu maximieren. Dazu gehört auch die Optimierung des Brennstoffverbrauchs und der Dampferzeugung, sodass sowohl bei steigender Last als auch bei Teillastbetrieb die Turbine immer mit der maximalen Effizienz läuft.
Ein Aspekt, der zunehmend wichtiger wird, ist die Integration von erneuerbaren Energien in das Dampfturbinen-Steuerungssystem. Wenn Dampfturbinen in Kraft-Wärme-Kopplungsanlagen oder in hybriden Systemen mit Solarenergie, Windenergie oder Biomasse betrieben werden, müssen die Steuerungssysteme so programmiert werden, dass sie flexibel auf die Schwankungen der erneuerbaren Energiequellen reagieren. Das bedeutet, dass die Dampfturbine dynamisch angepasst werden muss, um mit der Verfügbarkeit von Solar- oder Windenergie zu harmonisieren. Hier können intelligente Steuerungssysteme helfen, den Brennstoffverbrauch zu minimieren und gleichzeitig die Lastanforderungen zu erfüllen.
Moderne Kommunikationssysteme spielen ebenfalls eine große Rolle, besonders in großen, weit verteilten Industriestandorten oder Energieanlagen. Die Integration von IoT (Internet der Dinge) ermöglicht die Verbindung von Dampfturbinen mit anderen industriellen Systemen, um eine ganzheitliche Überwachung und Steuerung zu gewährleisten. Dies schafft eine transparente Infrastruktur, in der jede Turbine, jedes Modul und jede Komponente miteinander kommunizieren kann, um koordiniert und effizient zu arbeiten.
Zusätzlich zur Hardware können diese Systeme auch Software-basierte Tools zur Simulation und Modellierung des Dampfturbinenbetriebs beinhalten. Durch die Nutzung von modernen Algorithmen und digitale Zwillinge der Turbine lassen sich Betriebsverläufe in einer virtuellen Umgebung modellieren, um die Auswirkungen von Änderungen in den Betriebsbedingungen vorherzusagen. Diese Simulationen bieten wertvolle Erkenntnisse, wie die Turbine unter unterschiedlichen Szenarien reagieren würde, und ermöglichen eine noch präzisere Steuerung und Fehlerdiagnose.
Ein weiterer bemerkenswerter Trend ist die Integration von Sicherheitsüberwachung in das Gesamtsystem. Während das Überwachungs- und Steuerungssystem die Leistungsparameter der Dampfturbine in Echtzeit überwacht, stellt es gleichzeitig sicher, dass alle sicherheitsrelevanten Grenzwerte eingehalten werden. Dies umfasst nicht nur die Überwachung von Druck und Temperatur, sondern auch von Strukturschäden, die möglicherweise durch Ermüdung oder Korrosion entstehen können. In solchen Fällen werden Alarme ausgelöst und das System führt eine sofortige Notabschaltung durch, um Schäden zu verhindern. Diese Sicherheitsmechanismen sind in die gesamte Steuerungstechnik eingebettet und können in Echtzeit die kritischen Parameter anpassen.
Schließlich spielt auch die Benutzeroberfläche eine wichtige Rolle. Das Steuerungssystem einer Dampfturbine ist oft mit einer grafischen Benutzeroberfläche (GUI) ausgestattet, die es den Bedienern ermöglicht, alle wichtigen Betriebsdaten auf einen Blick zu sehen. Diese Benutzeroberflächen sind intuitiv gestaltet und ermöglichen eine schnelle Identifizierung von Anomalien oder Fehlfunktionen. Über Dashboards können alle relevanten Parameter angezeigt werden, und durch Alarmfunktionen erhalten Betreiber frühzeitig eine Warnung, wenn etwas außerhalb der Toleranzbereiche liegt.
Alles in allem ist das Überwachungs- und Steuerungssystem der Dampfturbine eine hochentwickelte Kombination aus Sensorik, Automatisierung, intelligenter Software und Kommunikationstechnologie, die zusammenarbeiten, um eine effiziente, sichere und umweltfreundliche Nutzung von Dampfturbinen in der modernen Energieproduktion zu gewährleisten.
Die kontinuierliche Weiterentwicklung der Überwachungs- und Steuerungssysteme für Dampfturbinen hat nicht nur technische Vorteile, sondern trägt auch zur Nachhaltigkeit und Reduzierung der CO₂-Emissionen bei. Dies ist besonders relevant, da Kraftwerke und industrielle Anlagen, die Dampfturbinen nutzen, weltweit einen wesentlichen Teil der globalen Emissionen verursachen. Die Energieoptimierung durch moderne Überwachungs- und Steuerungssysteme ist daher ein Schritt in Richtung einer grüneren Energieproduktion. Durch die ständige Anpassung und präzise Steuerung des Betriebs können Dampfturbinen effizienter betrieben werden, was zu einer Reduktion des Brennstoffverbrauchs und damit auch zu einer Vermeidung von Emissionen führt.
Ein weiteres zukunftsweisendes Konzept ist die Integration von Batterietechnologien in Dampfturbinenanlagen. Die Kombination von Batteriespeichern und Dampfturbinen kann dazu beitragen, die Stabilität des Netzes zu erhöhen, indem überschüssige Energie gespeichert und bei Bedarf wieder eingespeist wird. In Energieverbundsystemen, in denen Dampfturbinen als Teil eines Hybridsystems mit Batteriespeichern arbeiten, kann das Steuerungssystem dynamisch entscheiden, wann die Dampfturbine betrieben wird und wann die Batterien zur Deckung der Nachfrage beitragen. Diese Flexibilität ermöglicht es, den Energiefluss effizienter zu gestalten und den CO2-Ausstoß weiter zu minimieren.
Die Energieeffizienz von Dampfturbinen kann auch durch den Einsatz von hochmodernen Wärmerückgewinnungssystemen weiter optimiert werden. Ein solches System ermöglicht es, die Abwärme der Dampfturbine in andere Prozesse zu integrieren, sei es in der Heiztechnik oder in industriellen Prozessen. Diese Systeme verwenden ebenfalls Überwachungstechnologien, um die Temperatur und den Dampfdruck des Abgases zu messen und die Wärmerückgewinnung zu steuern, um die Effizienz des gesamten Systems zu erhöhen.
Darüber hinaus spielt die Digitale Transformation in der Wartungs- und Überwachungstechnik eine immer größere Rolle. Durch den Einsatz von Big Data und Cloud Computing können große Mengen an Betriebsdaten gesammelt, gespeichert und analysiert werden. Dies ermöglicht nicht nur eine detailliertere Einsicht in die Betriebsabläufe, sondern auch eine bessere Entscheidungsfindung. Dank der Fortschritte in der Datenverarbeitung können Unternehmen und Betreiber von Dampfturbinen ihre Wartungsstrategien weiter verbessern, indem sie Wartungspläne dynamisch an den tatsächlichen Zustand der Turbine anpassen. Das bedeutet, dass Wartungsarbeiten nicht länger nach festen Zeitplänen erfolgen müssen, sondern in Reaktion auf tatsächliche Betriebsbedingungen und Verschleißmuster durchgeführt werden. Diese Strategie reduziert Kosten, da nur dann gewartet wird, wenn es tatsächlich notwendig ist.
Ein weiteres bedeutendes Element der digitalen Transformation in der Dampfturbinenüberwachung ist der Einsatz von Augmented Reality (AR) und Virtual Reality (VR). Ingenieure und Techniker können diese Technologien nutzen, um virtuelle Modelle der Dampfturbinen zu erstellen und zu simulieren, wie sich verschiedene Betriebsbedingungen auf das gesamte System auswirken. Diese Modelle ermöglichen eine präzisere Planung und eine schnellere Fehlerbehebung, da potenzielle Probleme bereits in der Planungsphase erkannt und behoben werden können. AR und VR können auch als Schulungswerkzeuge für Betreiber und Wartungspersonal eingesetzt werden, um ein besseres Verständnis für den Turbinenbetrieb und für die Durchführung von Wartungsarbeiten zu vermitteln.
Die zunehmende Automatisierung und die intelligente Steuerung der Dampfturbinen erfordert auch eine gute Schulung und Weiterbildung des Betriebs- und Wartungspersonals. Es ist notwendig, dass das Personal mit den neuen Überwachungstechnologien und Steuerungssystemen vertraut ist, um in der Lage zu sein, die Systeme effizient zu bedienen und im Falle eines Problems schnell und richtig zu reagieren. Hierbei spielen Simulationen, Schulungen und die Ausbildung im Umgang mit modernen Steuerungs- und Diagnosesystemen eine wichtige Rolle. Durch die kontinuierliche Weiterbildung wird sichergestellt, dass das Personal nicht nur in der Lage ist, auf alltägliche Betriebsbedingungen zu reagieren, sondern auch auf ungewöhnliche Ereignisse, die während des Betriebs auftreten können.
Schließlich müssen auch die Energiepreise und marktbedingte Schwankungen berücksichtigt werden. Mit der zunehmenden Nachfrage nach Erneuerbaren Energien und der Unberechenbarkeit von Stromerzeugung und -verbrauch erfordert es eine flexible und dynamische Steuerung der Dampfturbinen, um auf die unterschiedlichen Marktbedingungen reagieren zu können. Dies wird durch moderne Steuerungssysteme unterstützt, die in der Lage sind, nicht nur den Betriebsablauf zu optimieren, sondern auch wirtschaftliche Zielgrößen wie den Kraftwerksertrag und den Strompreis in die Steuerung der Turbinen zu integrieren.
Insgesamt bedeutet die kontinuierliche Weiterentwicklung der Überwachungs- und Steuerungstechnik von Dampfturbinen nicht nur eine Verbesserung der Betriebs- und Wartungseffizienz, sondern auch einen entscheidenden Beitrag zur Nachhaltigkeit und Energieeffizienz in der globalen Energieversorgung. Die Turbinen werden immer intelligenter, effizienter und sicherer, was es ermöglicht, den Brennstoffverbrauch zu minimieren, den CO2-Ausstoß zu reduzieren und die Langlebigkeit der Anlagen zu maximieren. Dies spielt eine wichtige Rolle in der globalen Energiezukunft und hilft dabei, die Energieversorgung auf eine umweltfreundlichere und nachhaltigere Weise zu gestalten.
Ein weiterer zentraler Aspekt, der zunehmend in den Fokus rückt, ist die Integration von intelligenten Netzen (Smart Grids), die eine direkte Kommunikation und Interaktion zwischen Dampfturbinen und anderen Energiequellen oder -verbrauchern ermöglichen. In einem Smart Grid können Dampfturbinen nicht nur auf Energiebedarf reagieren, sondern auch aktiv in die Netzsteuerung eingebunden werden. So können Turbinen je nach Bedarf schnell hoch- oder heruntergefahren werden, um Spitzenlasten auszugleichen oder eine versorgungsunterbrechung zu vermeiden. Dies steigert die Flexibilität und Resilienz des Stromnetzes erheblich.
Dank der Automatisierung und den fortschrittlichen Überwachungssystemen können Betreiber auf Echtzeitdaten zugreifen, die es ihnen ermöglichen, den Zustand der Turbinen und die allgemeine Netzstabilität besser zu verstehen. Das bedeutet, dass die Dampfturbine aktiv zur Lastregelung des Netzes beitragen kann, indem sie je nach Netzanforderungen den Stromfluss anpasst. Diese Art der dynamischen Integration hilft nicht nur, die Netzfrequenz stabil zu halten, sondern optimiert auch die Verteilung von Erneuerbaren Energien, die schwankende Erträge aufweisen.
Das Zusammenspiel von Dampfturbinen und Speichersystemen, wie Pumpspeicherkraftwerken oder Batteriespeichern, wird ebenfalls zunehmend relevant. Wenn überschüssige Energie erzeugt wird, können Dampfturbinen in Kombination mit Speichertechnologien genutzt werden, um diese Energie zu speichern und bei Bedarf wieder ins Netz einzuspeisen. Diese Technologie hilft, die Stromerzeugung aus erneuerbaren Quellen wie Wind und Solar zu stabilisieren, deren Leistung aufgrund von Wetterschwankungen oft variieren kann. Dampfturbinen können als flexible Energiequelle fungieren, die eine lückenlose Stromversorgung gewährleistet, auch wenn die regenerativen Quellen vorübergehend keine Energie liefern.
Ein weiterer innovativer Trend ist der Einsatz von Wasserstofftechnologie in Verbindung mit Dampfturbinen. Hierbei werden Dampfturbinen in Kombination mit Wasserstoffkraftwerken genutzt, um grünen Wasserstoff zu erzeugen. Wasserstoff kann als zwischenzeitlicher Brennstoff in Zeiten hoher Nachfrage oder unzureichender erneuerbarer Energieproduktion dienen. In einem solchen Szenario könnte die Dampfturbine auf grünen Wasserstoff umgeschaltet werden, um die CO2-Emissionen weiter zu reduzieren. Die Umstellung auf Wasserstoff als Brennstoff stellt eine wichtige Weiterentwicklung für die Turbinenindustrie dar, da sie einen nachhaltigen Übergang zu einem kohlenstofffreien Energiesystem unterstützt.
Zusätzlich zur Verbesserung der Brennstoffnutzung gibt es auch eine zunehmende Integration von Abwärmenutzung aus Dampfturbinen. Diese Abwärme kann in anderen industriellen Prozessen oder für die Heizung von Gebäuden verwendet werden. Indem die Wärme, die während des Dampfturbinenbetriebs ungenutzt abgegeben wird, in Wärmenetze eingespeist wird, kann die Gesamtenergieeffizienz eines Kraftwerks weiter gesteigert werden. Dies reduziert den gesamten Energiebedarf und trägt zur Verringerung der CO2-Emissionen bei. Solche Kraft-Wärme-Kopplungssysteme ermöglichen es, sowohl Strom als auch Wärme gleichzeitig und effizient zu erzeugen.
Ein entscheidender Faktor in der Weiterentwicklung von Dampfturbinen sind auch die Forschung und Entwicklung (F&E), die ständig neue Technologien und Materialien hervorbringen. So werden beispielsweise zunehmend hitzebeständige und korrosionsbeständige Materialien entwickelt, die die Lebensdauer von Dampfturbinen verlängern und ihre Effizienz steigern. Diese neuen Materialien ermöglichen es, die Betriebstemperaturen der Dampfturbinen weiter zu erhöhen, wodurch auch die Thermodynamik des gesamten Systems verbessert wird. Die Verbesserung der Werkstofftechnologie ist dabei ein Schlüsselfaktor, um die effizienten Betriebsbedingungen bei gleichzeitig geringeren Wartungsanforderungen und längeren Wartungszyklen zu gewährleisten.
Die Zukunft der Dampfturbinen wird zunehmend von einer ganzheitlichen Sichtweise geprägt, die nicht nur den Betrieb der Turbinen optimiert, sondern auch die gesamte Energieinfrastruktur berücksichtigt. Diese Perspektive umfasst die Kombination von flexiblen Energiequellen, fortschrittlicher Steuerungstechnik, intelligenter Netzintegration und der Nutzung von erneuerbaren Energien. Dampfturbinen werden zunehmend als moderne, intelligente und nachhaltige Maschinen betrachtet, die in einer zukünftigen Energiewelt eine bedeutende Rolle spielen, in der Energieerzeugung, Verbrauch und Speicherung optimiert und nachhaltig gestaltet werden.
Zusammengefasst lässt sich sagen, dass die Zukunft der Dampfturbinen durch die Vernetzung und die Integration modernster Technologien geprägt wird. Sie werden nicht nur als Energieerzeuger betrachtet, sondern auch als intelligente Komponenten eines integrierten, flexiblen und nachhaltigen Energiesystems. Die kontinuierliche Verbesserung von Überwachungssystemen, die Entwicklung von neuen Materialien, die digitale Transformation der Wartung sowie die Integration in Smart Grids und erneuerbare Energien sind die Treiber dieser Entwicklung und tragen dazu bei, dass Dampfturbinen einen wichtigen Beitrag zur CO₂-Reduktion und zur Energieeffizienz leisten können.
Drucksensoren der Dampfturbine
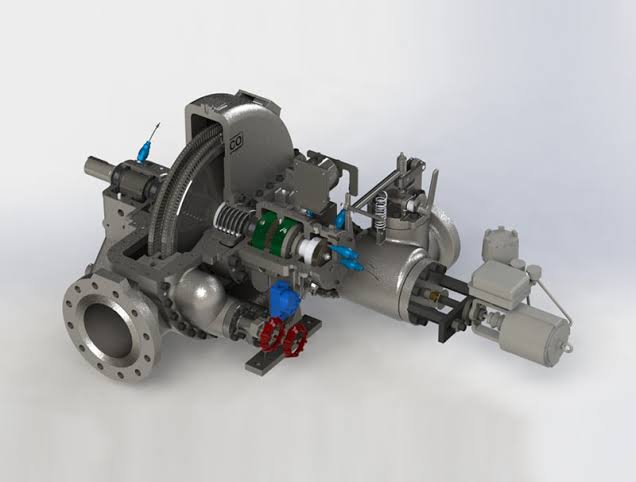
Drucksensoren spielen eine zentrale Rolle in der Überwachung und Steuerung von Dampfturbinen. Sie sind unverzichtbar, um den Dampfdruck in verschiedenen Abschnitten des Turbinenkreislaufs präzise zu messen und so den sicheren und effizienten Betrieb der Turbine zu gewährleisten. Der Druck des Dampfes ist ein entscheidender Parameter für die Leistungsfähigkeit und die Stabilität der Dampfturbine. Werden die Druckwerte nicht korrekt überwacht, können schwerwiegende Probleme wie Energieverluste, Überhitzung oder sogar mechanische Schäden an der Turbine entstehen.
Arten von Drucksensoren
Es gibt verschiedene Arten von Drucksensoren, die in Dampfturbinen eingesetzt werden:
- Piezoelektrische Drucksensoren: Diese Sensoren nutzen den piezoelektrischen Effekt, bei dem sich die elektrische Spannung ändert, wenn Druck auf das Material ausgeübt wird. Diese Sensoren sind besonders für kurzfristige Druckspitzen geeignet und werden in Dampfturbinen verwendet, um schnelle Änderungen im Dampfdruck zu erfassen.
- Kapazitive Drucksensoren: Diese Sensoren messen Änderungen im Abstand zwischen zwei Platten, die von dem Druck auf ein Material beeinflusst werden. Sie sind äußerst präzise und bieten eine hohe Langzeitstabilität, weshalb sie in Dampfturbinen weit verbreitet sind, um den Druck im Betrieb kontinuierlich zu überwachen.
- Membranbasierte Drucksensoren: Diese Sensoren enthalten eine flexible Membran, die sich unter Druck verformt. Die Membranbewegung wird in ein elektrisches Signal umgewandelt, das den Druck im System widerspiegelt. Diese Sensoren sind besonders robust und eignen sich gut für den Einsatz in den extremen Bedingungen einer Dampfturbine.
- Drucktransmitter: Ein Drucktransmitter besteht in der Regel aus einem Drucksensor und einem Signalumwandlungssystem. Der Sensor erfasst den Dampfdruck und wandelt diesen in ein elektronisches Signal um, das an das Steuerungssystem weitergeleitet wird. Solche Transmitter sind besonders nützlich, um den Druck in schwer zugänglichen Bereichen der Dampfturbine zu überwachen.
Einsatz von Drucksensoren in Dampfturbinen
Drucksensoren werden an verschiedenen Stellen im Dampfturbinenkreislauf eingesetzt, um unterschiedliche Druckwerte zu messen und zu überwachen:
- Eingangsdruck (Dampferzeugung): Am Eingang der Dampfturbine wird der Druck des erzeugten Dampfs gemessen, der in der Regel durch einen Kessel oder ein anderes Dampferzeugungssystem erzeugt wird. Ein stabiler Dampfdruck ist für eine optimale Energieerzeugung und den effizienten Betrieb der Turbine entscheidend.
- Druck im Turbinenstator: Innerhalb der Dampfturbine gibt es verschiedene Druckniveaus, die überwacht werden müssen, um die Effizienz des Turbinenbetriebs sicherzustellen. Drucksensoren im Turbinenstator messen den Druck des Dampfes, bevor er auf die Laufschaufeln trifft. Diese Messung ist wichtig, um sicherzustellen, dass der Dampf in die richtige Richtung strömt und die Schaufeln optimal angetrieben werden.
- Druck nach den Schaufeln (Exhaust): Am Ende der Turbine wird der Austrittsdruck des Dampfs gemessen. Der Druck am Turbinenende gibt Aufschluss über die Effizienz des gesamten Prozesses. Ein zu niedriger Austrittsdruck kann auf Probleme wie eine unzureichende Dampferzeugung oder Leckagen hinweisen, während ein zu hoher Druck auf ein unzureichendes Entspannungsniveau des Dampfs hindeutet.
- Kondensator- und Wärmetauscher-Drucküberwachung: Nach der Turbine wird der Dampf häufig durch einen Kondensator geführt, wo er abgekühlt und kondensiert wird. Der Druck im Kondensator muss präzise überwacht werden, um sicherzustellen, dass der Dampf kondensiert und das System richtig funktioniert. Ein zu hoher Druck im Kondensator könnte auf einen Blockadeffekt hinweisen, während zu niedrige Drücke zu einem ineffizienten Betrieb führen können.
- Konditionierung und Wartung der Drucksensoren: Drucksensoren in Dampfturbinen müssen regelmäßig gewartet und kalibriert werden, um ihre Zuverlässigkeit zu gewährleisten. Verschmutzungen, hohe Temperaturen und Korrosion können die Leistung der Sensoren beeinträchtigen. Eine präzise Kalibrierung der Sensoren gewährleistet, dass alle Druckwerte korrekt überwacht werden und keine unentdeckten Fehler auftreten.
Rolle der Drucksensoren für die Systemsteuerung
Drucksensoren liefern kontinuierlich Echtzeitdaten, die in das Steuerungssystem der Dampfturbine eingespeist werden. Diese Daten sind entscheidend, um den Betriebszustand der Turbine zu überwachen und zu steuern. Wenn der Dampfdruck von den gewünschten Normwerten abweicht, kann das System automatisch Anpassungen vornehmen, wie z. B.:
- Regulierung der Brennstoffzufuhr in den Dampferzeuger.
- Anpassung der Dampftemperatur, um den Druck in einem optimalen Bereich zu halten.
- Frühzeitige Fehlererkennung und Notabschaltung im Falle eines Druckabfalls oder -anstiegs, der auf potenzielle Schäden hinweist.
Ein präzises Druckmanagement in Verbindung mit anderen Sensoren wie Temperatursensoren oder Strömungssensoren ermöglicht eine effiziente und sichere Turbinennutzung und trägt zur Verlängerung der Lebensdauer der Turbine bei.
Weiterentwicklung der Drucksensoren
Mit der kontinuierlichen Weiterentwicklung von Sensorik und Messtechnologien werden auch die Drucksensoren in Dampfturbinen immer präziser und widerstandsfähiger. Die Verwendung von intelligenten Sensoren und Kommunikationsnetzwerken wie IoT (Internet of Things) ermöglicht es, die Messdaten nicht nur lokal zu überwachen, sondern sie auch in Cloud-basierte Systeme einzuspeisen, um sie mit anderen Anlagen oder Turbinen zu vergleichen und die gesamte Energieerzeugung zu optimieren. Diese Fortschritte werden dazu beitragen, den Betrieb von Dampfturbinen weiter zu automatisieren, die Energieeffizienz zu steigern und die Betriebs- und Wartungskosten zu senken.
Insgesamt sind Drucksensoren ein unverzichtbares Element für die präzise Steuerung und Wartung von Dampfturbinen. Sie ermöglichen eine effiziente Betriebsführung, helfen, Störungen frühzeitig zu erkennen, und tragen zur Sicherheit sowie zur Langlebigkeit der Turbine bei.
Drucksensoren in Dampfturbinen sind ein grundlegender Bestandteil, der für eine präzise Überwachung und Steuerung des Betriebsablaufs sorgt. Sie bieten eine kontinuierliche Rückmeldung über die wichtigsten Parameter, die für die Effizienz und Sicherheit der Turbine entscheidend sind. In der Praxis sind diese Sensoren so konzipiert, dass sie den Druck in verschiedenen Bereichen der Turbine messen, angefangen bei den Einlassbedingungen bis hin zum Druck im Kondensator oder dem Dampfaustritt. Diese Messwerte sind für die optimale Energieerzeugung und die Minimierung von Energieverlusten von wesentlicher Bedeutung.
Dank moderner Messtechnologien können Drucksensoren heutzutage nicht nur den reinen Dampfdruck messen, sondern auch zusätzliche Informationen wie Temperatur, Feuchtigkeit und Dichte des Dampfs erfassen. Dies ermöglicht eine noch detailliertere Prozessüberwachung und eröffnet neue Möglichkeiten für die Feinabstimmung des Turbinenbetriebs. So können beispielsweise durch die Kombination von Druck- und Temperatursensoren präzisere Thermodynamik-Modelle erstellt werden, die es ermöglichen, den Betrieb der Turbine an wechselnde Betriebsbedingungen anzupassen und maximale Effizienz zu erzielen.
Die Wartung der Drucksensoren ist ebenfalls von zentraler Bedeutung. Sie müssen regelmäßig geprüft und kalibriert werden, um eine langfristige Genauigkeit sicherzustellen. Dabei ist es wichtig, dass die Sensoren gegen Verschmutzung, Korrosion und hohe Temperaturen geschützt sind, um ihre Leistung nicht zu beeinträchtigen. In modernen Dampfturbinen wird zunehmend auf selbstüberwachende Systeme gesetzt, die eine automatische Fehlerdiagnose und Anpassung der Sensoren ermöglichen, wodurch Ausfallzeiten minimiert werden.
Ein besonders innovativer Trend ist die Nutzung von drahtlosen Drucksensoren, die die Installation und Wartung erheblich vereinfachen, insbesondere in schwer zugänglichen Bereichen der Turbine. Diese Sensoren übertragen die Daten kabellos an die zentrale Steuerungseinheit, was die Flexibilität der Überwachungssysteme erhöht und die Notwendigkeit reduziert, dass Wartungspersonal regelmäßig in schwierige Turbinenbereiche vordringen muss.
Darüber hinaus ist der Datenaustausch zwischen den Sensoren und den zentralen Steuerungssystemen ein wichtiger Schritt in Richtung der Industrie 4.0. Hierbei werden die Druckdaten in Echtzeit erfasst, analysiert und in komplexe Analyse-Tools eingespeist, die in der Lage sind, zukünftige Druckentwicklungen vorherzusagen. Auf diese Weise können potenzielle Probleme frühzeitig erkannt und präventive Wartungsmaßnahmen ergriffen werden, bevor es zu einem Ausfall oder einer schwerwiegenden Störung kommt. Dies erhöht nicht nur die Verfügbarkeit der Turbine, sondern trägt auch zur Reduzierung der Betriebskosten bei, da unnötige Reparaturen vermieden werden.
In einer zunehmend nachhaltigen und energiesparenden Industrie ist die Rolle der Drucksensoren in Dampfturbinen nicht nur auf die Überwachung und Steuerung des Betriebs beschränkt. Sie tragen auch aktiv dazu bei, die Energieeffizienz zu steigern und den CO₂-Ausstoß zu minimieren, indem sie eine präzise Abstimmung der Betriebsparameter ermöglichen, um den Wirkungsgrad zu maximieren und Verluste zu minimieren. Diese Fortschritte unterstützen die langfristigen Ziele der Energiewende, bei denen Dampfturbinen eine zentrale Rolle im Energiesystem der Zukunft spielen.
Ein weiterer wichtiger Aspekt im Zusammenhang mit den Drucksensoren in Dampfturbinen ist ihre Rolle in der Fehlersuche und -diagnose. Wenn während des Betriebs eine unerwartete Druckabweichung auftritt, können diese Sensoren sofort auf ein potenzielles Problem hinweisen. Dies kann zum Beispiel durch Druckabfälle im Turbinenkreislauf, Verstopfungen oder Leckagen im Dampfsystem verursacht werden. Durch die schnelle Erkennung solcher Anomalien können Notfallmaßnahmen eingeleitet werden, um eine weitere Verschlechterung des Betriebszustands zu verhindern, wodurch teure Ausfallzeiten und Reparaturen vermieden werden.
Die Integration von Drucksensoren in die gesamte Überwachungsstruktur der Dampfturbine erlaubt eine tiefergehende Prozessoptimierung. In modernen Dampfturbinen werden die Druckdaten häufig in ein integriertes Überwachungssystem eingespeist, das in der Lage ist, Muster und Trends zu erkennen, die auf zukünftige Probleme hinweisen könnten. Dies wird durch den Einsatz fortschrittlicher Künstlicher Intelligenz (KI) und Maschinellem Lernen (ML) ermöglicht, die die Daten in Echtzeit analysieren und proaktive Wartungsstrategien vorschlagen können.
Ein weiterer Fortschritt in der Druckmessung ist der Einsatz von drahtlosen, digitalen Drucksensoren, die es ermöglichen, den Druck in verschiedenen Bereichen der Dampfturbine ohne die Notwendigkeit von Kabelverbindungen zu überwachen. Diese Sensoren bieten eine flexible Installation, insbesondere in schwer zugänglichen Bereichen, und minimieren das Risiko von Kabelverschleiß oder -ausfällen. Die kabellose Kommunikation reduziert auch den Wartungsaufwand, da die Sensoren ihre Daten direkt an das zentrale Steuerungssystem senden, ohne dass die Sensoren physisch überprüft werden müssen.
Die Zuverlässigkeit und Langlebigkeit von Drucksensoren ist entscheidend, insbesondere in den extremen Betriebsbedingungen, denen Dampfturbinen ausgesetzt sind. Hohe Temperaturen, Druckschwankungen und die ständige Wechselwirkung mit korrosiven Substanzen wie Säuren und Kondenswasser setzen den Sensoren zu. Daher sind moderne Sensoren oft mit Schutzbeschichtungen ausgestattet, die sie vor diesen äußeren Einflüssen schützen und ihre Lebensdauer verlängern. Materialien wie Edelstahl oder Keramik sind häufig verwendete Materialien, die den Sensoren eine hohe mechanische Festigkeit und Korrosionsbeständigkeit verleihen.
Die regelmäßige Kalibrierung der Drucksensoren ist ebenfalls ein wichtiger Bestandteil, um sicherzustellen, dass sie ihre Genauigkeit über lange Zeiträume hinweg behalten. Viele Systeme ermöglichen automatische Kalibrierung oder bieten eine einfache Möglichkeit für den Betreiber, die Sensoren bei Bedarf zu überprüfen und anzupassen. Eine richtige Kalibrierung ist unerlässlich, da Drucksensoren, die nicht korrekt eingestellt sind, zu falschen Messwerten führen können, was im schlimmsten Fall zu schlechten Betriebsentscheidungen und Störungen im Turbinenbetrieb führt.
Mit der fortschreitenden Entwicklung von smartern Sensoren wird es auch möglich, weitergehende Diagnosen durchzuführen, indem Daten aus verschiedenen Sensoren kombiniert werden, die nicht nur den Dampfdruck, sondern auch Temperatur, Vibrationspegel und Schwingungen messen. Diese multisensorischen Systeme bieten eine vollständige Überwachung des Turbinenzustands, ermöglichen eine detaillierte Fehlerdiagnose und fördern eine präventive Wartungsstrategie, die dazu beiträgt, den gesamten Betrieb der Dampfturbine zu optimieren und ihre Lebensdauer zu verlängern.
Im Rahmen von Industrie 4.0 und der zunehmenden Automatisierung sind diese Fortschritte besonders wichtig, da sie den Weg für eine vollständig vernetzte und automatisierte Dampfturbinenüberwachung ebnen. Dabei werden Daten aus den Drucksensoren in Echtzeit an ein zentrales Leitsystem übermittelt, das diese Informationen zusammen mit anderen Betriebsdaten auswertet. Dies ermöglicht nicht nur eine optimierte Steuerung und Fehlerbehebung, sondern auch eine vorausschauende Wartung basierend auf den gesammelten Datenanalysen.
Insgesamt spielen Drucksensoren eine Schlüsselrolle bei der Überwachung, Diagnose und Optimierung von Dampfturbinen. Sie tragen dazu bei, Betriebsstörungen zu vermeiden, die Energieeffizienz zu steigern und den CO₂-Ausstoß zu minimieren. Ihre kontinuierliche Weiterentwicklung, kombiniert mit modernen Überwachungstechnologien, stellt sicher, dass Dampfturbinen als zuverlässige und effiziente Energiequellen auch in einer zunehmend digitalisierten und nachhaltigen Energiebranche eine führende Rolle spielen.
Ein weiterer wichtiger Punkt in der Weiterentwicklung der Drucksensoren in Dampfturbinen ist die Integration von Echtzeit-Datenanalyse und Vorausschauender Wartung (Predictive Maintenance). Mit der Möglichkeit, große Mengen an Sensordaten zu sammeln und zu analysieren, können nicht nur die aktuellen Betriebsbedingungen überwacht werden, sondern auch potenzielle Probleme im Vorfeld erkannt werden, bevor sie zu größeren Ausfällen führen. Dies geschieht durch die Anwendung von Datenanalyse-Algorithmen, die Muster in den Daten identifizieren und auf mögliche Anomalien hinweisen, die auf einen bevorstehenden Druckabfall oder -anstieg hindeuten könnten. Eine frühzeitige Erkennung von Problemen ermöglicht eine gezielte Wartung und vermeidet ungeplante Ausfälle, was wiederum die Betriebszeit maximiert und Kosten reduziert.
Der Echtzeit-Datenfluss aus den Drucksensoren wird zunehmend mit Cloud-Technologien kombiniert. Dies bedeutet, dass die gesammelten Daten nicht nur lokal verarbeitet, sondern auch in eine zentrale Cloud-Infrastruktur übertragen werden können. Diese Cloud-basierte Überwachung ermöglicht eine globale Vernetzung der Dampfturbinen und die Analyse von Daten aus mehreren Turbinen gleichzeitig. Betreiber können so den Zustand aller Turbinen in einem Verbund überwachen und vergleichen, was zu einer optimierten Entscheidungsfindung auf Unternehmensebene führt. Die zentrale Datenaggregation trägt auch dazu bei, Best Practices und Leistungsbenchmarking zu entwickeln, die den Betrieb der Turbinen auf lange Sicht verbessern.
Ein weiterer zukunftsweisender Trend ist die Verwendung von integrierten Drucksensoren, die nicht nur den Dampfdruck messen, sondern auch Temperatur, Vibrationen und Akustik überwachen können. Diese Sensoren arbeiten als multifunktionale Geräte, die verschiedene Parameter gleichzeitig messen und somit eine ganzheitliche Betrachtung des Turbinenbetriebs ermöglichen. Diese Art der multisensorischen Überwachung eröffnet die Möglichkeit, mehrdimensionale Datenmodelle zu erstellen, die es ermöglichen, den gesamten Zustand der Dampfturbine in Echtzeit zu bewerten. Ein solcher umfassender Ansatz sorgt dafür, dass alle relevanten Betriebsparameter miteinander korreliert werden, was eine präzisere Steuerung und frühzeitige Fehlererkennung ermöglicht.
Die digitale Zwillingstechnologie ist ein weiterer aufkommender Trend, der die Nutzung von Drucksensoren in Dampfturbinen revolutioniert. Bei der digitalen Zwillingsmodellierung wird eine virtuelle Kopie der Dampfturbine erstellt, die alle physischen und betrieblichen Merkmale der realen Turbine widerspiegelt. Diese digitale Replik kann dann mit den Echtzeitdaten aus den Drucksensoren versorgt werden, um eine präzise Simulation des aktuellen Betriebszustands zu ermöglichen. Auf diese Weise können mögliche Fehlerquellen oder Unregelmäßigkeiten im Betrieb identifiziert und simuliert werden, ohne dass physische Tests notwendig sind. Die digitale Zwillingstechnologie bietet somit eine äußerst effiziente Möglichkeit, Optimierungen und Fehlerbehebungen durchzuführen, ohne die tatsächliche Turbine in Betrieb zu nehmen.
Darüber hinaus wird die Energieeffizienz durch die präzise Druckmessung der Dampfturbine deutlich gesteigert. Indem der Druck genau überwacht und die Dampfturbine ständig im optimalen Druckbereich gehalten wird, wird sichergestellt, dass der Thermodynamische Wirkungsgrad maximiert wird. Ein konstanter, optimaler Dampfdruck bedeutet weniger Energieverluste und eine geringere Abnutzung der mechanischen Komponenten, da die Turbine unter stabileren Bedingungen arbeitet. Die regelmäßige Analyse der Druckdaten kann auch dabei helfen, langfristige Trends in der Leistung zu erkennen, was die Langfristplanung und die Prognose zukünftiger Wartungsbedarfe erheblich verbessert.
Die Zukunft der Drucksensoren in Dampfturbinen wird nicht nur durch Fortschritte in der Messtechnik geprägt sein, sondern auch durch die zunehmende Integration von Künstlicher Intelligenz (KI) und automatisierten Steuerungsmechanismen. Diese Technologien werden es ermöglichen, die Dampfturbine selbstständig auf Veränderungen der Betriebsbedingungen zu reagieren und Anpassungen vorzunehmen, ohne dass eine manuelle Intervention erforderlich ist. KI-Algorithmen können durch maschinelles Lernen aus den gesammelten Druckdaten Vorhersagen treffen und Optimierungen vorschlagen, die den Betrieb effizienter und sicherer machen.
Zusammenfassend lässt sich sagen, dass die Rolle der Drucksensoren in Dampfturbinen von einer rein messenden Funktion hin zu einer zentralen Komponente in einem vernetzten und hochgradig automatisierten Überwachungssystem gewachsen ist. Durch den fortlaufenden Einsatz von fortschrittlichen Datenanalysewerkzeugen, Cloud-basierten Systemen, KI und multisensorischer Technologie wird die Betriebsführung von Dampfturbinen zunehmend präziser, effizienter und kostengünstiger. Diese Entwicklungen bieten nicht nur eine Grundlage für langfristige, nachhaltige Energieerzeugung, sondern tragen auch zur Verkürzung von Ausfallzeiten und zur Verlängerung der Lebensdauer der Turbinen bei.
Temperatursensoren der Dampfturbine
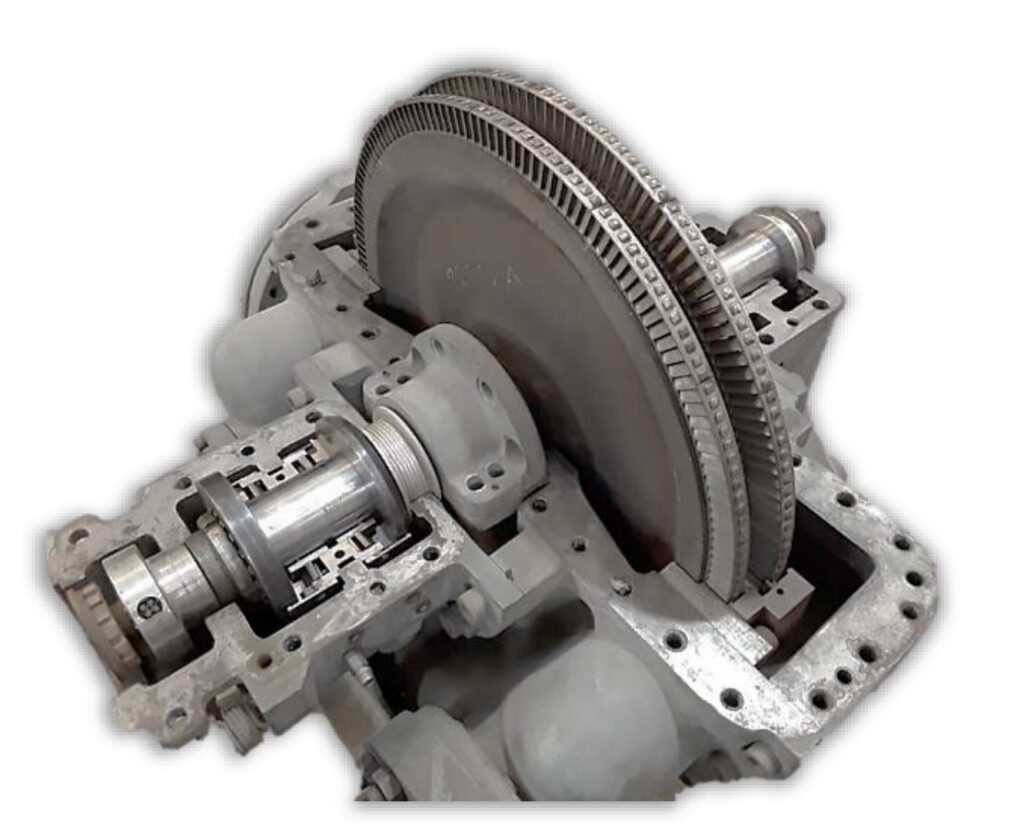
Temperatursensoren in Dampfturbinen spielen eine ebenso zentrale Rolle wie Drucksensoren und sind für die Überwachung und Kontrolle des Betriebszustands der Turbine von entscheidender Bedeutung. In Dampfturbinen wird die Temperatur des Dampfes zu verschiedenen Zeitpunkten im Betriebsablauf überwacht – vom Einlass bis zum Austritt der Turbine. Die genaue Messung der Temperatur ist entscheidend, um den Thermodynamischen Wirkungsgrad zu maximieren, den Betriebszustand zu überwachen und Schäden an den empfindlichen Turbinenkomponenten zu verhindern.
Funktion und Aufgaben der Temperatursensoren
Die Hauptaufgabe der Temperatursensoren besteht darin, sicherzustellen, dass die Betriebstemperatur innerhalb der vom Hersteller empfohlenen Grenzwerte bleibt. Wenn die Temperatur zu hoch wird, könnte dies zu einer Überhitzung führen, was die Lebensdauer der Turbine verringert und die Effizienz beeinträchtigen könnte. Ebenso könnte eine zu niedrige Temperatur den Dampfdruck und damit die Leistung der Turbine negativ beeinflussen.
Ein weiterer wichtiger Aspekt ist, dass die Temperaturmessung zur Überwachung von Wärmeschocks und Temperaturschwankungen dient, die zu mechanischen Spannungen führen und Schäden an den Turbinenkomponenten verursachen könnten. Besonders beim Starten oder Abschalten der Turbine treten häufig abrupte Temperaturänderungen auf, die mit Hilfe der Temperatursensoren überwacht werden müssen, um den Betrieb sicher zu gestalten.
Arten von Temperatursensoren in Dampfturbinen
Es gibt verschiedene Arten von Temperatursensoren, die in Dampfturbinen zum Einsatz kommen:
- Thermoelemente: Thermoelemente sind eine der am häufigsten verwendeten Technologien für Temperaturmessungen in Dampfturbinen. Sie basieren auf dem Prinzip, dass sich die Spannung zwischen zwei verschiedenen Metallen ändert, wenn sie einer Temperaturänderung ausgesetzt werden. Diese Sensoren sind besonders geeignet für hohe Temperaturen, da sie eine schnelle Reaktionszeit und eine breite Temperaturmessrange bieten.
- Widerstandstemperaturdetektoren (RTDs): RTDs messen die Temperatur durch den Widerstand eines Drahtes, der mit der Temperatur steigt. Sie bieten eine hohe Genauigkeit und Stabilität und sind daher für präzisere Temperaturmessungen bevorzugt. RTDs werden in Bereichen der Dampfturbine eingesetzt, in denen eine besonders hohe Messgenauigkeit erforderlich ist.
- Infrarotsensoren: Infrarotsensoren messen die Temperatur, indem sie die Infrarotstrahlung erfassen, die von einem Objekt abgegeben wird. Diese Art von Sensor wird oft in Bereichen eingesetzt, die schwer zugänglich sind oder wo eine berührungslose Messung erforderlich ist. Sie sind besonders nützlich, um die Temperatur von Oberflächen zu überwachen, ohne dass der Sensor direkt mit dem Messobjekt in Kontakt kommen muss.
- Thermistoren: Thermistoren sind eine weitere Art von Widerstandssensoren, die temperaturabhängige Widerstandsänderungen aufweisen. Sie sind in bestimmten Bereichen der Dampfturbine nützlich, wenn die Temperaturmessung im niedrigeren Temperaturbereich erfolgen muss, da sie empfindlicher gegenüber kleineren Temperaturänderungen sind.
Anwendungen der Temperatursensoren in Dampfturbinen
Die genaue Überwachung der Temperatur in verschiedenen Bereichen der Dampfturbine ist entscheidend, um die Betriebsbedingungen zu optimieren. Einige wichtige Einsatzbereiche sind:
- Dampfeinlass: Am Dampfeinlass wird die Temperatur des Dampfes überwacht, um sicherzustellen, dass der Dampf den richtigen thermodynamischen Zustand hat, um die Turbine mit maximaler Effizienz zu betreiben. Zu hohe oder zu niedrige Temperaturen können den Wirkungsgrad der Turbine negativ beeinflussen und die Effizienz senken.
- Zwischenstufen und Rotorgehäuse: In den verschiedenen Stufen der Turbine wird die Temperatur kontinuierlich überwacht, um zu verhindern, dass eine Überhitzung zu Materialermüdung oder Schäden an den Turbinenschaufeln führt. Dies ist besonders wichtig in den Bereichen, in denen der Dampf unter hohem Druck und hoher Temperatur expandiert.
- Kondensator und Auslass: Die Temperatur des Dampfs am Auslass der Turbine und im Kondensator muss ebenfalls überwacht werden. Wenn die Temperatur des Dampfs zu hoch ist, kann dies den Kondensationsprozess und die Wärmerückgewinnung beeinträchtigen, was die Effizienz des gesamten Systems verringert.
- Überwachung der Dampfqualität: Ein weiterer wichtiger Anwendungsbereich für Temperatursensoren in Dampfturbinen ist die Überwachung der Dampfqualität. Wenn der Dampf nicht den richtigen Sättigungsgrad hat, kann dies zu Korrosion und Ablagerungen im Turbinensystem führen, was die Leistung der Turbine beeinträchtigen würde.
Integration und Vernetzung der Temperatursensoren
Im Zuge der Industrie 4.0 und der Smart Grids werden Temperatursensoren zunehmend in ein vernetztes Überwachungssystem integriert. Diese Sensoren übertragen ihre Daten an zentrale Steuerungseinheiten, die in der Lage sind, die Betriebsdaten in Echtzeit zu analysieren. So können nicht nur Abweichungen von den Normalwerten schnell erkannt und behoben werden, sondern auch präventive Wartungsmaßnahmen aufgrund von langfristigen Temperaturtrends eingeleitet werden.
Ein zunehmend wichtiger Trend ist die Nutzung von drahtlosen Temperatursensoren, die die Installation und Wartung der Systeme vereinfachen. Diese Sensoren übertragen ihre Messwerte kabellos an das zentrale Steuerungssystem, was die Flexibilität erhöht und den Wartungsaufwand reduziert.
Herausforderungen und Wartung der Temperatursensoren
Temperatursensoren in Dampfturbinen sind extremen Bedingungen ausgesetzt – hohen Temperaturen, Dampfdruck und aggressiven Umgebungen. Daher ist es wichtig, dass die Sensoren korrosionsbeständig und robust sind. Darüber hinaus müssen sie regelmäßig gewartet und kalibriert werden, um sicherzustellen, dass ihre Messwerte stets genau sind. Verschmutzung, Vibrationen und Feuchtigkeit können die Leistung von Temperatursensoren beeinträchtigen, was regelmäßige Inspektionen und gegebenenfalls den Austausch von Sensoren erforderlich macht.
Die präzise Kalibrierung ist entscheidend, um sicherzustellen, dass die Temperatursensoren auch unter extremen Bedingungen weiterhin genaue Messwerte liefern. Fehlkalibrierte Sensoren können zu einer fehlerhaften Überwachung und Steuerung führen, was potenziell zu Schäden an den Turbinenkomponenten oder zu Ineffizienzen im Betriebsablauf führen könnte.
Fazit
Temperatursensoren sind eine wesentliche Komponente für den sicheren und effizienten Betrieb von Dampfturbinen. Sie sorgen dafür, dass die Turbine in den optimalen Betriebsparametern arbeitet, verhindern Schäden durch Überhitzung und tragen zur Optimierung der Energieerzeugung bei. Ihre fortlaufende Entwicklung und Integration in moderne digitale Überwachungssysteme verbessern nicht nur die Betriebsstabilität, sondern ermöglichen auch eine vorausschauende Wartung, die Ausfallzeiten minimiert und die Lebensdauer der Turbine verlängert.
Zusätzlich zur grundlegenden Funktion der Temperatursensoren in Dampfturbinen spielen diese Sensoren auch eine entscheidende Rolle bei der Optimierung von Wärmerückgewinnungsprozessen. In modernen Dampfturbinenanlagen, vor allem in Kraftwerksverbundsystemen oder Kombikraftwerken, wird die Abwärme der Dampfturbine nicht einfach abgeführt, sondern gezielt für andere Prozesse genutzt, etwa für die Heizung von Gebäuden oder die Stromerzeugung in Gasturbinen. Hierbei ist es von entscheidender Bedeutung, dass die Temperatur des Dampfes an verschiedenen Stellen des Systems präzise gemessen wird, um eine effiziente Energieübertragung und -nutzung zu gewährleisten.
Integration von Temperaturüberwachung in Smart Grid-Systeme
Mit der zunehmenden Verbindung von Dampfturbinenanlagen zu Smart Grid-Infrastrukturen wird auch die Temperaturüberwachung immer mehr in energiemanagementsysteme integriert. Dies ermöglicht nicht nur eine präzise Überwachung der Turbine selbst, sondern auch eine Echtzeit-Analyse der gesamten Energieerzeugung und -verteilung. Durch den Austausch von Temperaturdaten zwischen verschiedenen Komponenten des Kraftwerks und dem Smart Grid können beispielsweise Lastspitzen besser ausgeglichen und die Energieeffizienz des gesamten Systems verbessert werden. Eine präzise Steuerung der Temperatur hilft dabei, die Turbine nicht nur unter optimalen Bedingungen zu betreiben, sondern auch eine maximale Kohlenstoffreduktion zu erreichen.
Zukünftige Entwicklungen in der Temperaturmessung
Die Weiterentwicklung von Temperatursensoren in Dampfturbinen geht in mehrere Richtungen. Zum einen wird die Präzision der Sensoren immer weiter erhöht, insbesondere durch den Einsatz von Nanotechnologie und mikroelektronischen Sensoren, die eine noch genauere Messung und schnellere Reaktion ermöglichen. Diese Technologien könnten die Kompaktheit und Effizienz der Sensoren weiter steigern und ermöglichen, dass mehr Messpunkte an kritischen Stellen der Turbine platziert werden können, um eine noch detailliertere Überwachung zu gewährleisten.
Ein weiterer spannender Trend ist die Verwendung von künstlicher Intelligenz und maschinellem Lernen, um Temperaturmessdaten zu analysieren und so die Betriebsbedingungen in Echtzeit zu optimieren. AI-Algorithmen könnten dabei helfen, Muster in den Temperaturdaten zu erkennen, die für den Menschen schwer nachvollziehbar sind, und so eine frühzeitige Fehlererkennung und prozessoptimierende Eingriffe zu ermöglichen. Beispielsweise könnte AI in der Lage sein, zu erkennen, dass eine leichte Temperaturabweichung in einem bestimmten Turbinenbereich mit einer geplanten Wartung korreliert und eine Empfehlung für einen optimalen Wartungszeitpunkt abgeben.
Thermische Anomalien und ihre Auswirkung auf die Turbine
Wenn Temperatursensoren eine Abweichung von den normalen Betriebswerten feststellen, kann dies auf thermische Anomalien hinweisen, die eine Vielzahl von Problemen in der Dampfturbine verursachen könnten. Eine lokale Überhitzung kann beispielsweise dazu führen, dass bestimmte Komponenten wie Dichtungen und Lager schneller verschleißen oder sogar versagen. Auch eine ungleichmäßige Temperaturverteilung über die Turbinenschaufeln oder die Turbinenwelle kann zu mechanischen Spannungen und letztlich zu Rissen oder Brüchen führen. Die präzise und kontinuierliche Überwachung der Temperatur hilft dabei, solche Anomalien frühzeitig zu erkennen und zu verhindern.
Des Weiteren ist es von entscheidender Bedeutung, dass die Temperaturmesswerte in den Kondensatoren genau erfasst werden. Eine falsche Temperaturmessung hier könnte darauf hinweisen, dass der Kondensator nicht ordnungsgemäß funktioniert, was zu einer geringeren Kondensationseffizienz führt und somit die Gesamtleistung der Turbine negativ beeinflusst.
Wartung und Kalibrierung der Temperatursensoren
Die regelmäßige Wartung und Kalibrierung der Temperatursensoren ist entscheidend, um die langfristige Zuverlässigkeit und Genauigkeit der Messungen sicherzustellen. Sensorverschleiß, Verschmutzung oder Fehler in der Verkabelung können dazu führen, dass die Temperaturmessungen verfälscht werden und wichtige Betriebsdaten nicht korrekt erfasst werden. Daher sind inspektive Wartungsmaßnahmen, die regelmäßige Überprüfungen der Sensoren sowie ihre Neujustierung umfassen, notwendig, um sicherzustellen, dass die Sensoren weiterhin präzise messen und keine Fehler in den Betriebsablauf der Turbine hineinspielen.
Zudem kommen zunehmend selbstkalibrierende Systeme zum Einsatz, die in der Lage sind, sich regelmäßig selbst zu überprüfen und Fehler frühzeitig zu erkennen. Diese Systeme können durch Automatisierung und Fernüberwachung auch den Wartungsaufwand erheblich reduzieren und die Notwendigkeit für manuelle Eingriffe minimieren.
Fazit
Temperatursensoren sind in Dampfturbinen unverzichtbare Komponenten, die nicht nur für die Überwachung der Betriebsbedingungen wichtig sind, sondern auch einen entscheidenden Einfluss auf Effizienz, Leistung und Lebensdauer der gesamten Anlage haben. Ihre kontinuierliche Weiterentwicklung durch den Einsatz neuer Technologien, die Integration in digitale Überwachungssysteme und die Anwendung von KI-gestützten Analysetools eröffnen neue Möglichkeiten für die präzisere und effizientere Nutzung von Dampfturbinen. Gleichzeitig bleibt die regelmäßige Wartung und Kalibrierung ein unverzichtbarer Bestandteil des Systemmanagements, um die Langlebigkeit und Zuverlässigkeit der Temperatursensoren sicherzustellen und so den langfristigen Erfolg des Turbinenbetriebs zu gewährleisten.
Die Weiterentwicklung und die zunehmende Integration von Temperatursensoren in Dampfturbinen bieten zahlreiche Vorteile, sowohl für die Optimierung des Betriebs als auch für die Zuverlässigkeit der gesamten Anlage. Es ist wichtig, dass alle Temperaturmesssysteme nicht nur präzise sind, sondern auch robust genug, um den extremen Bedingungen in Dampfturbinen standzuhalten.
Herausforderungen bei der Integration von Temperatursensoren
Ein herausfordernder Aspekt der Temperatursensoren ist die Kompabilität und Integration der verschiedenen Messsysteme in die bestehenden Steuerungs- und Überwachungssysteme. Es gibt zahlreiche Modelle von Dampfturbinen mit unterschiedlichen Anforderungen und Spezifikationen für Temperaturmessungen. Einige Dampfturbinen benötigen präzise Messungen in speziellen Bereichen wie der Dampftemperatur am Einlass, der Verluste durch Wärmeübertragung im Kondensator oder der Thermodynamik der Turbine, was die Auswahl der richtigen Sensoren und die Systemintegration komplex machen kann.
Des Weiteren kann es je nach Alter und Zustand der Turbine vorkommen, dass ältere Sensoren oder Steuerungen nicht mit modernen digitalen Systemen kompatibel sind. Dies stellt eine Herausforderung bei der Modernisierung oder Retrofit von Dampfturbinen dar. Es wird notwendig sein, entweder neue, hochmoderne Temperatursensoren zu installieren oder auf eine Systemarchitektur umzurüsten, die die Vernetzung und Interoperabilität zwischen den alten und neuen Technologien ermöglicht.
Forschung und Innovation in der Temperaturüberwachung
Forschung und Innovationen in der Temperaturüberwachung werden weiterhin vorangetrieben, um bessere Materialien für die Sensoren und fortschrittlichere Messmethoden zu entwickeln. Ein prominenter Trend ist die Entwicklung von dünnfilmigen Temperatursensoren, die direkt auf die Turbinenkomponenten aufgebracht werden können, wie zum Beispiel auf Turbinenblätter. Diese Sensoren liefern kontinuierliche Echtzeitdaten und ermöglichen eine detaillierte Überwachung ohne zusätzliche Sensorinstallation.
Außerdem wird die Entwicklung von intelligenten Sensoren vorangetrieben, die in der Lage sind, Selbstdiagnosen zu erstellen. Solche Sensoren könnten bei einem Defekt oder einer falschen Messung automatisch eine Fehlermeldung generieren und dabei gleichzeitig Informationen über den Fehler liefern. Dies könnte nicht nur die Wartungsprozesse vereinfachen, sondern auch zu einer schnellen Fehlerbehebung und geringeren Ausfallzeiten führen.
Die Rolle von Temperaturüberwachungsdaten in der prädiktiven Wartung
Mit der fortschreitenden Verbreitung von prädiktiver Wartung in der Energieerzeugungstechnologie spielen die Temperaturmessdaten eine zentrale Rolle. Prädiktive Wartung nutzt historische und Echtzeit-Daten, um vorherzusagen, wann eine Komponente voraussichtlich ausfällt oder Wartungsbedarf hat. Auf Basis der Temperaturmessungen kann der Zustand der Dampfturbine und ihrer Teile wie Lager, Dichtungen oder Turbinenblätter beurteilt werden. Anhand von Temperaturabweichungen, die auf anomale Betriebsbedingungen hinweisen, können frühzeitige Reparaturen und Ersatzteile eingeplant werden, bevor ein kritischer Ausfall auftritt.
Ein praktisches Beispiel hierfür ist, dass bei Überhitzung bestimmter Schaufeln oder Turbinenteile durch zu hohe Temperaturabweichungen eine bevorstehende Materialermüdung oder ein Schaden erkannt werden könnte. Frühzeitige Prädiktionsmodelle könnten dann dazu führen, dass der kritische Punkt der Turbine rechtzeitig gewartet oder ersetzt wird, bevor er zu einem vollständigen Systemausfall führt.
Die Bedeutung der Temperaturüberwachung für die Effizienzsteigerung
Die kontinuierliche Überwachung der Temperatur trägt nicht nur zur Vermeidung von Schäden bei, sondern hilft auch dabei, die Effizienz der Dampfturbine zu maximieren. Eine exakte Temperatursteuerung ermöglicht eine feinabgestimmte Anpassung der Brennstoffzufuhr, des Dampfdrucks und der Wärmerückgewinnung, um sicherzustellen, dass die Turbine in ihrem optimalen Betriebsbereich arbeitet. Dies wirkt sich direkt auf die Energieerzeugung und die Brennstoffeffizienz aus, da die Turbine keine unnötige Energie durch Überhitzung oder Unterkühlung verliert.
Zudem können durch die optimierte Temperatursteuerung die Emissionswerte gesenkt und somit eine umweltfreundlichere Energieproduktion erreicht werden. Dies ist besonders wichtig in Zeiten steigender Umweltauflagen und des globalen Drucks auf Unternehmen, die ihre CO2-Emissionen reduzieren müssen.
Ausblick und zukünftige Trends
Zukünftig werden Dampfturbinen immer mehr zu intelligenten Maschinen mit fortschrittlichen Sensoren und Echtzeit-Überwachungssystemen, die eine hochgradige Automatisierung und Optimierung ermöglichen. In diesem Zusammenhang wird die Verknüpfung von Temperaturmesssystemen mit anderen Sensoren (z. B. Drucksensoren, Vibrationssensoren und Feuchtigkeitssensoren) zunehmend wichtiger. Eine umfassende Überwachung und Analyse all dieser Daten wird es ermöglichen, die Betriebsabläufe der Dampfturbine nicht nur effizienter, sondern auch sicherer zu gestalten.
In den nächsten Jahren wird ein wachsendes Interesse an der Entwicklung von Sensoren mit noch höherer Auflösung und schnellerer Reaktionszeit bestehen, die es ermöglichen, kleinste Temperaturveränderungen zu erkennen, die sich in den langfristigen Betriebseinflüssen der Turbine niederschlagen können. Darüber hinaus wird die Integration von künstlicher Intelligenz und Machine Learning in die Überwachungssysteme zu einer weiteren Optimierung der Turbinenleistung führen.
Abschließend lässt sich sagen, dass Temperatursensoren eine fundamentale Rolle bei der Überwachung und Steuerung von Dampfturbinen spielen und weiterhin entscheidend für die Zukunft der Turbinentechnologie sind. Ihre Weiterentwicklung und Integration in umfassende Überwachungs- und Steuerungssysteme wird dazu beitragen, die Effizienz, Sicherheit und Nachhaltigkeit der Dampfturbinenindustrie im kommenden Jahrzehnt weiter zu steigern.
Die kontinuierliche Weiterentwicklung der Temperatursensoren und ihrer Integration in Dampfturbinen steht nicht nur im Einklang mit einer besseren Fehlererkennung und Effizienzsteigerung, sondern auch mit der zunehmenden Notwendigkeit, den Betrieb von Dampfturbinen im Einklang mit den Anforderungen der Energiebranche und Umweltauflagen zu optimieren.
Digitalisierung und Vernetzung der Dampfturbinen
Die Digitalisierung von Dampfturbinen ist ein entscheidender Schritt in der Evolution moderner Energieerzeugungssysteme. Dies umfasst die Vernetzung von Sensoren und Steuerungssystemen, die es ermöglichen, Daten in Echtzeit zu sammeln, zu analysieren und auf Basis dieser Informationen Betriebsentscheidungen zu treffen. Die Temperatursensoren sind dabei ein wesentlicher Bestandteil des Datensystems, da sie Informationen liefern, die das Thermodynamikmanagement und die Kraftwerkssteuerung in Echtzeit unterstützen.
Durch die Verwendung von IoT-Technologie (Internet of Things) können diese Sensoren miteinander kommunizieren und die gesamte Dampfturbinenanlage überwachen. Diese Technologie ermöglicht es nicht nur, Temperaturwerte zu überwachen, sondern auch, diese mit anderen kritischen Systemdaten wie Druck, Feuchtigkeit und Vibration zu kombinieren, um einen umfassenden Überblick über den Zustand der Turbine zu erhalten. Die erfassten Datenmengen können durch Cloud-Computing und Edge-Computing sofort verarbeitet werden, was eine schnelle Analyse und gegebenenfalls sofortige Reaktionsmaßnahmen ermöglicht.
Die Vernetzung von Dampfturbinen über Cloud-basierte Plattformen erlaubt es Betreibern, Anlagen an verschiedenen Standorten remote zu überwachen, was besonders in großen Kraftwerksparks oder industriellen Anwendungsgebieten von Vorteil ist. Über eine zentralisierte Steuerung können Wartungspläne, Echtzeit-Fehlerdiagnosen und Performance-Optimierungen vorgenommen werden.
Vorteile der digitalen Überwachung
Die digitale Überwachung, die die Integration von Temperatursensoren beinhaltet, bietet eine Vielzahl von Vorteilen, sowohl für die Betreiber von Dampfturbinen als auch für die Energieerzeugung insgesamt:
- Frühzeitige Fehlererkennung und vorbeugende Wartung: Ein System zur digitalen Überwachung kann Anomalien wie Temperaturspitzen oder Temperaturschwankungen sofort erkennen und ein frühzeitiges Warnsignal an die Betreiber senden, wodurch Ausfälle vermieden und Reparaturkosten gesenkt werden.
- Betriebsoptimierung: Durch die Verknüpfung von Temperaturdaten mit anderen Anlagendaten können gezielte Anpassungen vorgenommen werden, um den Betriebsablauf zu optimieren. Dies umfasst beispielsweise die Steuerung der Konditionierung des Dampfes in Echtzeit, was zu einer besseren Wärmerückgewinnung und damit zu einer höheren Energieeffizienz führt.
- Langfristige Prognosen: Mit Hilfe von Datenanalytik und Machine Learning können langfristige Prognosen erstellt werden, wie sich Temperaturänderungen auf die Lebensdauer von Bauteilen auswirken. So können strategische Entscheidungen zur Teilerneuerung von Anlagen getroffen werden, bevor teure Ausfälle auftreten.
- Reduzierung von Ausfallzeiten: Durch die präventive Wartung auf Basis von Temperaturdaten lässt sich der Betriebsstillstand minimieren, was zu einer höheren Verfügbarkeit und einer verbesserten Gesamtenergieerzeugung führt.
Einbindung von Künstlicher Intelligenz (KI)
Künstliche Intelligenz (KI) kann eine Schlüsselrolle bei der Verbesserung der Betriebsweise von Dampfturbinen spielen, insbesondere in der Analyse von Temperaturdaten. KI-basierte Systeme können Maschinelles Lernen nutzen, um Muster und Trends in den Daten zu erkennen, die für den Menschen nicht sofort sichtbar sind. Diese Systeme können dann in der Lage sein, optimale Betriebsparameter vorzuschlagen und sogar automatisierte Anpassungen vorzunehmen.
Ein weiterer Vorteil von KI in der Temperaturüberwachung ist die Fehlerdiagnose. KI-Systeme können Anomalien oder ungewöhnliche Temperaturschwankungen schneller identifizieren und durch historische Datenanalyse feststellen, ob diese Abweichungen in der Vergangenheit zu Fehlfunktionen geführt haben. Auf diese Weise können vorausschauende Wartungsmaßnahmen ergriffen werden, bevor die Situation eskaliert.
Nachhaltigkeit und Umweltverträglichkeit
Die Verbesserung der Temperatursteuerung in Dampfturbinen trägt auch zu den globalen Zielen im Bereich Nachhaltigkeit und CO2-Reduktion bei. Durch eine optimierte Effizienz bei der Dampferzeugung und der Wärmerückgewinnung lässt sich die gesamte Kraftwerksleistung steigern, was zu einer geringeren Energiekosten und reduzierten CO2-Emissionen führt.
Insbesondere in einer Zeit, in der weltweit die Bemühungen zur Bekämpfung des Klimawandels intensiviert werden, ist die Fähigkeit von Dampfturbinen, auf höchstem Effizienzlevel zu arbeiten, entscheidend. Moderne Temperaturüberwachungssysteme helfen nicht nur dabei, die Leistung zu steigern, sondern auch, die Energieproduktion auf nachhaltige Weise zu maximieren, indem unnötige Emissionen vermieden werden.
Ausblick auf zukünftige Entwicklungen
Die Technologie der Dampfturbinen und ihrer Temperaturüberwachungssysteme wird sich weiterentwickeln, insbesondere in den Bereichen Sensorentechnologie und Datenanalyse. In der Zukunft könnten intelligente Sensoren noch stärker in der Lage sein, die Umgebungsbedingungen und dynamische Änderungen des Betriebs präzise zu erfassen. Eine noch tiefere Integration von KI wird es ermöglichen, nicht nur die Temperatur, sondern auch andere Betriebsparameter in einer intelligenten feedbackgesteuerten Regelung zu kombinieren.
Ein weiteres spannendes Zukunftsgebiet ist die Anwendung von dynamischen Simulationen und virtuellen Modellen in Verbindung mit den Temperaturdaten. Diese Modelle könnten es ermöglichen, eine digitale Zwillingstechnologie zu entwickeln, die eine exakte Replikation der Dampfturbine darstellt und so die Betriebsbedingungen noch detaillierter simuliert. Dies könnte die Planung und Durchführung von Wartungsmaßnahmen optimieren und langfristig zur Verlängerung der Lebensdauer von Dampfturbinen beitragen.
Abschließend lässt sich sagen, dass die Temperaturüberwachung in Dampfturbinen ein fortlaufend wachsendes und innovatives Feld bleibt. Die kontinuierliche Verbesserung von Sensoren, die Integration von Digitalisierung und KI sowie die Entwicklung neuer Nachhaltigkeitsstrategien werden entscheidend dazu beitragen, die Effizienz und Zuverlässigkeit von Dampfturbinen auf ein neues Level zu heben.
Drehzahlsensor der Dampfturbine

Ein Drehzahlsensor in einer Dampfturbine ist ein entscheidendes Messinstrument, das dazu dient, die Drehzahl der Turbinenwelle zu überwachen. Diese Welle ist die Hauptkomponente der Turbine, die durch den Dampfdruck in Bewegung gesetzt wird. Der Drehzahlsensor hilft nicht nur bei der Überwachung der Turbinenleistung, sondern auch bei der Schutzfunktion der Turbine, um eine Überdrehzahl zu verhindern, die zu schwerwiegenden mechanischen Schäden führen könnte.
Funktionsweise des Drehzahlsensors
Die Hauptfunktion des Drehzahlsensors besteht darin, die Rotationsgeschwindigkeit der Turbinenwelle zu messen. Dieser Sensor liefert präzise Daten, die in die Steuer- und Überwachungssysteme der Dampfturbine eingespeist werden. Es gibt verschiedene Arten von Drehzahlsensoren, die in Dampfturbinen verwendet werden, darunter magnetische Sensoren, optische Sensoren und induktive Sensoren. Die Wahl des richtigen Sensors hängt von den spezifischen Anforderungen der Turbine sowie den Betriebsbedingungen ab.
- Magnetische Drehzahlsensoren: Diese Sensoren nutzen Magnetfelder zur Erfassung der Rotationsgeschwindigkeit. Sie bestehen aus einem Magneten und einem Hall-Sensor, der die Magnetfeldänderung erfasst, wenn sich die Turbinenwelle dreht. Diese Sensoren sind besonders geeignet für hohe Drehzahlen und extrem robuste Umgebungen, da sie wenig anfällig für mechanische Abnutzung sind.
- Optische Drehzahlsensoren: Diese Sensoren verwenden einen Lichtstrahl, der von einem Reflektor an der Turbinenwelle reflektiert wird. Der Sensor misst die Häufigkeit der Reflexionen, um die Drehzahl zu berechnen. Diese Technologie bietet eine sehr hohe Messgenauigkeit und ist besonders nützlich, wenn hohe Präzision erforderlich ist.
- Induktive Drehzahlsensoren: Bei dieser Technologie wird die Induktivität eines Spulensystems gemessen, das sich in der Nähe eines elektrisch leitenden Objekts (wie der Turbinenwelle) befindet. Wenn sich das Metallobjekt dreht, verändert sich die Induktivität der Spule, was eine präzise Messung der Drehzahl ermöglicht.
Anwendungen und Bedeutung des Drehzahlsensors
Der Drehzahlsensor hat mehrere wichtige Funktionen in der Dampfturbine:
- Überwachung der Drehzahl: Die Drehzahl der Turbine ist entscheidend für die Leistungskontrolle. Wenn die Drehzahl zu hoch wird, kann dies zu Überlastung und Beschädigung der Turbine führen. Der Drehzahlsensor stellt sicher, dass die Turbine innerhalb des sicheren Betriebsbereichs bleibt.
- Schutz vor Überdrehzahl: Dampfturbinen sind so konstruiert, dass sie nur innerhalb eines bestimmten Drehzahlbereichs arbeiten. Ein Überdrehen der Turbine kann zu schwerwiegenden Schäden an der Turbinenwelle oder anderen Komponenten führen. Der Drehzahlsensor kann Teil eines Schutzsystems sein, das bei Erreichen einer kritischen Drehzahl sofort die Leistung reduziert oder die Turbine abschaltet.
- Optimierung des Betriebs: Der Drehzahlsensor trägt zur Effizienzsteigerung der Dampfturbine bei, indem er die Drehzahl konstant hält und gleichzeitig hilft, maximale Leistung zu erzielen, ohne die Turbine zu überlasten. Dies ist besonders wichtig in Kraftwerken, die mit variablen Lasten arbeiten und deren Leistung regelmäßig angepasst werden muss.
- Überwachung des Verschleißes: Abweichungen von der normalen Drehzahl können ein Anzeichen für mechanischen Verschleiß oder Probleme im Turbinensystem sein, wie z. B. eine fehlende Balance der Turbinenwelle oder Lagerverschleiß. Frühzeitige Erkennung solcher Probleme kann helfen, teure Wartungsmaßnahmen und Ausfallzeiten zu verhindern.
Integration mit Steuerungssystemen
Die Drehzahlsensoren sind eng mit den Steuerungssystemen der Dampfturbine verbunden. In modernen Dampfturbinen werden diese Sensoren in digitale Steuerungssysteme integriert, die kontinuierlich die Drehzahl und andere kritische Parameter überwachen. Wenn der Sensor eine Abweichung von den vordefinierten Werten erkennt, sendet er eine Warnung an das Überwachungssystem, sodass der Betreiber sofort reagieren kann.
Die Integration mit anderen Sensoren wie Temperatursensoren, Drucksensoren und Vibrationssensoren ermöglicht eine umfassende Überwachung und Fehlererkennung der Turbine. Dies hilft dabei, den Betrieb der Turbine zu optimieren und Ausfälle zu vermeiden. In vielen Fällen werden die Daten des Drehzahlsensors in Predictive Maintenance-Modelle eingespeist, die es ermöglichen, Wartungsmaßnahmen genau zum richtigen Zeitpunkt zu planen.
Wartung und Kalibrierung der Drehzahlsensoren
Drehzahlsensoren, wie alle anderen Sensoren in Dampfturbinen, erfordern regelmäßige Wartung und Kalibrierung, um eine langfristige Zuverlässigkeit und Genauigkeit zu gewährleisten. Im Allgemeinen müssen die Sensoren auf Verschleiß, Verschmutzung oder Vibrationen überprüft werden, die die Leistung beeinträchtigen könnten. Die Kalibrierung sorgt dafür, dass der Sensor unter verschiedenen Betriebsbedingungen stets die korrekten Werte liefert.
Ein weiterer wichtiger Aspekt der Wartung ist die regelmäßige Visuelle Inspektion der Sensoren und ihrer Verkabelung. Fehler in den Verbindungen oder Korrosion an den Komponenten können zu ungenauen Messwerten oder sogar zum Ausfall des Sensors führen.
Zukünftige Entwicklungen
Die Zukunft der Drehzahlsensoren in Dampfturbinen wird durch den Fortschritt in der Sensortechnologie geprägt sein. Eine mögliche Entwicklung ist die Verwendung von drahtlosen Sensoren, die die Installation und Wartung vereinfachen und dabei eine noch höhere Messgenauigkeit und Zuverlässigkeit bieten können.
Darüber hinaus könnte die Integration von KI und maschinellem Lernen auch bei der Analyse von Drehzahldaten eine Rolle spielen. KI-basierte Systeme könnten Muster und Abweichungen im Betrieb der Turbine erkennen, die auf kommende Probleme hinweisen und so eine frühzeitige Fehlerdiagnose ermöglichen.
Fazit
Der Drehzahlsensor ist ein unverzichtbares Element im Überwachungs- und Steuerungssystem einer Dampfturbine. Er ermöglicht eine präzise Überwachung der Turbinenleistung, schützt vor Überdrehzahl und trägt zur optimierten Effizienz und Zuverlässigkeit der Turbine bei. In Zukunft werden sich die Technologien weiterentwickeln, um noch robustere, genauere und intelligente Drehzahlsensoren bereitzustellen, die die Dampfturbinen noch effizienter und sicherer machen.
Ein weiterer Aspekt, der in Bezug auf den Drehzahlsensor nicht unbeachtet bleiben sollte, ist die kontinuierliche Forschung und Entwicklung im Bereich der Sensortechnologie. Die Integration von Fortschrittlicher Signalverarbeitung und Künstlicher Intelligenz wird eine Schlüsselrolle dabei spielen, wie Drehzahlsensoren ihre Datenanalyse und Fehlerprognose in Echtzeit verbessern. Ein adaptives Überwachungssystem könnte es ermöglichen, dass sich die Empfindlichkeit der Sensoren dynamisch an den Betriebszustand der Dampfturbine anpasst, was zu einer noch präziseren Steuerung und einer effizienteren Fehlervermeidung führt.
Ein weiterer Schritt in diese Richtung könnte die Verwendung von Smart Sensors sein, die nicht nur die Drehzahl messen, sondern auch zusätzliche Betriebsparameter wie Vibrationslevel, Temperaturveränderungen und Lagerzustände überwachen. Solche multifunktionalen Sensoren würden es ermöglichen, die Leistung der Dampfturbine umfassender zu verstehen und Wartungszyklen weiter zu optimieren. Diese umfassendere Datenerfassung könnte dazu beitragen, Lebensdauerprognosen von Turbinenkomponenten zu erstellen und potenzielle Ausfälle vorherzusagen, bevor sie eintreten.
Des Weiteren könnten Drehzahlsensoren in einer verteilten Architektur arbeiten, bei der mehrere Sensoren entlang der Turbinenwelle eingesetzt werden, um eine genauere Messung der Drehzahl in verschiedenen Bereichen der Welle zu ermöglichen. Dies könnte vor allem bei sehr großen oder komplexen Dampfturbinenmodellen von Vorteil sein, bei denen unterschiedliche Teile der Welle unterschiedlichen Belastungen und Geschwindigkeiten ausgesetzt sind. Ein solches Mehrpunktüberwachungssystem könnte die Drehzahlabweichungen besser erfassen und analysieren, was die Fehlerdetektion deutlich verbessert und die Systemstabilität erhöht.
Mit den fortschreitenden Entwicklungen in der Datenkommunikation und Internet-of-Things (IoT)-Technologien werden die Drehzahlsensoren zukünftig noch stärker in ein globales Netzwerk von Kraftwerkssteuerungssystemen integriert. Die Echtzeit-Datenübertragung aus Dampfturbinen zu zentralisierten Überwachungszentren oder sogar direkt zu den Wartungsteams wird es ermöglichen, einen globalen Überblick über die Betriebsbedingungen mehrerer Turbinenanlagen zu erhalten. Dies wird nicht nur den Betrieb der einzelnen Turbinen verbessern, sondern auch eine optimierte Energienutzung und eine bessere Lastverteilung im gesamten Kraftwerk ermöglichen.
Abschließend lässt sich sagen, dass der Drehzahlsensor eine Schlüsselkomponente im sicheren und effizienten Betrieb von Dampfturbinen bleibt. Mit der kontinuierlichen Verbesserung der Technologie und der Integration neuer Kommunikationsmethoden und Analysewerkzeuge wird seine Bedeutung in den kommenden Jahren weiter steigen.
Ein weiterer interessanter Aspekt ist die Möglichkeit, dass Drehzahlsensoren in intelligente Netzwerke eingebunden werden können, die den Betrieb von Dampfturbinen in Smart Grids unterstützen. In diesen Netzwerken wird der Betrieb von Energieanlagen durch vernetzte Systeme koordiniert, die es ermöglichen, die Energieproduktion in Echtzeit zu optimieren und den Energiefluss dynamisch anzupassen. Drehzahlsensoren könnten dabei helfen, die drehzahlabhängigen Lasten der Turbinen effizient zu managen, indem sie präzise Drehzahlmessungen in Kombination mit anderen Leistungsparametern liefern. Auf diese Weise könnten lastangepasste Betriebsstrategien entwickelt werden, die sowohl die Effizienz der Turbinen steigern als auch die Energieversorgung stabilisieren.
Ein weiterer Trend, der zunehmend in der Dampfturbinenüberwachung zum Tragen kommt, ist die Energieautarkie der Sensoren. Einige Drehzahlsensoren werden zunehmend mit selbstversorgenden Energiesystemen ausgestattet, die durch die Bewegung der Turbinenwelle selbst Energie erzeugen können. Solche energieautarken Sensoren benötigen keine externe Energiequelle und sind besonders vorteilhaft für Turbinen in abgelegenen oder schwer zugänglichen Bereichen, wo eine regelmäßige Wartung oder Kabelversorgung problematisch wäre. Diese Technologie basiert auf piezoelektrischen Effekten oder induktiven Generatoren, die die Bewegung der Turbinenwelle direkt in Energie umwandeln.
Die Datenverarbeitung der Drehzahlsensoren spielt ebenfalls eine zunehmend zentrale Rolle. Bei der traditionellen Auswertung der Drehzahl wurden häufig nur einfache Schwellenwerte zur Überwachung des Betriebs eingesetzt. Heutzutage werden jedoch fortschrittliche Algorithmen und Datenmodelle verwendet, die eine tiefere Analyse ermöglichen. So können Sensoren mittlerweile nicht nur die Drehzahl der Turbinenwelle überwachen, sondern auch Trendanalyse und Vorhersage von Anomalien liefern. Diese prädiktiven Wartungssysteme sind entscheidend für den proaktiven Umgang mit möglichen Ausfällen und tragen zur Optimierung des Gesamtbetriebs der Turbine bei.
Ein weiteres interessantes Entwicklungspotenzial besteht in der Kombination der Drehzahlsensoren mit Vibrationssensoren und Temperatursensoren. Während Drehzahlsensoren die Geschwindigkeit und den Betriebsstatus der Welle überwachen, können Vibrationssensoren Anzeichen für mechanische Probleme wie Lagerfehler oder Unwuchten in der Turbine erkennen. Zusammen mit den Temperaturdaten, die auf mögliche Überhitzung oder Abnutzung hinweisen können, bieten diese Sensoren ein umfassenderes Bild der Turbinenzustände. Die Fusionsanalyse dieser verschiedenen Messwerte in Echtzeit kann frühzeitig auf mechanische Probleme oder Leistungsabfälle hinweisen, noch bevor sie zu größeren Ausfällen führen.
In Bezug auf Energieeffizienz ist es zudem denkbar, dass Drehzahlsensoren künftig zur Feinanpassung von Regelstrategien in Kraftwerken eingesetzt werden. Insbesondere in Anlagen, die über mehrere Dampfturbinen verfügen, können die Sensordaten verwendet werden, um die Turbinenbetriebspunkte zu optimieren und die Gesamtleistung des Kraftwerks zu maximieren. Dies könnte durch eine adaptive Lastverlagerung oder durch die dynamische Steuerung der Turbinenbetriebspunkte in Verbindung mit der stromwirtschaftlichen Planung des gesamten Netzwerks geschehen.
Die zunehmende Integration von Drehzahlsensoren und verwandten Messsystemen in Automatisierung und Überwachungssysteme eröffnet den Weg für eine höhere Verfügbarkeit und Betriebsoptimierung von Dampfturbinen in Kraftwerken, Schiffsantrieben und anderen industriellen Anwendungen. Diese technologischen Weiterentwicklungen werden es ermöglichen, den Betriebsaufwand zu verringern, die Betriebszeiten zu maximieren und den Energieverbrauch besser zu steuern, was nicht nur die Wirtschaftlichkeit steigert, sondern auch zur Nachhaltigkeit der Kraftwerksbetriebe beiträgt.
Zusammenfassend lässt sich festhalten, dass der Drehzahlsensor in der Dampfturbine weit mehr ist als ein einfaches Messgerät. Er stellt ein unverzichtbares Instrument zur Überwachung, Optimierung und Sicherheit des Turbinenbetriebs dar und wird durch die Fortschritte in der Technologie und der Vernetzung immer leistungsfähiger. Mit den kontinuierlichen Verbesserungen in der Sensortechnologie, der Datenanalyse und der automatisierten Steuerung werden Drehzahlsensoren eine immer zentralere Rolle bei der Zukunftsfähigkeit und Effizienz von Dampfturbinenanlagen spielen.
Ein weiteres spannendes Entwicklungspotenzial im Bereich der Drehzahlsensoren für Dampfturbinen ist die Integration von Cloud-Technologien und Big Data. Durch die Anbindung der Drehzahlsensoren an Cloud-basierte Plattformen können riesige Mengen an Betriebsdaten in Echtzeit erfasst, gespeichert und analysiert werden. Diese zentralisierte Datenverarbeitung ermöglicht es, große Mengen an historischen und aktuellen Sensordaten zu kombinieren, um langfristige Trends zu erkennen, Verschleißmuster zu identifizieren und fehlerhafte Komponenten frühzeitig zu diagnostizieren. Dies könnte die Entwicklung von intelligenteren Wartungsstrategien vorantreiben und den Betrieb von Dampfturbinen noch effizienter gestalten.
Ein weiterer Vorteil der Nutzung von Cloud-Technologie besteht in der Möglichkeit, auf die Sensorendaten aus der Ferne zuzugreifen. Dies bedeutet, dass Techniker und Ingenieure die Betriebsbedingungen der Turbinen jederzeit überwachen können, ohne physisch vor Ort sein zu müssen. Dies verbessert nicht nur die Effizienz der Wartungsplanung, sondern auch die Reaktionsgeschwindigkeit bei Problemen, was zu reduzierten Ausfallzeiten und einer höheren Verfügbarkeit der Dampfturbinen führt.
Ein weiterer Trend in der Überwachung und Steuerung von Dampfturbinen ist die zunehmende Verwendung von Künstlicher Intelligenz (KI) zur Analyse der Drehzahl- und Sensordaten. KI-Algorithmen können die Datenströme aus Drehzahlsensoren in Echtzeit auswerten, Muster erkennen und potenzielle Anomalien automatisch identifizieren. Diese Systeme könnten in der Lage sein, langsame Veränderungen in der Drehzahl oder minimale Abweichungen zu erkennen, die für den Menschen oft schwer zu identifizieren sind. Maschinelles Lernen kann dabei helfen, das Verhalten der Turbine zu lernen und zu verstehen, wodurch es möglich wird, außergewöhnliche Ereignisse zu antizipieren und präventive Maßnahmen zu ergreifen, bevor es zu ernsthaften Störungen kommt.
In der Praxis könnte dies zu einer proaktiven Wartung führen, bei der vorausschauende Wartungsmaßnahmen auf Grundlage von Datenanalysen ergriffen werden, noch bevor ein Fehler tatsächlich auftritt. Dies ist besonders wichtig in komplexen Anlagen wie Dampfturbinen, die oft extrem hohen mechanischen und thermischen Belastungen ausgesetzt sind. Ein vorausschauendes Wartungssystem könnte nicht nur die Lebensdauer der Turbine verlängern, sondern auch Kosten senken und die Energieeffizienz optimieren, indem es unnötige Reparaturen und Ausfallzeiten vermeidet.
Ein weiterer wichtiger Bereich, der die Zukunft der Drehzahlsensoren in Dampfturbinen prägen könnte, ist die Entwicklung von Sensorsystemen, die selbstkalibrierend sind. Diese Sensoren könnten sich automatisch an veränderte Betriebsbedingungen anpassen, ohne dass eine manuelle Kalibrierung erforderlich ist. Dies würde nicht nur die Genauigkeit und Zuverlässigkeit der Messungen verbessern, sondern auch den Wartungsaufwand minimieren.
Zukünftige Multisensorkonzepte könnten es ermöglichen, dass Drehzahlsensoren in Verbindung mit anderen Umweltsensoren, wie z. B. Feuchtigkeits-, Druck- und Temperaturmessgeräten, kombiniert werden, um eine noch genauere Gesamtbeurteilung der Turbinenleistung zu ermöglichen. Diese umfassenden Überwachungssysteme könnten dann in intelligente Steuerungseinheiten integriert werden, die nicht nur auf die Drehzahl reagieren, sondern auch andere kritische Variablen wie Vibrationsmuster oder Lagerbelastungen berücksichtigen, um so den gesamten Betriebszustand der Turbine zu bewerten und auf Veränderungen im Betrieb dynamisch zu reagieren.
Ein solcher integrativer Ansatz würde eine genauere Überwachung und eine optimierte Leistungskontrolle ermöglichen. Auch die Fehlererkennung könnte schneller und präziser erfolgen, indem komplexe Interaktionen zwischen den verschiedenen Betriebsparametern berücksichtigt werden. Dies wiederum würde dazu beitragen, die Betriebsstabilität der Dampfturbine zu erhöhen und sicherzustellen, dass die Turbine immer unter optimalen Bedingungen arbeitet.
Die Integration von Drehzahlsensoren mit modernen Automatisierungstechnologien wird ebenfalls zunehmend von Bedeutung. Durch die Autonomie dieser Systeme könnte die Turbine in der Lage sein, sich automatisch an verschiedene Betriebsbedingungen anzupassen, wie z. B. Änderungen im Dampfdruck, in der Temperatur oder im Kraftwerkbedarf. Dies könnte zu einer stabileren Leistung und einer geringeren Betriebskosten führen, da die Turbine in der Lage wäre, sich effizienter auf die Betriebsanforderungen einzustellen, ohne dass ständige manuelle Eingriffe notwendig wären.
Insgesamt lässt sich sagen, dass die Drehzahlsensoren für Dampfturbinen nicht nur als einfache Messinstrumente dienen, sondern zunehmend als intelligente Bausteine in einem komplexen Überwachungs-, Analyse- und Steuerungssystem. Durch die kontinuierliche Weiterentwicklung der Technologie, die zunehmende Integration mit Künstlicher Intelligenz, Cloud-Computing und Smart Sensors wird ihre Rolle in der optimierten Wartung, der Fehlererkennung und der Betriebssteuerung noch weiter wachsen, was zu einer deutlich effizienteren Nutzung von Dampfturbinen in der Zukunft führt.
Schwingungsdämpfer in einer Dampfturbine

Schwingungsdämpfer spielen eine zentrale Rolle in der Dampfturbine, da sie dazu beitragen, unerwünschte Vibrationen und mechanische Belastungen, die durch die Drehbewegung der Turbine erzeugt werden, zu minimieren. Diese Vibrationen können durch verschiedene Faktoren verursacht werden, einschließlich mechanischer Unwuchten, Unregelmäßigkeiten im Dampfstrom, Lagerfehler oder Unregelmäßigkeiten bei der Drehzahl. Wenn diese Vibrationen nicht ausreichend kontrolliert werden, können sie zu Strukturschäden führen, die Lebensdauer der Turbine beeinträchtigen und die Betriebsstabilität gefährden.
Funktion von Schwingungsdämpfern
Die Hauptaufgabe von Schwingungsdämpfern ist es, die Energie der Vibrationen zu absorbieren und diese so in Wärme oder andere Formen der Energie umzuwandeln, die keine Schäden an den Turbinenkomponenten verursachen. Schwingungsdämpfer reduzieren so die Amplitude der Schwingungen und schützen die Welle, die Lager und andere empfindliche Bauteile vor mechanischen Belastungen.
In Dampfturbinen werden Schwingungsdämpfer oft an kritischen Stellen wie der Turbinenwelle, den Lagern oder der Verbindung zwischen Turbine und Generator installiert. Sie können in verschiedenen Formen auftreten:
- Elastische Dämpfer: Diese Dämpfer bestehen aus Gummimaterialien, die in der Lage sind, Schwingungsenergie zu absorbieren und diese Energie als Wärme freizusetzen. Elastische Dämpfer sind besonders effektiv bei der Dämpfung niedriger bis mittlerer Frequenzen und werden häufig in Bereichen mit geringen bis moderaten Belastungen eingesetzt.
- Viskose Dämpfer: Diese Dämpfer nutzen die Viskosität von Flüssigkeiten (z. B. Öl oder spezielle Dämpfungsflüssigkeiten), um Schwingungsenergie zu absorbieren. Sie bieten eine hohe Dämpfungsleistung, vor allem bei mittleren bis hohen Frequenzen, und sind häufig in hochbelasteten Bereichen von Dampfturbinen zu finden.
- Magnetorheologische Dämpfer: Diese modernen Dämpfer nutzen magnetische Felder und spezielle Fluide, um die Dämpfungsleistung in Echtzeit zu steuern. Sie bieten eine hohe Dynamik und Anpassungsfähigkeit an verschiedene Betriebsbedingungen und sind besonders nützlich in Dampfturbinen mit variierenden Lastbedingungen.
- Feder-Dämpfer-Systeme: Diese Systeme kombinieren Federn und Dämpfer, um eine aktive Dämpfung in Schwingungssystemen zu erreichen. Sie werden häufig verwendet, wenn zusätzliche Stabilität bei sehr hohen Drehzahlen erforderlich ist, insbesondere in der Nähe der kritischen Frequenzen, bei denen Schwingungen zur Gefahr werden können.
Bedeutung von Schwingungsdämpfung
- Verlängerung der Lebensdauer der Turbine: Übermäßige Vibrationen können zu frühem Verschleiß und Materialermüdung führen, die die Lebensdauer der Turbine erheblich verkürzen können. Durch den Einsatz von Schwingungsdämpfern können diese mechanischen Belastungen reduziert und die Lebensdauer der Turbine verlängert werden.
- Vermeidung von Resonanzphänomenen: Resonanz tritt auf, wenn die Frequenz der Schwingung mit der Eigenfrequenz eines Bauteils übereinstimmt, was zu einer erheblichen Erhöhung der Schwingungsamplitude führen kann. Schwingungsdämpfer helfen dabei, Resonanzphänomene zu vermeiden, indem sie die Frequenzkomponenten der Vibrationen gezielt dämpfen und die Amplitude der Schwingungen kontrollieren.
- Erhöhung der Betriebsstabilität: Durch die Dämpfung von Vibrationsspitzen wird der Betrieb der Dampfturbine stabiler und sicherer. Dies trägt zur Vermeidung von Schäden und zu einer gleichmäßigeren Leistung bei.
- Reduzierung von Geräuschen: Übermäßige Vibrationen können auch zu akustischen Störungen führen, die nicht nur für die Turbine selbst problematisch sind, sondern auch für das gesamte Kraftwerk oder die Umgebung. Schwingungsdämpfer tragen dazu bei, diese Lärmemissionen zu verringern und den Lärmpegel zu minimieren.
Herausforderungen und Innovationen
Die Anforderungen an Schwingungsdämpfer in Dampfturbinen werden durch immer höhere Drehzahlen, größere Turbinen und striktere Sicherheitsstandards immer anspruchsvoller. Moderne Turbinen arbeiten zunehmend mit hohen Drehzahlen und variierenden Lasten, was dazu führt, dass Schwingungsdämpfer in der Lage sein müssen, sich schnell an wechselnde Betriebsbedingungen anzupassen.
Eine aktuelle Entwicklung im Bereich der Schwingungsdämpfung ist die Verwendung von intelligenten Materialien und adaptiven Systemen, die sich in Echtzeit an veränderte Schwingungsmuster anpassen können. Diese Technologien nutzen Sensoren, um die Vibrationen in der Turbine zu messen, und steuern dann die Dämpfungseigenschaften entsprechend den aktuellen Bedingungen. Solche Systeme bieten nicht nur eine verbesserte Leistungsfähigkeit, sondern auch eine größere Flexibilität, da sie sich automatisch an unterschiedliche Betriebsbedingungen anpassen können.
Wartung und Überwachung
Schwingungsdämpfer müssen regelmäßig überwacht und gewartet werden, um sicherzustellen, dass sie ihre Funktion auch unter extremen Betriebsbedingungen beibehalten. Schwingungsüberwachungssysteme können eingesetzt werden, um Daten zu den Schwingungsamplituden und -frequenzen in Echtzeit zu sammeln. Diese Daten können dann genutzt werden, um Frühwarnungen auszugeben, falls die Dämpfungskapazität des Schwingungsdämpfers nicht mehr ausreichend ist.
Moderne Überwachungssoftware kann automatisch erkennen, wenn ein Schwingungsdämpfer versagt oder nicht mehr effektiv arbeitet, und den Wartungsbetrieb anweisen, das System zu überprüfen oder zu ersetzen. Dies stellt sicher, dass keine unnötigen Schäden durch unzureichende Dämpfung entstehen und dass die Dampfturbine unter optimalen Bedingungen läuft.
Fazit
Schwingungsdämpfer sind ein wesentlicher Bestandteil der Betriebsstabilität, Langlebigkeit und Sicherheit von Dampfturbinen. Durch die kontinuierliche Weiterentwicklung von Dämpfungstechnologien und die Integration moderner Überwachungs- und Sensortechnologien können Dampfturbinen künftig noch effizienter und zuverlässiger betrieben werden. Der Einsatz dieser Technologien trägt dazu bei, die Betriebskosten zu senken, die Wartungsintervalle zu verlängern und die Energieproduktion zu optimieren, was für den Betrieb von Dampfturbinen in industriellen Anwendungen von großer Bedeutung ist.
Schwingungsdämpfer in Dampfturbinen sind entscheidend, um die strukturelle Integrität und die Betriebseffizienz aufrechtzuerhalten. Neben der primären Aufgabe, Schwingungen zu reduzieren, spielen sie eine zunehmend wichtige Rolle bei der Schutzfunktion der gesamten Turbine und der Vermeidung von Mechanikschäden, die durch unerwünschte Vibrationen entstehen können. Bei modernen Dampfturbinen, die mit sehr hohen Drehzahlen arbeiten, sind die Anforderungen an die Schwingungsdämpfung besonders hoch, da die Turbinenkomponenten extremen Belastungen und kräfteintensiven Schwingungen ausgesetzt sind. Besonders kritisch sind dabei die Lager und die Turbinenwelle, die durch anhaltende Schwingungen oder Resonanzeffekte Schaden nehmen könnten. Daher müssen Schwingungsdämpfer nicht nur statische Schwingungen absorbieren, sondern auch dynamische Lasten bei wechselnden Betriebsbedingungen aufnehmen.
Ein weiterer wichtiger Aspekt ist die Optimierung der Dämpfungsleistung während des Betriebs. Hierbei spielen individuelle Anpassungen eine wichtige Rolle, besonders in Bereichen, in denen sich die Frequenzen der Schwingungen schnell ändern oder nicht konstant bleiben. Dies kann durch den Einsatz von adaptiven oder aktiven Dämpfungsmechanismen erfolgen, die auf Sensorinputs reagieren und die Dämpfungswirkung automatisch an die Schwingungsintensität und -frequenz anpassen. Diese selbstregulierenden Systeme werden zunehmend zur Norm, insbesondere in hochkomplexen Systemen wie Dampfturbinen, bei denen exakte Steuerung für die Aufrechterhaltung des sicheren und effizienten Betriebs erforderlich ist.
Die Effizienz von Schwingungsdämpfern hängt nicht nur von der Technologie selbst ab, sondern auch von der richtigen Positionierung der Dämpfungselemente innerhalb der Turbine. Bei Dampfturbinen sind strategische Installationsorte besonders wichtig, um die maximale Schwingungsdämpfung zu erreichen. Schwingungsdämpfer werden häufig an kritischen Stellen wie den Turbinenwellen und den Lageraufhängungen montiert, da diese Bereiche besonders anfällig für Schwingungen sind, die die Turbine destabilisieren könnten.
Die Wartung und Überwachung der Schwingungsdämpfer sind ebenfalls unerlässlich für die Aufrechterhaltung der Funktionsfähigkeit der Turbine. Regelmäßige Inspektionen und Prüfungen der Schwingungsdämpfer auf Verschleiß, Risse oder Abnutzung sind notwendig, um sicherzustellen, dass die Dämpfungseffekte immer auf dem gewünschten Niveau bleiben. Der Einsatz von Schwingungsmessgeräten und Sensoren, die die Schwingungsamplituden kontinuierlich überwachen, ermöglicht eine präzise Analyse des Dämpfungsverhaltens. Mit modernen Fehlerdiagnosetools können bereits frühzeitig Anzeichen von Schäden oder Leistungsabfällen erkannt werden, was zu einer gezielten Wartung führt und den Austausch oder die Reparatur von defekten Dämpfungselementen erleichtert.
Zukünftige Entwicklungen in der Schwingungsdämpfung könnten sich auf intelligente Materialien und dynamische Steuerungssysteme konzentrieren, die es ermöglichen, Dämpfer mit höherer Präzision und in Echtzeit an die Betriebsbedingungen der Dampfturbine anzupassen. Dazu könnten etwa piezoelektrische Dämpfer gehören, die sich bei Bedarf je nach Schwingungsfrequenz und -intensität anpassen und so eine noch präzisere Steuerung der Schwingungsdämpfung bieten. Auch die Integration von KI-basierten Analyseplattformen zur Optimierung der Dämpfungsstrategien könnte eine Rolle spielen, indem vorhergesagte Schwingungsmuster die notwendige Anpassung der Dämpfungstechnik ermöglichen, bevor die Schwingungen die kritischen Schwellenwerte überschreiten. In der Kombination dieser intelligenten Systeme mit traditionellen mechanischen Dämpfungstechnologien könnte eine noch nie dagewesene Schwingungsreduktion erzielt werden, die zur Sicherstellung der Zuverlässigkeit und Lebensdauer von Dampfturbinen beiträgt.
Die kontinuierliche Forschung und Entwicklung im Bereich der Schwingungsdämpfungstechnologien für Dampfturbinen verspricht nicht nur eine verbesserte Leistung und einen sichereren Betrieb der Turbinen, sondern auch eine höhere Energieeffizienz und eine Reduzierung der Betriebskosten. Durch die Einführung von fortschrittlichen Materialien, intelligenten Steuermechanismen und anpassungsfähigen Dämpfungstechnologien kann die Leistung von Dampfturbinen weiter optimiert werden, was letztlich zu einer kosteneffizienteren und umweltfreundlicheren Energieerzeugung beiträgt.
Die Weiterentwicklung von Schwingungsdämpfungstechnologien für Dampfturbinen hat auch Auswirkungen auf die Reduktion von Betriebsstörungen. Insbesondere in kritischen Bereichen, in denen die Turbinenwellen hohen mechanischen Kräften und Schwingungen ausgesetzt sind, tragen Schwingungsdämpfer dazu bei, potenzielle Fehlerquellen zu identifizieren und deren Auswirkungen zu minimieren. Durch den Einsatz von hochentwickelten Sensortechnologien und diagnostischen Algorithmen lassen sich Schwingungsdaten in Echtzeit überwachen, was eine schnelle und präzise Fehlerdiagnose ermöglicht. Dies führt zu einer besseren Prävention von Ausfällen und einer Steigerung der Anlagensicherheit.
Die Einführung von intelligenten Schwingungsdämpfersystemen, die sich an Betriebsbedingungen und Frequenzveränderungen anpassen können, stellt einen weiteren bedeutenden Schritt in der Entwicklung dar. Diese Systeme basieren auf adaptive Steuermechanismen, die es ermöglichen, die Dämpfungsleistung dynamisch zu verändern, ohne dass manuell eingegriffen werden muss. Solche Systeme können die Betriebsoptimierung weiter vorantreiben, indem sie in Echtzeit auf plötzliche Lastwechsel oder unvorhergesehene Schwingungsereignisse reagieren. Die Fähigkeit zur Automatisierung der Schwingungsdämpfung verbessert nicht nur die Energieeffizienz, sondern reduziert auch den Verschleiß an mechanischen Komponenten, was die Wartungsintervalle verlängert und die Lebensdauer der Dampfturbine insgesamt erhöht.
Ein weiterer bedeutender Vorteil dieser neuen Technologien ist die Verbesserung der Geräuschkontrolle. Schwingungsdämpfer, die speziell für die Reduktion von akustischen Vibrationen entwickelt wurden, tragen dazu bei, den Lärmpegel in und um das Dampfturbinenhaus erheblich zu senken. Dies ist besonders in Bereichen von Bedeutung, in denen Lärmschutz eine wesentliche Anforderung darstellt, etwa in städtischen Gebieten oder in der Nähe von Wohngebieten, wo hohe Geräuschpegel nicht nur die Betriebsbedingungen beeinträchtigen, sondern auch rechtliche Probleme verursachen können.
Die Integration von Industrie 4.0-Technologien in den Bereich der Dampfturbinen bietet weitere Potenziale zur Optimierung der Schwingungsdämpfung. Mit der Einführung von IoT-basierten Systemen (Internet of Things) können Sensoren, die an den verschiedenen Komponenten der Dampfturbine angebracht sind, kontinuierlich Schwingungsdaten und Betriebszustände überwachen und diese Informationen in Cloud-basierte Plattformen übertragen. Diese Plattformen bieten eine umfassende Analyse der gesammelten Daten und ermöglichen es, Trends zu identifizieren, Frühwarnungen zu generieren und Vorhersagen über den Zustand der Schwingungsdämpfer und anderer kritischer Komponenten zu treffen. Dies führt zu einer deutlich schnelleren Erkennung von Problemen, einer optimierten Wartungsplanung und letztlich zu einer maximalen Betriebszeit der Dampfturbinen.
Mit der Weiterentwicklung der Computermodelle für die Schwingungsanalyse, die eine genauere Simulation von Schwingungsmodellen und Schwingungsdämpfungsverhalten ermöglichen, wird es zudem möglich, maßgeschneiderte Lösungen für spezifische Turbinenkonfigurationen und Betriebsbedingungen zu entwickeln. Diese Modelle können den Ingenieuren helfen, die optimale Platzierung und Spezifikation von Schwingungsdämpfern in Dampfturbinen zu bestimmen und sicherzustellen, dass die Schwingungsdämpfung bei jeder Betriebsphase der Turbine den maximalen Nutzen bringt.
Die Integration von KI-gesteuerten Algorithmen zur Überwachung und Analyse der Schwingungsverhalten ist ein vielversprechender Bereich. Künstliche Intelligenz kann nicht nur bei der Erkennung von Anomalien oder Abweichungen im Schwingungsverhalten helfen, sondern auch automatisch Vorhersagen über notwendige Wartungsmaßnahmen treffen und die Dämpfungseffizienz kontinuierlich verbessern, indem sie sich an veränderte Betriebsbedingungen anpasst.
Die anhaltende Forschung und Entwicklung von Schwingungsdämpfungstechnologien trägt so nicht nur zur Erhöhung der Betriebssicherheit und Verlässlichkeit von Dampfturbinen bei, sondern hat auch langfristige Auswirkungen auf die Energieproduktionseffizienz und Wirtschaftlichkeit von Kraftwerken. Letztlich wird erwartet, dass der fortschreitende technologische Fortschritt in diesem Bereich dazu beitragen wird, die Energieversorgung nachhaltiger zu gestalten und die Betriebszeiten der Turbinen auf eine neue Ebene zu heben.
Die fortschreitende Integration von intelligenten Schwingungsdämpfungssystemen in Dampfturbinen eröffnet neue Möglichkeiten, die Betriebsdynamik zu verstehen und zu optimieren. Die Verwendung von Datenanalyse und prädiktiver Wartung ermöglicht es, Schwingungsprobleme nicht nur zu identifizieren, sondern auch zu verhindern, bevor sie ernsthafte Auswirkungen auf den Betrieb haben. Künstliche Intelligenz (KI) und maschinelles Lernen bieten in dieser Hinsicht ein enormes Potenzial, indem sie nicht nur Schwingungsmuster erkennen, sondern auch die Ursachen für diese Muster automatisch analysieren und entsprechende Lösungen vorschlagen.
Ein zunehmend wichtiger Trend ist die Integration von Schwingungsdämpfern mit anderen Systemen innerhalb der Dampfturbine. Beispielsweise kann die Schwingungsdämpfung in Kombination mit Überwachungssystemen für Temperatur, Druck und Ölstand eingesetzt werden, um eine ganzheitliche Analyse des Turbinenzustands zu ermöglichen. Indem alle diese Datenpunkte zusammengeführt werden, können Ingenieure und Techniker nicht nur die Schwingungen, sondern auch die Auswirkungen von Temperaturspitzen, Druckschwankungen und Kraftstoffverbrauch auf die gesamte Dampfturbine untersuchen. Diese multifunktionalen Systeme bieten eine präzisere und umfassendere Fehlerdiagnose und ermöglichen eine effizientere Betriebsführung.
Zusätzlich zur Nutzung von Echtzeitüberwachungssystemen ist auch der Einsatz von Simulationstechnologien im Bereich der Schwingungsdämpfung von entscheidender Bedeutung. Simulationen auf der Basis von Finite-Elemente-Methoden (FEM) oder anderen modernen Computermodellen ermöglichen es, das Verhalten der Schwingungsdämpfer unter verschiedenen Lastbedingungen und Szenarien zu modellieren. Dies trägt dazu bei, die optimale Konfiguration und Dimensionierung von Dämpfungselementen zu ermitteln, noch bevor diese in den tatsächlichen Betrieb integriert werden. Durch diese detaillierte Planung und Simulation können Fehler und unnötige Reparaturen vermieden und der gesamte Entwicklungsprozess effizienter gestaltet werden.
Ein weiterer spannender Bereich ist die Entwicklung von nachhaltigen und umweltfreundlichen Schwingungsdämpfungstechnologien. Die Anforderungen an die Energieeffizienz und den Umweltschutz werden immer strenger, und die Dämpfungssysteme in Dampfturbinen sind keine Ausnahme. Die Verwendung von umweltfreundlichen Materialien für Dämpfer, die nicht nur die Schwingungen effektiv reduzieren, sondern auch geringere CO2-Emissionen verursachen oder recycelbar sind, gewinnt zunehmend an Bedeutung. Forschungseinrichtungen und Industriepartner arbeiten gemeinsam daran, innovative Lösungen zu entwickeln, die den Betrieb von Dampfturbinen nicht nur effizienter, sondern auch umweltfreundlicher gestalten.
Energieeffizienz und optimierte Wartungsprozesse sind nicht nur von wirtschaftlicher Bedeutung, sondern auch für die Zukunft der Energieerzeugung entscheidend. Dampfturbinen, als Herzstück vieler moderner Kraftwerke, müssen sich zunehmend an unvorhersehbare Betriebsbedingungen, wie sie beispielsweise durch Schwankungen im Energiemarkt oder durch die Integration erneuerbarer Energiequellen entstehen können, anpassen. Schwingungsdämpfer tragen dabei nicht nur zur Stabilität und Langlebigkeit von Dampfturbinen bei, sondern ermöglichen es auch, die Turbinen effizienter in flexiblen und variablen Betriebsumgebungen zu betreiben.
Die kontinuierliche Weiterentwicklung von Schwingungsdämpfungs- und Überwachungstechnologien wird eine immer größere Rolle bei der Sicherstellung einer nachhaltigen, effizienten und sicheren Energieproduktion spielen. In einem zunehmend komplexen und anspruchsvollen Energiemarkt müssen Dampfturbinen nicht nur leistungsfähig und langlebig, sondern auch adaptiv und intelligent sein. Schwingungsdämpfer werden dabei zu einem unverzichtbaren Teil eines umfassenden Betriebsmanagements, das eine Kombination aus Prävention, Überwachung und Fehlerbehebung umfasst. Der technologische Fortschritt in diesem Bereich verspricht nicht nur eine Verbesserung der Dampfturbinenleistung, sondern auch einen Beitrag zur globalen Energieeffizienz und einem nachhaltigeren Betrieb von Kraftwerken weltweit.
Zusammenfassend lässt sich sagen, dass Schwingungsdämpfer eine zentrale Rolle im Betrieb und in der Wartung von Dampfturbinen spielen. Sie sorgen nicht nur für mechanische Sicherheit, sondern optimieren auch die Energieeffizienz, verlängern die Lebensdauer der Anlagen und reduzieren Betriebsrisiken. In Kombination mit modernen Technologien wie Echtzeitüberwachung, KI-gestützten Analysen und anpassungsfähigen Dämpfungssystemen bieten sie enormes Potenzial für die Zukunft der Dampfturbinenindustrie.
EMS Kraftmaschinen – Ihr Partner für Hochleistungs-Dampfturbinen
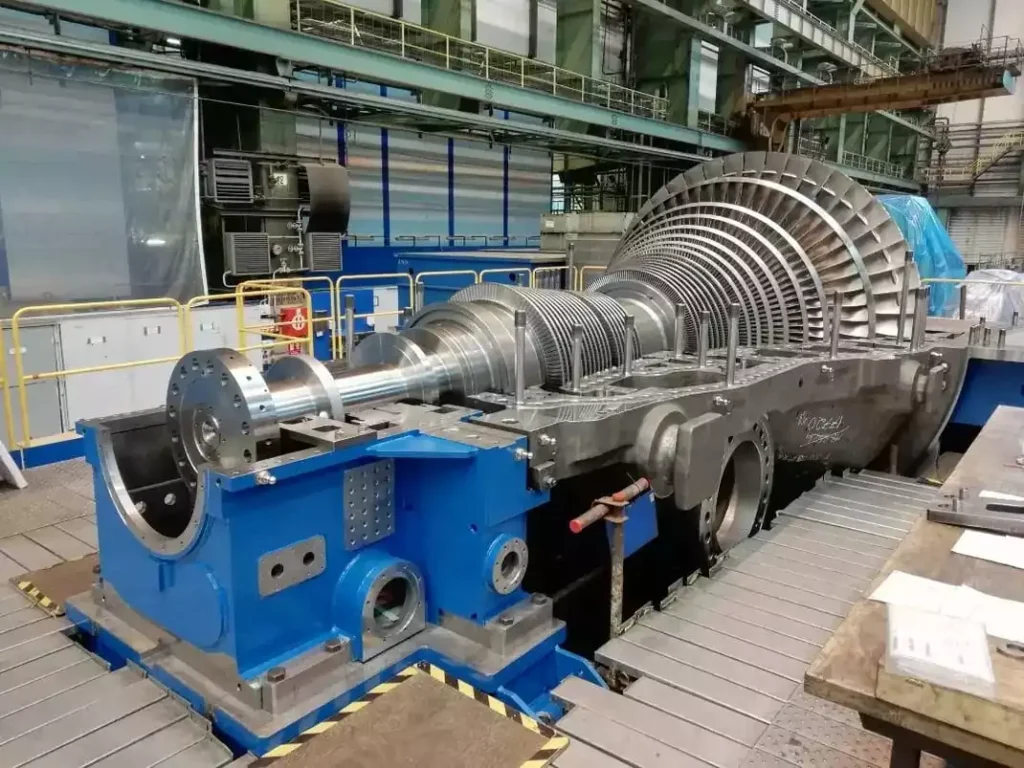
EMS Kraftmaschinen ist ein führendes Unternehmen in der Entwicklung und Herstellung hochwertiger und effizienter Dampfturbinen. Mit jahrzehntelanger Erfahrung und technischem Know-how hat sich EMS Kraftmaschinen als zuverlässiger Partner für Kunden in unterschiedlichsten Industriebereichen etabliert.
Hochwertige Dampfturbinen für jede Anwendung
Die Dampfturbinen von EMS Kraftmaschinen sind ein Synonym für Präzision und Effizienz. Sie werden aus erstklassigen Materialien gefertigt und nach den höchsten industriellen Standards entwickelt, um eine lange Lebensdauer und maximale Leistung zu garantieren. Dank der flexiblen Konstruktionsweise können die Maschinen individuell an die spezifischen Anforderungen jedes Projekts angepasst werden.
Ob in der Energieerzeugung, in der chemischen Industrie, im Schiffsbau oder in der Papier- und Zellstoffindustrie – die Dampfturbinen von EMS Kraftmaschinen bieten zuverlässige Lösungen für jeden Einsatzbereich.
Warum EMS Kraftmaschinen?
- Innovative Technologien: EMS investiert kontinuierlich in Forschung und Entwicklung, um die Effizienz und Umweltfreundlichkeit seiner Produkte zu steigern.
- Maßgeschneiderte Lösungen: Jedes Projekt wird individuell geplant, um den Anforderungen der Kunden gerecht zu werden.
- Zuverlässigkeit: Mit einem erstklassigen Service und langlebigen Produkten hat EMS das Vertrauen von Unternehmen weltweit gewonnen.
- Nachhaltigkeit: Moderne Dampfturbinen von EMS tragen zur Reduzierung von Energieverlusten bei und fördern eine umweltfreundliche Nutzung von Ressourcen.
Effizienz und Nachhaltigkeit im Fokus
In einer Zeit, in der Energieeffizienz und Nachhaltigkeit an oberster Stelle stehen, bietet EMS Kraftmaschinen die perfekte Lösung. Die Dampfturbinen zeichnen sich durch einen hohen Wirkungsgrad aus, der nicht nur Betriebskosten senkt, sondern auch die Umweltbelastung minimiert.
Ihr zuverlässiger Partner
Mit EMS Kraftmaschinen setzen Sie auf innovative Technologien, höchste Qualität und einen starken Fokus auf Kundenzufriedenheit. Kontaktieren Sie uns, um mehr über unsere Dampfturbinen und deren Anwendungsmöglichkeiten zu erfahren – wir entwickeln die Lösung, die perfekt zu Ihren Bedürfnissen passt.
EMS Kraftmaschinen – Effizienz trifft auf Präzision.